摘要
本文介绍了为新型FCV研制的高压储氢系统。为了进一步推广FCV,这一开发成功地提高了系统的性能,降低了成本。这个新的存储系统由多个不同大小的油箱组成,经过优化,可以在不牺牲车辆内部空间的情况下存储所需数量的氢气。通过采用与碳纤维制造商合作开发的高强度碳纤维,并优化层状结构设计,减少碳纤维的数量,实现了世界上最高的体积效率之一。为了增加可用的氢气的数量,较长的高压罐安装在车辆地板下,不像以前的模型。通过以下两种措施就可以实现这一点:首先,采用了对储罐的单独设计和制造措施。衬垫的形状被优化,以适应在极低的温度下的快速加油。优化了成型条件,简化了制造工艺,防止了成型缺陷。其次,将高压存储系统优化为一个综合系统。尽管采用了多个不同尺寸的储罐,但通过优化温度传感器的布置和氢射角的角度,确保了与之前系统相同的高填充效率。此外,还采取了各种降低成本的措施。采用CFRP(碳纤维增强塑料)高压储罐的新材料加速树脂固化,并采用储罐阀和调节器的新加工方法,缩短了制造时间。这些措施有助于显著降低新型高压储氢系统的制造成本。电力和氢的利用被认为是促进车辆与全球环境共存的一种很有前途的手段。丰田汽车公司从1992年开始开发燃料电池汽车(FCVs),并进行了一些开发项目,目的是实现这些车辆的广泛采用。2014年,丰田为“MIRAI”FCV轿车开发了一种新的70MPa高压储氢系统。该系统帮助“MIRAI”实现了更低的成本和相当于传统汽油车的长驾驶里程。丰田现在开发了一种新的高压氢储罐系统,旨在鼓励fcv的广泛普及。该新型氢储罐系统比“MIRAI”系统实现了进一步的性能提升和更低的成本。70MPa高压储存系统概述
