点阵结构由结点和结点间的连接杆件按照一定的空间周期规律扩展构成。金属点阵结构具有超轻、高孔隙率、高比强、高比刚、高强韧、高能量吸收等优良力学性能,以及吸声、减震、散热、电磁屏蔽、渗透性优等特殊性能,使其兼备结构和功能的双重功用,是一种性能优良的多功能工程结构材料,在航空航天、国防军事、交通能源等各行业中均具有非常乐观的应用前景。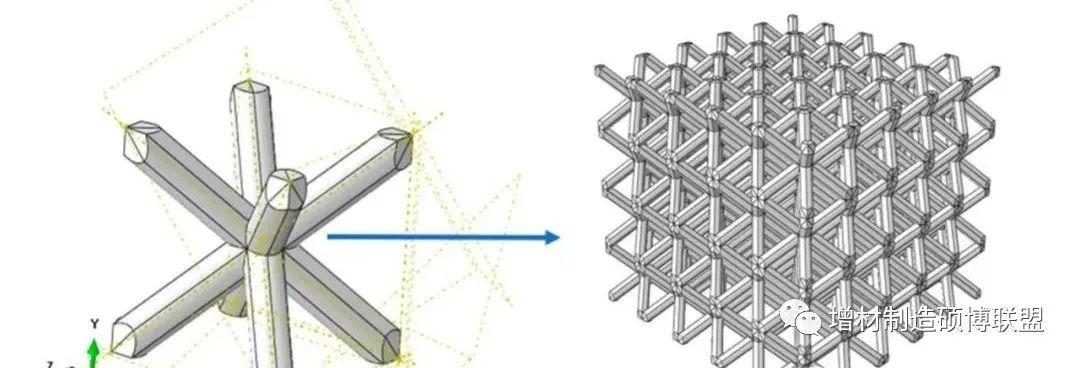
点阵结构示意图
2011年美国加州大学和加州理工大学的研究人员制备出超轻金属镍微点阵结构,它由0.01%的固体和99.99%的空气组成,密度仅为0.9mg/cm3,具有极高的能量吸收能力,压缩到98%后还可以恢复到原来的形状。劳斯莱斯生产的点阵结构油气分离器,孔隙率高达95%,密度仅为0.5g/cm3,油气分离效率高达99%。声波进入点阵结构后引起空气震动,经多次反射和折射,原有入射声波大部分能量变成热量散失到环境中,美国杜克大学根据此原理制造出了点阵结构的“声学隐身装置”。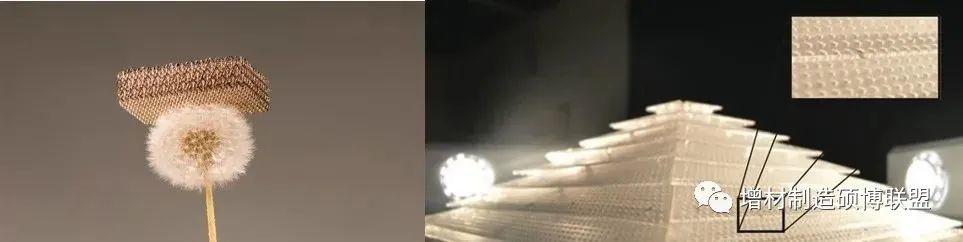
超清金属点阵和声学隐身装置
