增材综述丨金属增材制造技术在民用航空领域的应用与挑战
作者:中国航发上海商用航空发动机制造有限责任公司 雷力明,侯慧鹏等摘要:金属增材制造技术在民用航空领域应用前景广阔,通过对比3种典型的金属增材制造技术,总结了金属增材制造技术在面向金属增材制造的设计、原材料、工艺过程3个方面的研究现状,并按照技术分类介绍了典型应用进展。基于民用航空零部件适航认证特殊要求,分析并提出金属增材制造技术存在设计方法不成熟、加工效率低、质量监控手段有限、缺乏统一的适航认证要求等若干挑战,并对未来发展趋势进行展望。
关键词:增材制造;民用航空;成形工艺;结构件;航空发动机民用航空装备及系统中越来越多的零部件结构设计趋向复杂化、功能结构一体化,传统铸造、锻造结合机械加工的制造工艺已经无法适应零部件的快速迭代研发和低成本制造需求。金属增材制造是一项集成热源(激光、电子束等)、机械、计算机软件、材料、控制、网络信息等诸多现代先进技术而形成的一项实现高性能致密金属零件快速自由成形的新型制造技术。与传统加工技术相比,金属增材制造技术具有加工周期短,材料利用率高,无需刀具、模具,小批量零件生产成本低等优点,可实现多种材料复合制造,可以解决型号研制阶段快速响应的难题,在民用航空领域取得了快速发展。在民用航空领域主要应用的金属增材制造技术有两类,一类是粉末床熔融技术,如选区激光熔融(Selective Laser Melting,SLM)、电子束熔化(Electron Beam Melting,EBM)。另一类是定向能量沉积技术,如激光熔化沉积(Laser Melting Deposition,LMD)。以上3 种技术对比如表1所示。增材制造技术可极大提升设计自由度,开展面向增材制造的零件结构设计研究,对于发挥其技术优势起到关键作用。面向增材制造的设计方法基础研究方面,国内外相关研究机构已取得部分成果。如法国通信与控制研究院Ponche等提出了面向增材制造设计(Design For Additive Manufacturing,DFAM)的3个步骤的方法 论;英国威尔士大学Thomas对SLM 成形能力进行了测试,为结构设计提供依据;美国路易威尔大学Yang等针对金属增材制造三维网格设计和加工进行了相关研究;德国Kranz等对SLM成形TC4钛合金设计规则进行了细致研究,提出了大量适用于SLM技术的结构特征。增材制造技术在民用航空领域的应用场景主要分为两类:一类是基于传统设计方案,经过合并、拓扑优化设计得到新设计方案,这也是目前主要研究方向。美国国防部、Sandia实验室等单位已经将拓扑优化技术应用于航空产品设计,并开展了试验件加工和验证性试验。Altair公司在考虑稳定性的同时,使用一种多级方法实现了翼梁结构的拓扑优化设计。在国内,张卫红等在飞机发动机挂架和后机身结构布局优化设计方面取得重要进展。设计软件的开发也在不断适应拓扑优化设计的需求,其中比较著名的有美国Altair公司的Optistruct软件、ANSYS公司研制的大型通用有限元分析软件、德国FE-DESIGN公司的Tosca软件。第二类是从零开始进行的面向增材制造的结构功能一体化设计。