三合一电驱动系统振动噪声分析研究
驱动电机作为电动汽车的关键部件之一,其性能决定了电动汽车的主要性能指标[1]。振动噪声特性是一个非常重要的电机评价标准,不正常的振动会加剧电机内部的摩擦,增加损耗,进而影响电机的使用寿命,还会影响乘客的乘坐舒适性。 目前,为了达到成本控制、轻量化设计等要求,电机、控制器、减速器等一体化发展成为必然趋势。三合一电驱系统具备以下优势:结构紧凑,利于布置;质量轻,行驶能耗低;三相直连,可靠又经济;重心下降,利于整车操控;高速传动,带来较高的扭矩容量和总成效率的提升。 相比于传统驱动电机,三合一电驱动系统带来了其他的振动噪声问题,主要是电磁噪声和机械噪声。电磁噪声主要由径向电磁力产生,目前已对电磁噪声的产生机理进行了深入研究。 本文对某新型三合一电驱动系统进行振动噪声测试,发现控制器盖板发生共振,辐射出强烈的噪声;提出从“源”与“接受者”(电机激励与控制器盖板)进行优化,通过对转子开槽减小径向电磁力波,通过对盖板进行加筋与加厚处理,增加盖板的刚度。试验结果表明,优化后的驱动系统噪声水平显著降低。 1 驱动系统振动噪声产生机理
1.1 驱动电机径向电磁力分析
电机中,主磁通沿径向进入气隙,并在转子和定子上产生径向力,从而引起电磁振动和噪声。作用于定子铁芯内表面单位面积上的径向电磁力[6]可以表示为: 
