故障诊断学习 | 振动信号,为何如此的“与众不同”?
注:本文转自卓微科技公 众号,成都卓微科技有限公司(卓微科技)致力于设备健康管理系统的关键器件和核心软件研发。卓微科技的核心团队在传感器领域、设备状态监测软件开发和应用方面具有丰富经验。
上一节介绍了什么是机械状态监测与故障诊断,本节将对常见状态监测与故障诊断技术,振动信号为什么在机械设备状态监测中与众不同、基于振动信号实现状态监测的过程进行介绍。
一.常见状态监测与故障诊断技术
1. 基于振动信号的方法
通过振动数据采集器对所监测设备采集振动数据,利用专业的振动数据分析仪分析振动数据,其会提供如图1所示的各种波形图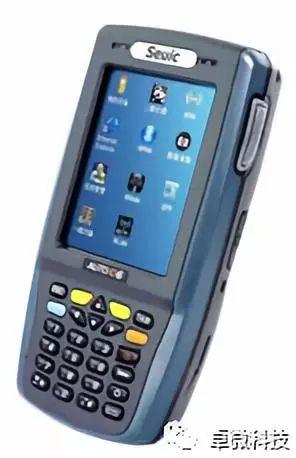
图 1 某型振动数据采集分析仪(常称为:数采器)
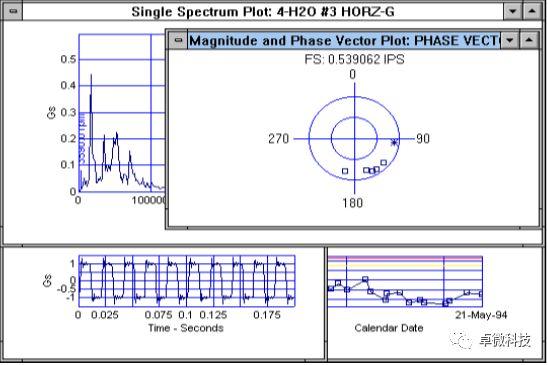
图 2 数据分析仪分析后得到的波形图
2. 润滑油分析
通过对润滑油的各种理化指标进行检测,如各种元素含量,金属颗粒大小和形状等。从而掌握设备的健康状态。
图 3 润滑油分析
3. 基于温度监测的方法
左上图为红外测温,左下图为红外成像。右边两图为维修前后的红外成像图,可以看到左边维修前在联轴器处图像比右边维修后颜色更亮,表示温度更高。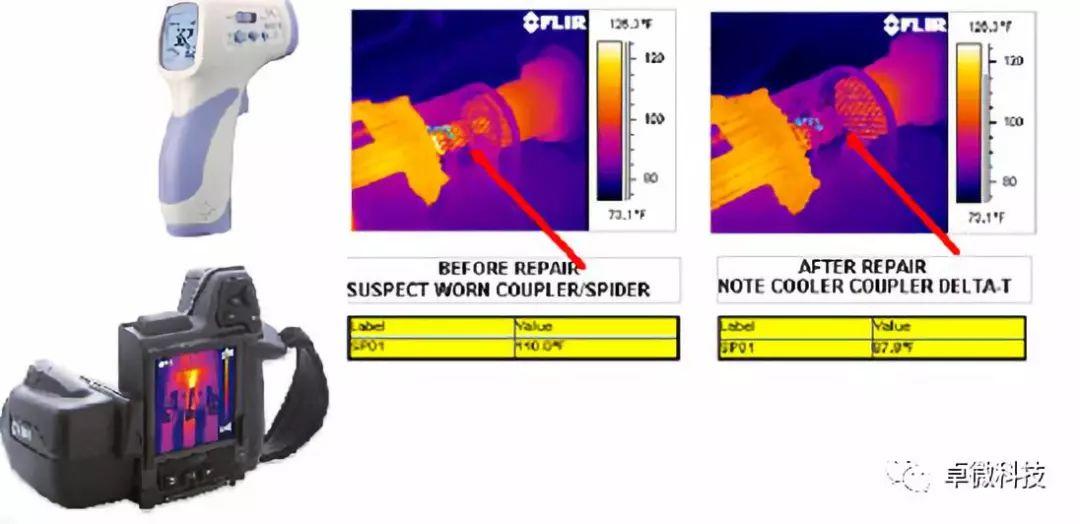
图 4 基于温度监测的方法
4. 基于电流的电机故障检测
通过对电机的电流进行检测(通常是通过上图右边的钳形表),可以检测出多种电机故障,如断条,匝间短路等。
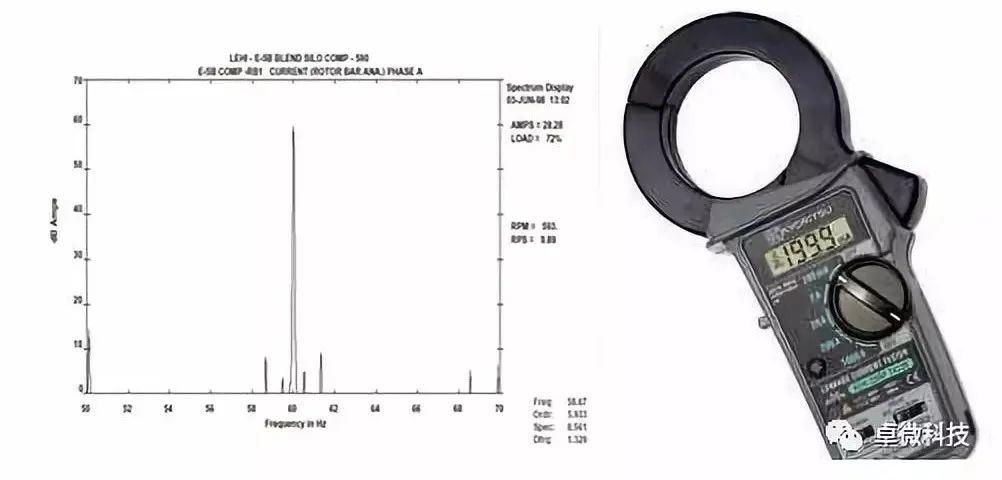
图 5 基于电流信号的电机故障检测