点阵结构空间还可以作为散热或主动致冷通道,北京航空材料研究院采用点阵结构热交换芯体替代传统板翅结构,大幅度提高了热交换器的换热面积。改变钛合金点阵结构中孔洞的体积分数和尺寸分布,可以解决植入物和骨头之间的弹性失配问题,使植入物具有量身定制的力学性能,此外,点阵结构中的开放性孔洞也更有利于骨内生长和植入物的结合。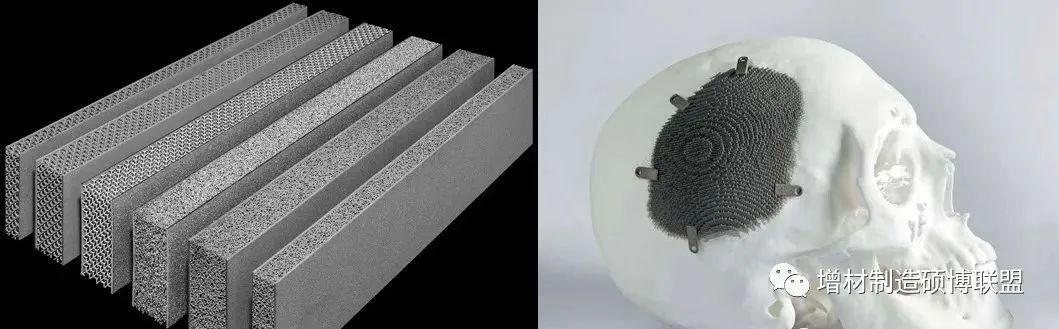
目前金属点阵结构增材制造技术的研究主要集中在成形零件尺寸精度和成形零件性能两个方面。
大型薄壁结构

薄壁结构的特征形式有衬套、壳体、肋板等,在航空发动机叶片、机匣、燃烧室等部位广泛存在。传统铸造、锻造、焊接、机械加工生产工艺周期长,材料利用率低,且一般深径比超过10:1的薄壁结构就很难采用数控加工制备。相比而言,增材制造比较容易实现大深径比薄壁结构的制备。不过,增材制造过程中零件局部温度场呈现动态变化,相比实体结构,薄壁结构散热面积小、温度变化大、结构刚性差,其成形过程极易受温度场变化的影响,成形稳定性较差。薄壁结构一直是增材制造研究的热点与难点之一。 
铂力特激光立体成形多层薄壁结构
目前,针对薄壁结构定向能量沉积增材制造成形过程中的温度场、尺寸精度控制等已经做了大量研究,但由于薄壁结构对增材制造工艺条件和环境的变化十分敏感,成形过程中的每个细微波动都会逐层累积,进而影响后续成形,因此保证成形过程的稳定性是获得质量优异薄壁件的关键。