其中:b(θ,t)为气隙磁密;μ0=4π×10-7H/m;θ为空间角度;t为时间。 当忽略饱和时,气隙磁密为:b(θ,t)=f (θ,t) λ(θ,t) (2) 其中:λ(θ,t)为气隙磁导;f (θ,t)为气隙磁势。 在电机振动问题中,可能引起电机强烈振动噪声的力波具有以下3个特点:① 力波的幅值较大;② 力波的阶次较低;③ 力波的力型及变化频率与结构的振型及固有频率接近,易引起共振。由于驱动系统采用的是8极48槽永磁同步电机,主要关注定子磁场一阶齿谐波与转子谐波磁场调制出的低阶次力波,其阶次和频率分别为: 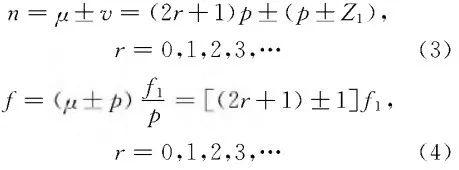
当r(或r+1)与Z1/2p(每极槽数)最接近时,所产生的力波最容易引起负载时电机的振动噪声,且当电机的每极槽数为整数时,将会出现阶力波,0阶力波易激励起电机的呼吸模态,发生强烈的振动。从频率上看,力波的频率均为2倍电网频率。相应地,相对于转子转频,径向力波的频率为转子转频的2rp倍,即径向力波相对于转子转频的时间阶次为2rp阶。
1.2 减速器及控制器噪声分析
减速器作为三合一电驱动系统的动力调节装置,将电机的高速输出调整为转矩与转速合理分配的输出形式。齿轮传动时,齿与齿之间不可避免地产生撞击和摩擦,从而使齿轮产生与转速有关的啮合振动和噪声。齿轮啮合噪声的频率为: 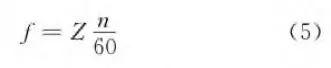
