广汽G-MC 机电耦合系统技术解析
机电耦合系统是混合动力汽车的关键核心动力传动部件,该系统的研发及产业化需要攻克多项系统集成级和部件级技术课题,并提升上下游产业链关键零件制造能力。广汽集团于2014年初立项开发自主第一代G-MC机电耦合系统,G-MC全称为GAC - Mechatronic Coupling, 即广汽机电耦合系统,采用了油冷电机技术、集成式电液控制技术、湿式离合器与固定轴齿集成技术,以及能量最优综合控制等多项先进技术。搭载该系统的多款车型,其动力性、经济性、操控性及舒适性均处于行业先进水平,具有较明显的市场竞争优势。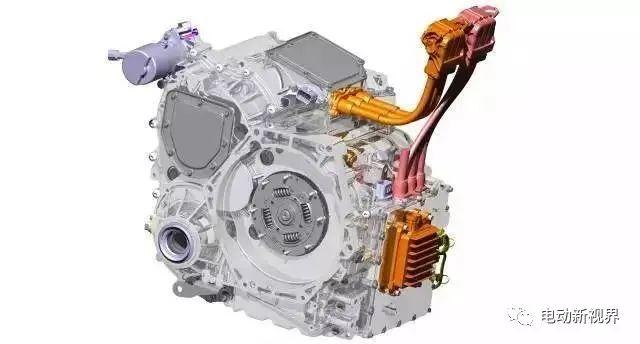
图1
为跟随市场发展趋势、实现技术和性能全面引领,本项目拟升级G-MC产品,完成自主创新及产业化。升级产品需提高系统整体效率,在大幅提高扭矩容量的前提下,减小体积和重量, 降低产品成本。G-MC升级产品将在能量分配与管理、多动力源瞬态功率耦合品质、多部件协同控制精度、输出转矩密度提升、全工况系统效率最优作为开发的主要方向,完成全部设计、开发和验证工作,确保投入量产。1.广汽已上市的混动方案及技术特点
广汽 GMC 是一款拥有完全自主知识产权的混合动力机电耦合系统,是广汽混合动力整车最核心的零部件。该系统可以实现纯电动模式、增程模式、混动模式、再生制动模式、驻车发电模式。1.5 ATK 发动机+发电机+驱动电机三个动力源,根据动力需求进行智能化最佳组合,为整车提供可靠的动力保障。