在航空航天应用中,金属增材制造的技术和商业优势潜力巨大,这从前面几节所述的四大类应用中可以明显看出。但与此同时这些技术在航空航天应用中也面临特殊的挑战。本节重点介绍当前的主要挑战和未来的机遇。当前的一个主要挑战是航空航天工业缺乏金属增材制造的技术标准和认证方法。过去十年增材制造技术快速增长,造成了技术标准和认证方面的滞后,亟待完善,从而在整个行业达成一致,以确保航空航天领域应用的增材制造组件的可重复性、可靠性和质量。
▲图1 通过AM生产的具有复杂几何形状的金属零件:(A) AlSi10Mg分配器外壳和(B)Oerlikon AM 生产的大型散热器
欧洲联盟航空安全局(EASA)、美国航天局、欧洲航天局和联邦航空管理局等主要管理机构正在实施越来越严格的测试协议和认证,这些协议和认证是在关键任务和非关键应用中使用航空航天部件所必需的。其过程通常涉及生产过程的可重复性和制造组件质量的一致性,这两者目前在金属增材制造行业都是相当大的挑战,尤其是在大量生产组件时。与对传统工艺材料的全面理解以及存在的重要数据库形成鲜明对比的是增材制造缺乏大的数据库和一致的属性材料。增材制造组件认证过程的主要挑战是缺乏先验知识(之前无相关经验)、缺乏对增材制造过程的完整理解、缺乏对其详细的特性的了解、缺乏属性数据库以及关于故障机制的数据。目前,国际标准化组织(ISO)和美国材料试验学会(American Society of Testing Materials-ASTM)制定了一系列增材制造标准(如下表),这些标准在不断发展优化,新的标准也在不断出现,以适应航空航天领域增材制造应用的认证和设计要求。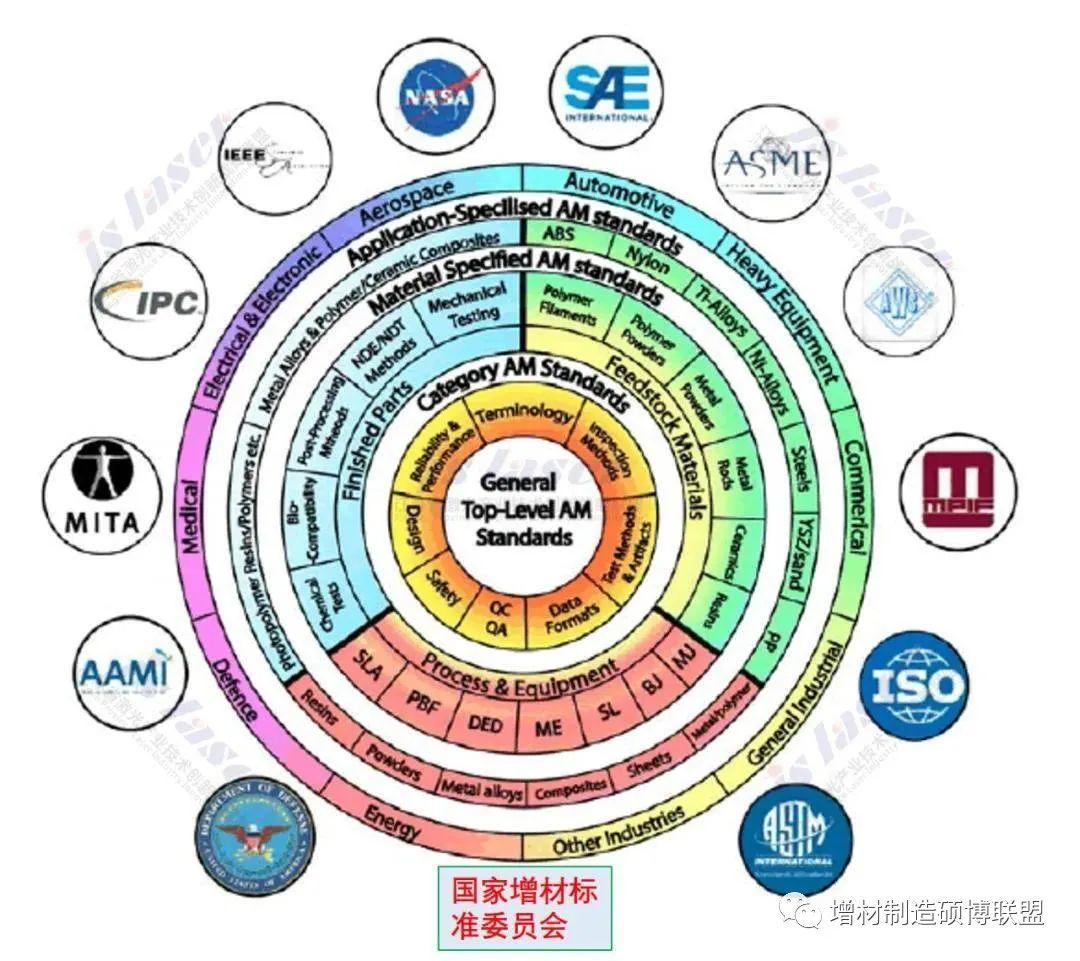
▲图2 上图—国家增材标准委员会组成,中—NASA当局及其总承包商的增材制造制品的展示,下—ASTMF42及ISO TC261的增材标准框架图
结构完整性对于航空航天关键任务的应用至关重要,包括高低温热循环模式下的动态载荷。对动态载荷的疲劳响应是增材制造在航天应用**别关注的问题。金属增材制造构件的静态机械性能研究相对较好,比如强硬度已经能相互匹配,并超过传统制造材料的性能。然而,与此相对的是诸如疲劳和蠕变等动态机械性能的研究相对较少,航空航天公司之间仍然缺乏测试数据报告。现有的增材制造文献中关于疲劳的数据表明,与常规制造工艺相比,孔隙率、残余应力和表面粗糙度是高循环疲劳区(high cycle fatigue-HCF)和低循环疲劳区(low cycle fatigue-LCF)试验场景中最大的问题,总体疲劳性能通常不达标。我们也欣喜地看到这些问题已经有所缓解,现阶段可在最小化缺陷的情况下提高部件性能,并实现与传统制造技术相当的机械性能(包括疲劳性能)。