FCV的优点之一是比电动汽车有更长的驾驶距离。通过提高燃料电池(FC)系统的燃料效率和氢气容量,进一步扩大了新型FCV的驱动范围。新开发的高压氢罐的形状进行了优化,使安装在中心隧道空间,位于轿车类型车辆的地板下(图1)。油箱的形状确保了车辆有足够的内部空间和氢气的能力。结果,氢气量增加到5.6公斤。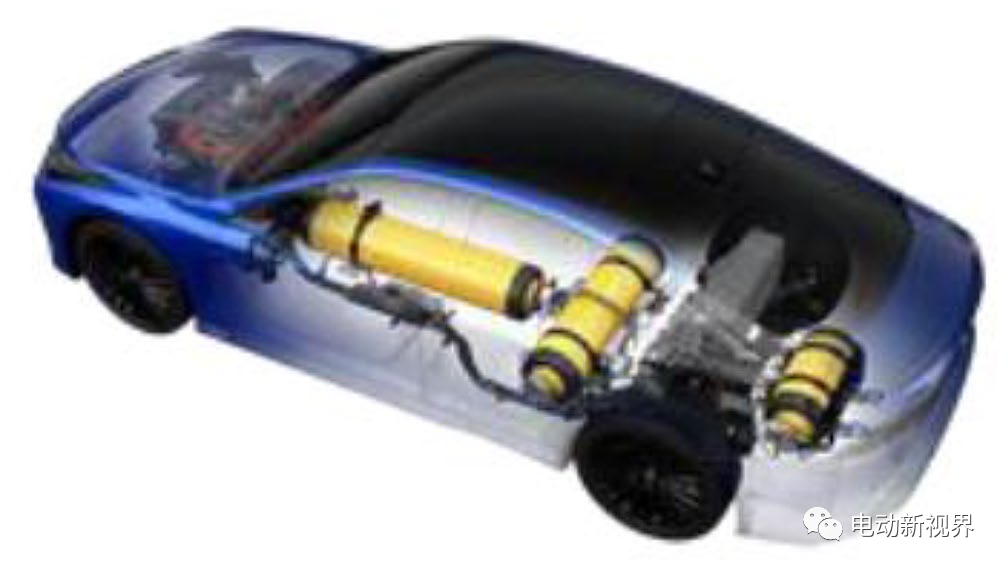
图1 储罐的安装布局
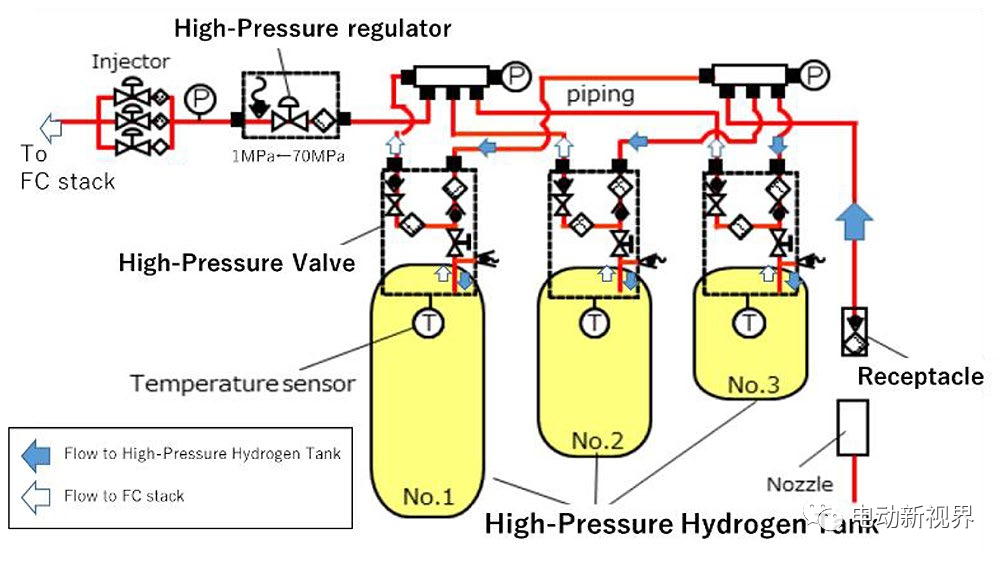
图2 高压存储系统的基本配置
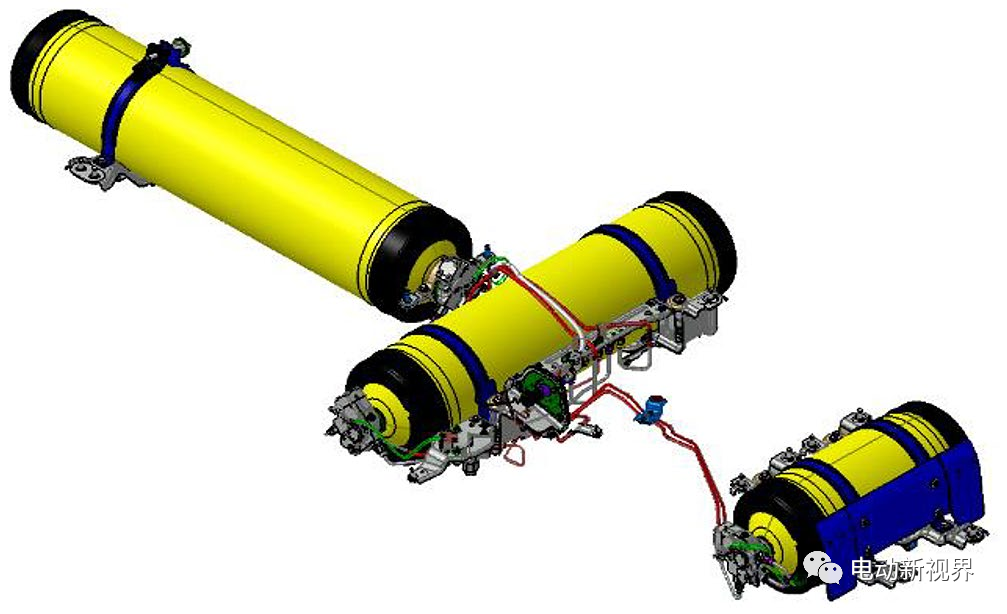
图3 高压储存系统的外观
在到达FC堆栈之前,通过高压调节器和喷射器分两个阶段降低了来自这些储罐的高压(图2)。高压储罐使用圆形支架安装在地板下面(图3)。高压氢气罐的研制
图4显示了高压储罐的结构。储罐由最内层的塑料衬里组成,以密封氢气,周围是能够承受高压的强碳纤维增强塑料(CFRP)层。其周围是具有高抗冲击性的玻璃纤维增强塑料(GFRP)层,最后是一个保护层。铝制的老板位于塑料衬里的两端,有一侧用于阀门配件。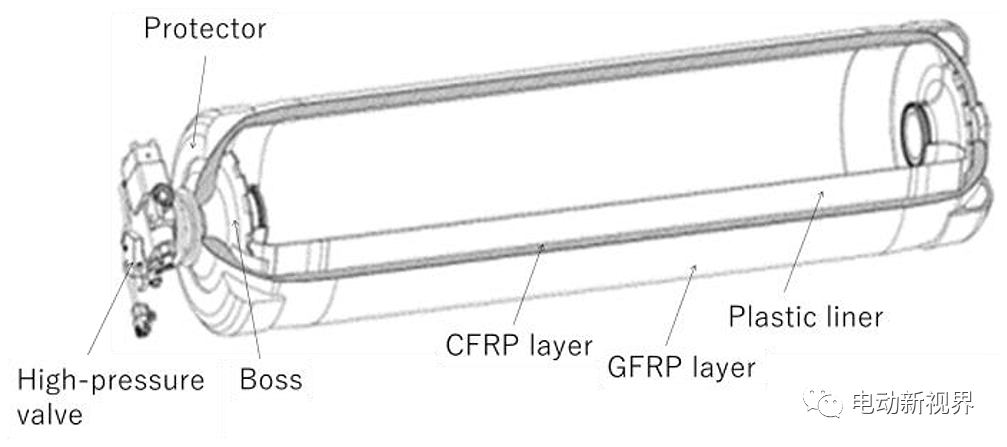