G-MC 机电耦合系统集成了电机系统、齿轮传动系、差减、驻车系统、离合器等,极大的提高了整机的集成度,有效缩减了整机尺寸和重量。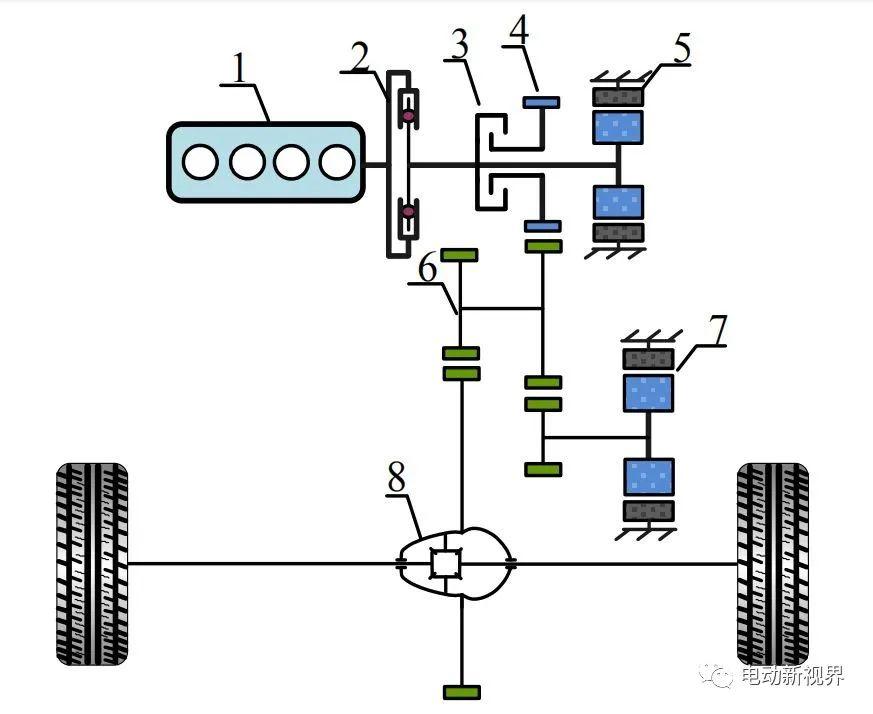
1.发动机;2.扭转减振器;3.离合器;4.一级齿轮;5.发电机MG1;6.中间轴;7.电动机MG2;8.主减。
图2 G-MC1.0 构型原理
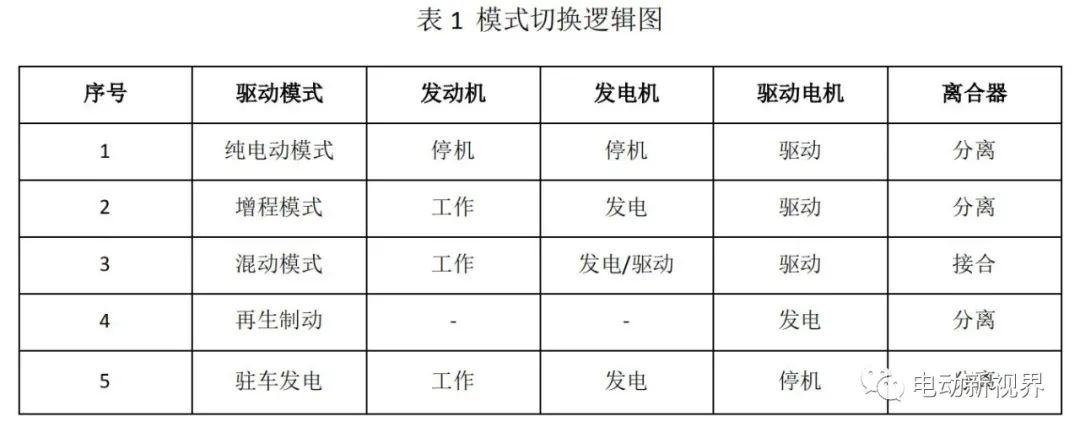
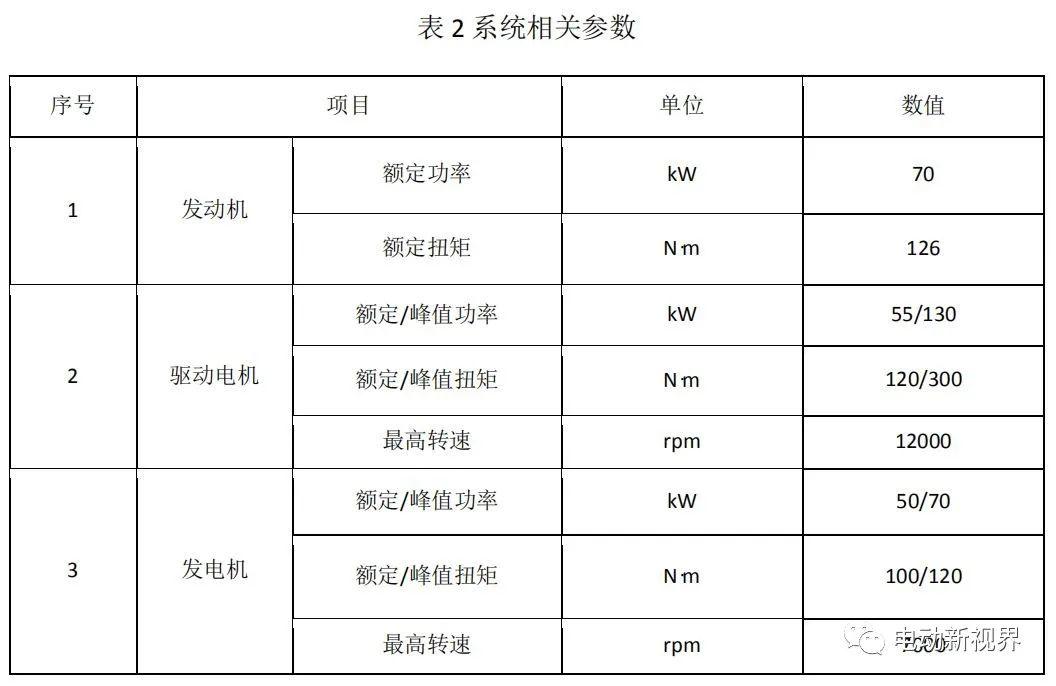
G-MC 机电耦合系统开发过程中主要遇到以下难题:
2.G-MC1.0混动方案升级与优化
针对 GMC1.0 系统,匹配 1.5TM 发动机及速比,对零部件进行优化升级,目前已开发至 C样,计划 2019 年底上市。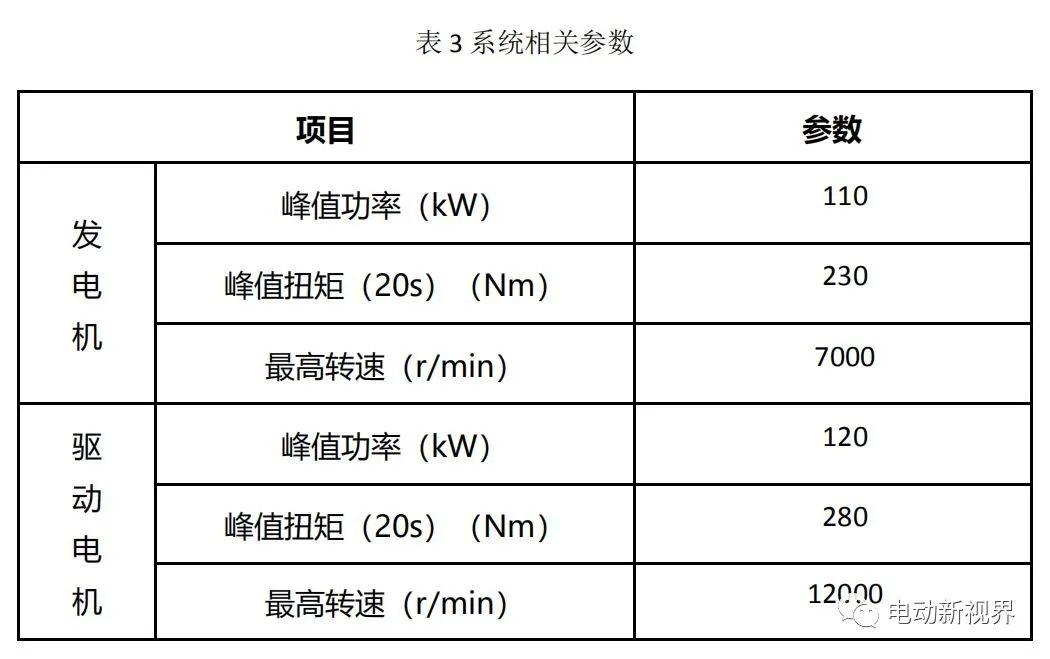
3.1 研究方法
本项目采取自主研发与借鉴/吸收国外先进技术相结合,理论分析和试验研究相结合的研究方法,在总结第一代机电耦合系统基础上,结合对标分析和理论分析,提出全新概念方案,确定最优技术方案。构型优选:首先设定搭载整车的性能表现、机电耦合系统的总体性能、发动机特性和电机最高转速为边界条件,将电机个数、电机性能参数、档位数量、速比、执行元件数、各旋转元件最高转速差等作为变量,以系统效率最高、成本最低、体积重量最小为目标,进行多目