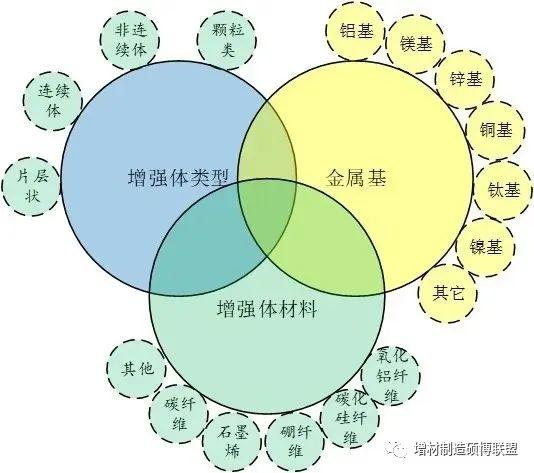
激光粉末床熔融LPBF增材制造的最新进展为陶瓷增强金属基复合材料的发展开辟了一条新途径。独特的逐层工艺方式简化了复合材料制造的工艺路线和交货时间。采用SLM技术制造陶瓷增强金属基复合材料有以下优势:
1.第二相强化和晶粒细化。陶瓷颗粒具有较低的密度和热膨胀系数,以及较高的硬度、模量和强度。添加陶瓷颗粒可以提高金属基体的强度、硬度和耐磨性。此外,陶瓷(尤其是纳米级陶瓷颗粒)可以作为异质形核位点,从而阻碍晶粒的生长和细化凝固晶粒。除此之外,熔池凝固过程中的高冷却速度有利于形成细晶粒,可以进一步提高强度和硬度。 2.提高激光吸收率。激光吸收率对SLM形成质量有重要影响。在1060nm波长的激光下,陶瓷对激光的吸收率高于金属。因此,这些陶瓷的加入可以提高金属基体的激光吸收率,从而有效提高成形效率及零件性能。 3.提高零件的成型质量。使用陶瓷颗粒可以改善熔池稳定性和液相的粘度,从而提高制件机械性能。同时,激光加工过程中陶瓷和金属之间的原位放热反应可以提高熔池的温度并提高零件的密度。此外,陶瓷颗粒还能阻碍裂纹扩展,这对于提高机械性能至关重要。
华南理工大学机械与汽车工程学院、广东省科学院新材料研究所、武汉理工大学材料合成与加工先进技术国家重点实验室等单位的研究人员提出通过加入SiC颗粒可以诱导C300马氏体时效钢(MS)原位析出相的形成,从而制备出SiC和原位析出相双相增强的MS基复合材料。相关研究成果以题为 “Duplex strengthening via SiC addition and in-situ precipitation in additively manufactured composite materials” 发表在复合材料学科顶级期刊《Composites Part B: Engineering》。 