本项目开发的车身多学科性能集成优化软件平台具有不依赖于设计数据,参数化建模完成后自动划分网格,依据一个模型可以开展多学科仿真优化等特点,应用到项目前期概念设计阶段,可以极大指导设计工程师完成结构设计工作。在乘用车项目开发中,车身结构作为最重要的系统需要满足刚度、强度、碰撞、耐久、NVH、轻量化等多种性能要求,是最复杂的结构设计之一。近年来,随着CAE 技术的普及,国内各车企在车身结构设计中均已逐步形成“设计-仿真-设计”的标准流程。CAE 技术的应用,解决了在生产试制之前对车身性能进行仿真评估的问题,但也存在着以下问题:(1)仿真依赖于设计,即仿真总是在设计数据完成后才能开展工作,此时,结构设计边界已基本固化,如要更改,将对项目开发周期产生重大影响。(2)仿真过程需要经历网格建模-子模型处理-全模型处理-边界载荷施加-模型试算-正式计算-结果提取等一系列复杂操作,周期长、易出错。等到完成仿真时,设计方案早已由于造型、工艺等原因发生了改变(如设计变化,以上步骤需从头开始),仿真工作费时费力没有效果。(3)不同的仿真学科独立开展性能评估,从各自角度提出改进建议,诉求往往互相矛盾,方案选择时只能妥协一部分性能以换取另一部分性能,无法达到整体最优。因此,随着项目开发周期的缩短,采用较传统的仿真方法已不足以应对逐步提高的各性能要求,研究更具指导意义、更加快捷、综合性更高的仿真技术具有非常高的技术价值,本项目也就应运而生。本文共计2275个中文字,阅读时长约6分钟,如果您有类似的项目需求,请通过公 众 号解决方案菜单内咨询/技术负责人联系方式洽谈。
本集成平台技术首先在前期开发阶段,根据基础车模型和整车边界,建立车身拓扑优化模型,基于动、静态载荷进行拓扑优化,完成车身框架的优化设计。其次利用参数化设计软件,建立某乘用车开发平台概念白车身隐式全参数化三维几何模型,快速验证拓扑优化方案,同时结合有限元网格自动生成技术,对车身模型接头、截面等各项特性参数进行有效设置,联合isight、Optistruct、Radioss可实现运算过程无须人工干预的优化循环,基于白车身模态、扭转刚度、弯曲刚度、整车碰撞性能对车身结构进行形状与拓扑优化,实现“CAD 设计与CAE 分析一体化”设计。最后,结合平台开发车型的边界定义,快速衍生平台定义车型的概念车身模型,并进行相关性能摸底,预测平台性能带宽。另外,在车型设计阶段,运用参数化模型快速变换的优势,对车型初期各关键区域造型变化调整对车身刚度、模态、整车碰撞等性能评估,为造型设计提供性能依据。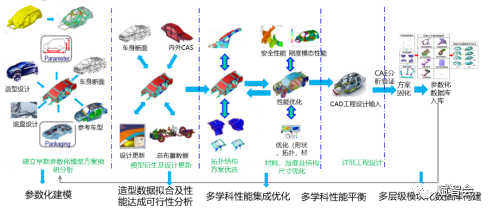
车身多学科性能集成优化软件平台开发工作技术路线
通过全参数化几何与拓扑建模技术,实现点、线、截面、梁、自由曲面等参数化,基于精细化的建模流程及命名规范,实现高精度和智能装配。另外,通过智能映射技术可实现智能化模型装配。单元属性/类型、焊接/胶粘、边界条件/载荷定义等和有限元软件对应且兼容,拥有独特的快速/自动网格生成技术,根据几何模型的变化实时生成高质量有限元网格,连接关系可自动识别(如铆接、焊点、焊缝、螺栓等)。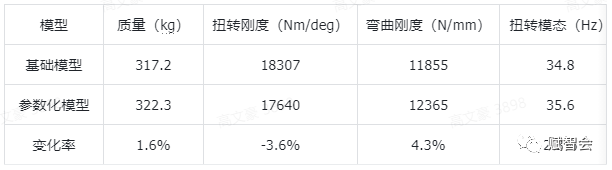
基于参数化模型,搭建车身刚度、模态、碰撞安全、重量等多学科性能优化平台,进行车身结构的尺寸、材料、形状、拓扑结构等优化,得到满足多学科性能要求的车身轻质结构,有效解决性能集成问题,优化效率提升60%以上。基于参数化模型,拟合平台、车型开发边界,形成结构刚度分析、NVH分析所需参数化车身模型以及整车安全性能分析所需的整车碰撞模型。首先,通过平台下装和基础车上装参数化模型,结合总布置边界、造型外CAS数据、车身止口、主断面尺寸,对参数化车身模型进行拟合,以用于车身结构耐久、NVH性能分析。同时,结合车身外部网格数据,按照既定规则进行连接,形成用于整车碰撞分析的参数化整车碰撞模型。本方案对优化区域进行动态非线性分析,得到位移响应,基于位移响应计算等效静态载荷,施加载荷进行优化。同时兼顾车身刚度等静态(应变能)指标、碰装冲击变形量等动态指标,将整体应变能、碰撞冲击工况下关键区域变形量等进行加权叠加,以加权后的结果作为优化目标,将整体应变能、前舱变形量和防火墙变形量加权后作为目标函数。基于断面优化、梁系布置优化等,进行灵敏度分析,识别关键断面及最优位置等,并基于车身模态、刚度、整车正碰、偏置碰等性能进行优化,与优化工具和求解器组合,实现自动化的闭环优化,通过DOE技术建立近似模型, 实现多学科、多目标优化。通过本项目的车身多学科性能集成优化软件平台,得到拓扑优化方案12个,优化截面变量33个,优化板件料厚51个,实现减重8kg,同时扭转性能提升20%左右,弯曲性能提升2%-3%,整车碰撞关键区域侵入量有所降低,形成高性能、轻量化的技术方案,车身整体性能达到预期目标。该车身多学科性能集成优化软件平台使仿真工作提前介入项目开发,解决了仿真依赖详细3D数据不能前置的问题。