当齿轮啮合的频率与齿轮本身的某阶固有频率接近时,会激发出强烈的噪声,齿轮啮合产生的动负荷使轴产生变形并在轴承上引起动负荷,轴承的动负荷又传给减速器壳体,使壳体激发出噪声。 在三合一电驱动系统中,直接用螺栓将控制器固定在电机与减速器上,在驱动系统工作时,电机端和减速器端的振动将传递到控制器,尤其是刚性较弱、面积较大的上盖板,极易响应电机端与减速器端的振动激励,发生共振,产生强烈的振动和噪声。 2 驱动系统振动噪声测试分析
三合一电驱动系统的结构如图1所示。采用米勒贝姆公司的数据采集设备和测试软件对驱动系统进行满载匀加速近场噪声测试,3个振动加速度传感器分别布置在电机壳体、减速器输出轴和控制器盖板,如图2所示。 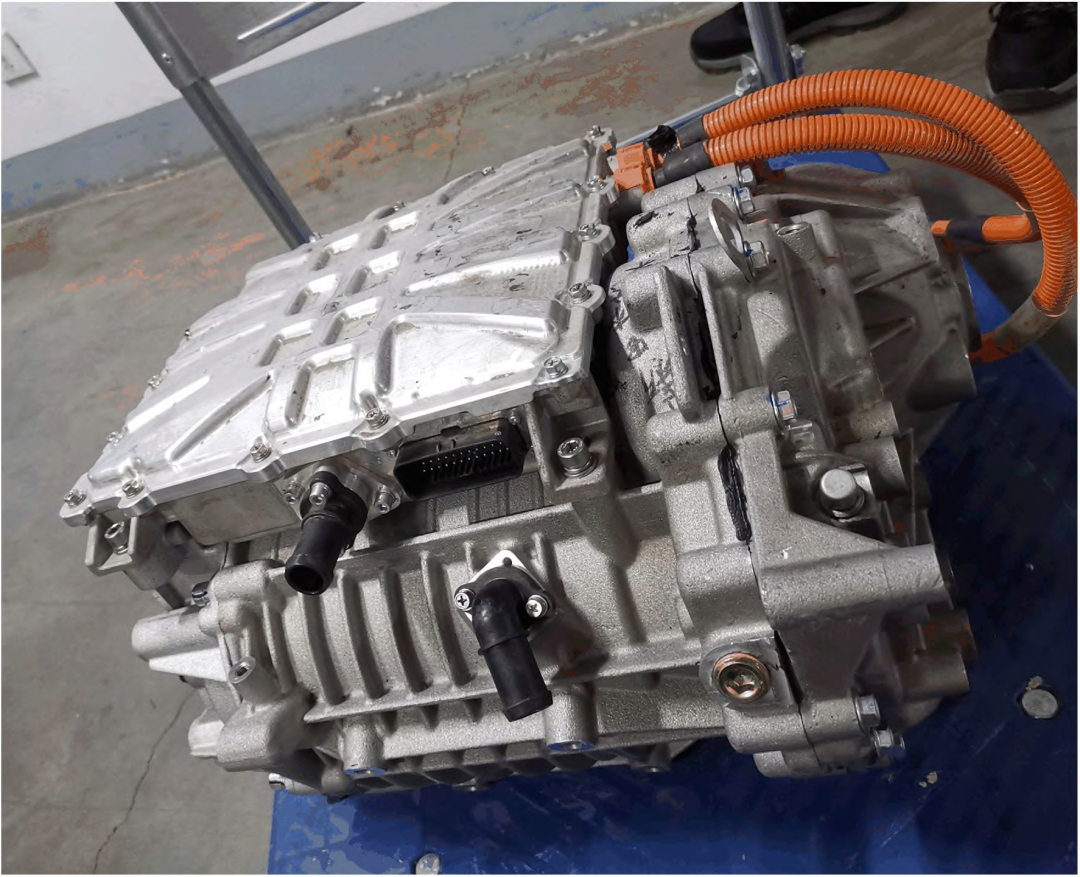
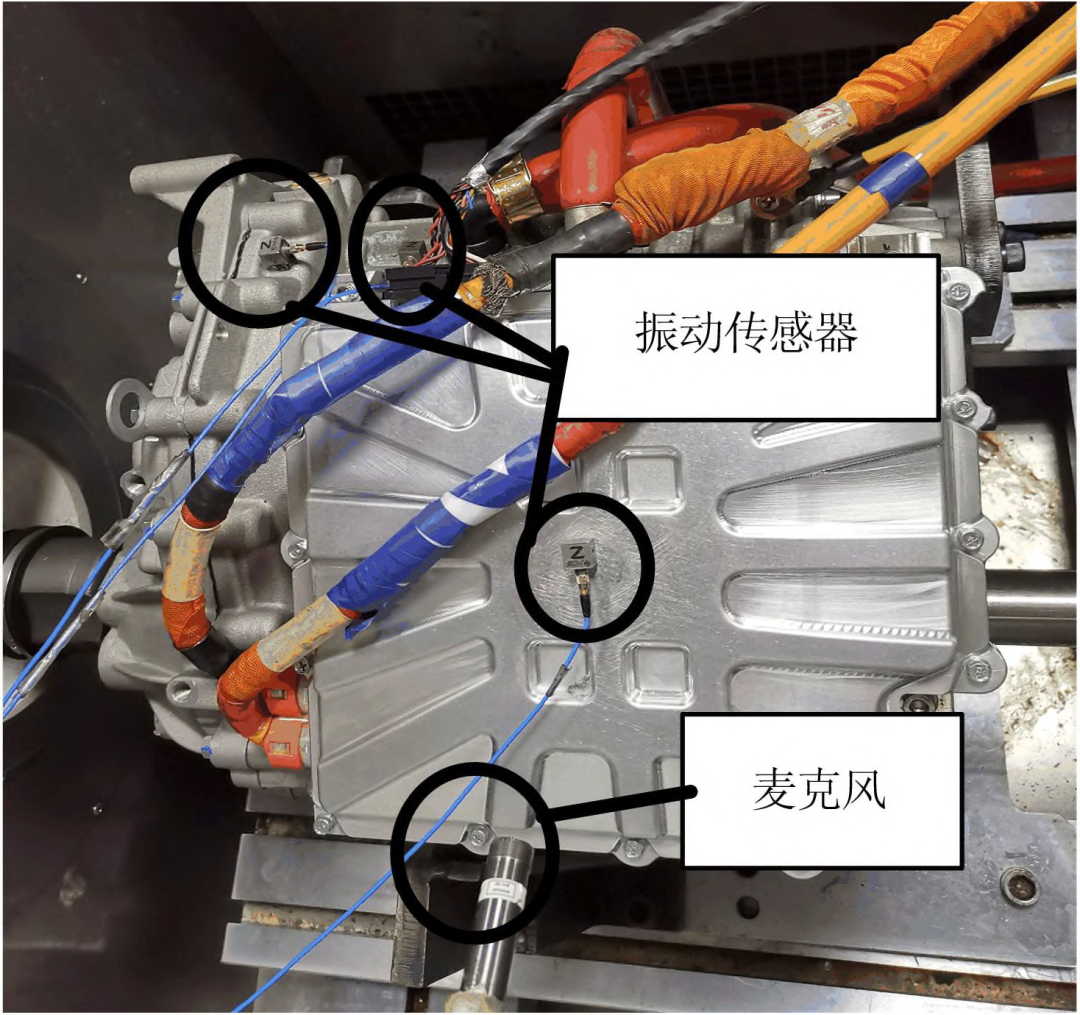
驱动系统满载匀加速A计权声压级近场噪声如图3所示。 图3中存在2条共振带和4条突出的阶次线,分别为5.94、11.88、22.00、48.00阶。 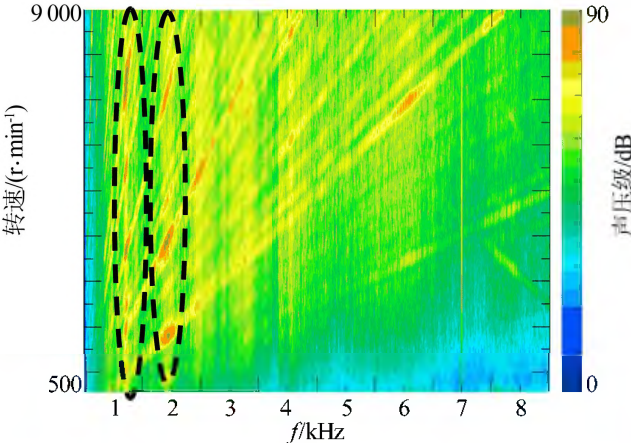
本文驱动系统采用的是8极48槽永磁同步电机,其极对数p=4。根据上文分析可知,电机运行时会产生8倍及其整数倍的径向电磁力波,因此48阶噪声为电机的电磁噪声。电机输出轴齿数与减速器各齿轮齿数见表1所列。 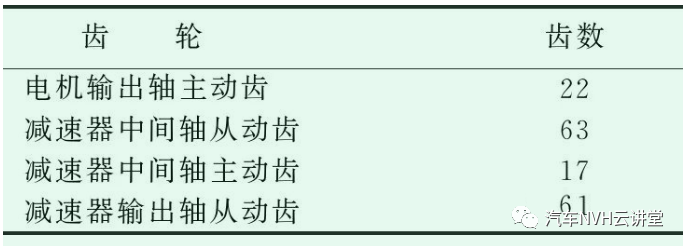

其中:f为齿轮啮合噪声频率;n为参考轴转速。以电机输出轴转速为参考转速,因此电机输出轴主动齿与减速器中间轴从动齿啮合时噪声的阶次为: 
