比亚迪刀片电池详解
比亚迪刀片电池详解
比亚迪刀片电池推出以后,确实在市场上引起了很大反响,其中争议最大的就是宁德时代也搞了针 刺实验,这里我们不对比宁德时代和比亚迪的电池技术孰优孰劣,宁德时代也有类似的 CTP 技 术(Cell To Pack,即电芯直接集成到电池包,而非像早期的特斯拉汽车采用的电池组),单从刀片电池结构来讲讲有什么特点。
说到“著名的针 刺实验”,有不少人认为只是单一的模拟电动车受到碰撞时的电池损伤情况(挤压、变形、穿刺等)。其实不然,针 刺实验主要还是考验电池内部隔膜破裂时的内部短路情况,毕竟类似电动汽车这种大容量电池在密闭的空间短路起火后,会非常迅速地发生爆炸,灭火装置基本起不到作用。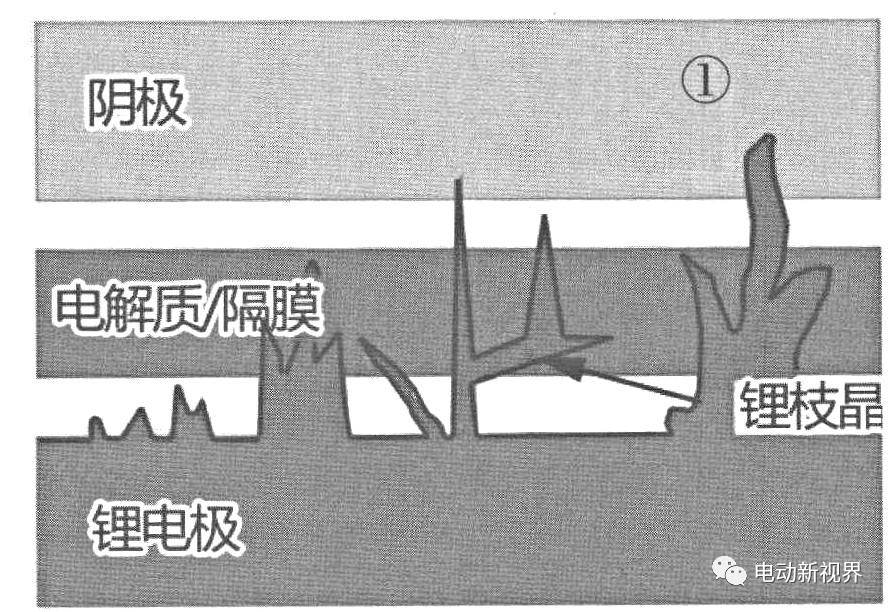
正常情况下,锂电池在充电时,锂离子从正极脱嵌并嵌入负极;而在过充、低温或者强电流等非正常情况下,从正极脱嵌的锂离子会在负极出现嵌入异常的情况,锂离子就只能析出在负极表面,我们称之为析锂(见图 1)。如果发生析锂现象,锂离子会在负极表面还原成不同形态的金属锂,其中有一种叫锂枝晶,它会随着析锂现象像树枝一样不断生长,且这一过程不可逆;当锂枝晶长到一定长度时,会穿破正负极间的隔膜,导致电芯的内部短路,极有可能引发热失控乃至爆炸,这是非常的危险的。