汽车轻量化材料应用分析
综述
目前汽车轻量化使用的材料主要有:高强度钢、铝合金、镁合金和碳纤维复合材料。从减重效果看,高强度钢-铝合金-镁合金-碳纤维呈现减重效果递增的态势;从成本方面看,高强度钢-铝合金-镁合金-碳纤维呈现成本递增的态势。
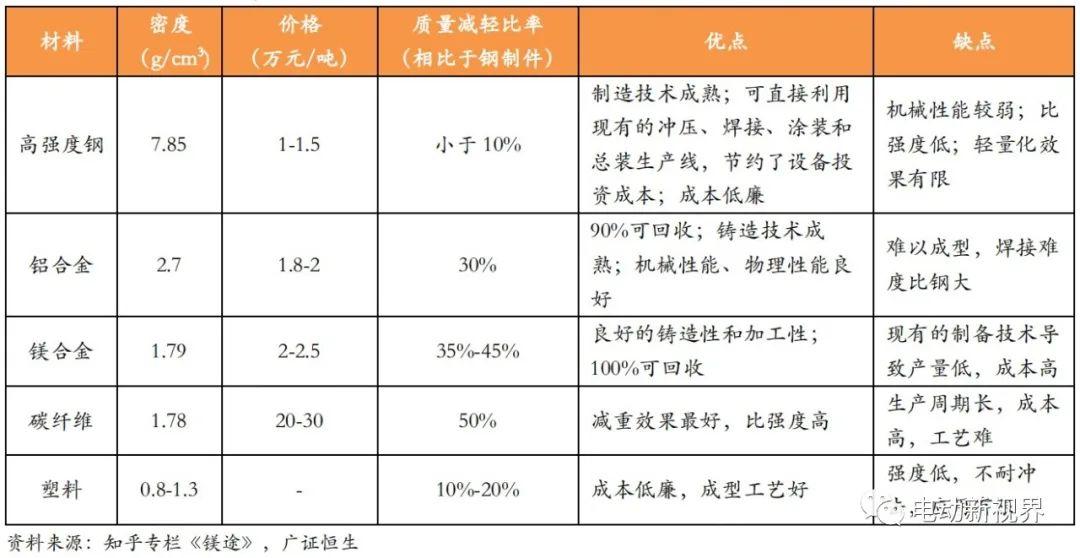
高强度钢
高强度钢是指冷轧 340MPa、热轧 490MPa 以上的钢。钢的强度越高,减重效果越好。相对于传统的340MPa 的材料,600MPa 级的钢种在理论上的减重潜能大约为 20%,800MPa 的材料减重潜能会提高至 30%以上。目前高强钢主要应用在汽车安全件、底盘及车身等方面。
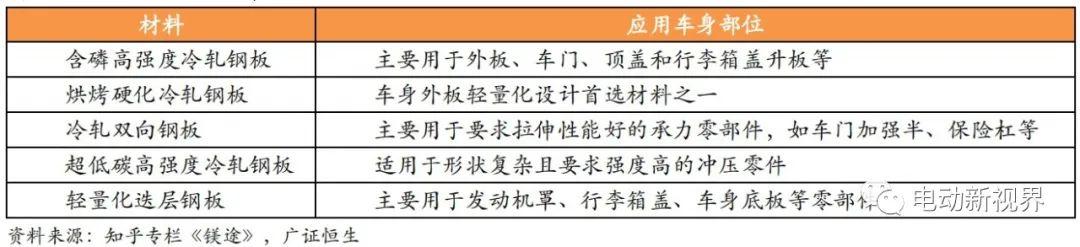