建立可靠的增材制造过程实时监控和反馈系统,实现闭环控制,是提高大型薄壁件增材制造成形过程稳定性,提高成形的精度的有效方法。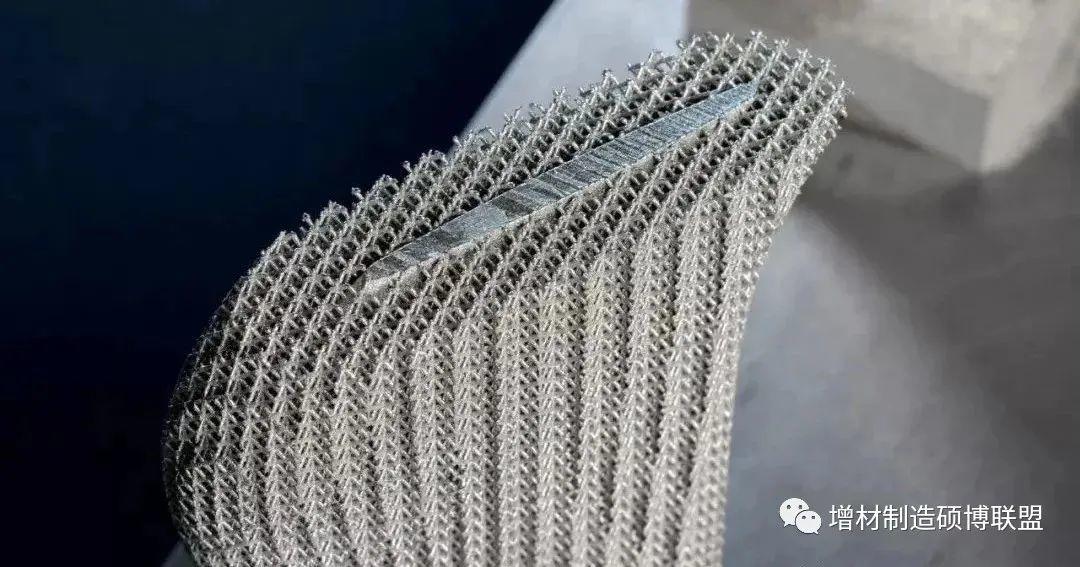
Fraunhofer为薄壁结构开发点阵保护支撑
复杂曲面是指包含如球、椭球、双曲面等二次曲面和自由曲面的组合曲面。当前个性化且具有复杂曲面的零件日益广泛地应用于人们的生产生活中,在飞机、船舶、汽车等重要制造行业,为满足流体力学要求,常需采用结构复杂曲面结构;部分艺术品等,需要通过复杂的外型结构设计来满足人们日益增长的审美需求。如何高精度、高效率和低成本地制造这些复杂曲面结构,是工业设计领域对现代制造业提出的基本要求。增材制造由于其独有的成形工艺,在加工曲面零件的复杂表面和内部结构方面,具有独特的制造优势。 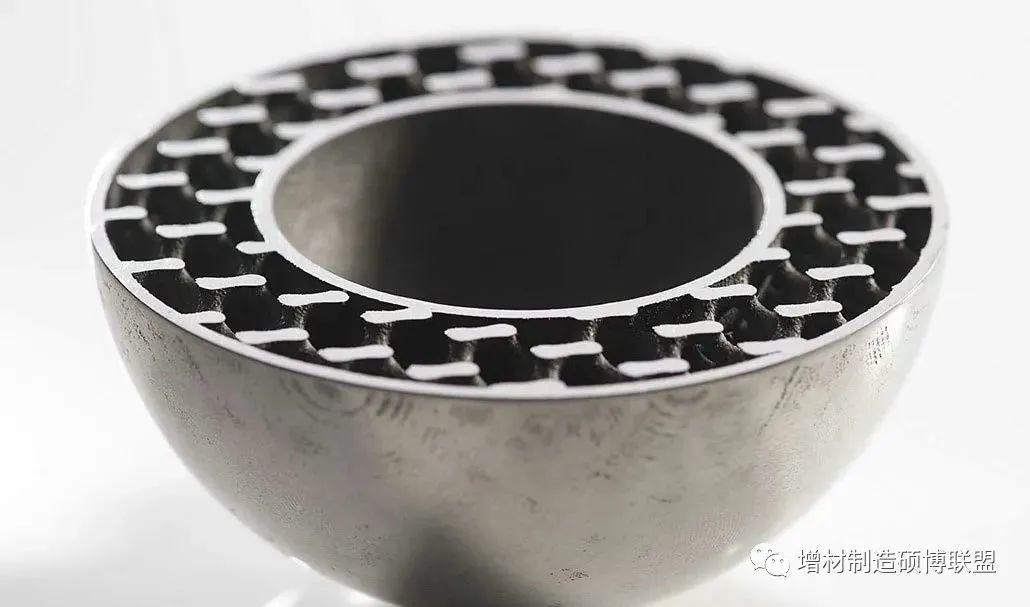
含点阵的半球体结构
GE公司采用增材制造技术制备了具有自由空间曲面的发动机风扇叶片。美国Los Alamos实验室(LANL)采用螺旋轨迹扫描技术制备出全致密半球零件。国内北京航空航天大学、北京航空材料研究院、西北工业大学等单位均采用LMD技术制备了带空间自由曲面叶片的航空发动机整体叶盘。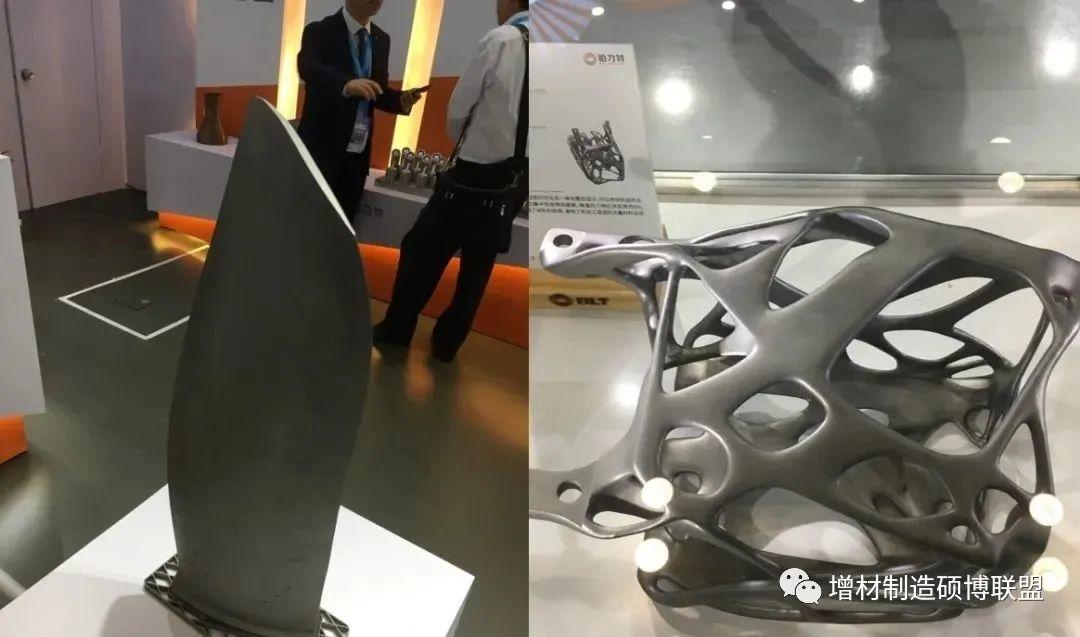