▲图3 在热等静压和后续加热的轮廓孔隙率样品中观察到起泡效应
组装过程中的残余应力可能导致零件翘曲、开裂和机械性能下降,而这取决于所用材料、所用工艺参数、组装室的几何形状和方向、热历史等因素。类似地,孔隙度的形成很大程度上依赖工艺参数以及构建过程中的局部变化。金属增材制造中孔隙形成的各种机制已被确定,正是这些机制导致缺乏熔合和小孔孔隙,其程度和三维分布取决于各种因素。孔隙的存在降低了材料的延展性,但在疲劳载荷中尤其重要,因为孔隙会成为应力集中区,从而形成裂纹,导致过早失效。成品部件的表面粗糙度通常是不规则的,并且随着建造方向、工艺参数和其他因素而变化——这些因素会造成应力集中区和裂纹。所获得的材料微观结构通常是各向异性的,并且纹理取向取决于构建方向,从而影响机械性能(如图4)。需要适当的后处理热处理和热等静压工艺((HotIsostatic Pressing,简写为HIP)来改善这一点。
▲图4 研究样本的细节:a)样本的形状(“成品”表面是蓝色的,带点划线的表面是加工过的表面);b)样品系列A-E支架位置方向
所有这些制造缺陷仍然需要积极缓解和认识的不断深化,因此需要在增材制造工艺的所有阶段进行全链条质量控制,从粉末原料到环境气体纯度、工艺参数控制、工艺优化、现场监控以及每个单独工艺和所需原料组合的后处理。即使工艺和材料质量最佳,仍可能出现意外错误,需要进行某种加工和进一步的后处理(图5)。所有这些操作都会增加生产组件的成本,但绕过这些步骤会导致性能和可靠性的损失。热等静压已经在航空航天中广泛采用,它对于封闭孔隙、均匀化微观结构和提高部件的延展性非常有用。这也导致金属增材制造部件的疲劳性能大大提高,导致这类部件在航空航天制造中广泛采用。
▲图5 不同后处理后铝硅合金样品的力学性能与疲劳极限的相关性
▲图6 基于粉末的DED-L采用没有粉末进料模拟的熔池模型计算温度场和速度场:(a)Wei等人的模型,(b)Manvatkar等人的模型,(c)Knapp等人模型,(d)Gan等人的模型,(e)Wirth报道的基于COMSOL Multiphysics的模型。(f)Wei等人的模型