由于高强度钢相对于其他轻量化材料使用成本更低,各大车企以及相关配套企业对第三代先进高强度钢研究及资金的投入力度越来越大。这些钢种通过调节合金成分及热处理工艺,获得比现有先进高强度钢更高的强度和延展性能,连接能力也更加高效,同时成本也低。
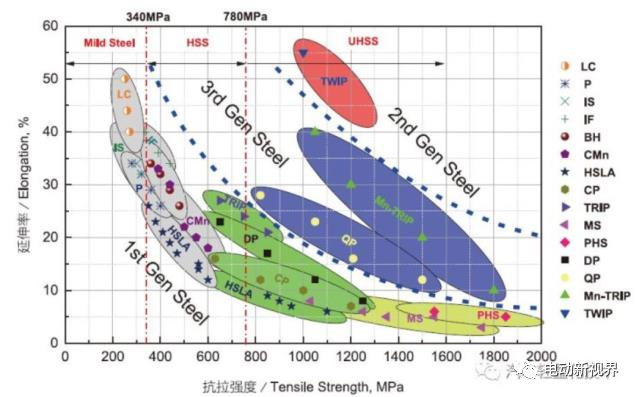
铝的密度是钢的 1/3,质量更轻,具有较高的比强度、很好的挤压性、很强的耐腐蚀性和高度的可回收性。铝合金在汽车产品上运用,减重的同时,能实现更佳的刹车性、更优的操控性、更好的驾驶舒适度和更突出的动力。铝合金型材生产工艺流程:熔铸、挤压、表面处理、深加工工。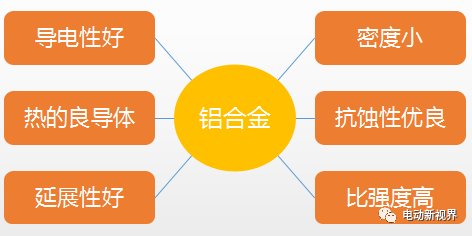
表4 铝合金生产工艺流程
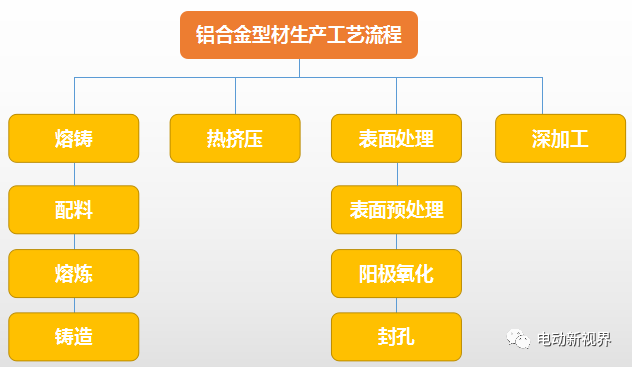
