设计电驱齿轮箱、电机和电力电子的创新性系统方法
摘要
新能源汽车的电驱动总成是系统工程,仅不断优化某个子系统,无法获得最优的电驱总成,这已成为业界的普遍共识。整个电驱动行业更加趋向于集成化的开发思路,也让系统化、创新化的开发方法变得更加重要。
传统的系统工程方法历经几十年的发展,其目标是管理由多个子系统构成的复杂系统的设计工作。它认识到系统之间的因果关系,在其典型的应用与实践中,系统工程成为一种便利的方法来应用和管理系统之间的边界,从而在组织、软件代码等之间进行信息交流。
不幸的是,在现代高度集成的新能源汽车电驱动系统中,不同子系统之间的相互作用更加复 杂,因此传统方法难以解决这些问题。单一物理场和多物理场之间的相互作用与复杂行为,如动力学、噪声、热和效率等,都无法用简单的功能分析和分配来表示。
本文讲解了Romax科技有限公司在传统的系统工程方法的基础上开发的一种方法,该方法能够考虑不同子系统之间的复杂相互作用,并介绍了齿轮箱、电机和电力电子系统在动力学和热特性方面复杂的相互作用的案例,同时也详细介绍了Romax公司在新能源汽车动力总成交钥匙设计项目中的能力及工程实践。
新能源汽车已从低产量、小众市场转向大规模生产,电动化显然已被视作未来全球汽车行业的主导技术。所有的公司都在考虑在新能源车型上实施合适的电动化方案,并以此来获得竞争优势。在技术方面,功率密度、效率、噪音和成本等各方面的指标也对电动汽车动力系统提出了更高的子系统集成化要求。
在所有组织中,研究工作的组织方式是共同的,以便制定各种方法,使该组织的目标能够更有效和更高效地实践与应用。制造工艺和过程管理时常采用科学管理和准时制等理念,同时对设计过程进行了研究,提出了确保设计过程顺利管理和实施的方法(参考文献1)。在任何情况下,目的都是确保流程的输出与输入目标在多方面相互匹配,如最大程度的确定性、最低的风险和最少的资源消耗(如时间、人力和资金)。
系统工程是设计过程管理的主要方法之一,在复杂系统的设计中已经应用了数十年,并被应用于新能源汽车电驱动总成的设计。这是非常合乎逻辑的,因为它同时处理不同系统的管理与协同。本文研究了如何很好地满足这一挑战,以及如何确保该流程符合预期目标。
系统工程的基本概念
“系统工程”一词在20世纪40年代首次被贝尔电话公司使用,但实际的方法是在战后几年的国防项目中发展起来的。在该方法中提出了不同的概念,并开发了相关的工具,如质量功能实 施,已被全球众多企业所使用。
系统工程在新产品导入过程常用V模型来表示。它分为两个方面,左边是设计阶段,右边是开发阶段。在图1所示的说明中,有三个层次,总系统由许多子系统组成,子系统由各部件组 成。该模型可支持更多的层次,但这里我们不必讨论。