5. 转子现场动平衡技术
转子不平衡是指,转子的质量中心不在转子的旋转中心上,从而造成很大的离心力降低机械效率或损坏机械。而转子动平衡就是通过加重或减重让转子质量中心发生改变从新回到旋转中心上。传统的转子动平衡是要把转子从设备上拆下后,运输安装到动平衡机上去进行转子动平衡。采用现场动平衡技术,可以不用拆卸,直接在现场进行转子平衡。从而大大节省时间和费用。上图显示了现场动平衡时仪器传感器的安装情况,及不平衡时转子的摆动状态。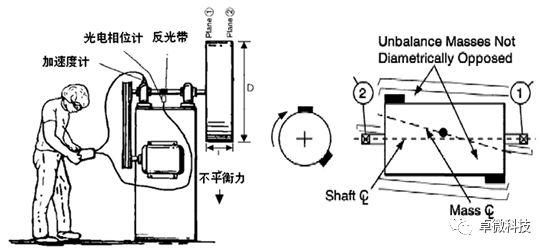
图 5 现场转子动平衡技术
6. 机器不对中检测
机器不对中,指两个机械部件的运动中心不在一条直线或一个平面上。如左上图表示两根轴不在一条直线上,这样用联轴器把这两根轴联接起来后就会产生很大的内部破坏力。右下图表示用仪器进行皮带轮的轮毂进行对中检测,以保证两轮毂运行在一个平面上;右图表示对一个联轴器进行激光对中检测,以保证两根轴在一条直线上。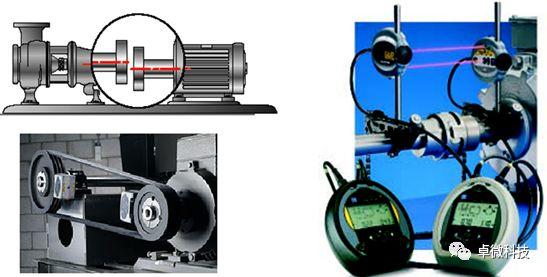
图 6 现场转子动平衡技术
7. 其它技术
状态监测与故障诊断技术还有很多,符合在设备运行中或基本不拆卸全部设备的情况进行检测的技术都可归为状态监测技术如:l 内窥镜
l 超声波
l X光检测仪
l 铁谱
l ………
二、振动信号为什么在机械设备状态监测中与众不同
机械状态监测技术中,如上所述可以通过各种方法,测量多种多样的物理参量来监测机械的状态及诊断故障。在所有的可监测的物理量之中,振动信号具有特殊的地位。翻开任何一本机械故障诊断的书籍,你会发现大量的内容都是振动相关的。也许你会产生疑问,这本书为什么不叫机械振动信号分析而要叫做机械状态监测故障诊断?