减速器中间轴主动齿与减速器输出轴从动齿啮合时噪声的阶次为: 
其中:Z1为电机输出轴主动齿;Z2为减速器中间轴从动齿;Z3为减速器中间轴主动齿。 因此,5.94阶噪声为减速器中间轴主动齿与减速器输出轴从动齿的啮合噪声;11.88阶噪声为减速器中间轴主动齿与减速器输出轴从动齿啮合噪声的2次谐波;22.00阶噪声为电机输出轴主动齿与减速器中间轴从动齿的啮合噪声。 利用锤击法测得盖板自由模态的一阶弯曲频率为712.3 Hz,二阶弯曲频率为1 213.5 Hz,其一阶弯曲振型和二阶弯曲振型如图4所示。 图3中存在2条突出的共振带,其频率为680~750 Hz、1 200~1 450 Hz,盖板的一阶弯曲频率和二阶弯曲频率恰好位于共振带频率段内,可见电机端及减速器端的振动激励起控制器盖板的弯曲模态,发生共振,噪声幅值明显增大。 采用的加速度传感器为三向加速度传感器,对比每个传感器所测得的振动加速度幅值最大的方向,结果如图5所示。 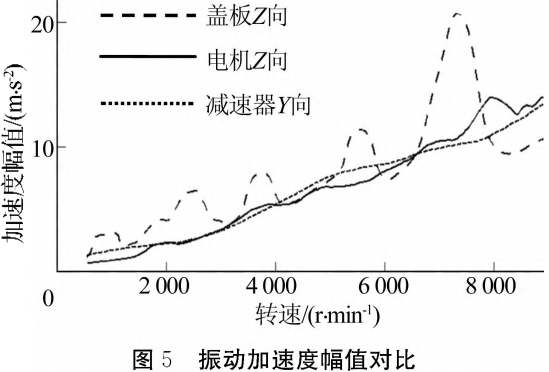
盖板的Z向振动加速度整体上大于电机壳体和减速器的振动加速度,并且在转速7 330、5 550、3 770 r/min处存在3个峰值,这3个速度点均位于共振带中噪声幅值较大的速度段内,此时盖板振动所辐射的噪声为驱动系统工作时噪声的主要贡献量。振动噪声分析常采用“源路径接受者”的模型进行分析,三合一电驱动系统由于结构紧凑、传递路径简单,从“源”与“接受者”(电机激励与控制器盖板)进行优化更加高效可靠。 3 激励源优化