增材制造发动机风扇叶片和拓扑天线支架
增材制造成形空间复杂曲面结构的研究,大多集中在针对特定材料、特定工艺参数下的临界成形倾角的确定,较少关注具体结构的成形。实时监测及闭环反馈控制同样是提高复杂曲面结构增材成形过程稳定性、保证成形精度的有效途径之一。
结构一体化是零件设计和发展的重要趋势,增材制造可以将原本由多个构件组合的零件进行一体化制备,避免了多个零件组合时所需的连接结构,如法兰、焊缝等。
GE公司将原本20多个零件的燃油喷嘴进行一体化设计与SLM制备,并将其应用到 LEAP发动机上,不仅改善了喷油嘴容易过热和积碳的问题,还使其服役寿命提高了5倍。霍尼韦尔公司采用EBM制造了镍基合金HTF7000发动机的管腔,由原本的8个部件组合形成1个部件,交付周期从几个月大幅缩短至几周,生产成本降低50%。一体化结构还被广泛应用到航空发动机整体叶盘、增压涡轮、支座、吊耳、起落架等其他结构。空间异型管道的传统制造工艺为注塑成形、铸造等方式,不仅制造成本高、生产周期长,对于管道需要的复杂样条曲线一次很难制备成功,增材制造为空间异型管道一体化制备提供了可实用的技术。