这也是针 刺实验为什么要模拟电池内部隔膜被锂枝晶穿破的主要原因之一,即发生不安全情况下,如何保障车内乘坐人员的安全问题。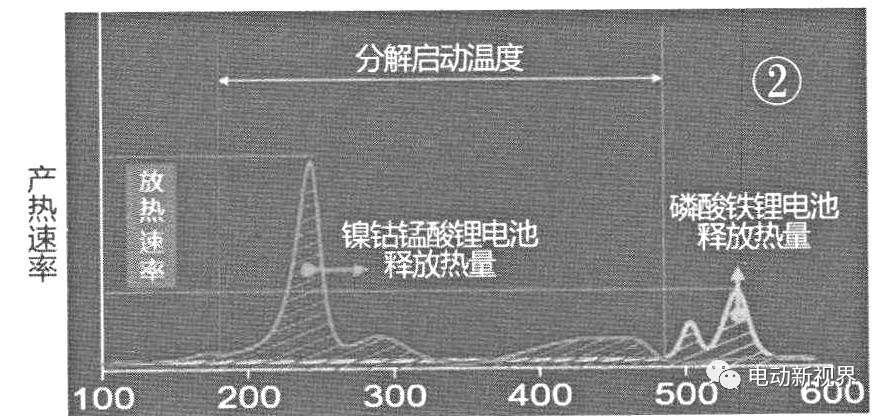
温度
而刀片电池本身采用的是磷酸铁锂电池,其特点是在温度接近 500℃时才会开始分解,并且在分解过程中不释放氧气,而三元锂电池(镍钴锰酸锂电池)的这个临界点只有 2000℃,两者放热速率和放热量也不一样(见图 2)。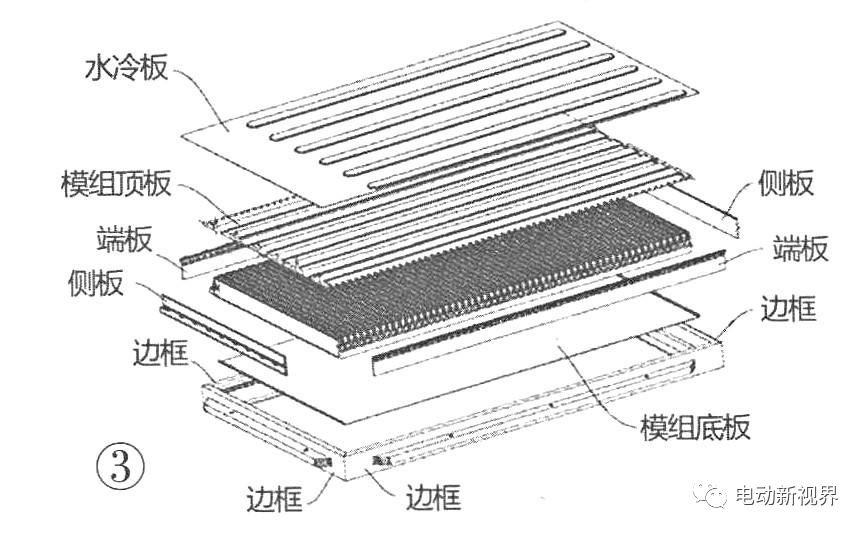
刀片电池本身也是一种 CTP(Cell To Pack,无模组)方案,属于结构创新而非材料创新。CTP 技术大幅减少了电池组中的电池模组,将十数个小的模组变成了两个或四个大的模组,从而省去了大量的零部件、连接线和壳体,在相同体积的电池组中容纳了更多电芯,提高了电池组整体的能量密度(见图 3)。而比亚迪的刀片电池组由于其电芯本身足够长,通过特殊的设计和组装工艺,可以实现更彻底的无模组化。首先刀片电池的长度达到了 960mm(比亚迪还在研究长度达到 2000mm 的极片及其封装技术),自然其内部的极片也是这个长度,而其他厂家的电池极片一般都在 700mm 甚至 500mm 以下。可见 960mm 的极片生产工艺还是有一定难度的。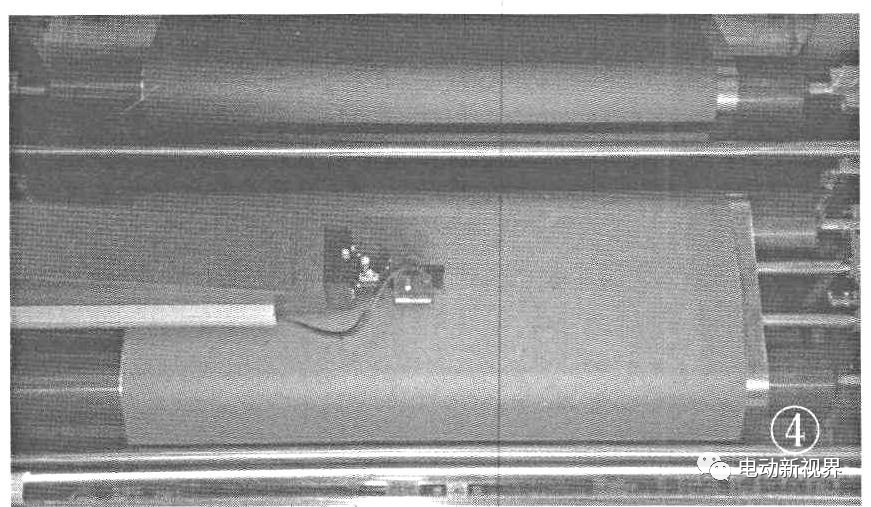