驱动系统运行时,激励源主要来自永磁电机的径向力波。在Maxwell中建立驱动系统所采用电机的二维电磁模型,如图6所示。仿真参数设置见表2所列,仿真时长为1个电周期(电机每转包含4个电周期),其中绕线方式为双层链式。 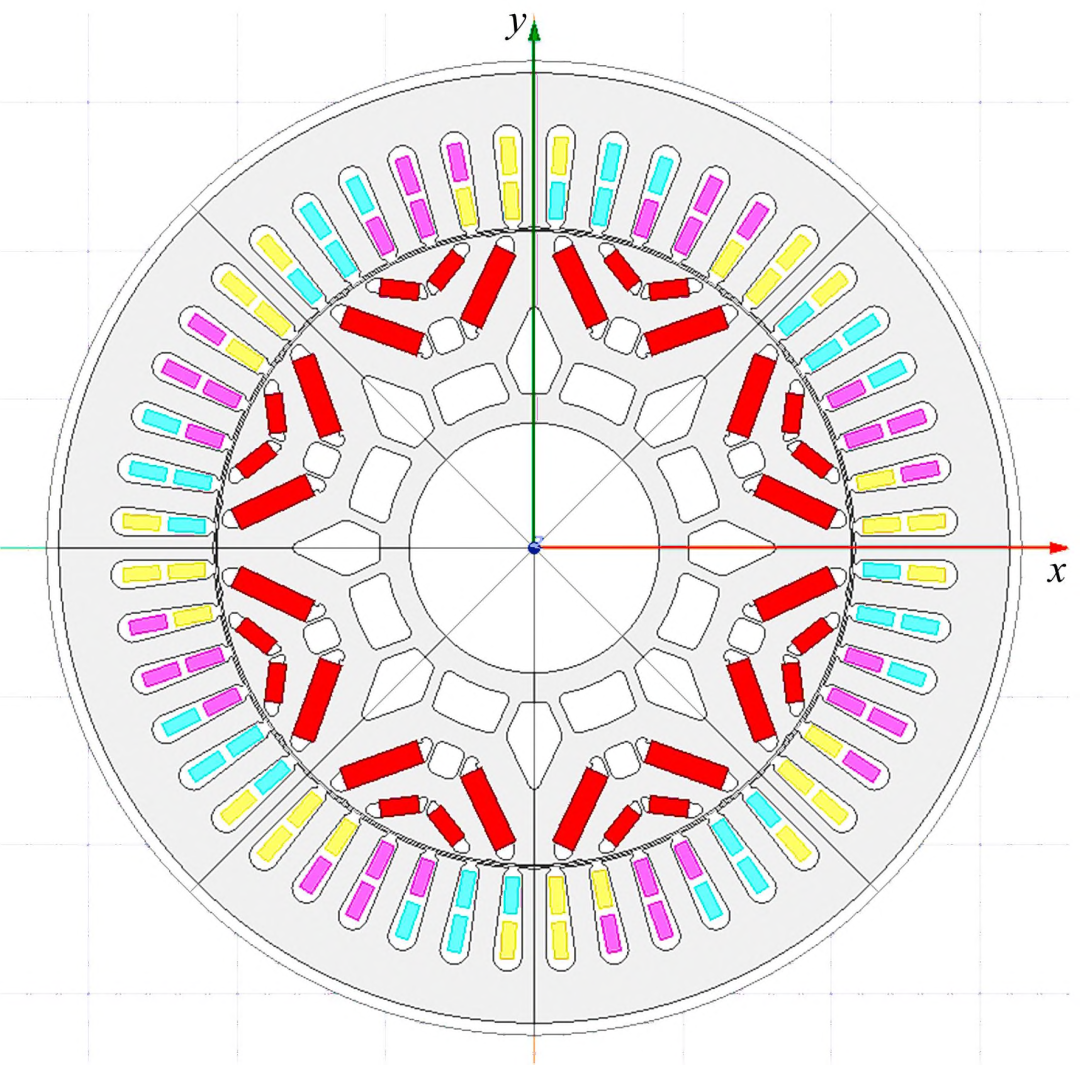
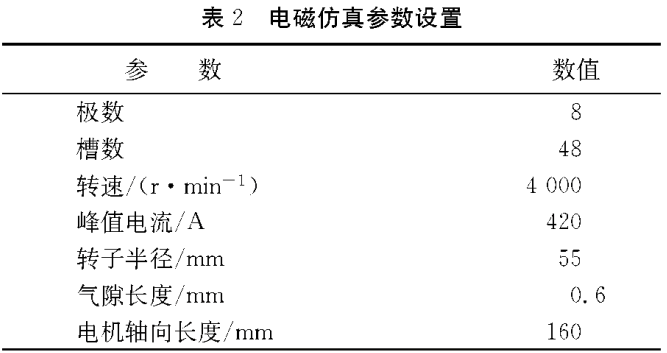
仿真得到电机径向电磁力波,力波存在空间与时间上的变化,对其进行二维傅里叶变换,得到径向电磁力波的时空分布,如图7所示。 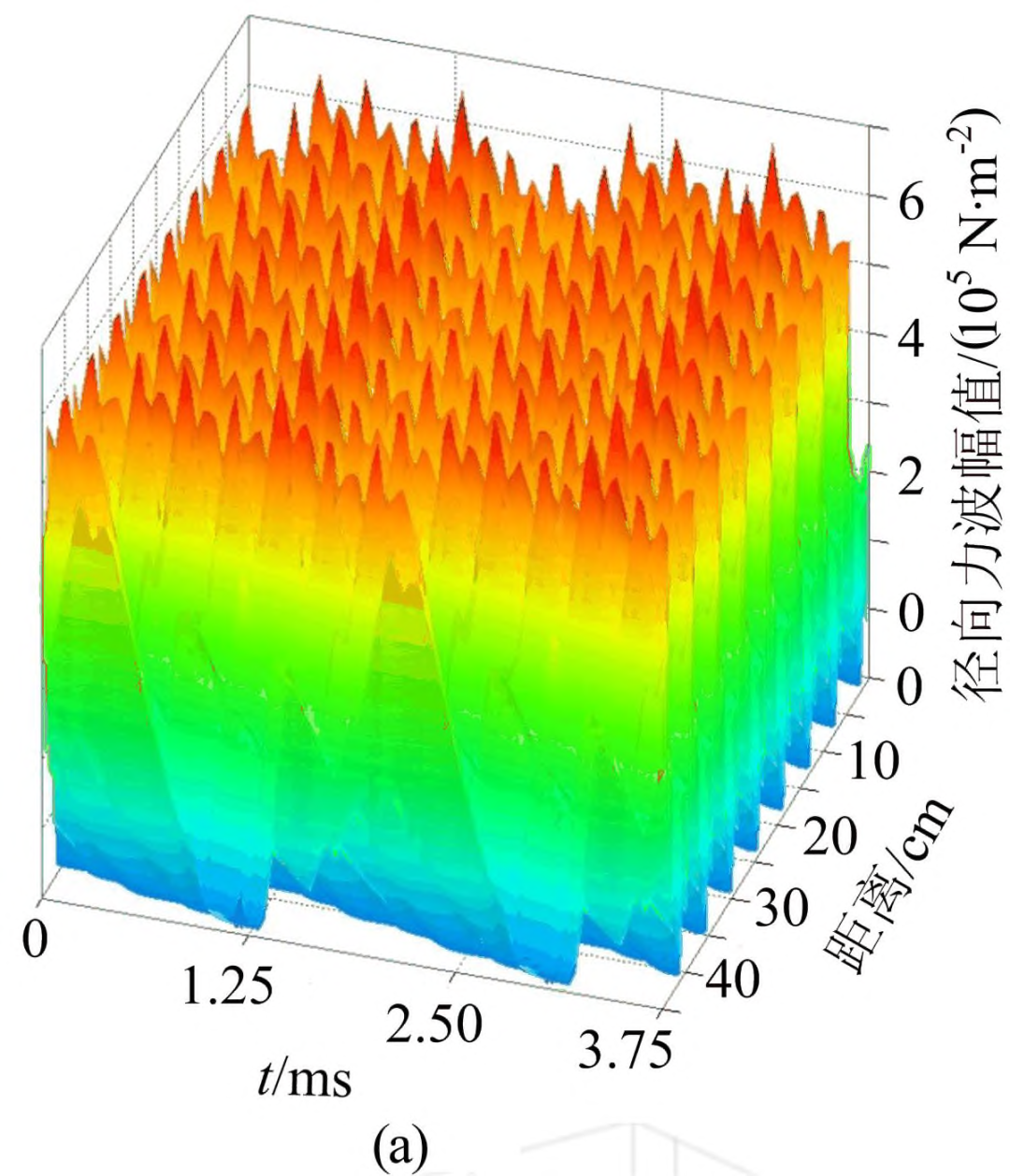
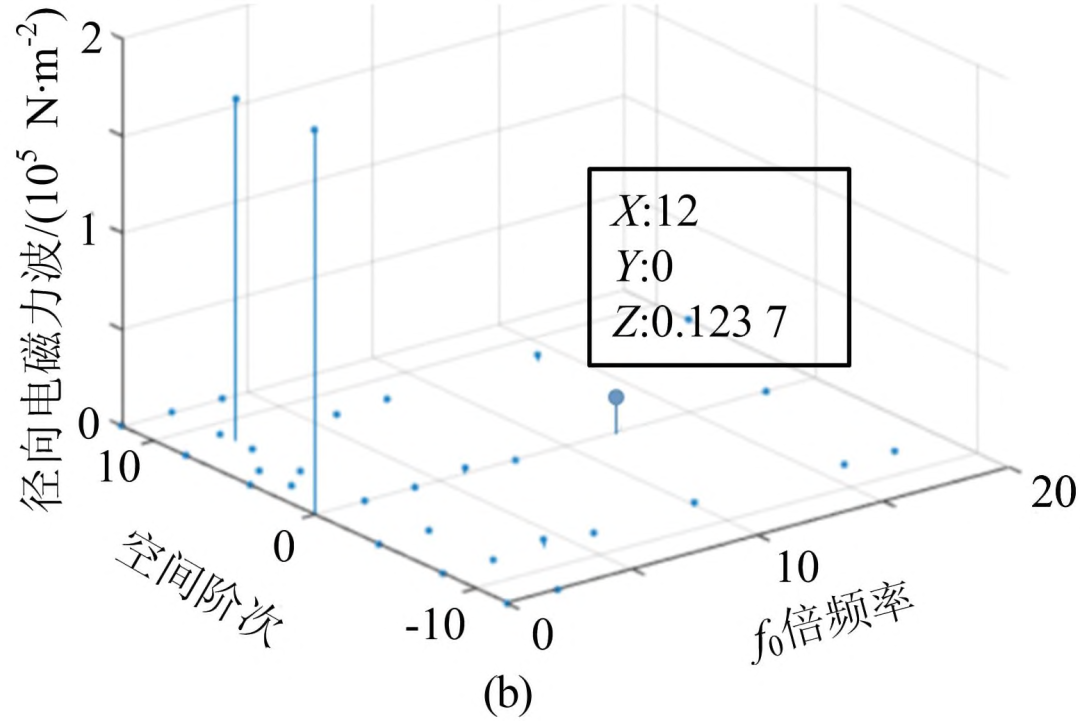
为减小电机径向电磁力波,需对转子进行再设计。对转子进行周向开槽,如图8所示,在一定程度上可减小气隙磁密,进而减小径向电磁力波。 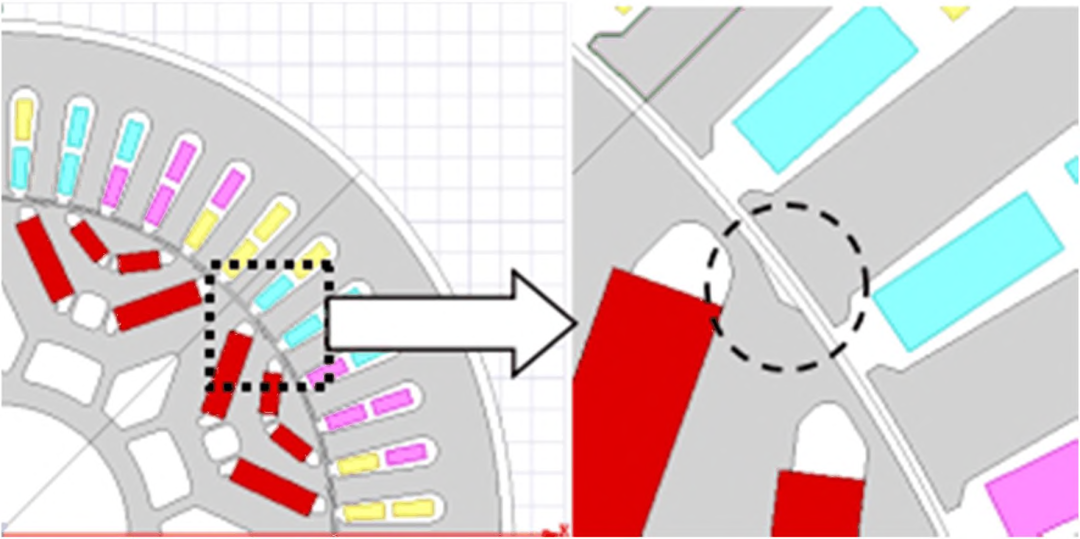
对开槽后的电机模型进行有限元分析,得到电机的径向电磁力波,如图9所示。从图9可以看出,对驱动系统振动噪声影响最大的0阶48倍频径向电磁力波幅值降低了11.8%。 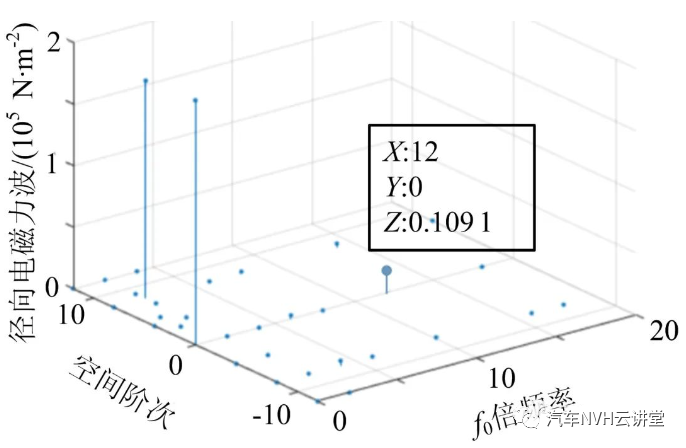
4 控制器盖板优化