那是因为振动信号的监测、分析是机械状态监测中最重要的方法,也是机械状态监测中最有专业度的物理量之一。是什么让振动方法如此的“与众不同”呢?主要有以下的原因:适应的故障面广:在国内外的资料统计中,许多种类的机械故障通过振动信号可以确认,几乎所有的机械故障振动方法都有诊断帮助;
经济效益突出:经过统计,采用振动方法能减少大约50%的维修维护费用,其它单一方法不超过20%(不同行业,不同机组会有一些不同);
性价比高:很少有什么方法能像测量振动这么简便和易于实施,且只需要很小的投入;
振动力学、转子动力学等众多学科的理论支持;这些理论的指导,可以使得诊断摆脱完全依赖经验的限制;
各个工业领域大量成功经验:大量的实际成功案例可以显著的降低诊断的难度。
正因为以上这些原因,振动信号的检测与分析几乎成了机械状态监测与故障诊断的代名词。
振动为什么能诊断机械故障?振动为什么能诊断机械故障,对这个问题的认识决定了运用振动诊断机械问题的高度。很多人认为振动能反映和诊断故障是不言而喻的:振动大了就是有问题了,振动小了就没有问题(虽然实践中大部分情况下是这样的)。事实上用振动方法来监测和分析机械故障的原理不是这么简单,振动能够反映机械运行状态和分析故障,本质上是因为振动对应着机械部件所受的力。
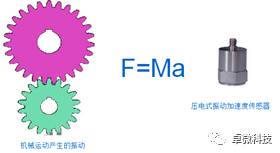
图 7 力产生振动示例
如上图7所示:(为了简化问题,我们这里用振动加速度传感器举例,不涉及振动速度和振动位移)使振动产生的力,由力学定律F=Ma(力=质量*运动加速度)可知,在质量确定的情况下力和加速度a成正比。而在工程上直接测量力在大部分情况下非常困难,而通过压电式振动加速度传感器能够很容易的测量到物体的振动加速度,从而间接反映机械各部件所受的力(包括力的大小,力的方向,力的形式等)。除了质量外,从力到振动还受到物体刚度、阻尼的影响。因此,用振动信号分析的方法来进行故障诊断并不是只看振动的大小。比如:把一根钢丝拉断需要很大的力,但反复在一个位置用较小的力来回折叠这个钢丝却很容易弄断这根钢丝。这说明力的不同形式对材料的破坏效果是不一样的。