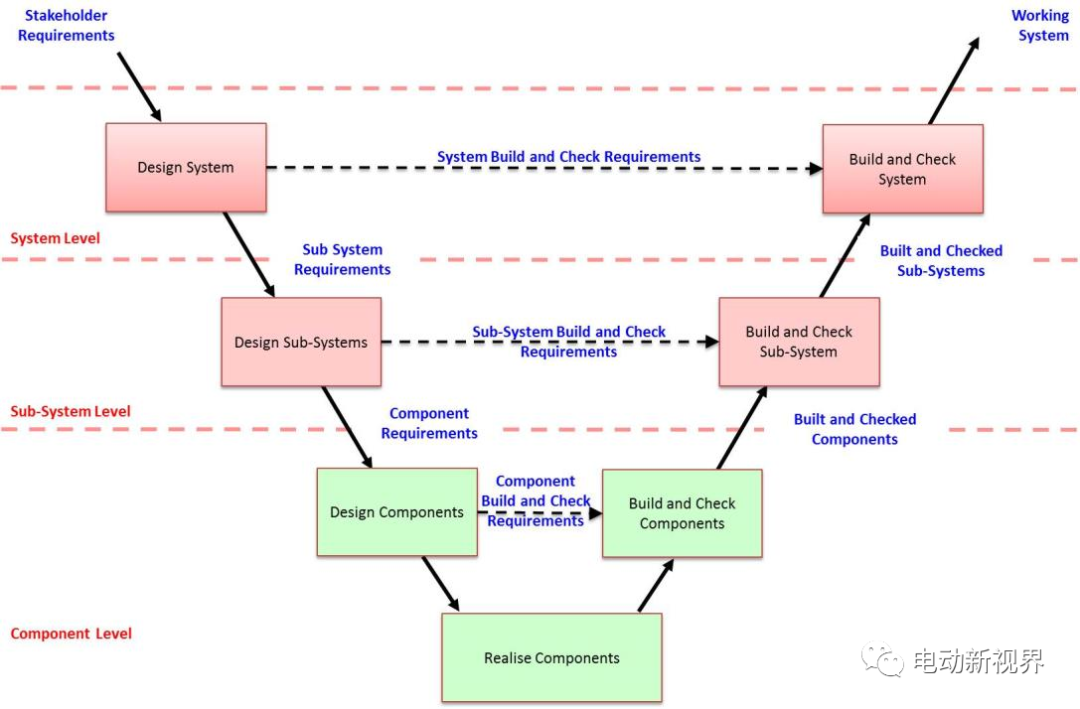
图 1 :经典的系统V-模型
系统的顶层需求由项目的发起方来定义,逐级向下分解来定义子系统的目标,继而相应地向下分解到部件的设计需求。开发中,对部件进行设计和采购,然后可以对部件进行测试,以确保它们符合目标规范(从设计需求中获得)。在此之后,将各个部件装配为子系统,再按照子系统的要求进行测试与验证等。其目标是确保最终的产品可以根据项目发起方的原始需求集 合进行充分的验证和测试。
此类子流程如图2所示,在每个阶段都要研究所需的功能并制定潜在的解决方案,然后研究这些解决方案是否符合规范,以便选择最佳解决方案。在这个阶段,人们可以研究如何将其应用到新能源汽车动力系统的设计。
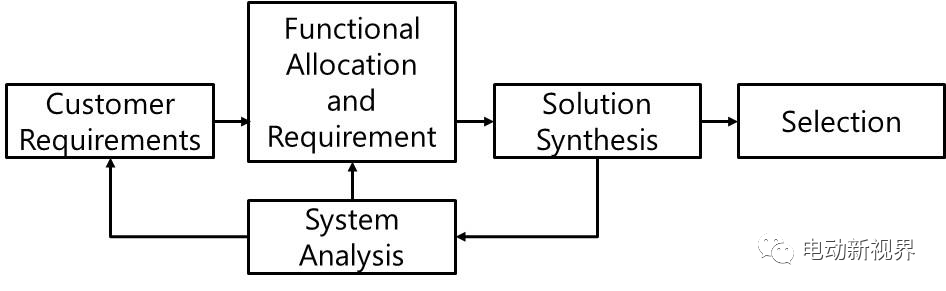
图 2:典型的功能分配过程和系统综合分析
系统工程方法在新能源汽车电驱动系统开发中的应用
从V形图的左上角开始,第一步是项目发起方的需求设置,以便能够创建和评估合适的解决方案。在此阶段,目标的设置多为抽象类型,以便鼓励和生成更多的创新思路,而不是简单地遵循以前的解决方案。
然而,为了简洁起见并突出重点,本文以一个包含齿轮传动的新能源乘用车电驱动总成为案 例,忽略其它很多选项,比如,由压缩空气或机械飞轮储存能量,使用燃气轮机作为动力源, 以及人们普遍使用的公共交通等。
车辆的顶层需求比较容易定义。很多人会关注车辆的各项指标,如载客和行李存储空间的能力、车型、成本等。消费者更感兴趣的是与动力系统相关的某些限制和指标:
同样,在寻找潜在的解决方案时可以使用一定程度的抽象,但是为了贴合本文的主题,这里假设该项目是将电池、电力电子、电机和齿轮箱集成起来的电驱动总成。
系统工程将我们带到一个熟悉的起点,在这里,每个子系统的顶层需求可以根据它们如何交付车辆的主要功能和需求来定义,即:
在这一阶段,需要对电池技术、电机的拓扑结构、变速箱是单速还是多速,甚至是否有一个、两个或四个从动轴进行决策,但这不是本文的主题。这里的重点是在设计过程中如何设置和监视目标。标准结果是每个子系统的一组边界条件,例如速度、扭矩和变速箱的速比要求。
此处的重点集中在变速箱的主要功能上,即传输机械旋转功率和改变速度及扭矩,以及如何定义变速箱与其相邻的子系统(电机和传动轴)之间的边界。这种方法可以确保设计流程易于管理,每个子系统的设计目标都非常清晰且可以被分配到相应的部门或供应商的团队,同时,可以通过主要的项目管理功能和最终的系统交付程度来监控是否达成此规范。
基于模型的系统工程的必要性