图4 高压氢气罐的结构
为了增加有限空间内的可用氢气使用量,采用了与碳纤维制造商共同开发的高强度碳纤维,通过优化层状结构设计,减少了碳纤维的使用量。因此,新的高压储罐达到了世界上最高的体积效率之一。“MIRAI”型储罐采用的商用碳纤维强度进一步提高。在碳纤维制造商的合作下,强度比以前的模型提高了大约4%。车辆包装约束条件下可用氢气的最大化
为了达到最大数量的船上氢,储罐的布局包括使用中心隧道。然而,需要解决两个主要问题:在车辆的纵向上实现安全安装,以及确保长油箱的功能和耐久性。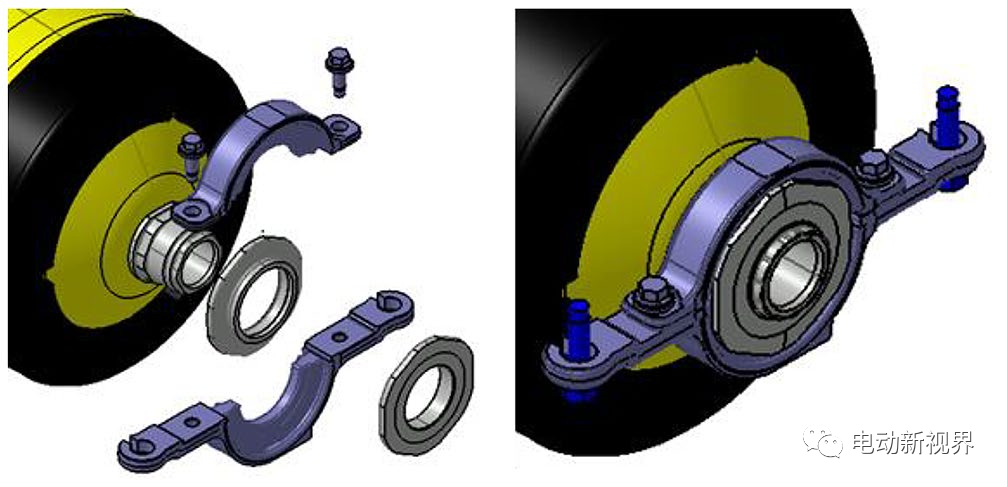
图5 颈安装式固定结构
新的坦克固定结构,以确保车辆纵向的约束力,以安全固定车辆,采用颈式固定装置(图5),这大大增加了纵向上的结合力。此外,利用中心隧道前面较大的上部空间,只在车辆后侧设置颈安装结构,高压罐外径最大化,氢气容量增加。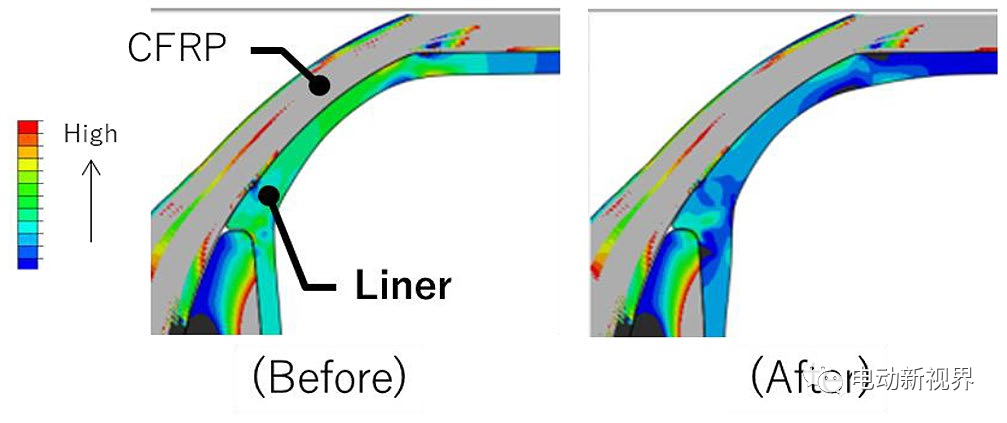
图6 形状优化后,衬里的应力
随着罐内的压力降低,罐内的压力降低,气体温度也会因为气体膨胀而降低。如果FCV在极低的温度下长时间运行,油箱压力和温度将极低,由于这些材料的线性膨胀系数的差异,CFRP和衬里之间出现间隙。当油箱遇到这些情况时,当衬里沿轴方向拉伸以试图填补间隙时,油箱衬里会产生高应力。