目前铸造铝合金约占汽车用铝量的 77%,可用于制造发动机零部件、壳体类零件和底盘上的其他零件;变形铝合金(锻造铝合金和铝合金板材)在车身零件及结构件的应用方面也发展较快,主要应用于发动机盖、翼子板、保险杠、车厢底板结构件、热交换器、车轮以及车身骨架等。汽车车身用铝合金材料主要包括:铜元素含量最高、硬度也较高的 2000 系;主含镁元素,又称“镁铝合金”的 5000 系;镁硅含量高、抗腐蚀和抗氧化性能好的 6000 系;镁锌铜含量高、可热处理合金、有良好的耐磨性和焊接性的 7000 系。汽车车身的不同受力部位会采用不同系列型号的板材、型材、管材及高性能铸铝等铝合金材料。表5 汽车用铝合金分类及应用
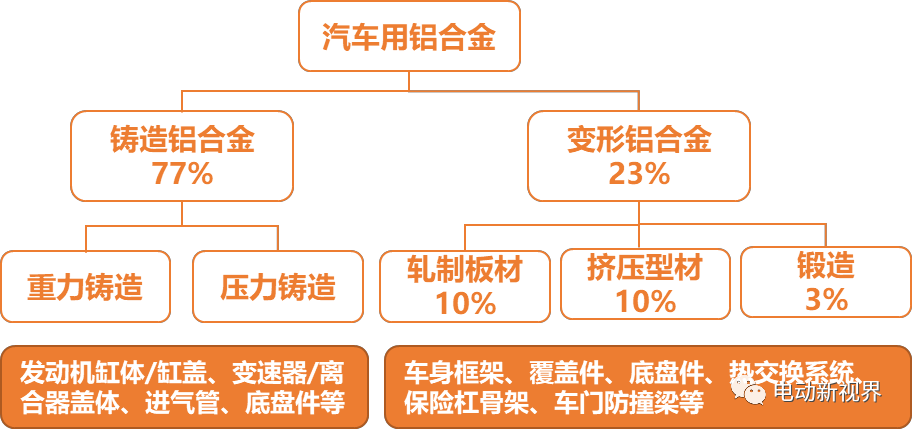
表6 铝合金材料、应用部件及工艺形式
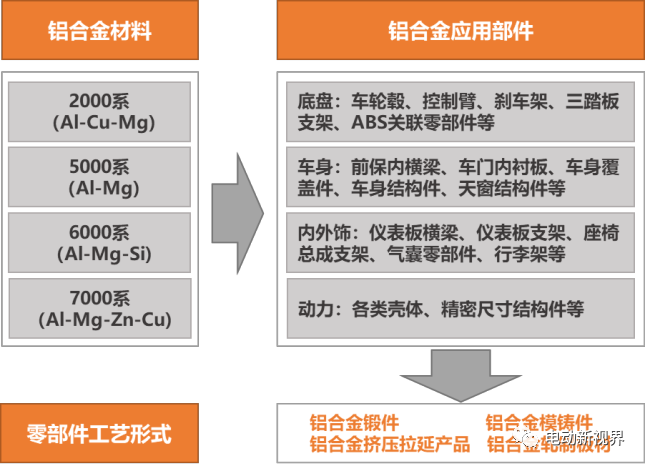