如面向功能需求重新设计零件等,可充分利用增材制造工艺优势,同时与传统工艺有机结合实现优势互补,兼顾生产效率与经济性。与第一类零件对比,第二类零件对面向增材制造的设计方法提出了更高要求,是未来的主流研究方向。金属粉末作为金属增材制造的原材料,其化学成分、粒度分布等指标对制件质量存在重要影响。在粉末化学成分方面,目前多进行定性分析,如明确O、N、Si 含量升高会降低Hastelloy X制件的持久性能,C元素含量降低会降低 制件的强度等。随着增材制造成形机理和特点逐渐明晰,部分学者也开始进行面向增材制造工艺的新材料设计,通过成分调配以适应成形工艺并提高制件的性能。在粉末粒度方面,15~45μm的粉末适用于SLM 成形,45~110μm的粉末适用于EBM成形,45~220μm的粉末适用于LMD成形。粉末粒径越小,越容易在成形过程中出现过热现象;粉末粒径过大,可能导致零件的致密度下降。对粉末床熔融而言,粉末粒径分布决定铺粉层厚,小的粉末粒径和较窄的粒度分布范围有利于获得稳定的熔池并提高制件的致密度。粉末受潮会导致粉末表面形成单层或多层分子层,氢键增加,相互作用力增大,流动性降低,造成制件孔隙率升高等。对粉末床熔融而言,粉末中的卫星球、长条颗粒会影响粉末的流动性,从而影响铺粉质量。在粉末空心率方面,空心粉会导致制件中气孔缺陷的产生,降低 制件的致密度,大量孔洞的存在导致合金拉伸强度和屈服强度下降,尤其使缺口持久寿命和疲劳性能明显恶化。循环利用方面,随着粉末循环使用次数的增加,金属粉末的粒径会稍有增加,表面粗糙度升高(图1),O、N元素含量上升,粒度分布范围变窄,拉伸强度略有提升。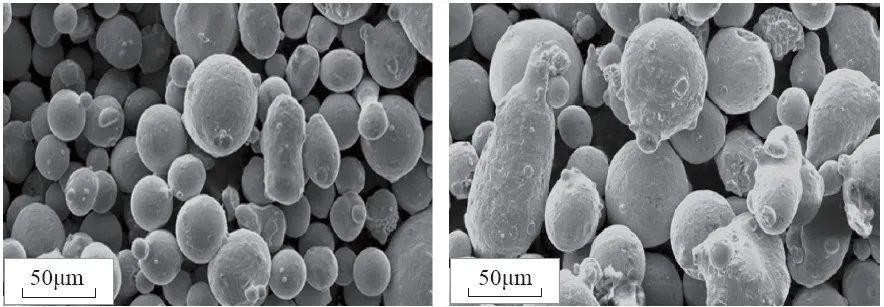
金属增材制造成形过程是一个涉及移动熔池、快速非平衡凝固、固态相变的复杂冶金过程,该过程的非均匀快速热-力耦合和变形行为导致制件易出现翘曲变形、裂纹及孔洞等缺陷,这些缺陷对制件的尺寸精度、致密度及力学性能等产生不利影响。为了预防上述缺陷的发生,需要借助增材制造工艺仿真深入理解该过程。近年来,随着金属增材制造技术的发展,该过程的数值模拟技术也得到了快速发展。目前已经发展出覆盖各个尺度的数值模型,包括零件的宏观热应力分布数值模型、熔池内流动的介观数值模型、熔池凝固过程的相场、组织模拟等。姜亚琼等建立了C919飞机钛合金T型缘条构件缩比有限元模型,对其激光成形过程进行定性分析,研究了钛合金T型缘条激光熔化沉积过程中热/应力演变过程(图2)。德国埃尔朗根-纽伦堡大学Gurtler等采用了三维流体体积法模拟了激光选区熔化过程,研究了熔池内的液相流动以及气孔等缺陷的形成。Fallah等模拟了Ti-Nb合金激光熔化沉积的凝固微观组织。在熔池固-液界面,根据FEM模型计算的温度梯度,将其简化成局部定向凝固的形式研究Ti-Nb合金熔池凝固微观组织演化行为。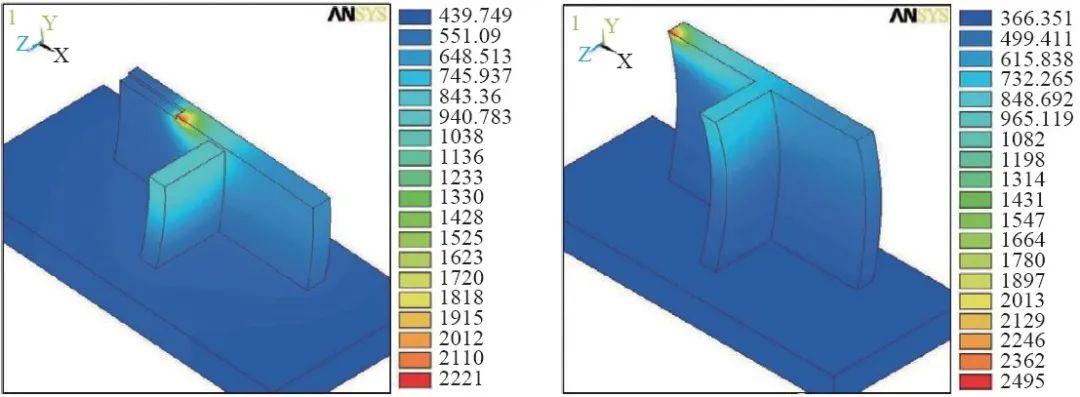
