有些技术就像是挂在我们头顶上的一串葡萄,充满了诱惑,我们跳啊跳地去够,但总是差一点,或者是能吃到一两颗,但终究感觉不解渴……SiC(碳化硅)应该就是这样一种技术。
作为第三代半导体材料的代表,如果单从性能来看,SiC可以瞬间“秒杀”它的前辈——那些Si(硅)器件。和Si材料相比,SiC的禁带宽度是其2.9倍,导热率是3.3倍,最高工作温度为3倍,击穿场强高10倍,工作频率可达10倍以上,而开关损耗只有Si器件的1%……
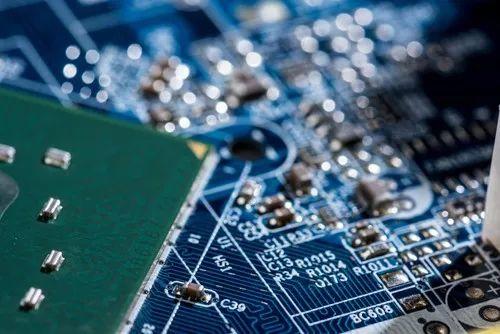
从以上的特性我们不难得出结论,SiC特别适合于制成功率半导体器件,在电力电子领域实现高压应用中的能量转化和控制。而传统上Si器件一直是该领域的主流——几百伏以下的应用基本上是Si材料MOSFET的天下,400伏至10千伏高压应用则被IGBT把持。但是,IGBT的开关速度很慢,且在电力电子领域Si材料的发展已经达到了理论极限,很难进一步降低其传导损耗和开关损耗,提升效率。而更高速、低功耗、更靠性,这些设计挑战都可以随着SiC的驾到迎刃而解。比如从开关损耗这个指标来看,采用平面工艺的SiC MOSFET的开关虽好比IGBT减少60%,如果采用沟槽工艺,还可在此基础上再减少42%,SiC器件性能提升潜力由此可见一斑。
因此曾有人预言,到2010年左右,SiC器件将主宰功率半导体市场。可是我们知道,现实并非如此。今天,Si器件依然“老”当益壮,扮演着功率半导体市场的主角,同为第三代半导体材料的GaN的发展势头也有点后来居上的味道,在30-600伏的中高压区间站稳脚跟,而SiC的爆发却迟迟没有到来。
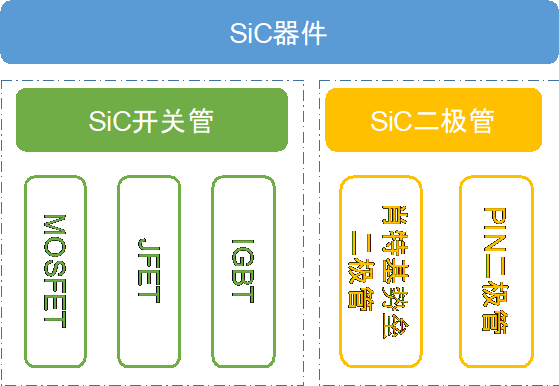
SiC市场爆发最大的阻碍就是其一直高企的成本。目前,SiC MOSFET器件的每安培成本比同类IGBT高出五倍以上。尽管SiC器件制造商已经将工艺从4英寸晶圆升级到6英寸,尽力降低成本,但是SiC固有的制造工艺上的问题还是没有完美解决。归纳起来,SiC工艺上的挑战主要有以下几个方面:
- SiC的晶片一直受到微管缺陷的困扰,虽然近年来这方面已经取得显著的进展,但制作大尺寸晶圆的产能依然受限。
- SiC的外延生长也容易出现缺陷,大尺寸晶圆更为明显,同时气相外延速率低,液相外延产量低,没有一种最佳方案。
- 掺杂工艺要求特殊,只能使用比较“贵”的离子注入方式。
- 此外,在金属电极制作、相关材料配套上也有不成熟的地方。