增材制造设计 (Design for AM-DfAM)可用于优化设计,从而获得最佳制造质量,最大限度地减少支撑结构和后处理。这也可以结合构建模拟来确定零件在构建平台上的最佳方向,帮助确定构建策略以最小化残余应力和由此产生的变形,并最小化支撑结构。这种模拟和DfAM方法很耗时,并且依赖于AM工程师的专业技能和所用计算机的计算能力,但这些是非常必要的。模拟还需要明确的参数输入,如合金的机械和液相线和固相线温度下的热物理性质,而这些参数相对而言不易获得。
▲图7 传热传质以及流体流动对于理解AM工艺和制造金属部组件的中心作用
虽然前文讨论了TO和晶格结构,但在实际应用中仍存在一些挑战。因为这些技术通常基于一组已知的输入和约束来优化设计,所以必须很好地理解航空航天部件的载荷路径。这些载荷路径以及组合的结构、热力、动态和综合环境在航空航天应用中并未被明确。这就导致其设计通常需要高设计余量来解决这些不确定性。
▲图8 使用各类型粉末的PBF模拟的熔池和粉末颗粒:(a) PBF-L由ALE3D,(b) PBF-L由OpenFOAM,(c) PBF-EB由LBM,(d) PBF-L由Flow-3D,(e) PBF-EB由Flow-3D,(f) PBF-L由Fluent
后处理是金属AM中经常被低估的关键步骤。对于具有精细特色尺寸的复杂零件,捕获的粉末可能是一个难以去除的难题。由于安全问题,处理这种粉末的难度就相应加大了。典型的方法包括旋转运动,从表面空腔和通道中敲打和吹出粉末。在CT扫描中可以观察到被捕获的粉末,但是如果在热处理之前不去除,它们可能会被永久捕获。进一步的后处理步骤可能涉及载体去除、表面抛光和其他热处理。对于所有后处理步骤,必须小心防止损坏(例如移除支架时),以确保零件符合设计且未有表面损坏。随着AM零件复杂性的增加,表面抛光、机械加工或其他加工方法进一步受到挑战,必须在工艺早期进行精心设计。4.6.无损检测(Non-Destructive testing-NDT) 由于这种种挑战,无损检测被用于所有由金属AM制造的关键飞行部件中。无损检测对于识别关键部件中的缺陷(如孔隙或裂纹)非常重要,可以使用多种方法实现,包括射线检测、染色渗透、涡流、超声波检测等。AM零件的这种无损检测也面临着一些新挑战,比如复杂的零件需要更优化的无损检测方法,而且一些传统工具与这种复杂的零件并不相容。此外,固有的表面粗糙度降低了一些传统无损检测工具的灵敏度。尽管有这些挑战,但有一种方法已经被证明足够”优秀“——X光计算机断层扫描(X-ray computed tomography-CT)。这种方法可成功用于检查裂纹、孔隙、捕获的粉末、设计几何形状中的偏差、热处理引起的翘曲等。该方法的一个优势就是在不同时间进行多次扫描,它能够提供零件随时间变化的各种信息,比如裂纹形成或磨损程度或可能发生的其他损坏的信息。这种方法提供的尺寸评估可用于评估进一步的适用性,甚至提供预期寿命的预测。