中国乘用车单车用铝量距离发达国家仍有一定距离。预计到 2020 年,我国乘用车平均单车用铝量将达231kg,年平均复合增速达 15%。预计 2020 年我国汽车用铝量需求为 510 万吨,按照车用铝合金 4 万元/吨市场价计算,市场空间可达 2500 亿元。2016-2020 年 CAGR 为 12%,其中 SUV 和新能源汽车将是汽车用铝成长最快的领域。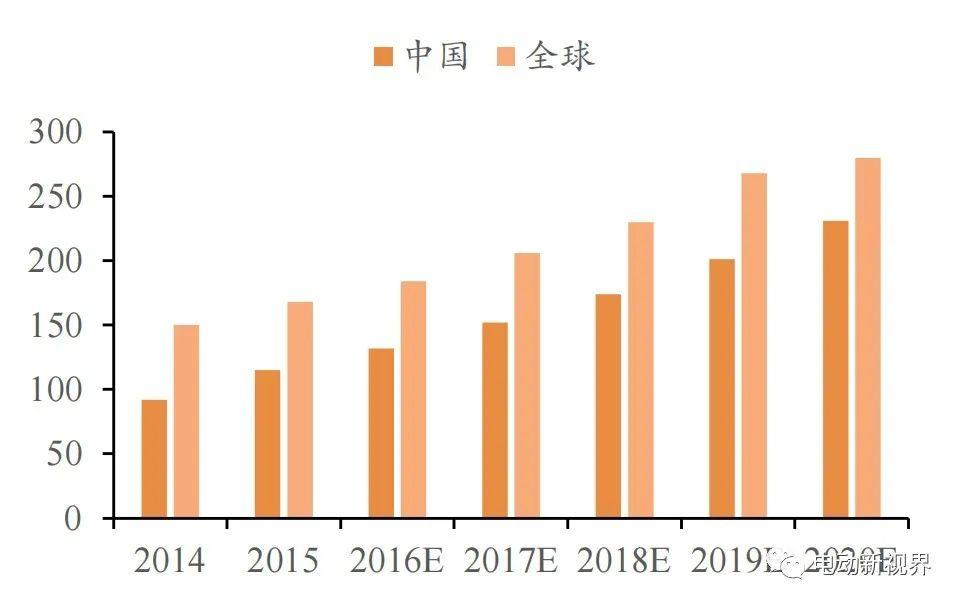
表8 汽车用铝需求量(万吨)
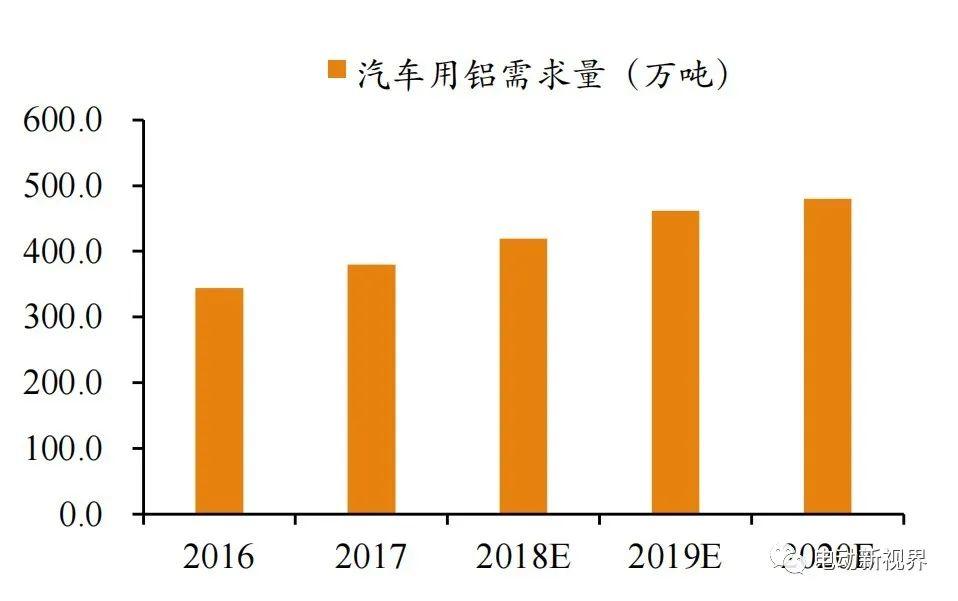
镁合金是目前商用的最轻的金属结构材料。镁的密度只有 1.8 g/cm3,是铝的 2/3,钢的 2/9,采用镁合金可在使用铝合金的基础上再减轻 15%-20%。镁合金具有优良的导电性、导热性、电磁屏蔽性能、高的比强度、减震性、加工工艺性能、易回收和有利于环保。