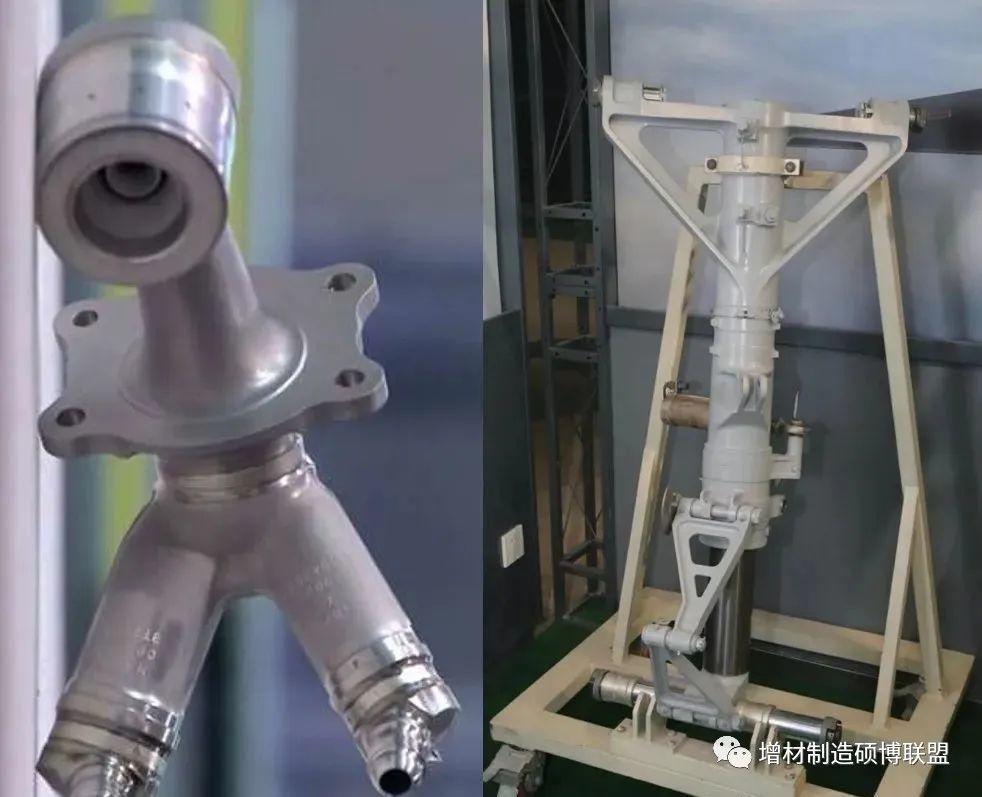
3D打印一体化制造的燃油喷嘴和飞机起落架
除了静态结构以外,增材制造还能方便实现动态机构的一体化制造。动态一体化机构特点在于免组装、可实现动态联接,传统机械构件需要分步制备各个单独构件,然后再将其装配起来,而增材制造可直接得到免组装的整体机构,节省装配步骤。 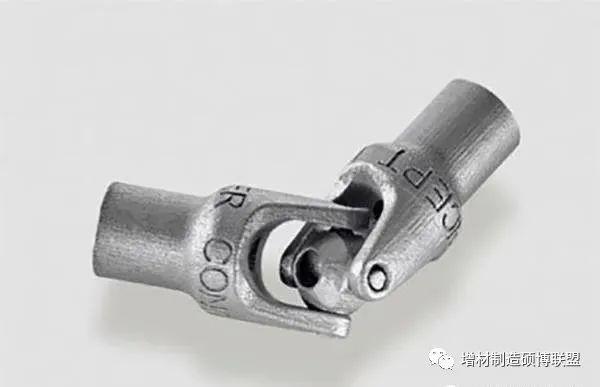
一体化制造的免组装铰链结构
增材制造在复杂结构制造方面具有显著的优势,不过要实现大批量工程化应用仍有大量基础科学问题需要解决。增材制造构件的表面质量与同等尺寸精密铸件相比尚存一定差距,目前常规SLM成形的尺寸精度为0.1mm左右、表面粗糙度Ra在6.3μm左右,EBM成形精度为0.1~0.2mm、表面粗糙度Ra为20~30μm。
此外,增材制造成形过程伴随着复杂的物理、化学、冶金过程,应力变形控制难度大,十分容易产生气孔、未熔合、裂纹等冶金缺陷,严重影响构件尺寸精度及力学性能。进一步加强增材制造基础工艺研究,揭示成形过程中应力演变规律、快速熔凝固原理、变形开裂行为、内部缺陷形成机制等,依然是今后增材制造复杂结构的研究重点。来源:增材制造硕博联盟