▲图9 CT揭示的工艺参数对激光粉末床熔化孔隙率的影响
该技术的主要限制是大型零件、厚壁部件的分辨率相对较低,铜等合金所带来的挑战,以及所涉及的时间和成本。此外,一些金属对x光的吸收性很高,使得它们的CT大部分都会无效。在这些情况下,建议使用较小的试样来检查工艺优化条件,与较大零件一起构建的试样可以很好地表明其质量。对于较大的零件,使用更高能量的X射线源在技术上是可行的,但这些射线源不太普遍。由于上述原因,现在许多流程监控工具正在开发之中,以在过程中做出改进而不是过程后再去进行缺陷识别。这篇综述展示了许多金属AM在航空航天应用中的成功例子。各种AM技术被用于航空航天应用,其中最受欢迎的是L-PBF和DED。DED用于构建量大的组件,除构建组件外,还可用于修复现有组件。L-PBF是应用于航空航天领域最为广泛的,它能够以高分辨率生产具有复杂几何形状的全致密化部件,具有小到中等的构建体积(图9)。并且金属AM在航空航天中的大多数应用都显示出了成本降低和生产时间缩短的优势。
▲图10 洛克希德马丁公司最大的卫星新坦克配备了一个三维印刷圆顶,图中一名工程师在该公司位于丹佛的太空设施检查三维印刷圆顶原型。最终的圆顶直径为46英寸,足够容纳74.4加仑的液体
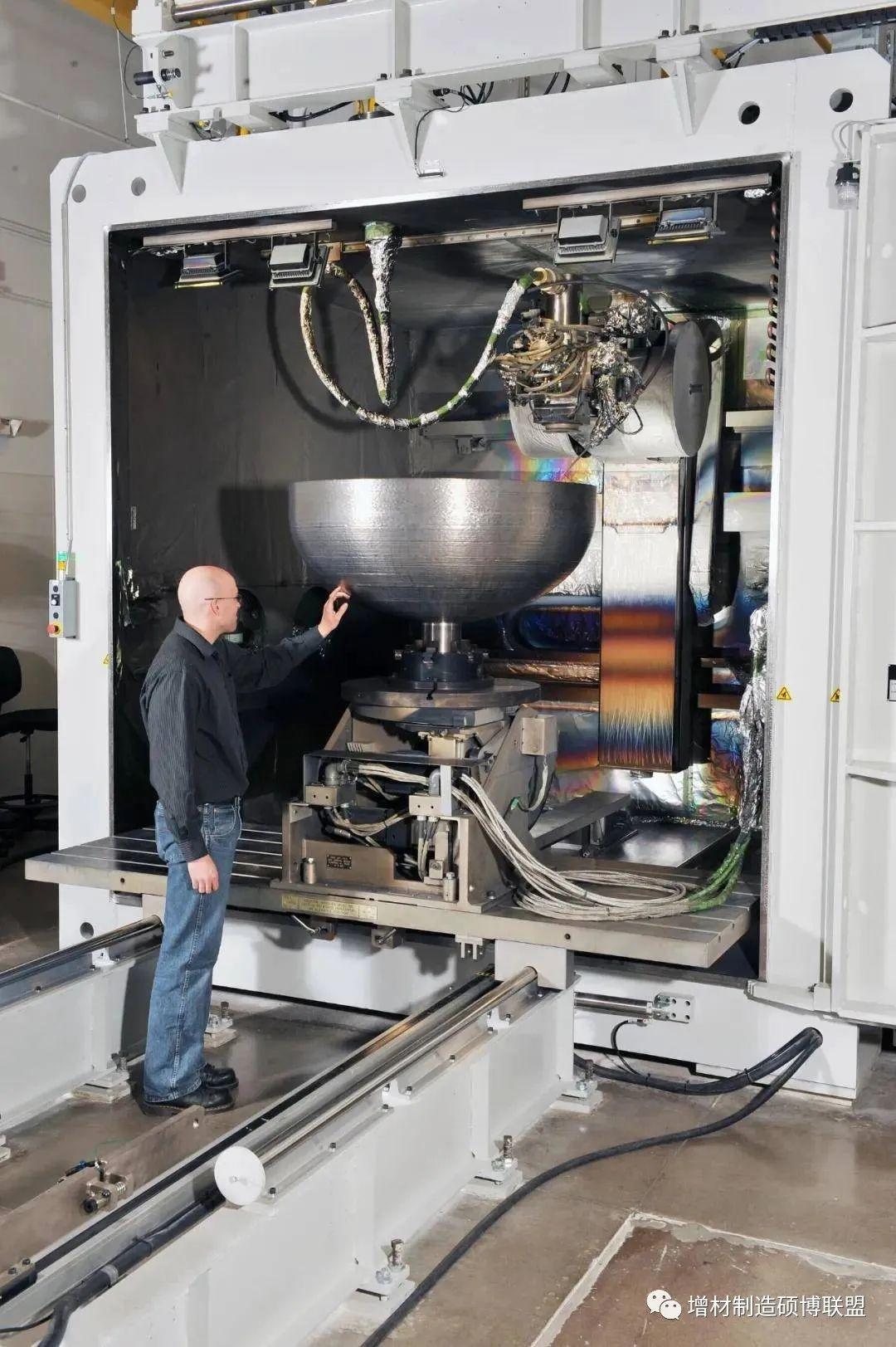
然而,金属AM面临零件认证、独特的质量控制要求、低批量生产率、使用的材料有限、后处理挑战、潜在的疲劳性能降低、供应链成熟度不够、机器成本高以及生产功能组件所需的专业性知识较多等挑战。许多悬而未决的研究问题仍然存在,在不久的将来或许会加强对这些问题的理解、并进一步优化发展。• 多功能组件,如集成电子器件和AM工艺中的传感器
▲图11 重要出版物中所讨论的航天航空领域AM相关的话题
未来重要的发展领域包括新型定制合金的应用、双金属和多金属加工和表征、详细的工艺-结构-性能理解、AM材料数据库、工艺认证、设计优化和工艺模拟。TO的应用和晶格结构的使用具有轻质化潜力,这也是航空航天的重要要求。在这两种情况下,对这种结构的设计和成功制造的深入理解会导致设计越来越复杂的部件可以不断改进和优化。TO已经在整个航空航天领域有所应用,强调部件的轻量轻质化。