这是比亚迪旗下的弗迪电池工厂专门研制的涂布设备,可以实现 1300mm 宽度的极片双面涂布,单位面积的涂敷重量小于 1%,宽度尺寸偏差小于 0.5mm,速度为每分钟 70 米(见图 4)。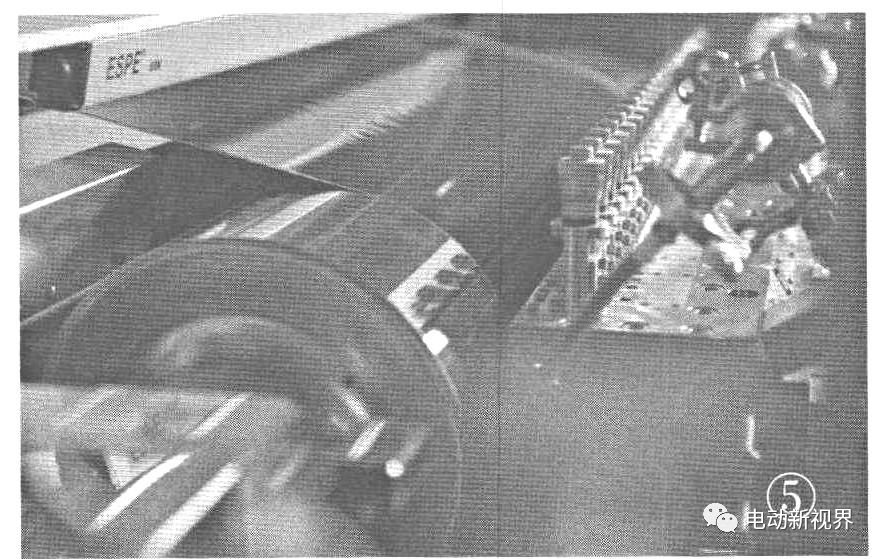
在辊压工序方面,弗迪工厂的辊压设备可以实现 1200mm 宽度的极片辊压,可以将极片厚度差控制在 2 微米以内,速度为每分钟 120 米(见图 5)。此外还有叠片工艺,相较卷绕工艺实现了更高的能量密度,但如此长的极片,要保证分切地一致、堆叠时对齐,才能保证生产出的电池拥有良好的一致性。通过完全独立自主开发的设备和裁切方案,弗迪电池工厂的叠片在 960mm 宽度的基础上,实现了每分钟 200 片的叠片速度和小于 0.3mm 的对齐公差控制。电芯密度解决了,但是磷酸铁锂的低温特性也是其短板之一,那么刀片电池又是如何解决的呢?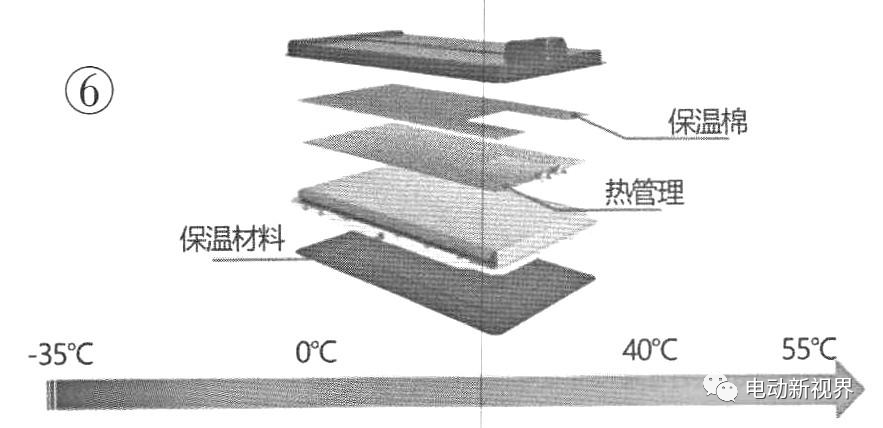