抑制盖板结构振动的有效方法是增加盖板刚度,提高其固有频率。薄板的弯曲刚度为: 

对于板的共振来说,一般低阶的弯曲模态占主导作用。增加板的刚度,板的固有频率随之升高,共振峰响应向高频推移,能量响应峰值也有所降低[8],为此对盖板进行周向加筋并增加厚度。 为了提高盖板的固有频率,需要对其进行形貌优化,得到较优的加筋布置方案。用一个max模型来描述线弹性结构的固有频率最大化问题,对设计区域进行有限元离散化后的形貌优化模型的数学表达为: 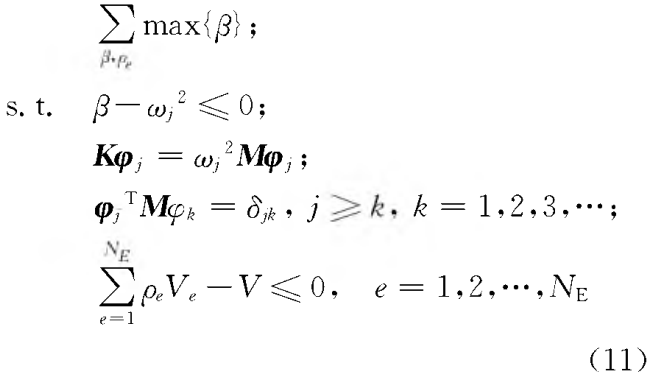
其中:j=1,2,3,…;β为标量因子,用于约束每阶固有频率的平方均小于β;ρe为单元材料的相对密度,其数值为0~1;NE为单元总数;特征值λj=ωj2为结构第j阶固有频率的平方,满足结构振动的广义特征值方程、即约束中第1式;φj为第j阶振型模态,满足关于结构质量矩阵M的正交归一化条件,即约束中第2式。 采用ABAQUS对盖板三维数模根据数学模型进行形貌优化处理,得到具有更高固有频率的结构模型,如图10所示。 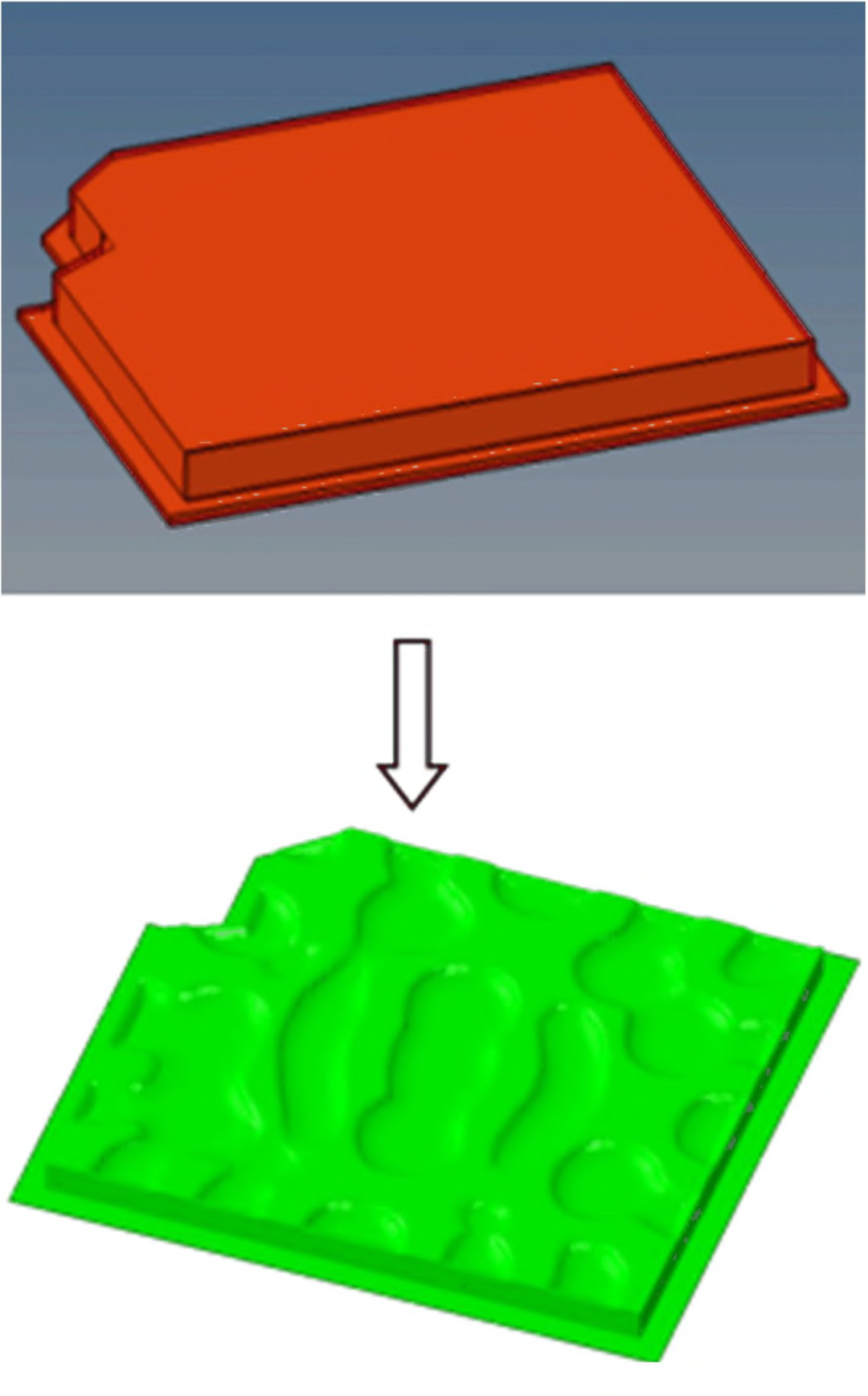
因为得到的形貌优化模型较为复杂,不满足工程实际需要,所以根据形貌优化的三维模型来进行优化加筋布置,从而得到形貌优化的最终结构,如图11所示。 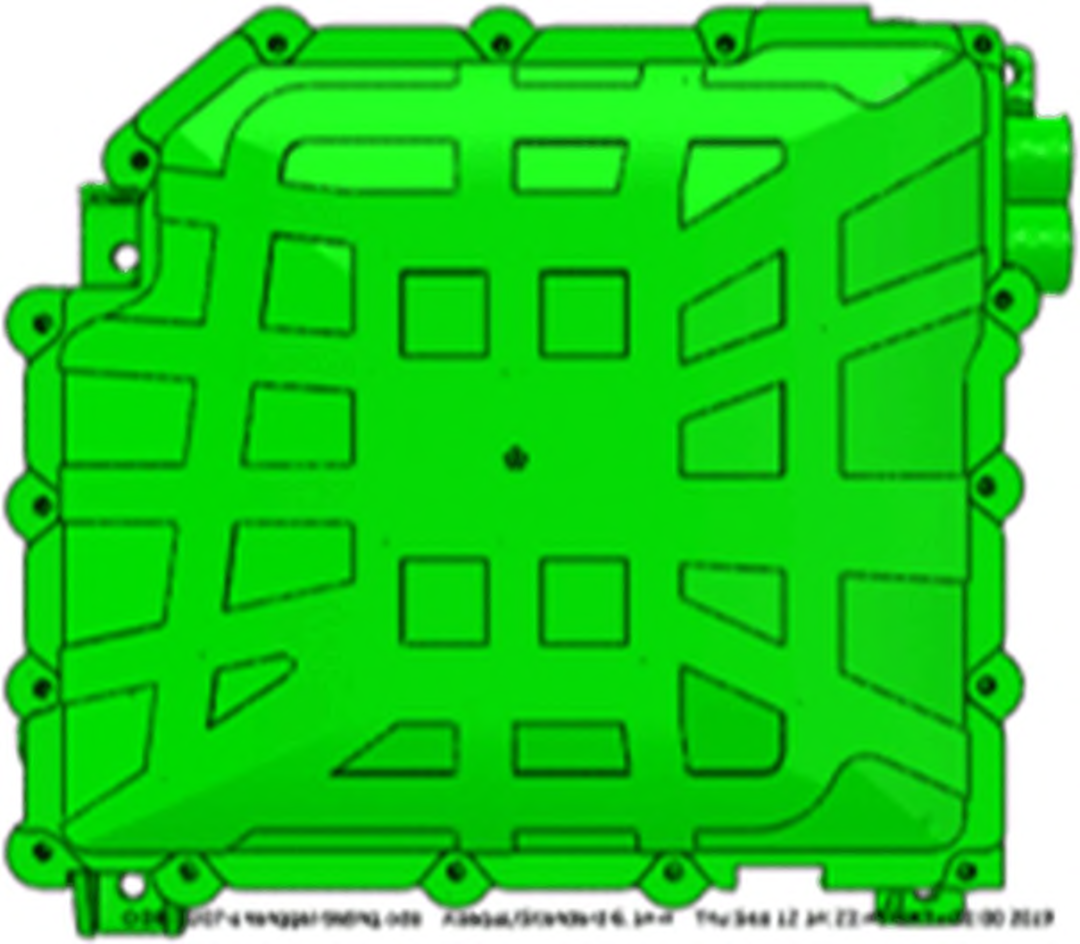