晶格结构具有独特和精确设计的特性,如能量吸收特性、重量轻和传热特性,在航空航天应用的设计改进方面显示出很大的潜力,有望在不久的将来成为航空航天应用研究的热门课题。这些优化的几何形状不仅可提升质量,还可以支撑结构或悬垂区域最小化与最少化,从而提高表面质量并最小化缺陷形成。通过找到最佳方向和突出潜在热积聚的区域,构建模拟有望在优化构建质量方面发挥越来越重要的作用,这可以为设计过程提供更多有效信息。虽然TO和晶格结构的潜力可用于减轻质量,但除了综合载荷之外,还需要对机械和热载荷路径有更好的理解,以确保该技术得到适当应用,并保证任务安全、成功完成。这是另一个研究领域了。正如这里所强调的,金属AM在航空航天领域的主要优势是降低成本和交付周期。质量减少也是优化设计或使用多种合金的一个重要特色,但是这些技术需要深入理解,其性能也需要被更好地定义。此外,组件整合是该行业的一大优势。金属AM中固有的零件复杂性允许组件内部的高复杂性,包括传热应用的通道和高表面积。AM也在许多大规模应用中得到了证明,因此规模将不再是一个限制。金属AM在航空航天中的这些优势为该领域更广泛地采用这一技术提供了巨大的潜力,这将进一步推动待克服的挑战一个个被攻克。原文链接:
Metal additive manufacturing in aerospace: A review, Material and Design
https://doi.org/10.1016/j.matdes.2021.110008
参考资料:
1.End-to-end process of hollow spacecraft structures with high frequency and low mass obtained with in-house structural optimization tool and additive manufacturing. INCAS Bull., 9 (3) (2017), pp. 13-20.
2.Decision methods application to compare conventional manufacturing process with metal additive manufacturing process in the aerospace industry. J. Braz. Soc. Mech. Sci. Eng., 39 (1) (2017), pp. 177-193.