到目前为止,如果子系统本质上是独立的,并且它们的物理相互作用仅限于一两个简单的行 为,那么这种方法就可以很好地满足要求。然而,在现代电动汽车动力系统的设计中,情况并非如此。图3是ODIN项目动力总成的剖面图,这是一个由欧盟框架计划7(FP7)资助的合作项目。该项目从2012年至2016年运行,由博世有限公司(Bosch GmbH)牵头,由雷诺(Renault)、Romax Technology、GKN Driveline、CIE Automotive、Fuchs和亚琛工业集团(RWTH Aachen)共同参与完成。
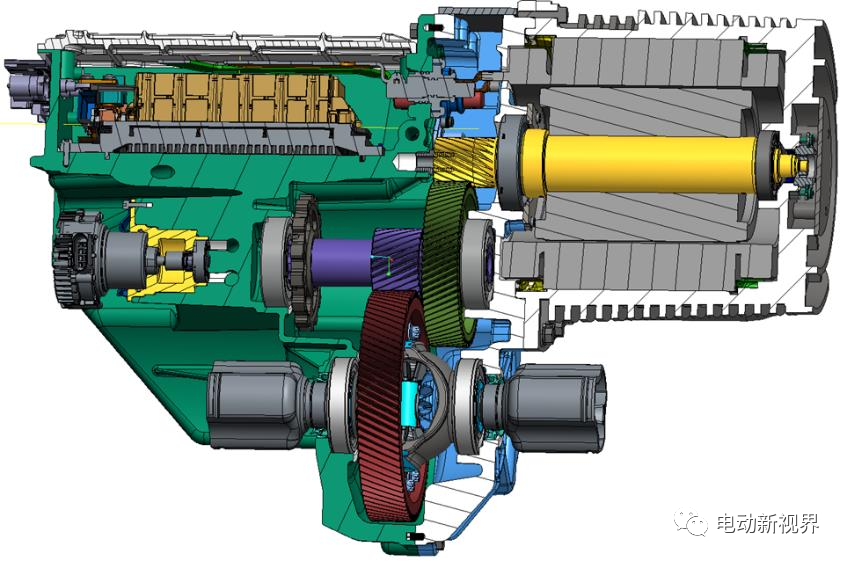
图 3:ODIN项目电驱动力总成的剖面图
上图展示了现代电动汽车动力总成的高度集成化特性,齿轮箱的主要功能是传递机械动力和改变转速与扭矩,这也导致了齿轮箱相邻部件的影响,即扭矩、转速等。虽然这些上层的相互依赖关系很重要,但它们并没有完全描述当齿轮箱、电机和电力电子设备如此紧密地集成在同一个壳体内时所发生的物理相互作用。以电机与齿轮箱之间的扭矩传递为例,我们可以简单地考虑其峰值扭矩和转速,也可以是扭矩与转速的关系曲线,但实际上,电机传递的扭矩信号不仅仅是直流分量,还包含扭矩脉动,由一系列不同的谐波组成,所有这些谐波都随着电机扭矩和速度的变化而变化。
“动力总成”和“传动链”这两个术语经常互换使用,而传动链意味着电机和齿轮箱之间的另一种相互作用,与扭矩传递的“简单”功能有关。传动系统内的任何扭转动力学都涉及这两个子系统,因此对两个子系统之间的物理相互作用的正确定义还应包括动态阻抗项。同样,动态阻抗也随频率、扭矩和转速而变化。
还应考虑其他物理相互作用,在每种情况下,都可以看到相互作用的简单定义远远不能描述现实。更重要的是,完整的描述不仅更复杂,而且数据量也很大,无法在文档中描述,因此很难通过电子邮件、电话或与部门主管或供应商的会议进行检查。
名义相互作用 |
子系统之间相互作用的简单 定义 |
充分考虑子系统之间的相互作用 |
扭矩传递 |
-最大扭矩和转速;或扭矩- 转速曲线 |
-扭矩值、随转速和扭矩变化的扭矩脉动及谐波; -随转速和扭矩变化的动态 阻抗 |
发热与冷却 |
-最高绕组温度目标;磁铁不产生退磁 | -多个热源:电机、齿轮、轴承、电力电子; -通过冷却剂和润滑油传热 -各结构的热容和电导 -结构和环境的多个散热器
|