在结构的形貌一定时,结构的尺寸往往对结构的性能有显著影响,对于厚度不同的加筋板,在改变板厚使结构体积增加时, 弯曲刚度会随着板的厚度增加呈现一种增大的趋势。原始盖板的厚度为3 mm,加厚盖板的厚度为4、5 mm,采用ABAQUS对不同厚度加筋盖板样件进行自由模态仿真分析,得到优化样件的前2阶弯曲模态的频率及前2阶弯曲模态的振型云图,如图12所示。 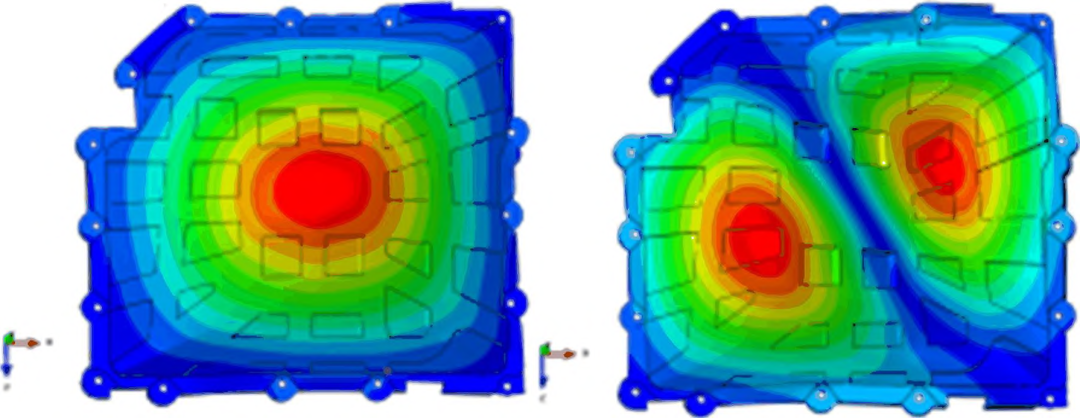
(a) 一阶弯曲仿真云图 (b)二阶弯曲仿真云图
采用锤击法对样件进行自由模态测试,得到前2阶弯曲模态的频率。仿真与测试结果见表3、表4所列。 由表3、表4可知,采用有限元仿真和锤击法得到的模态固有频率数据具有较好的一致性。 为了进一步定性验证优化方案对振动的抑制效果,对不同厚度的加筋板模型的中心点加载单位简谐激励,对加筋板模型的螺栓孔采用完全约束,得到不同厚度加筋板模型的中心点对激励的振动响应频谱图,如图13所示。 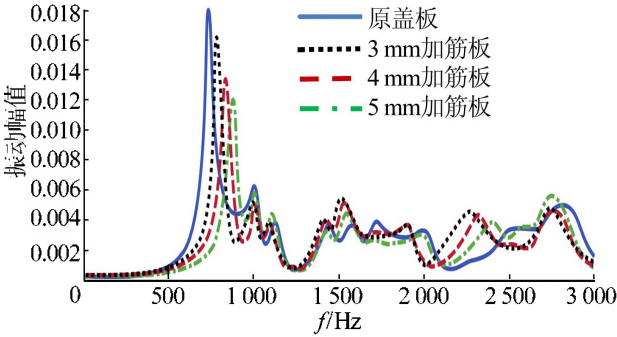
从图13可以看出,在700 ~1 300 Hz段,优化方案的振动幅值明显降低,但厚度为4 mm的加筋板与5 mm的加筋板效果相差不大。 5 测试试验
对优化后的驱动系统进行振动噪声测试,测试结果如图14所示。 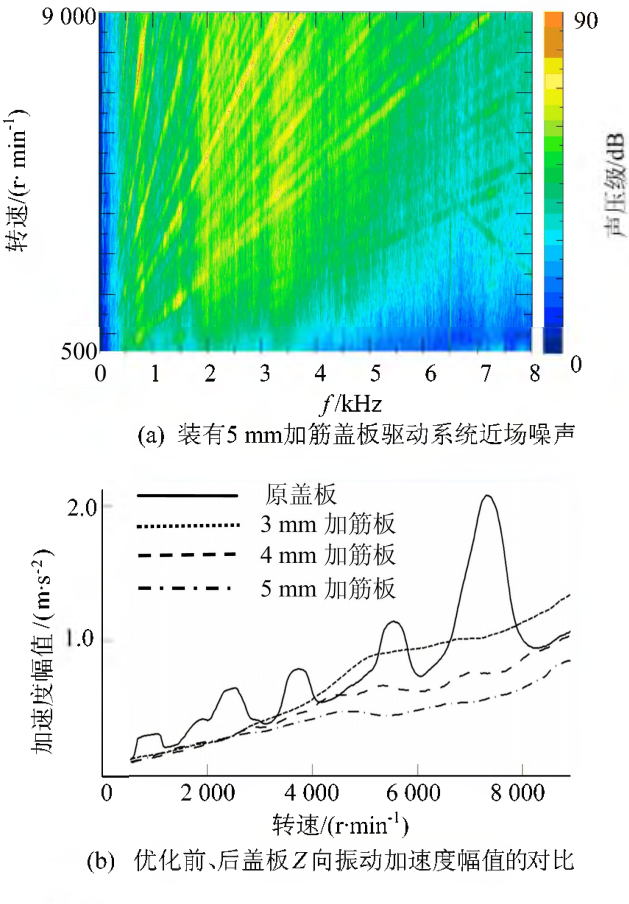
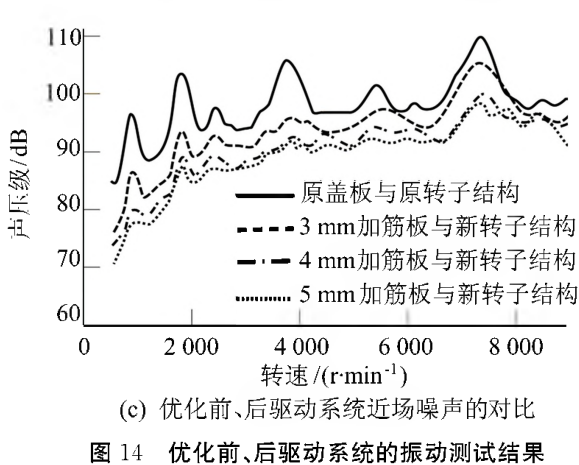
