金属增材制造(Metal additive manufacturing AM)包含添加材料从而生产一层层的金属组件的制造技术。这项技术的重要特色就在于其商业化和性能优势,使得其在航空航天工业发展迅速、应用广泛。 ▲图0 本文的Graphical Abstract
具体而言,航空航天应用中金属增材制造的基本优势包括:成本和生产周期显著降低、材料新颖和设计解决方案独特、高效轻量的设计可减轻部件的质量、通过多种方式整合各组件以实现性能增强或风险管理(例如利用热负荷部件的内部冷却功能或者取消传统的连接过程。这些正被大规模商用于一系列备受瞩目的航空航天应用中,包括液体燃料火箭发动机、推进剂储罐、航空部件、热交换器、涡轮机、阀门和遗留设备的维保。该文全面回顾了航空航天工业中的金属增材制造,概述当前的技术水平,同时提供金属增材制造的主要应用场景以及相关的商业和技术价值。基于这些观察以及成功案列,针对每个应用场景进行了存在的挑战和潜在机会的介绍,并且对未来发展潜力和应用领域进行了展望。 航空航天部门包括商业和军事飞机、空间探索和空间系统、导弹、卫星和通用航空。新冠肺炎(COVID-19)对航空航天部门的收入造成了极负面影响,从2019年的3422亿美元下降到2020年的2980亿美元。这一下降主要是由航空旅行限制、社交距离和其他限制造成的。尽管商业航空业面临着巨大挑战,由于对新商业飞机的长期需求、全球军费开支的增加、航天航空的多个活动以及整个疫情大流行期间仍持续进行的大量研发,航天部门收入仍有望到2025年增长到4308.7亿美元。 航天制造业受到许多相互作用的技术和经济目标的限制,比如性能要高,生产周期要少,重量要轻,复杂性逐步增强,成本管理和维护的优化等。这些目标都有很强的针对性,且彼此之间关系密切,以及选择最佳设计时必须仔细考虑所有因素。这些目标的相对重要性取决于具体的航空航天应用,但总的来说可以描述如下: 其一,性能——航天部门需要在相对固定的交付时间,提供在其预期环境中高度安全运行的组件。 其二,生产周期缩短——在设计与航天相关的高价值组件时,需要满足快速产品认证并保持设计灵活性。 其三,轻量化——与航天的技术和经济发展有关。具体而言,航空航天的技术和允许的任务有效载荷在物理层次上是有限的,这意味着系统质量减少需要在这两方面下功夫。包括降低燃料成本、降低排放、增加有效载荷和增加航程。轻量化的目标受到成本管理的限制,并且特定的财务资源只可用于特定的设计目标。成本管理、轻量化和生产周期相互关联,因此要想实现轻量化或缩短生产周期,系统成本通常会增多。成本管理适用于组件使用的所有方面,包括认证和维护,以及降低成本管理的认证风险。 航天AM应用的关键挑战是认证,需要监管机构确信AM系统得到充分理解,并且可以重复设计和监管,从而保证可靠性和安全预期。这些认证要求根据其AM系统的重要性(安全性、任务关键性等)而有所差异。实际认证要求与传统制造的现有标准以及新兴AM工艺标准都紧密相关。 其四,复杂性——航天结构通常高度复杂且系统体积小,因此维保挑战大。主要包括老旧飞机的部分适用性、再制造和维修,以及现有飞机的其他用途的重新认证。复杂性是设计“天生”所具备的,因为成千上万的零件组成系统和子系统才能实现预期环境中所需的性能,当它们被集成到整个飞行系统中,通常组件超数百万个。