这些问题汇集在一起,令SiC半导体功率器件一直在低产能、低良率、高成本上徘徊,虽然一直在进步,但是其进步的速度似乎没有竞争对手快——比如IGBT技术从20世纪90年代至今已经更迭了七代,成本也降到了原先的五分之一……
不过,近期市场的发展有望为SiC的发展助一臂之力。要知道,市场和技术总是相辅相成的,技术固然可以推动市场,市场需求的崛起也会拉动技术的进步,包括相关应用生态的完善。对于SiC来说,这个市场机会很可能来自于电动汽车。
有数据显示,到2025年全球电动汽车市场规模将达到2500万辆,是2018年的15倍以上。在电动汽车上,DC-DC转换器、车载充电器、牵引逆变器等都为SiC提供了用武之地。
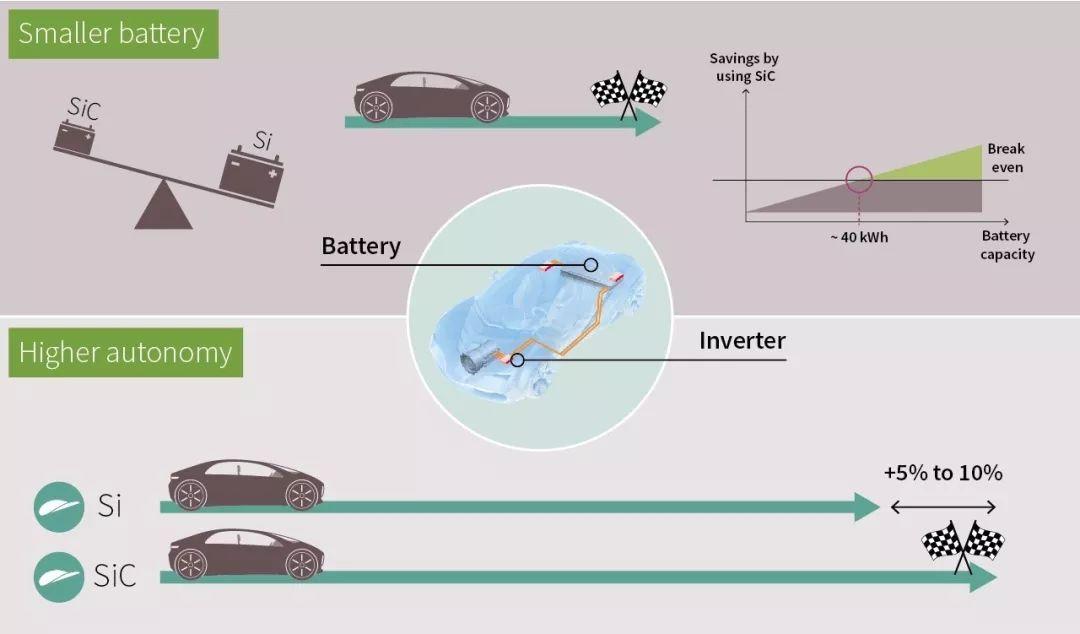
图2,SiC和Si器件在电动汽车市场的应用比较(图片来源:英飞凌)
其中,牵引逆变器是将动力电池电能转化为汽车主电机驱动力的关键部件,是电动汽车中功率半导体应用的制高点,将是技术竞争的焦点。在传统的方案中,牵引逆变器的核心功率器件是6个IGBT,以及与每个IGBT配合使用的一个Si二极管。
而如果用SiC MOSFET替代IGBT,将使工作频率提升至四倍,效率提高90%,且只需更少的外部元器件,大大优化系统的外形和重量。当然SiC MOSFET的成本也是IGBT的三倍,这也让电动汽车制造商不敢贸然启用SiC MOSFET。
不过好消息是,特斯拉正在Model 3中使用意法半导体生产的SiC MOSFET,尽管其他车企的态度依然审慎,但毕竟大家有了一个可以围观的参照物。与特斯拉比较激进的技术路线相比,业界也有一些折中的方案,比如保留牵引逆变器系统中的Si IGBT,但用SiC二极管替换Si二极管,这样既可以借助SiC器件提升部分性能,优化效率,也可以控制成本。
当然,也有SiC厂商认为当下聚焦牵引逆变器应用并不是最恰当的时机,比如英飞凌就认为SiC会最先在车载充电器领域发力,因为在该领域SiC高开关频率下的效率优势和简化的BOM足以补偿SiC器件自身的高成本。据估算,采用SiC器件的直流充电站体积只有微波炉大小,而损耗可以减少三分之二。 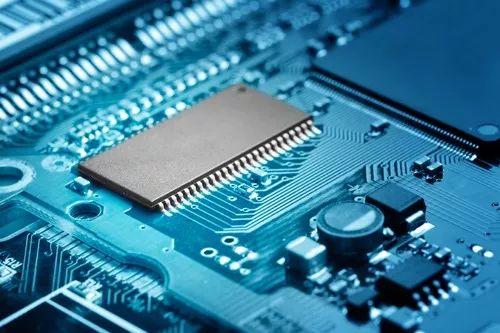
不论是哪个应用市场率先发力,对于SiC技术的发展都将是利好。据Yole的分析,2017年全球SiC功率器件市场为3.02亿美元,较2016年增长了22%,而从2018年起,在电动汽车行业的推动下SiC功率器件将开始加速,到2023年市场规模预计将达到15亿美元。
希望这次SiC的好季节是真的来了,我们期待着沉甸甸的“葡萄”可以垂到我们面前,让我们无需费力即可美美地享用。