现阶段 62%的镁合金制品应用在汽车产业上,镁合金在汽车上的应用主要集中于车身、发动机和内饰三大部分。镁合金在汽车上应用的零部件有 100 多种,主要分为壳类和架类两类零件。表9 镁合金具体应用及作用
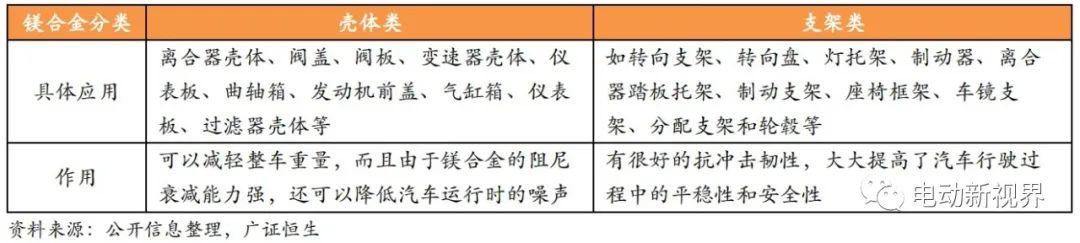
表10 欧美采用铝合金制造的部分汽车零件
北美、欧洲、日本等地汽车用镁持续增长,我国成长空间大。2015 年北美地区单车用镁量已达到 3.8kg,使用和研发中的镁合金零部件达 100 多种;日本单车用镁量高达 9.3kg,越来越多的在汽车的变速杆、座椅架等部位采用镁合金材料;欧洲车用镁合金铸件的使用量以年均 25%的速度增长,奔驰、通用、宝马的部分车型,镁合金用量已超过 20kg。相比而言,我国 2015 年单车用镁量约为 1.5kg。