用于金属增材制造的仿真软件有ABAQUS、ANSYS、3DSIM、SIMUFACT、AMPHYON等,但是目前针对金属增材制造建立的理论和数值模型采用了过多的简化假设条件,使得计算结果仅能定性分析工艺过程。当零件结构复杂或尺寸较大时,有限元模型也面临计算量过大而无法满足实际需要的问题。针对这些问题,在提高模型准确性方面,目前研究主要集中在基于原位测量的模型参数修正技术;在快速计算方面,主要采用动态自适应网格技术和多GPU 并行计算方法,提高计算效率。材料的显微组织与其经历的热过程密切相关,增材制造材料在激光或电子束等移动热源的作用下经历“逐点扫描-逐线搭接-逐层堆积”多次复杂的热循环过程,制件每一层都经历了多周期、变循环、剧烈加热和冷却的短时热历史,因此与传统工艺在组织结构上相比有较大的差异。增材制件沉积态组织主要是从基体沿着温度梯度较大的沉积方向外延生长的柱状晶粒。增材制造组织的各向异性导致了力学性能各向异性。此外,零件尺寸、零件摆放方向、摆放位置、能量输入、与基板距离等多个因素对增材制件组织及缺陷存在影响。国内外研究机构在组织演变和提高力学性能等方面开展了大量研究工作。Fraunhofer研究所、美国空军研究实验室等研究了热处理和热等静压对微观组织和性能的影响,热处理大大降低了组织内应力,热等静压消除了层间气孔等缺陷,使成形件的力学性能达到了锻件水平。在国内,北京航空航天大学、西北工业大学分别研究了钛合金、镍基高温合金零件的激光熔化沉积成形工艺,并通过优化热处理制度,使钛合金、镍基高温合金制件组织得到改善,性能明显提高,成功应用于飞机大型承力结构件的制造。此外,超声振动辅助激光熔化沉积的试验结果表明:施加超声振动后,微观组织得到细化,其强度和塑性都得到提高。感应加热辅助激光熔化沉积技术也可有效减小基体与熔化层之间的温度梯度,消除气孔、裂纹和夹渣等微观缺陷。在应用方面,美国GE公司首个使用SLM成形且通过美国联邦航空管理局(Federal Aviation Administration,FAA)认证的金属零部件是T25传感器壳体(图3(a)),该零件在2015年实现装机应用,目前已被安装在超过400台的GE90-94B发动机中。GE公司采用SLM技术成形的燃油喷嘴(图3(b))在2016年通过了FAA认证,装机应用于Leap X航空发动机。2015年,GE公司采用增材制造技术进行全新涡轮螺旋桨发动机(ATP)的研发,如图3(c)所示,该款发动机中约35%的部件(如燃烧室、动力齿轮箱等)由增材制造技术完成,零件总数由原来的855个减少至12个,这样简洁的一体化结构设计使发动机重量得以降低,燃油消耗量降幅达20%,发动机的动力提升了10%。从GE公司的增材制造技术应用来看,该技术在航空发动机领域正在逐渐由零件级向整机级应用发展。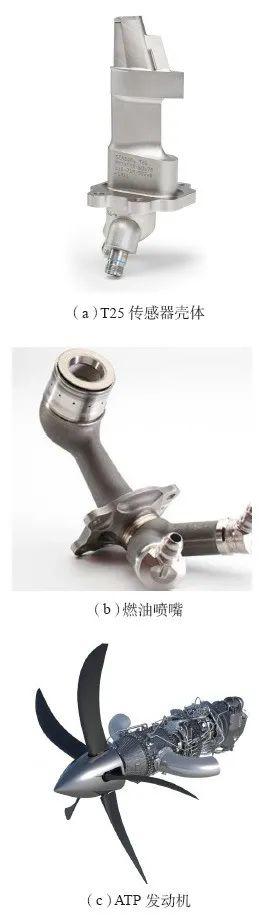