标多变量全局寻优,找到适合的备选构型方案;部件优化:在选定的备选构型下,完成各部件布置及结构设计后,结合生产制造要求、上下游产业链技术水平,对系统效率、系统工作模式、控制策略、疲劳耐久等搭建数学模型,通过CAE 仿真计算、经验评估、专家咨询,对备选方案进行综合对比,确定最终的系统方案和子系统方案,并完成各部件的详细设计;试验策划:本项目将策划机电耦合系统 A 样、B 样、C 样的试制与试验,从零部件、子系统、系统层级逐一完成台架试验,也将同步开展整车搭载试验,包括效率测试、三高测试、耐久测试等一系列完整的测试验证,确保产品的优秀性能表现和可靠耐久。表4 G-MC2.0模式切换逻辑
序号 | 驱动模式 |
1
| EM2 纯电驱动 |
2 | EM1 一挡纯电驱动 |
3 | EM1 二挡纯电驱动 |
4 | 增程模式 |
5
| 一挡并联驱动 |
6
| 二挡并联驱动 |
7
| 再生制动 |
8
| 驻车发电 |
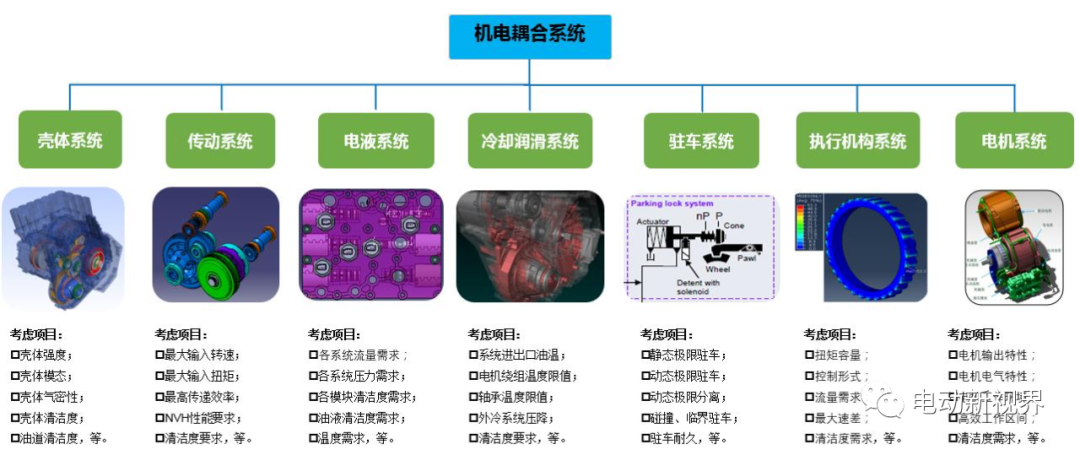
图 3 技术方案
第一代产品总体表现良好,但存在成本高、重量大等主要问题。新一代升级产品首先从系统层级上将优选双电机系统,拓展系统的工作模式,从以下各技术领域优化:电机系统:延续集成式双电机系统,电机本体采用油冷式,集成于机电耦合系统本体中, 电机控制器在布置方式上与机电耦合系统集成,减少电机控制器与机电耦合系统之间的连接线,进一步提升机电耦合系统的集成度;执行机构:在执行机构的选择与布置上,要满足双电机纯电驱动、驻车发电机等的需求, 