预计 2020 年国内单车用镁量目标为 10kg,汽车业对镁合金的需求量将达到 33.1 万吨。表11 2015 年部分国家与地区单车用镁量(kg)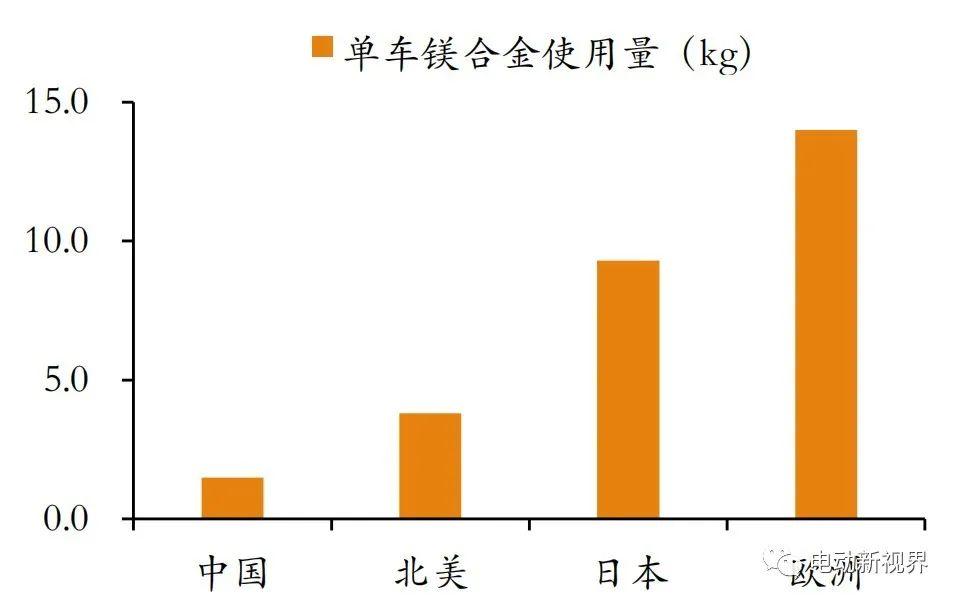
表12 汽车用镁需求量(万吨)
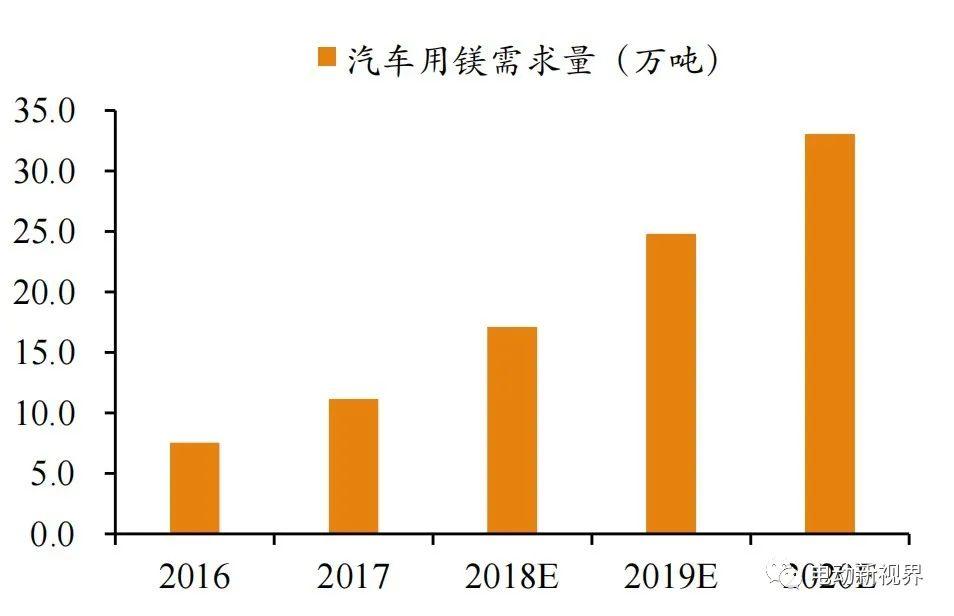
碳纤维是有机纤维经碳化及石墨化处理而得到的,一种含碳量在 95%以上的高强度、高模量的新型纤维材料。碳纤维是一种高强度、高模量的高性能纤维材料,不仅具有碳材料强抗拉力的特性,还兼具纤维软加工性,与传统材料相比,碳纤维密度不到钢的 1/5,强度是钢的 8 倍。碳纤维还对一般的有机溶剂、酸、碱具有良好的耐腐蚀性,具有很好的润滑性,摩擦系数小,导电性好,不存在生锈问题。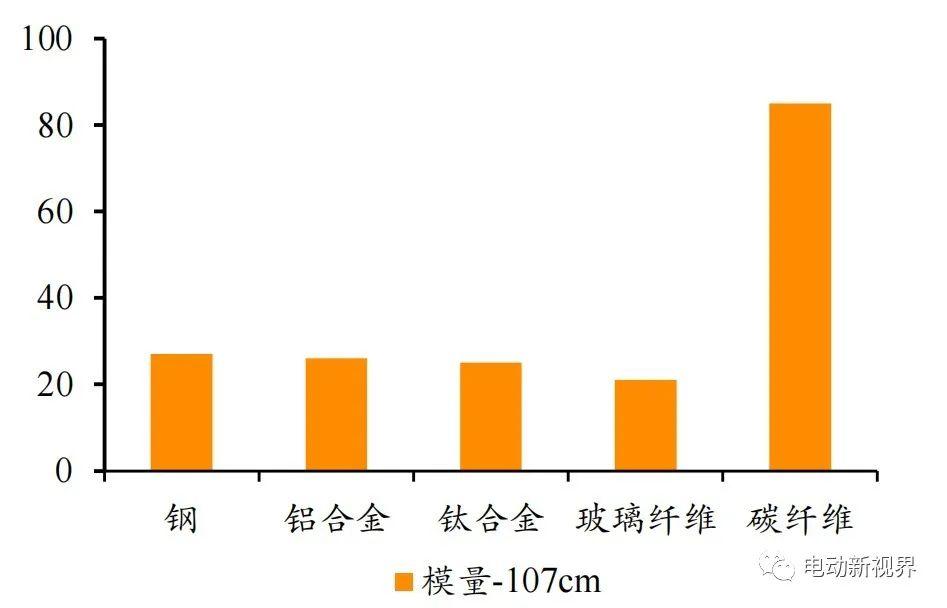