这种应力与高压储罐的长度成比例增加。新的油箱采用了优化的衬里形状,设计以减少压力来解决这个问题。如上所述,对应力影响最大的因素是CFRP和衬里之间的间隙。当罐受压力时,衬里摩擦系数和CFRP的差异影响间隙处的材料相互作用。如果摩擦系数较小,衬里伸长均匀,衬里上的拉伸应力分布。相比之下,如果摩擦系数很大,那么衬里上的拉伸应力就会集中在衬里的圆顶区域。然而,使用实际的储罐,不能很容易、准确地估计摩擦系数。因此,这一发展使用X射线计算机断层扫描(X射线CT)来观察实际衬里的拉伸行为。为了便于观察伸长行为,一个特殊的金属球被附加在实际的罐内衬内。利用这些结果建立了一个CAE模型,并确定了一个优化的衬里形状。通过使用这个模型,衬里上的最大应力比之前的设计减少了大约30%(图6)。该模型能够根据对实际罐的检验,预测不同形状的罐在衬里上产生的应力。当填充多个明显不同体积的高压罐时,出现的问题是,预冷氢在油箱内部产生温度分布。这导致平均气体温度和平均内部罐温度之间的差异。这可能是在通信填充过程中降低充电状态的一个因素。这种差异的影响随着油箱容量的增大而增加,因为加油流量随着油箱容量的增大而成比例增加。优化温度传感器的布置和氢喷射角度,即使最大容量为最大的气体流量,也能检测平均气体温度。最佳条件是通过对实际油箱的实验来确定的。然而,使用CAE分析模型可以预测罐内的温度分布,并且比只使用实际的罐更容易开发(图7)。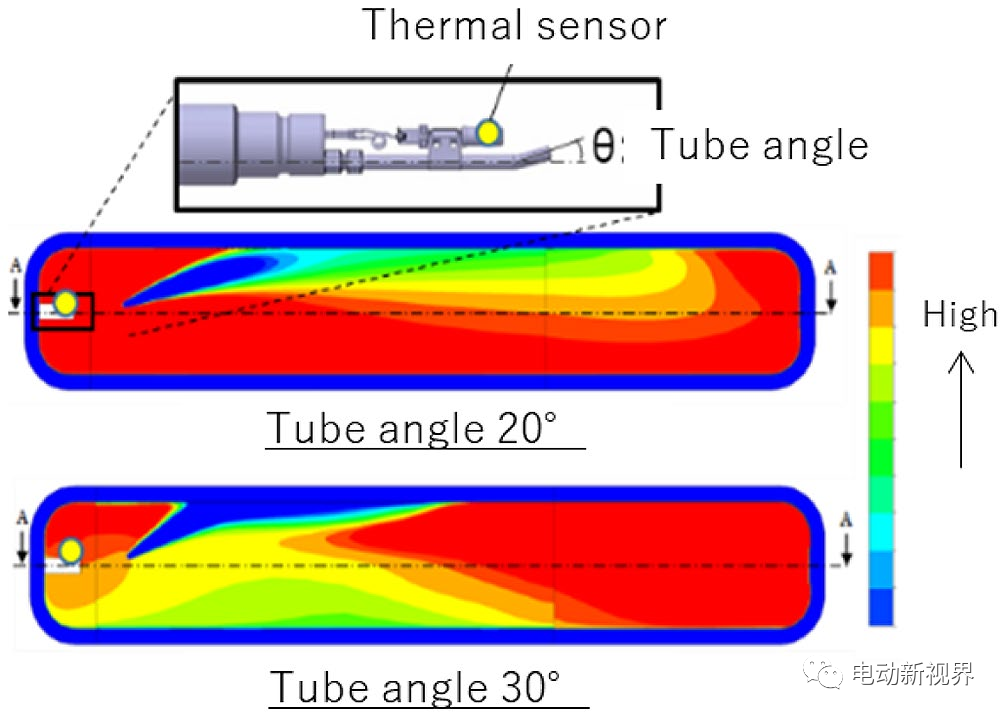