刀片电池组中全部采用了液冷式热管理系统,同时在电芯的上下部分采用了大面积的保温材料,以保证热管理系统可以良好运作(见图 6)。在极片材料上,比亚迪采用了纳米化的磷酸铁锂,通过减小材料粒径缩短锂离子的迁移路径,改善了电池组的低温功率性能。这样刀片电池组在-20℃的环境下,依然可以保持常温 90%的放电能力。而在充电时间和充电功率方面,在-10℃时,刀片电池的充电速度要比 NCM811 型三元锂电池慢 15 分钟左右,差距要比此前的磷酸铁锂电池改善了很多。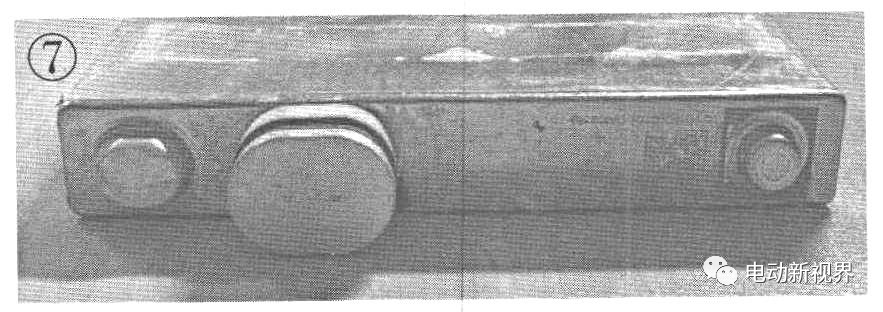
由于刀片电池也是一种 CTP 方案,它的电池组内部是由一个个电芯组成的,这些电芯并非直接放置在电池组中的,而是被各种连接件安装、并通过特殊胶水固定的。这种用来固定电芯的胶水可以牢牢地将电芯固定在电池组中,同时起到一定的导热、阻燃和缓冲效果,但反之,电芯被黏在一起之后就很难再拆开(见图 7)。当电池组中的单个电芯出现故障,就要直接更换整个电池组。而传统的模组化电池组,就可以通过更换单个模组来维修,而在刀片电池的电池故障维修中就非常麻烦了。目前唯一可行性的维修措施是通过超低温来破坏胶的强度,再从 CTP 电池组内将损坏的电芯取出。不过该维修技术实现还是难度很大、环境要求高、成本高,暂时还难以大规模的应用,只能尽量通过提高电芯一致性、降低单个电芯的故障概率来减少电池组的维修需求。早在2008年,比亚迪就一直在研究,如何解决电池组长宽比从3:8发展到10:6带来的阻耗问题、电路密度以及快充问题(见图 8)。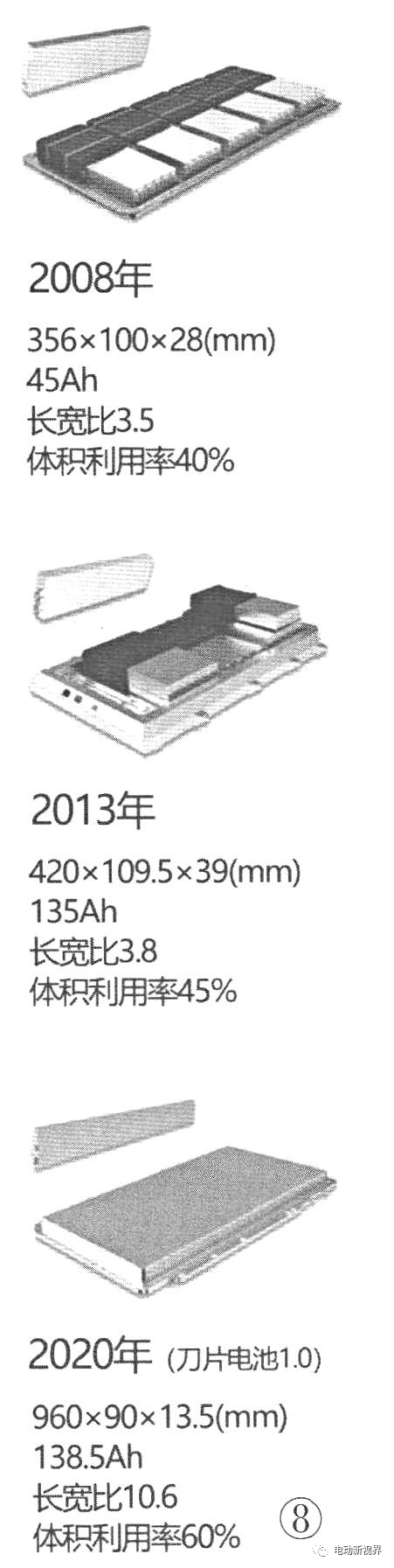