由图14可知,在装有5 mm加筋盖板与新转子结构的驱动系统近场噪声彩图中,图3中的2处共振带不再出现;对比优化前后的测试数据可以看出,盖板的法向振动加速度有所降低,在最大峰值处优化效果显著;驱动系统的噪声整体优化效果显著,并且在转速7 330、5 550、3 770 r/min处噪声幅值大幅降低,其中采用新转子结构与5 mm加筋盖板的驱动系统的噪声整体下降约13.3 dB。 6 结 论
本文对某新型三合一电驱动系统进行了振动噪声测试分析,发现电机端和减速器端的振动激励起控制器盖板的弯曲模态引起盖板强烈振动和噪声;提出了一种通过减小电机径向电磁力波与改进控制器盖板结构来优化三合一电驱动系统噪声水平的方法,并进行了试验验证,结果驱动系统噪声显著降低。 (1) 较大面积的盖板类结构易响应系统的振动激励,引起结构的共振,从而辐射较大的噪声。(2) 通过转子开槽可减小电机径向电磁力波,改变盖板厚度及加筋处理能有效增强盖板类结构刚度、提高固有频率、抑制结构振动,显著改善噪声水平。(3) 当盖板厚度相同时,形貌优化能显著改善结构振动噪声响应;但当加筋板厚度增加时,对噪声的优化效果会有所降低。 【免责声明】本文来自网络,版权归原作者所有,仅用于学习等,对文中观点判断均保持中立,若您认为文中来源标注与事实不符,若有涉及版权等请告知,将及时修订删除,谢谢大家的关注! 著作权归作者所有,欢迎分享,未经许可,不得转载
首次发布时间:2023-03-28
最近编辑:1年前