表14 不同材料的比强度
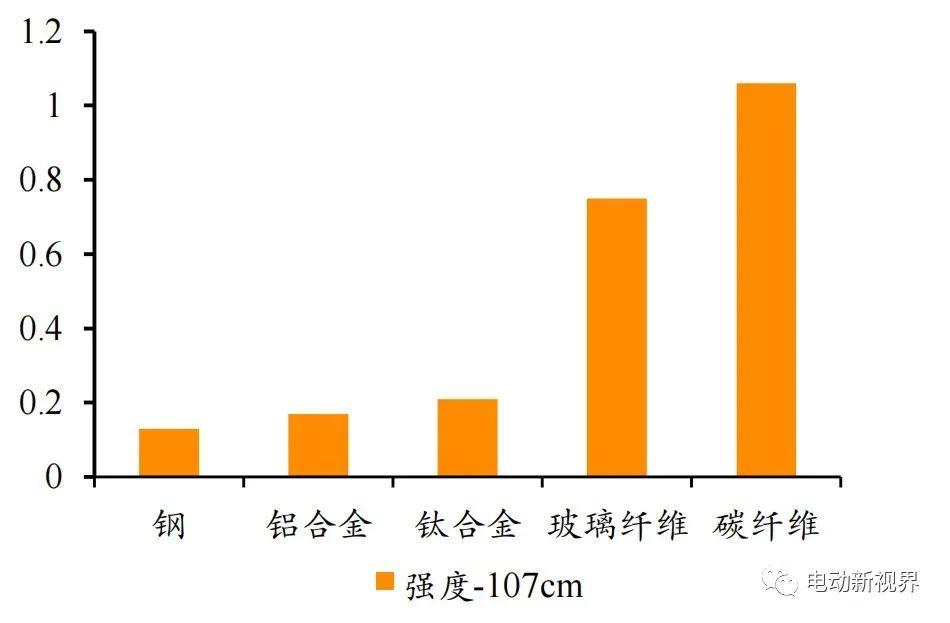
表15 不同材料的密度 g/cm3
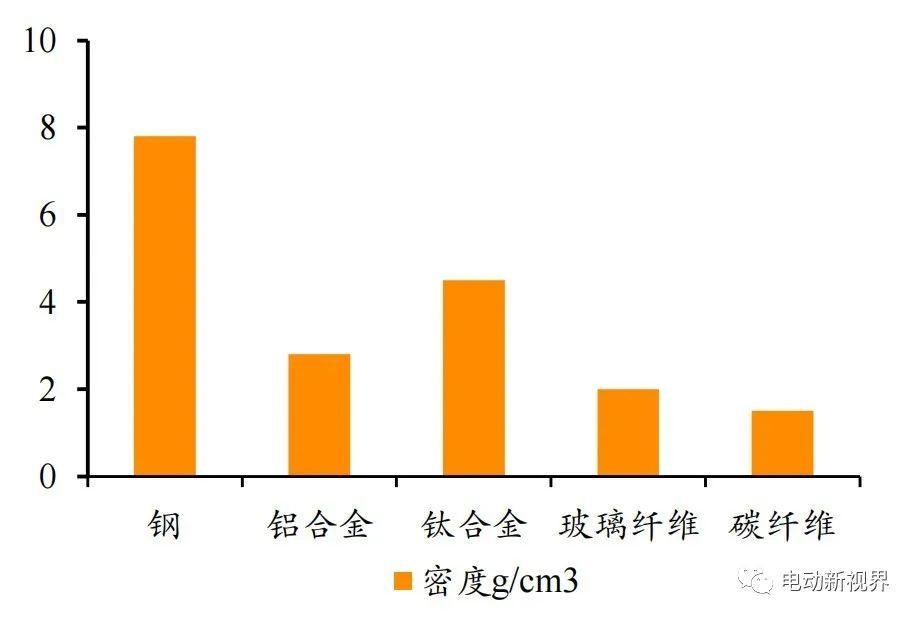
表16 不同材料的拉伸模量-GPa
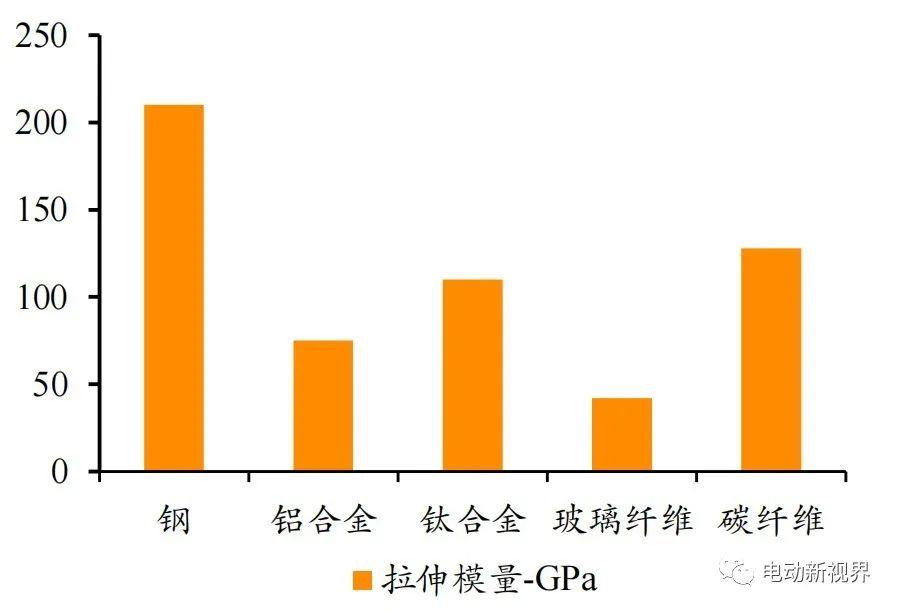
碳纤维复合材料(CFRP)在汽车中可应用于车身、底盘、车顶、车门、头盖、引擎盖、尾翼、压尾翼、中控台、装饰条、传动轴、板簧、构架、刹车片、内饰和外饰配件等系统。宝马 i8 车型使用复合材料模块化设计,全碳纤维的座舱(LifeDrive 架构),类似 F1 赛车的设计,整车重量仅 1480 千克。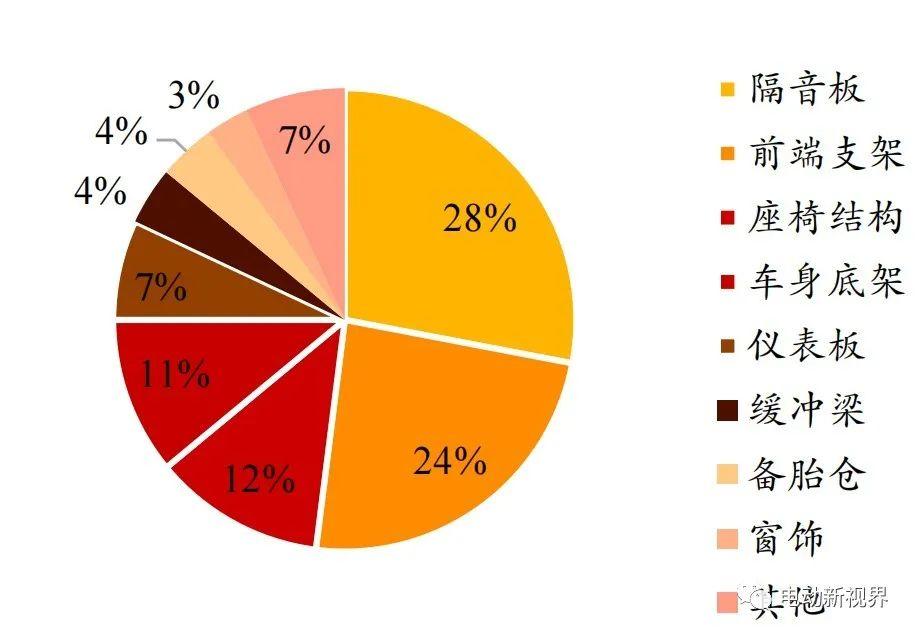
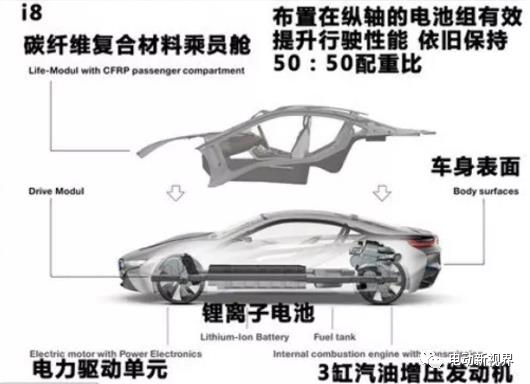
