增材制造(AM),也称为3D打印,是一种很有前途的技术,可从高功率密度热源熔化的粉末或线材中快速生产净成形部件。在激光辅助增材制造过程中,金属粉末被聚焦的激光束熔化。激光扫描模式由计算机控制,熔融金属凝固形成连续的沉积层。增材制造的应用包括机械部件、电子产品、组织、植入物和假体的打印。增材制造中使用了多种材料,包括镍基高温合金、钛合金、不锈钢和聚合物材料。在这些材料中,镍基合金因其优异的拉伸和蠕变性能以及抗热腐蚀和抗氧化性而被广泛用于涡轮叶片、燃烧室和核反应堆。由于织构会影响制造组件的机械和化学性能,因此其控制对于获得任何其他方式无法制造的增材制造零件的目标性能至关重要。
具有完全相同形状和尺寸的部件可以通过不同的激光扫描模式制成。然而,由于激光束的横向路径会影响凝固模式,因此具有完全相同几何形状的组件可能具有明显不同的凝固模式。据报道,在多层激光组件的沉积过程中,Inconel 718的凝固形态受到激光扫描模式的显着影响。单向激光扫描过程中的凝固模式导致在所有层上形成与基板成60°角的初级枝晶。然而,对于双向扫描,每层的初级枝晶的生长方向相对于前一层的初级枝晶的生长方向改变了90°。凝固模式取决于生长界面附近的局部温度场和衬底的晶粒取向。以前的工作表明柱状晶粒在单晶衬底上外延生长。固液界面处的局部温度梯度和凝固生长速率受到AM工艺参数的显着影响。高功率密度、低激光功率和高扫描速度有利于柱状晶粒生长外延到表面。单晶衬底的晶体取向也影响柱状枝晶的取向。相反,多晶衬底包含许多随机取向的晶粒。对于这些衬底,晶粒取向通过在平行或几乎平行于立方材料的局部热流方向的六个<100>优选生长方向之一中的竞争性晶粒生长来选择。美国宾夕法尼亚州立大学的学者基于三维传热和流体流动的数值模型,研究了各种激光束扫描模式的热流方向,展示了数值建模不仅可以更深入地了解增材制造过程中的凝固生长模式,还可以作为定制凝固织构的基础。相关研究以 “Evolution of solidification texture during additive manufacturing” 为题发表在《Scientific Report》期刊上。表1 数值模拟材料参数
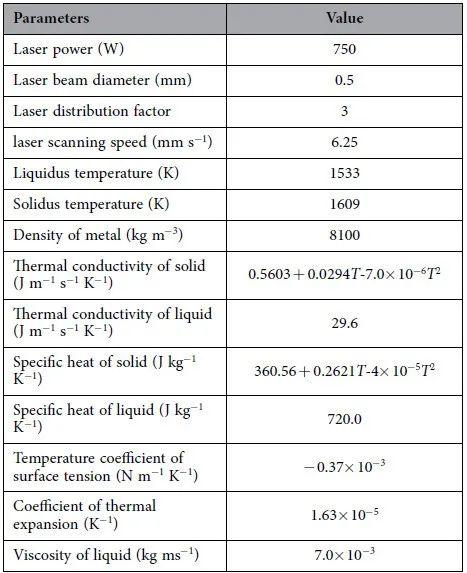