图7 油箱内的温度分配和加油SOC
降低成本和缩小规模
通过缩短制造时间,降低了成本。这是通过使用新的罐材料加速树脂固化,并采用新的罐阀和调节阀的加工方法来实现的。这些措施有助于显著降低新型高压储氢系统的制造成本。高压罐
与材料制造商合作开发了一种新的环氧树脂,以缩短固化过程的持续时间,同时保持锅的寿命。采用这种新树脂将固化工艺的持续时间缩短了三分之二(图8)。新树脂的主要成分是通用双酚A环氧树脂和末端的环氧基活性稀释剂。相比之下,传统树脂的主要成分是一种低反应性、高纯度的双酚F环氧树脂。新树脂通过提高反应速度缩短了固化过程。此外,使用活性稀释剂来降低初始粘度也达到了必要的罐子寿命。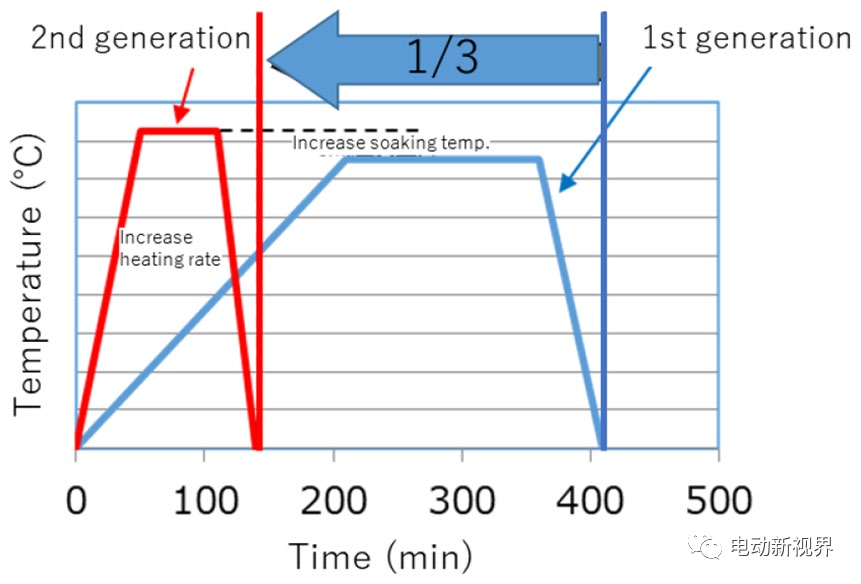
图8 储罐固化过程的温度转变
然而,增加浸泡温度被发现可以促进内衬里表面的氧化降解。在固化过程中,通过将加压介质转变为氮气来防止这种氧化降解。由此提高的生产力大大降低了成本。对高压阀门采用了一种新的生产方法,以提高了生产效率,降低成本。近网锻铝阀体
采用适合批量生产的连续铸材料。通过采用近网形锻造,材料产率比以前的阀门增加了20%(图9)。此外,通过优化锻件模具的形状,减少了锻造步骤的数量。为方便复杂形状的金属注射成型,不锈钢零件采用MIM,使材料产率提高了35%。内外结合采用AUS316L-H2,以对抗氢脆化和确保强度。