正是在此基础上(不代表以此作为相互作用的定义),系统工程发展为基于模型的系统工程(MBSE),有助于对只能通过大数据定义来描述的子系统之间的相互作用的深入理解,因此需要借助计算机系统进行处理。显然,计算机辅助工程(CAE)是佳选择。对可能发生的情况进一步分析会引出额外的复杂性,例如:齿轮的错位量(静力学分析)影响轮齿接触,从而影响齿轮的摩擦行为(摩擦学),从而影响发热量。散热受传导(热)和对流(流体力学)的影响,但都会影响动力总成的内部温度分布,这会导致其自身的系统变形,并会影响齿轮错位量。因此,这里存在多个物理系统的相互作用(子系统之间作用的多个物理交互实例)和多物理场系统的相互作用(子系统之间相互影响的行为实例,涉及多种物理现象)。在这个阶段,存在着掉进技术“兔子洞”的风险。模拟所有这些物理现象和多物理场之间的相互作用,以及为一个子系统的设计团队提供另一个子系统的知识和数据,这些都可能导致分析瘫痪。此外,将所有这些不同的CAE系统连接在一起的成本可能令人望而却步,因为每个系统都需要有相关领域的技术专家来运行。针对新能源汽车电驱动总成的应用级MBSE开发
Romax在约25年前指出,解决这一难题的关键在于,应从全系统角度对传动系统进行工程仿真,而不是单独孤立的零部件角度。近年来由于电动化的发展趋势,该方法也有了新的应用场景。Romax Nexus是专门为旋转机械开发的软件产品,尤其适用于各种齿轮箱和传动链。通过与通用CAE工具的合作,Romax Nexus的仿真方法为“一次分析即考虑多个物理场”,而不是“所有的分析只考虑单个的物理场”。该方法可处理多种物理场,例如静力学、动力学、效率、接触力学等,此外,也可处理多物理场之间的交互作用,例如错位量影响齿轮轮齿的接触力,导致齿轮产生传动误差,从而激励动态模型,最终导致振动噪声和产生。作为一款专用的仿真软件,所有这些多物理场及其之间的相互作用都可自动分析,并具有正确的细节程度。更重要的是,25年的持续改进和优化意味着关键系统的影响已经确定并在重要性上得到了提升。能够模拟所有物理场的相互作用,并不意味着每次必须去这样做,会消耗巨大的资源,工程实践中一般要求按照优先级考虑一级效果和二级效果,工程经验则进一步帮助发展和完善这种方法。Romax的业务范围主要是工程仿真与技术咨询(故障解决和其他独立技术服务),近年来扩展至交付完整的电动汽车动力总成设计和开发的交钥匙项目。这些项目的交付范围包括齿轮箱、电机、电力电子和控制系统,从概念设计到详细设计、部件和子系统测试,在为客户投产提供技术支撑。这可以再次映射到图 1上,因为子系统和部件的规范定义了测试需求,此时系统工程方面仅为只读的作用。这样一来Romax特定的MBSE方法也必须扩展,仅考虑机械方面是不充分的(静力学、接触、摩擦学、效率、NVH)。在这个列表中,需要添加电磁学、控制、热力学等,这些都是在电动化传动链中非常重要的特性。子系统之间的相互作用是非常复杂的,并且发生在设计过程的不同阶段,涵盖了性能的各个方面。在概念设计的最初阶段,必须确定电机转速、齿轮箱总速比和档位数。