德国MTU公司利用SLM技术直接制备PW1100G-JM航空发动机的镍基合金管道镜内窥镜套筒及多联体导向叶片。2017年,法国赛峰公司首个增材制造零件——镍基合金涡轮喷嘴通过欧洲航空安全局认证,该涡轮喷嘴是eAPU60微型涡轮发动机的核心部件之一,重量减轻了35%。2019年,赛峰公司增材制造的LEAP发动机润滑单元通过适航认证。2017年9月,空客宣布在批量化生产的A350 XWB系列飞机上首次安装SLM成形的钛合金闩锁轴。GE公司利用EBM技术成功制造了航空发动机TiAl合金低压涡轮叶片,比传统镍基高温合金叶片减重50%。GE公司已经在GEnx、GE9X等航空发动机上采用了EBM成形的TiAl叶片。英国罗罗公司研究使用EBM技术制造XWB-97发动机的前轴承座部件,该部件直径1500mm,厚500mm,含有48个翼面。中国航发商用航空发动机有限责任公司在国内率先开展SLM和LMD技术在商用航空发动机中的应用研究,分别试制了燃油喷嘴、预旋喷嘴、涡轮冷效叶片(图4)、测试受感部及发动机安装节平台等零件,其中增材制造燃油喷嘴已在CJ-1000AX核心机和整机上装机应用(图5)。此外,2017年还完成10kg推力的全金属增材制造微型涡喷发动机的制造。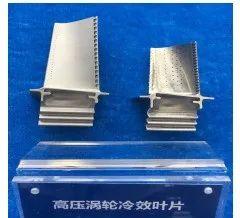
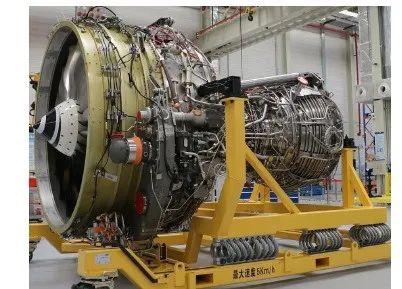
国内定向能量沉积技术已在飞机结构件上得到大量应用,如北京航空航天大学成功研制出飞机大型整体钛合金起落架整体支撑框、飞机座椅支座及腹鳍接头等金属部件,使我国成为目前世界上唯一实现激光成形钛合金大型整体主承力构件成功装机工程应用的国家;沈阳飞机设计研究所、上海飞机设计研究院等通过激光熔化沉积研制出了30余种钛合金和超高强度钢大型整体关键主承力构件;西北工业大学对TC4、TA15、IN718等合金开展了大量研究工作,图6(a)为C919机翼上下缘条钛合金构件,图6(b)为激光修复的航空发动机轴承后机匣。LMD技术的一个重要应用领域是对受损零件的修复。2008年以来,英国罗罗公司与国防部联合资助开展整体叶盘的低成本修复技术研究,通过引进美国Optomec公司LENS850R设备和德国Trumpf公司的LMD1005激光直接沉积设备开展整体叶盘激光修复基础研究。通过大量基础技术研究工作,国外初步建立起整体叶盘的激光修复装备、技术流程和相应数据库,推动了整体叶盘激光修复技术的工程化应用。MTU 公司也利用激光熔化沉积对单晶高涡叶片进行修复研究,对低压涡轮叶片进行“Z”型齿阻尼面耐磨层修复。增材制造零件通过适航认证是实现民用航空领域工程化应用的前提。增材制造技术的应用水平高度依赖于部件的创新设计,在零件设计、制造和验证过程中,应充分考虑结构设计、成形工艺(模型摆放位置、支撑设计、打印方向等)、过程质量监测和控制、后处理技术及零件检测技术可靠性等方面的影响因素。基于民用航空领域对新材料、新工艺技术的安全符合性及经济性要求,增材制造技术还存在以下挑战。面向增材制造的设计对于增材制造技术的应用起到关键作用。面向传统制造的设计方法(Design For Manufacturing)已经广泛建立起有效的设计原则,如面向机械加工的设计需考虑刀具和装夹,面向冲压成形的设计需考虑材料的塑性及模具结构等。与传统制造相比,尽管金属增材制造技术给复杂金属零件的制造带来了革命性的影响,但由于增材制造技术工艺特点与传统工艺具有本质不同,设计人员对增材制造工艺技术特点认识的局限性限制了零部件在结构、形状、尺寸、功能、重量等多维度的优化设计,使得增材制造的技术优势难以充分发挥。