以进一步减小对电机系统的需求;在控制方式上,尽可能采用液压式,并与油冷系统共用油液;液压系统:电机本体、执行机构等共用油液进行冷却润滑、结合分离控制,液压系统需满足冷却与控制需求;控制系统:将电机控制器集成到机电耦合系统中,视电机控制器开发任务及供应商情况, 将液压系统控制、驻车机构控制等集成至电机控制器,提高系统集成度,降低重量、成本。升级产品将采用全新传动方案,使发动机、驱动电机及发电机混联,实现三个动力源重度混合,以此达到系统能量最优分配,进一步降低燃油消耗量。升级产品将采用集成式控制器,将双电机(驱动电机和发电机)控制器等多控制器集成开发,提高电气系统效率,降低生产成本。升级产品将零部件高度集成,包含齿轮与离合器毂电子束焊接、多重轴齿及轴承嵌套、多层液压阀板及多层控制电路等技术实现集成。升级产品将基于一套技术完成插电式和非插电式混合动力车型的应用开发,同时并行开发大扭矩版本和小扭矩版本,覆盖广汽传祺全部整车平台。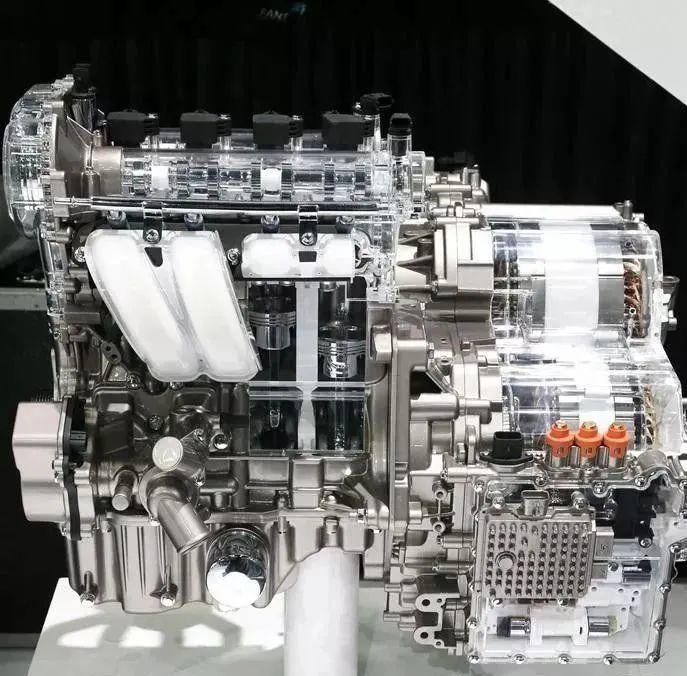
图4
除了1.5L ATK阿特金森发动机本身油耗具有优势以外,G-MC根据不同工况下对动力输出模式做出的正确选择也起到了关键作用。它一共具有纯电模式、增程模式、混动模式和制动能量回收模式等四种动力模式:在城市路段拥堵路况时,G-MC自动切换为纯电模式,驱动电机为车辆提供动力,避免普通汽油车频繁启停发动机或者发动机长期运行在非经济区所造成的燃烧不充分,油耗高,排放高的问题。