如果总速比较小, 则齿轮尺寸可以小一些,但此时需要有更大扭矩的电机,因此电机会占用更大的空间。这个决策的影响会进一步扩展到各个子系统。高速电机的趋势意味着,对于给定的电机拓扑结构,为了保持波形的精度,开关频率会增加。然而,为了更接近目标正弦波和减小转矩脉动, 开关频率升高也已经成为必然趋势,这一点可以从齿轮箱壳体的辐射噪声中体现出来,但高开关频率会带来额外的功率损耗,从而影响能源效率和热性能。有能力单独处理所有这些领域中的问题固然重要,但更重要的是能够使用基于模型的系统工程方法识别子系统之间的相互作用并将其量化,将量化信息及时传输到前台,使用数据驱动的决策方法对设计项目做出工程判断,以应对开发时间压力和市场压力。这正是Romax eDrives团队一直在寻求的方法。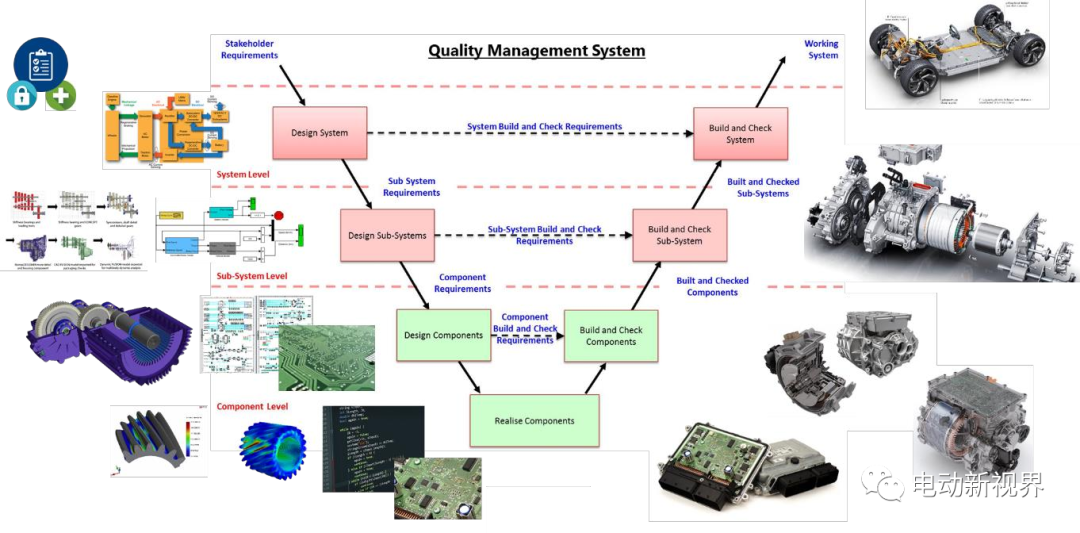
图 4:Romax eDrive团队设计开发能力范围
这些设计和开发项目已经成为一个平台,Romax可以在此平台上为电动汽车动力总成设计开发其专用的MBSE工具;这些工具是当前设计项目所需要的,但随着时间的推移,这些工具会应用于Romax的咨询服务,然后集成到Romax Nexus软件平台。
其中之一就是在动力总成噪声仿真中对电机控制效果的仿真研究。Romax率先提出在时域内预测齿轮箱噪声,其在该领域的工作始于20年前(参考文献 2、3),而且是第一个将电机和齿轮箱噪声仿真集成在一起的公司(参考文献 4、5)。
目前最先进的方法是使用电磁仿真工具进行电机激励计算,然后与Romax Nexus进行数据交互,联合仿真。但这种方法中,也只是假设“理想的”电流波形,即纯正弦波。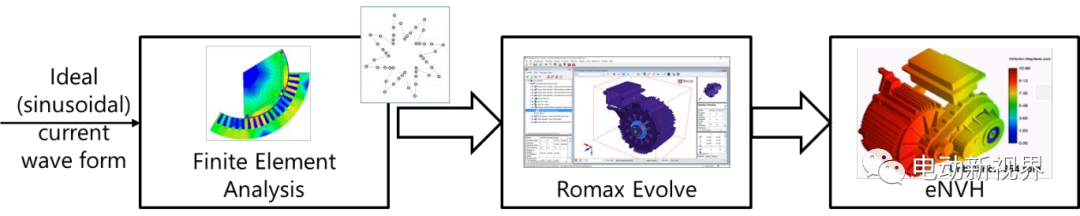
图 5:应用于集成式电驱动力总成的高级噪声仿真方法
在最近的一个项目中,Romax在Simulink中开发了一个电动化动力系统的集成模型,包括电力电子、电机和电机控制。对整个系统进行了仿真,导出了实际电流波形(非正弦波)。然后将其输入电机的电磁仿真工具,从电磁仿真工具中输出激振力用于Romax Nexus中的噪声仿真,这一扩展的流程如图 6所示。
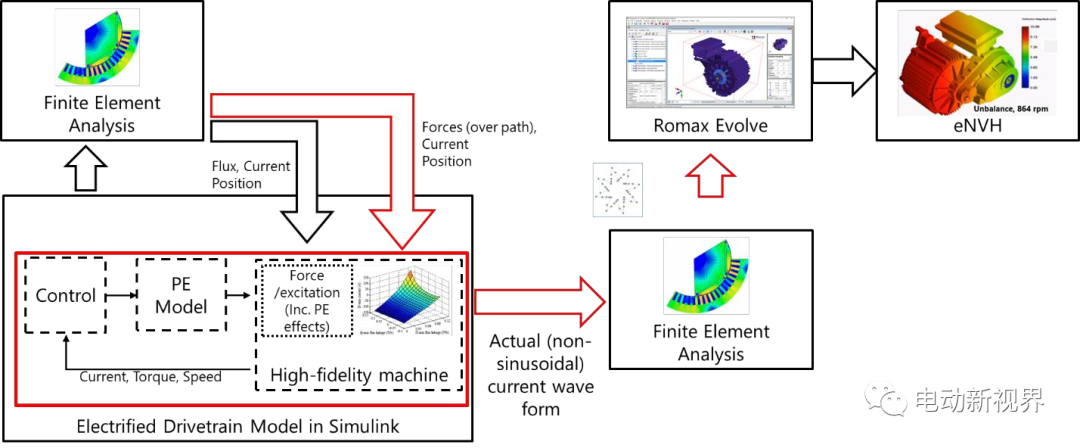
图 6:电驱动力总成NVH分析的扩展方法 – 考虑电机控制效果
从图 7可以看出,与纯正弦波相比,附加模型可识别出与开关频率相关的新频率(不同的附加谐波取决于开关基频是5khz还是8khz)。
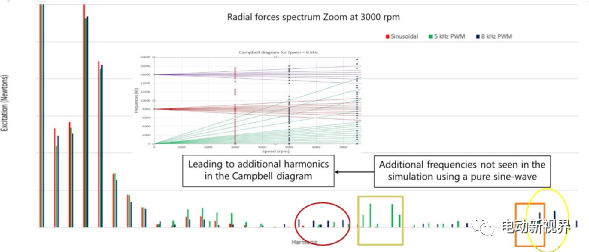
图 7:扩展方法的仿真结果中出现由自脉宽调制引起的附加谐波
总结