经过几代的改进,比亚迪才推出了刀片电池 1.0 版本,其零件数量从 1236 件减少至 756 件,体积能量密度和利用率也由原先的 40%增长至 60%。目前的技术范围内,刀片电池长度可在 600~2000mm 之间改变,且与电池包宽度一致,单个刀片电池内,包含多个容纳腔,每一个容纳腔包含一个极芯,容纳腔通过隔板隔开。看上去就如同几个电芯组成一个串联模组(见图 9)。基于这种内部多容纳腔与极芯的设计,比亚迪可以通过增减容纳腔的数目,来调节刀片电池长度,灵活多变,几乎覆盖了所有乘用车的电池包宽度尺寸,还支持有模组的电池包以及三元锂电池,能兼容更大型号的车辆和更大续航的车型。同时,封胶技术也在不断探索中,力争后续的刀片电池版本能做到一定程度的维修更换。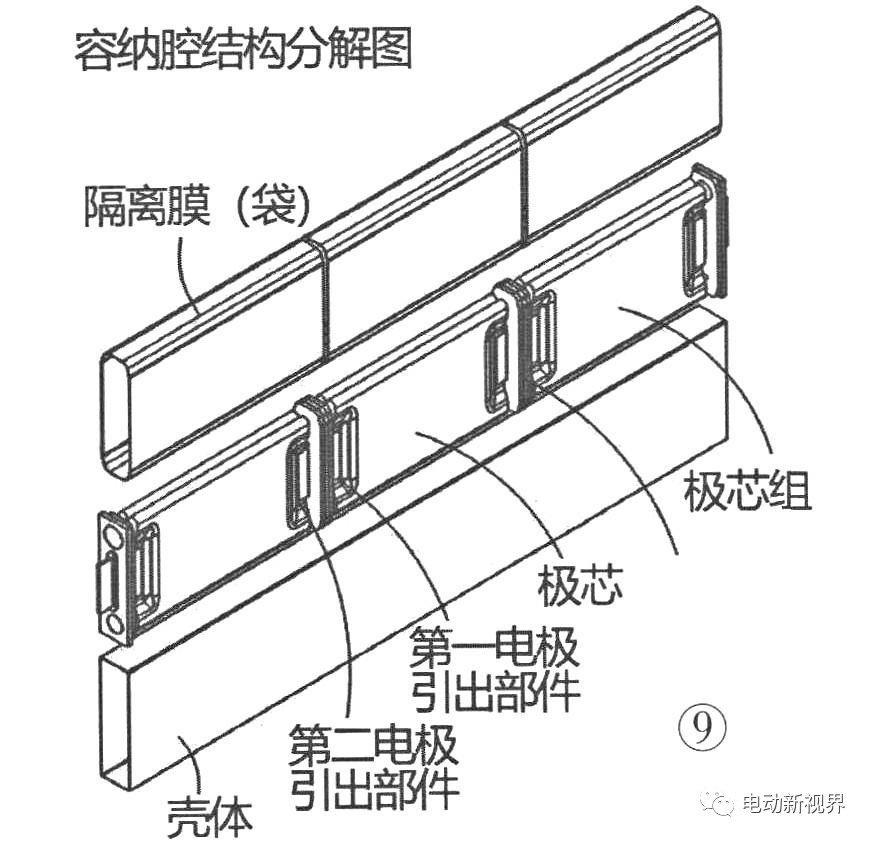
今年,刀片电池 1.0 版能实现续航 600 公里(汉 EV 两驱长续航版);而 2021-2022 年,刀片电池(搭载磷酸铁锂版)后续版更有望达到 700~800 公里。著作权归作者所有,欢迎分享,未经许可,不得转载
首次发布时间:2023-06-15
最近编辑:2年前