此外,采用低频振动切割(LFV)解决工作性问题。LFV是一种通过恒定循环使刀具接触到工作的技术。它有助于防止来自切割芯片的干扰,并限制温度的升高。因此,与之前的模型相比,处理时间大大缩短,成本减少了四分之三。
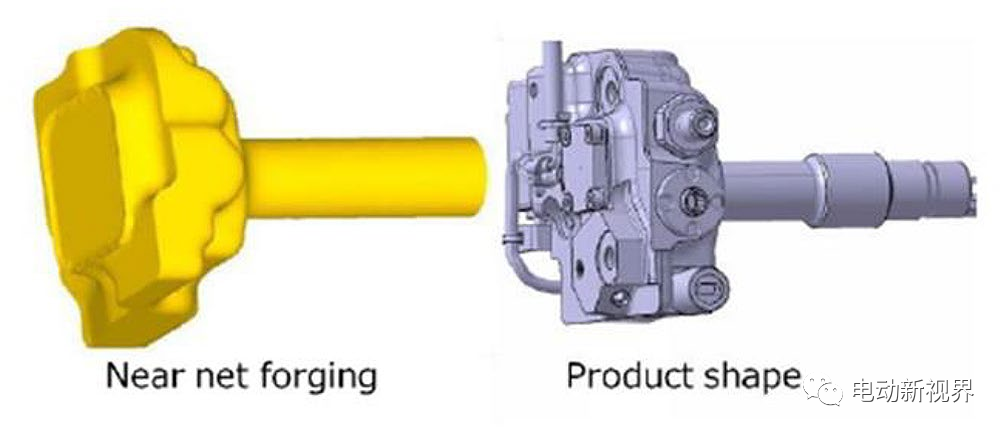
图9 接近网状成形的锻造件
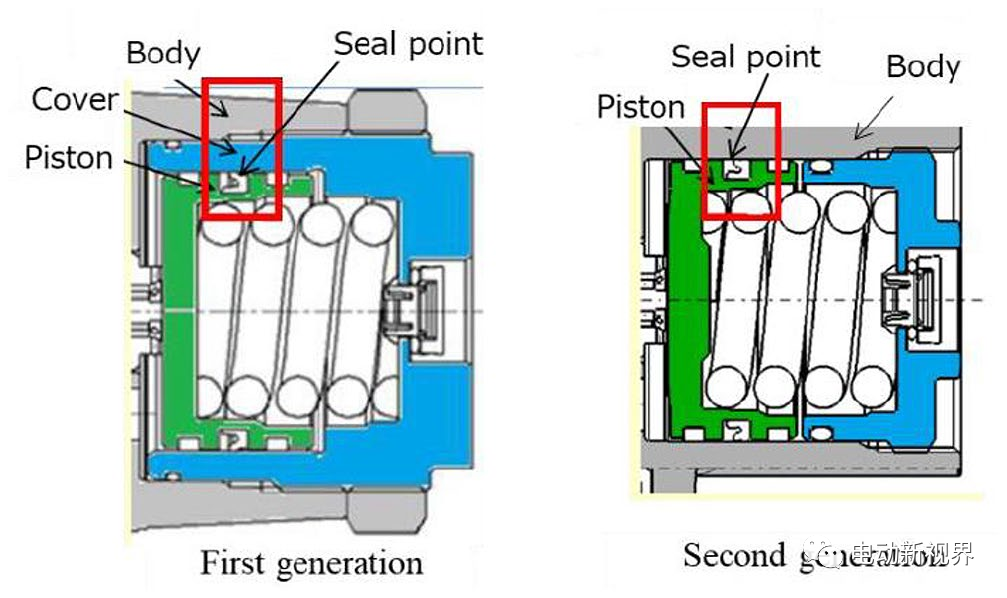
图10 调节器的结构
高压调节器
高压调节器的活塞密封部件需要承受数千万次的滑动循环。活塞在喷油器的打开和关闭操作后移动,时间间隔为10ms。因此,滑动部件受到高级的表面粗糙度控制,以及微米级的精密切割和表面处理。为新型高压调节器本体的滑动部件引入了一种高刚度车床,实现了微米级的精密切割。此外,调节器活塞密封组件的结构从三层简化到两层(图10)。因此,成本比之前的模型降低了三分之一。为新型FCV开发了一种新的高压储氢系统。该系统提高了性能,降低了成本,并有助于进一步推广FCV的目标。为了增加可用的氢气的数量,该设计采用了新开发的高强度碳纤维和优化的设计,从而减少了所需的碳纤维的数量。由此产生的氢罐设计实现了世界上最高的体积效率之一。通过优化衬里形状和成型条件,增加了可用氢的量。通过这些改进,尽管采用了更长的坦克形状,但新的坦克实现了与在极低温环境下的“MIRAI”坦克相同的耐久性。
作者:Hiroki Yahashi 丰田汽车公司
参考文献
1. Mizono, H., Nishiumi, H., and Kizaki, M., “Development of the Fuel Cell Hybrid Vehicle with 70MPa Hydrogen Tank,” JSAE Paper 62(11), 2008.
2. Mizuno, M., Ogami, N., Negishi, Y., and katahira, N., “HighPressure Hydrogen Tank for FCHV,” JSAE Paper 84-05, 2005.
3. Yamashita, A., Ishitoya, T., Kondo, M., and kuroyanagi, M., “Development of High-Pressure Hydrogen Valve System for FCHV,” JSAE Paper 24-10, 2010.
4. Yamashita, A., Kondo, M., Goto, S., and Ohgami, N., “Development of High-Pressure Hydrogen Storage System for the Toyota Mirai,” in SAE 2015 World Congress & Exhibition, 2015.