当电池电量不足时,G-MC自动切换到增程模式,发动机给发电机发电,由发电机为驱动电机继续提供能源驱动车辆。此时发动机转速被控制在最佳经济区,其油耗要远低于由发动机直接驱动车辆所产生的油耗。当电池电量不足且汽车运行在中高速路段时,G-MC自动切换为混动模式,由驱动电机和发动机共同驱动车辆,此时可以充分发挥发动机的高效区,减少燃油的消耗。当车辆制动时,开启制动能量回收模式,驱动电机充当发电机作用将制动能量回收存储在电池中。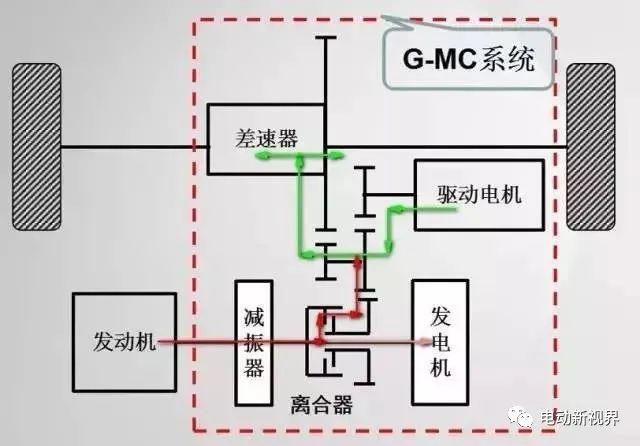
图5 G-MC机电耦合系统的结构图
5.动力性
搭载G-MC的GA3S PHEV整车实测百公里加速时间8.9s,起步、加速超车都有强烈的推背感,在家用车中算得上出类拔萃了。在车辆起步时,G-MC自动切换到纯电模式,此时电机扭矩大的优势一览无余,峰值扭矩达到300牛米,轮端最大输出扭矩可达2321牛米,保证了0-50km/h加速时间不超过4s;在中高速超车时,电池组为驱动电机提供额外电能,让驱动电机瞬时产生最大功率输出,足以与高性能燃油车匹敌。6.经济性
广汽表示,搭载广汽自主研发的1.5L ATK+G-MC这套混动系统的GA3S PHEV百公里油耗仅仅只有1.4L。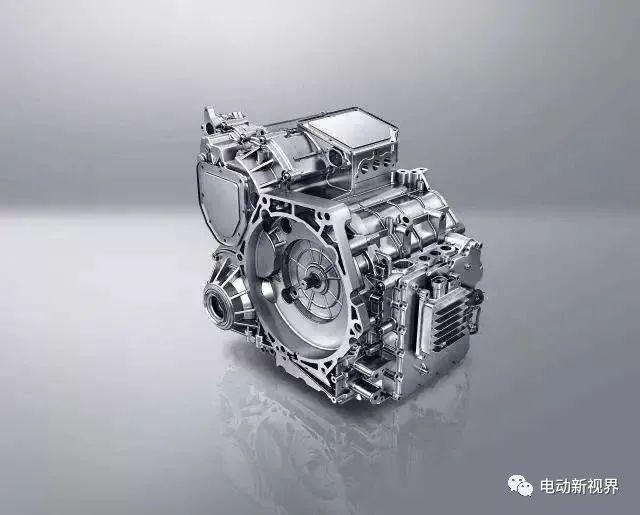
图6
作者:祁宏钟
广汽研究院首席技术总监