所以,由振动信号分析机械的机械状态和故障,其本质是“间接的”分析振动产生的力、振动部件质量、刚度、阻尼及其交互作用。而任何一种机械故障,都会引起上面四个要素的变化,从而导致振动信号(大小、频率、方向、相位等)发生变化,由此,我们可以从振动信号的变化反向推导出故障情况。例如:转子动平衡故障主要变化的是转子旋转时的离心力;轴裂纹故障主要引起的是转子的刚度变化;这些都会引起振动信号的变化。
三、基于振动信号实现状态监测的过程:振动信号的采集和处理分析
图 8 一个简略但完整的振动信号采集和信号分析过程
一个简略但完整的振动信号采集和信号分析过程如上图8所示。先由振动加速度传感器采集原始的振动数据;振动原始数据形成时域波形(振动大小随时间变化的波形),这个波形主要根据振动的大小,波形的形状等对机械状态进行定性分析(是良好,优秀,注意还是故障报警);然后通过FFT(快速傅利叶变换)获得右下角的频谱图,这个波形主要根据振动的信号频率构成对机械状态进行定位分析(哪个部件出现故障,是哪种种类的故障),主要的分析方法是和左下角的机械设备的典型频谱图进行比对(如图中是典型的机械零部件松动故障信号频谱图)。
值得注意的是,故障可以由不同的方法或不同的信号处理方法检测到,但不同的方法和不同的信号处理方法对不同故障及相同故障不同严重程度的敏感度是不一样的。如滚动轴承常见的点蚀剥落类故障,其发展过程及对应的检测方法见下图9所示: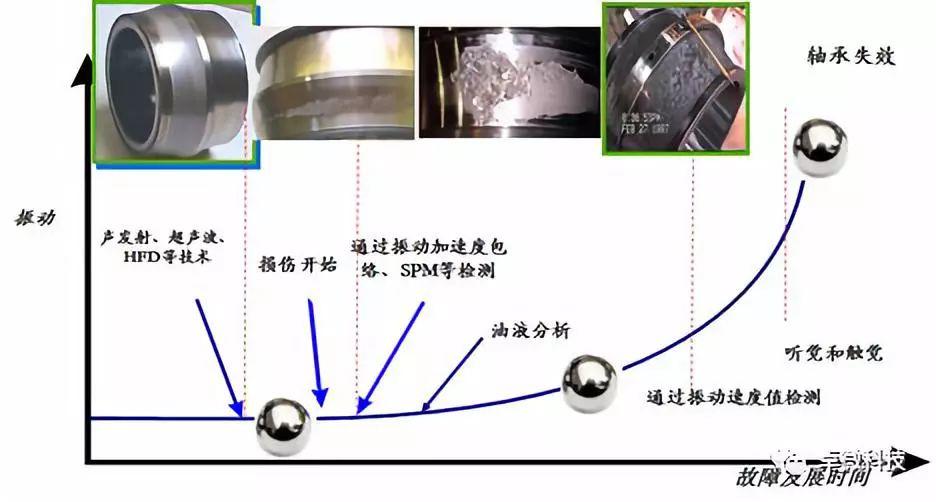
图 9 滚动轴承点蚀剥落过程及对应监测方法
在最早期的时候,滚动轴承受交变应力出现故障是在表面微米级下出现,从轴承表面肉眼是看不出来的,这时候可以用声发射,超声波,HFD(高频检测)等检测技术发现;再往后,表面微小损伤出现,可以通过振动加速度包络技术或SPM(冲击脉冲)检测出来;再往后,油液检查可以反映异常;故障进一步扩大,可以通过振动速度值检测出来;最后可以通过听觉和触觉及温度等方式检测出来。
通过以上例子,我们可以知道:
1. 不同的检测方法或信号分析方法,都可以检测同一类故障,但不同故障时期对不同检测方法或信号分析方法敏感度是不一样的。因此,我们在实践中应该尽可能采用多种方法或信号处理方法来进行检测,以更好的判断故障的严重度并防止漏报、误报故障;
2. 在状态监测工程应用中,应尽可能早的发现故障,这样在对设备的维修维护中更有主动性(如有更充足的时间安排备品备件,安排停工检测期等)。
下节预告:下节将对振动信号基本知识进行介绍(振动系统、振动信号三要素、从时域到频域的变化、振动监测入门指南)