碳纤维复合材料在汽车上应用不但能满足轻量化的需求,还能提升安全性能,实现更好的驾驶性能,更低的组装耗费和更好的碰撞安全性。碳纤维复材的总体需求量将不断上升,预计到 2020 年,碳纤维复材的需求量可以达到约 20 万吨的左右。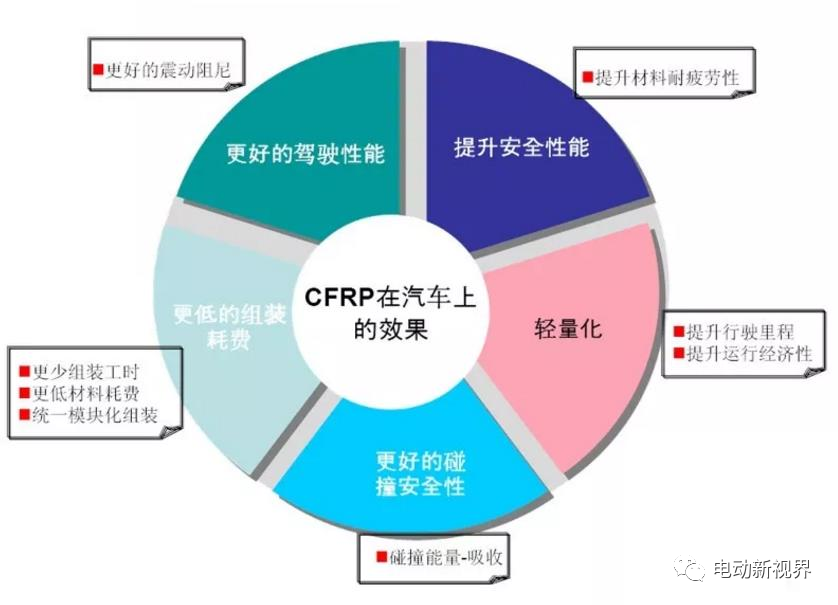
表19 汽车碳纤维需求量(万吨)
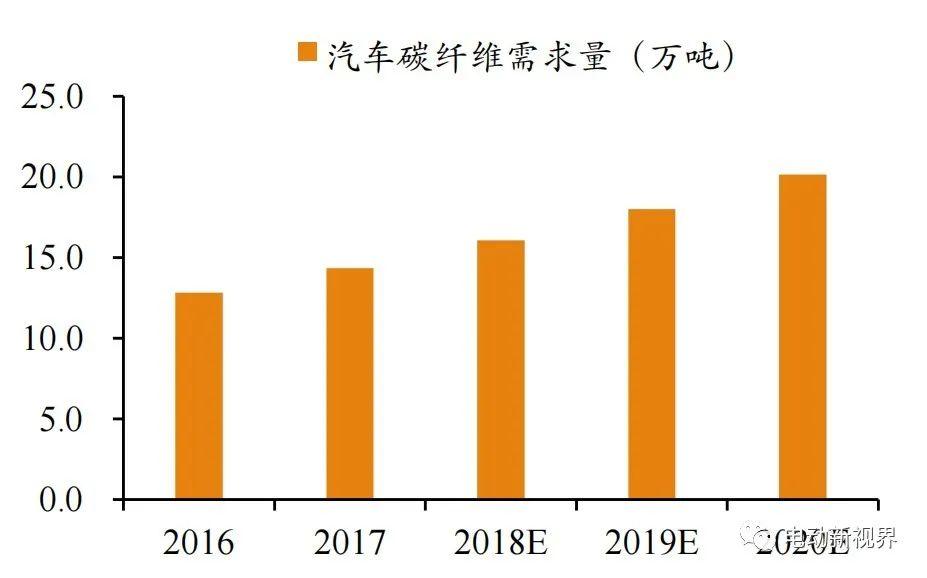
总结
在汽车轻量化材料中,铝合金材料综合性价比要高于钢、镁、塑料和复合材料,无论应用技术还是运行安全性及循环再生利用都具有比较优势。铝合金应用范围广,国内外全铝汽车的快速发展,特斯拉(TESLA)ModelS 系列车型中 95%结构采用铝合金材料。此外,上游供应稳定,配套产业完善,铝合金零部件厂商议价能力有保障。