这些组件复杂程度很高,才能保证多性能(结构、流量、热量、可靠性、耐用性、兼容性。轻量化等)。 通过成本、缩短生产周期以及轻量化等不断提高效率的努力中,更复杂的设计和高性能材料的使用也越来越多。当然,这必须控制在合理的成本和满足商业订单或任务要求的时间区间内。几十年来,传统制造系统和战略不断发展以适应这些航天目标,并且发展着的AM也会反过来对这些目标产生影响。AM数字化转型——常被吹捧为工业4.0,到2025年将以20.24%的综合年均增长率使其在航空航天领域的市场规模增至31.87亿美元。 与传统的减材制造(subtractive manufacturing)技术不同,增材制造利用多层制造,在普通原料上(通常是被热源或者固化剂熔化的粉末或金属丝)以数字热源轨迹产生最终的图案。使用AM制造的优势就是缩短生产周期、减少相关成本、增强设计和制造复杂几何形状的能力;能够实现轻量化;整合多个组件以提高性能;在一定的成本和时间范围内,提供方案和技术风险管理的优化。利用金属AM的设计灵活性,可以优化材料布局,减少质量,保持部件的机械性能和其他性能,还可以组合组件以降低风险和成本,减少跨接头的潜在失效风险。此外, 通过利用机械、热量和其他优化方法,发挥其内在优势(如燃烧室或涡轮刀片上的保形冷却通道),可以增强其性能,而这些是以前复杂零件的设计方法所无法实现的。虽然生产周期的缩短是现在航空航天应用中使用AM的主要驱动力,但特殊的制造场景也是一个重要的驱动力(图1)。 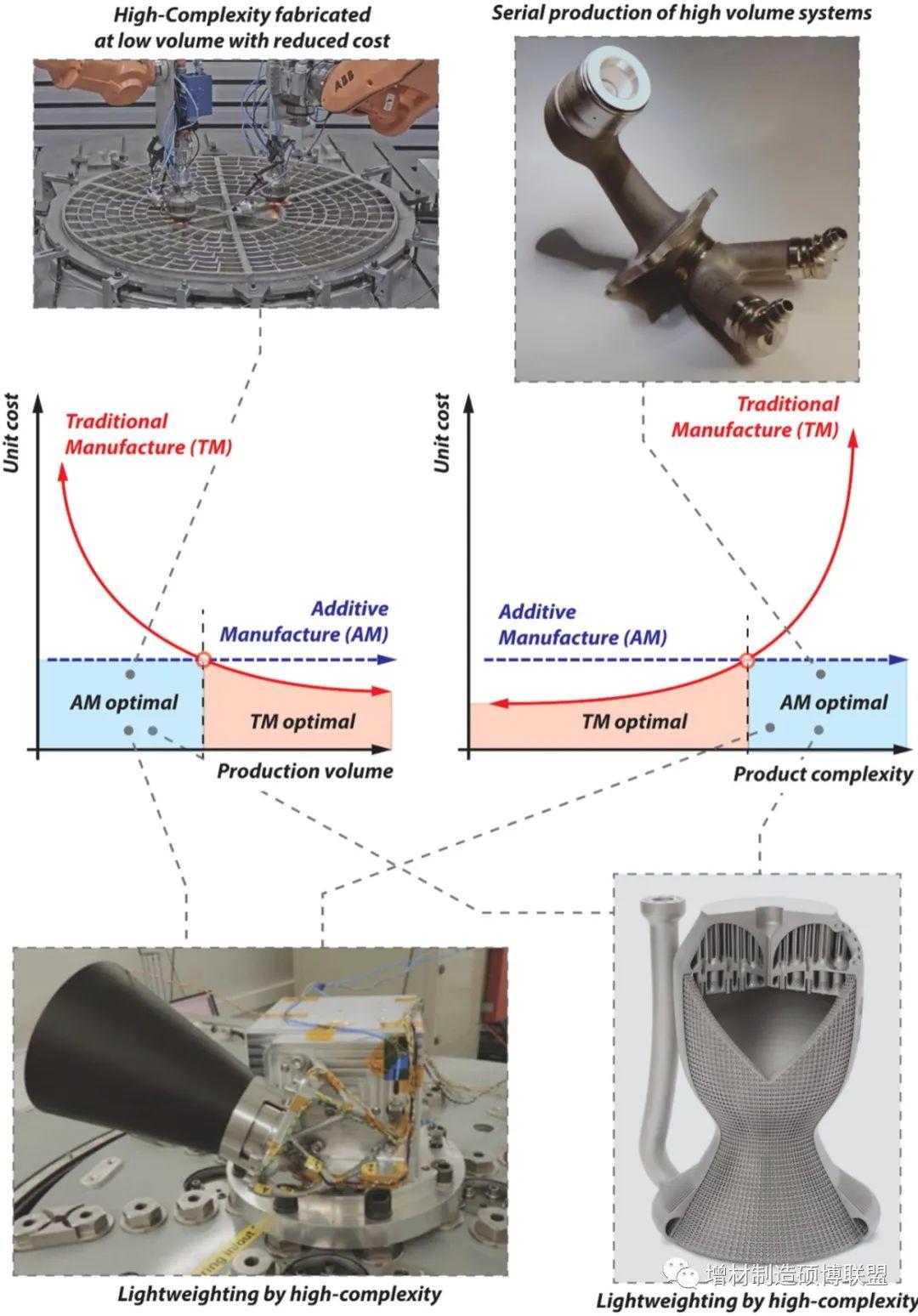
▲图1 单位成本与产量和生产复杂性的对比,以确定进一步发展的经济和技术最佳方案——特定应用满足多种目标,例如高复杂性和低产量。这些场景对于商业AM应用至关重要 AM的复杂性是这种技术的一大优势,因为新的设计可以实现增强机械和热性能以及轻量化等多个目的。AM设计的复杂性和适用性使得其能将多个组件合并为一个,并通过提高技术效率实现轻量。 尽管关于AM 技术,存在所谓的“无技术约束”的误解,它们的确与高复杂组件高度兼容,通过将材料配置成技术(结构、振动或热量)所需,而不是反过来受相关制造过程的限制。 需要注意的是,复杂性应该在设计中和AM的整个生命周期内进行权衡,一旦处理不当或者理解有误,可能会需要额外的操作或造成意想不到的操作难点。 此外,多个组件的合并可以大大降低整体制造成本。这种成本降低可以通过降低生命周期成本以及与其他方面(故障零件的设计、认证和风险管理等)相关的非经常性费用的减少得以实现。 航天部门高度依赖于高价值结构系统的加工锻造。这种制造方法可最终形成高质组件,因为坯料容易明确孔隙率和微观结构,但增加了大量的直接制造成本和缩短生产周期引起的成本。这种加工需要昂贵模具、高成本制造和多次试验,并且坯料加工固有的BTF比(即Buy-to-fly ratio, 指的是制造一个零件所需原材料量与最终零件中所含有材料量的比率)高达20:1。这就相当于质量为10公斤的最终产品将需要200公斤原材料。甚至还有人声称这一比例接近40:1。 根据逐层制造的特质,增材制造的BTF比在1:1和3:1 之间,使用的原材料质量要少得多,形成的浪费很少,可以说几乎没有!