设计下一代新能源汽车电驱动总成意味着必须有合适的设计流程,以确保最终产品符合目标并具有市场竞争力。全球各公司寻求将他们的设计过程建立在诸如系统工程之类的既定方法的基础上,在很大程度上,这是一个良好的开端。
当今新能源汽车电驱动系统的高度集成设计意味着系统之间的相互作用众多且极其复杂,这需要使用大数据方法,因此需要基于模型的系统工程方法(MBSE)。
本文阐述了特定的MBSE方法如何为设计流程带来最大的生产力,从而提高传动效率、增加功率密度、更好的NVH效果、更低的成本且更快地进入市场。该方法已应用于Romax公司的电动汽车动力总成交钥匙设计项目。
除此收益外,这也带来了系统级仿真方法的新发展,这将及时为全球更广泛的设计工程师群体提供更高级的软件功能,包括能够在电机和齿轮箱噪声仿真中考虑电机控制因素和PWM边频带的影响。
参考文献
1.“Engineering Design – A Systematic Approach” – Gerhard Pahl & Wolfgang Beitz
2.“Development of a Gear Whine Model for the Complete Transmission System” - James, B. and Douglas, M., SAE 2002-01-0700.
3.“Predicting Variation in the NVH Characteristics of an Automatic Transmission using a Detailed Parametric Modelling Approach” - Pears, J., Smith, A., Platten, M., Abe, T. et al., SAE 2007-01-2234.
4.“Simulation and Optimisation of Noise for a Highly Integrated EV Drivetrain” – Barry James, Romax Technology Ltd., Dr. Christian Lang, Robert Bosch GmbH, CTI Berlin December 2013.
5.“Simulating and Reducing Noise excited in an EV powertrain by a Switched Reluctance Machine” – Barry James, Romax Technology Ltd., Dipl.- Ing. Andreas Hofmann, RWTH Aachen University, SAE 2014-01-2069.