目前在民用航空应用领域,缺少从应用需求出发、摆脱传统设计进行的面向增材制造的原创设计,尚未形成面向增材制造的设计方法。为突破这一局限,增材制造设计及制造应当加强协同,在已开展增材制造零件试制的基础上,打破传统制造技术造成的概念壁垒,尝试进行全新设计。以民用航空中典型零件为载体,逐步基于增材制造工艺特点优化设计方法,兼顾尺寸精度限制、结构形式对工艺难度的影响、力学性能各向异性特点等,利用三维模型设计及仿真技术,最终设计出高可靠性、轻量化、结构功能一体化的零件。为获得良好的尺寸精度和表面质量,在成形精密复杂构件时,工艺参数设置需采用较小的层厚及较小的光斑,导致增材制造毛坯的成形效率远低于传统工艺。采用粉末床熔融增材制造,其粉末原材料单价远远超过传统工艺,且在成形大尺寸零件时粉末占用量很大。同时增材制造设备成本较高,国内多数增材制造装备仍处于科研阶段,尚未形成规模化生产,也在一定程度上导致了成本上升。由于目前成形效率低、成本较高,增材制造装备技术在民用航空领域,特别是商用飞机方面仅限于少量实例,尚未大范围推广应用。为提升生产效率、降低生产成本,在设备方面,多光束增材制造设备已逐步成熟,成形效率得到有效提升。同时随着技术逐步普及,设备及原材料单价已出现较大降幅。此外,设计方案决定了产品成本的80%,应当从增材制造零件设计阶段就开展成本评估,在零件设计阶段基于成本控制思想进行设计,使传统工艺与增材制造实现合理匹配。增材制造成形过程中,热源、移动熔池与粉末基体的交互作用存在复杂的物理、化学和热力耦合现象。除复杂的热过程外,激光功率及定位精度、成形气氛、飞溅物及烟尘排除等也对零件质量产生重要影响。由此导致了增材制造成形质量过程监控难度很大,如何实现有效监控是当前面临的关键难点之一。主流增材制造设备已初步实现熔池监控、铺粉质量监控,即可获取熔池形成及凝固过程、铺粉质量的具体信息,综合判断成形过程是否存在异常,可以辅助推断零件具体 位置的缺陷情况。当前业内采用的监控手段的效果有限,尚未达到充分有效的程度。开发集光学、热学、声学等方法于一体的过程监控体系,将是未来发展的重要方向之一。增材制造零件性能高度依赖于后处理,包括热处理、去支撑、表面光整等。由于成形过程快速熔化和凝固以及热循环等特点使得组织结构复杂,存在各向异性,传统的热处理工艺制度不再完全适用;对于粉末床熔融成形复杂结构零件,工艺支撑去除手段有限,多采用钳工去除,存在零件变形及损坏风险,质量一致性难以保证;毛坯零件需要经过表面处理才能达到或接近零件最终使用要求,浅表层存在的微细裂纹限制了其在转动件或承力件上的使用。内表面光整处理是粉末床熔融增材制造后处理技术的关键难点。现阶段主要的技术方法为电化学加工、磨粒流、磁力抛光等,对于简单流道可基本满足要求,但在复杂流道、盲孔、薄壁、变截面、复杂曲面等方面尚存在较大不足,容易出现去除量不均匀、流道破损等现象。新型内腔光整技术和支撑去除技术是未来增材制造后处理技术发展的方向,进一步提高零件尺寸精度和表面粗糙度对提升零件综合性能可以起到关键作用。