与传统制造技术相比,AM可采取适当的预防措施,在显著降低 制造航空零部件的成本并简化回收和再加工流程方面发挥巨大潜力。许多航空合金生产所需锻造原料的周期较长。由于许多AM工艺兼容多种普通合金,使用的粉末或线材原料,其商业生产周期可以大大缩短。目前,生产周期的显著缩短是AM在这个行业的主要优势。 过去,AM在还没有商业终端应用前,以零件展示和初始功能测试的形式被广泛用于快速原型制作。飞行时使用AM的起源可以追溯到21世纪初,从2010年到2011年,AM的使用范围扩大到了包括关键任务组件在内的最终生产。随着技术改进、供应链理解的加深以及应用的严格性、标准化和认证,制造加工的数字化转型取得了初步成功。 AM的基本原理是利用CAD形成的3D模型数据中构建近终型多层组件。这是一个复杂的流程(复杂既是优势,也带来了挑战),因为大量工艺参数对生产部件质量都会产生重要影响。随着对这些参数理解的加深,可逐步减少相关质量影响。这些参数包括功率、扫描速度、开口间距(hatch spacing)或轨迹重叠、扫描策略(例如使用轮廓、每层的阴影线的角度更改等),它们会影响整个制造过程,从而影响组件质量和性能(包括表面光洁度, 孔隙、残余应力、相关的组件裂纹、翘曲、独特的微观结构等)。这可以追溯到材料特性化的根源以及我们经常提及的工艺-结构-性能(Process-Structure-Properties)。 AM的其他缺点包括材料有限、材料特性不确定、设计限制、后处理要求、废物的产生(比如用过的粉末,基板或者是过程失败造成的废物)、为了实现可行的复杂设计和轻质部件对设计技能的高要求、通常利用较为耗时的拓扑优化软件以及严格的质量控制和认证。虽然AM机器越来越多,但其技术不像传统技术那样简单容易,因此制造技术供应链有待成熟。后处理是一个极具挑战的领域,需要定制开发或优化的热处理、组件清洁度和表面增强以改善粗糙度。 所有航空制造都受到严格的质量控制(如Quality Systems - Aerospace SAE AS9100和 Standard for Additively Manufactured Spaceflight Hardware MSFC-STD-3716, NASA Standard 6030),进一步加剧了AM过程的复杂性,对组件质量产生了影响。最近逐步成熟的技术和许多研究报告中完全不同的机械性能(如疲劳性能)都佐证了其重要性。而这会导致材料性能的不确定性和所需控制的差异性。各种国际标准目前正在开发中,以解决这一问题。通过恰当的质量控制和优化程序,上面提到问题都可以缓解或最小化。在粉末移除、热处理、基板移除,热等静压工艺(HotIsostatic Pressing,简写为HIP)、表面抛光以及最终加工中通常需要进行后处理(post-processing)。 尽管存在上述缺点,但在特定的场景中AM仍然远优于传统制造工艺,比如AM非常适合航空航天应用。 下集预告:航空航天领域的金属增材制造——航空航天中AM的4大类独特应用 原文链接:
Metal additive manufacturing in aerospace: A review, Material and Design
https://doi.org/10.1016/j.matdes.2021.110008