增材制造典型缺陷的基本特征、形成机理及控制方法目前尚不完全明确,这些冶金缺陷在电磁场、超声波等外物理场或外介质中的物理化学响应行为、无损检验特性及方法,以及这些内部缺陷的微观力学行为、对材料及构件力学性能的影响规律及缺陷损伤容限特性等均在探索中。传统制件检验标准不再适用于增材制造零件的检测和评价。如沿用传统铸件或锻件的检测方式进行增材制造零件的检测,部分缺陷无法准确检出或无法准确分析评价。在零件、部件考核方面,由于进行了一体化设计、结构集成以及拓扑优化等全新设计,原方案的考核要求也不再适用。增材制造零件的检测需根据其特征采取多种检测方法协同的方式进行。适用于增材制造的检测方法有光学测量、计算机断层扫描、射线检测、涡流检测、渗透检测、过程补偿谐振测试、热成像检测、超声波检测等。增材制造技术具有强工艺相关性的特点,在零件批量生产的批次稳定性控制方面仍然存在许多问题。影响增材制造零件批次稳定性的因素复杂,主要包括原材料、设备系统、成形工艺、后处理工艺等方面。原材料在化学成分、粒度分布、流动性等方面的变化会对增材制造零件批次间的组织和性能带来差异,在原材料的性能控制、循环使用等方面尚未形成行业内严谨统一的规则,增大了工艺技术风险。设备系统的热源(如激光束、电子束)定位精度、气氛控制、机械系统控制对制件的表面粗糙度、尺寸精度及制件成分的稳定性有影响。成形工艺和后处理工艺对制件的批次稳定性有着决定性的影响,成形工艺参数控制、烧结策略、平均能量密度、粉末层层厚等因素直接影响成形制件各批次的质量,后处理工艺则通过去支撑方法、热处理温度、冷速或压力控制以及表面光整技术影响零件批次生产的稳定性。应当从人员、设备、材料、工艺和环境多方面控制增材制造零件批次稳定性,推动增材制造技术朝着智能化、自动化与集成化的方向发展,这也是增材制造未来发展的主要方向。根据FAA 33.15(国内民航局为CAAC 33.15)及AP-21等条款相关规定,必须提供足够证据支撑增材制造零件可靠性、安全性和产品质量一致性等符合性验证工作。目前国内外增材制造零件适航认证仍缺乏统一规则,但其适航思路应与传统工艺基本保持一致,经过材料符合性、制造符合性技术审核,按照固化工艺过程、建立标准规范、验证满足设计要求、完善质量控制体系的过程,最终完成适航取证。按照从易到难的原则,适航认证的零件正在逐步从现有材料、现有设计向新材料、新设计发展,从非承力构件向承力构件发展,从一般件向关重件发展,取得了长足进步。近20年,金属增材制造技术水平得到快速提高,对民用航空零件的设计及制造带来重大变革,且随着面向增材制造的设计思想逐步深入、工艺技术逐步完善、标准体系逐步建立,可以预见未来其在民用航空领域中具有巨大应用潜力。然而,目前增材制造技术仍在设计、材料、工艺、标准等方面存在诸多问题,限制了技术应用水平。建议在基础研究方面,充分重视并持续加强在增材制造相关机理和科学问题方面的研究工作,更好地实现产品质量一致性控制;在产业化应用方面,基于综合成本与技术因素,选择民用航空典型零件为“突破口”,快速推动涵盖面向增材制造的原材料、设计、制造、检测、考核及适航认证的全流程技术体系发展,提升金属增材制造技术在民用航空领域中的应用水平。