doi.org/10.1016/j.compositesb.2022.109820 与以往研究中主要通过陶瓷颗粒强化金属基复合材料不同,本工作研究了SiC增强沉淀硬化钢以引发原位沉淀并促进双相强化,通过激光粉末床熔融LPBF技术制备的马氏体金属基复合材料的抗拉强度和屈服强度分别达到1.6Gpa和 1.2Gpa,相比基体材料分别提高了38%和29%,同时保持了10.1%的延伸率。 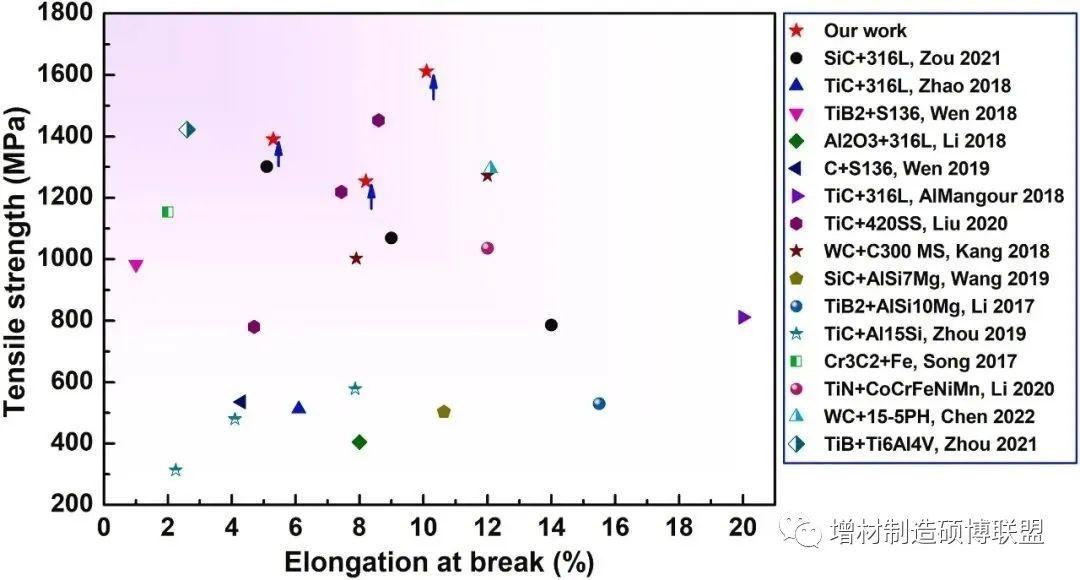
本研究制备的MS-SiC复合材料的力学性能及与以往研究的对比 目前采用LPBF技术加工的陶瓷增强金属基复合材料可分为异位制备和原位制备两种方法。异位制备是将陶瓷颗粒与金属粉末直接混合,然后进行LPBF打印。由于增强材料和基体之间的物理不匹配,以及在陶瓷颗粒表面形成氧化膜,通过异位方法形成的复合材料可能会遇到界面结合问题。相比之下,原位方法通过两种或多种原材料之间的化学反应在基体中形成强化相,从而实现稳定的热力学性能和更均匀的强化颗粒分布。此外,原位制备可以避免氧化,从而提高界面结合强度,并且可以获得比非原位制造更好的机械性能。 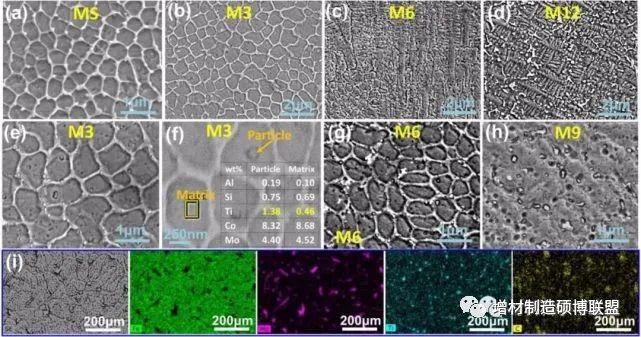
LPBF制备SiC颗粒增强MS基复合材料的显微组织 与现有主要由陶瓷颗粒增强的3D打印陶瓷增强金属基复合材料不同,华南理工大学的团队研究了通过添加陶瓷颗粒的原位触发沉淀,这促进了金属基体的双相强化(陶瓷颗粒+沉淀物)。选择马氏体时效钢作为基体,因为其在热处理后可以通过金属间化合物实现沉淀硬化。研究人员推测,这些沉淀物可以通过添加陶瓷颗粒后在LPBF过程中原位异相成核。碳化硅因其高模量和硬度、较低的密度和良好的激光吸收而被选为增强陶瓷。SiC和Fe在1060nm波长激光下的激光吸收率分别为0.78和0.64,这表明根据复合粉末中吸收率的混合规则,添加SiC可以提高马氏体时效钢的激光吸收率。此外,SiC与铁具有良好的润湿性,可以抑制复合过程中棘手的界面键合问题。团队人员对SiC的含量对致密化的影响行为、微观结构演变、沉淀动力学、机械性能和底层强化机制进行了研究。 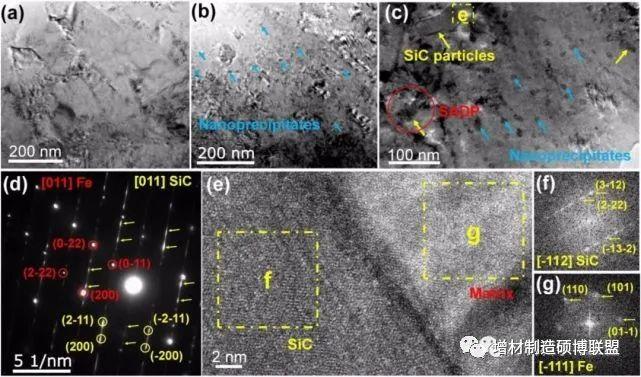
TEM组织图谱
1. 复合材料的激光成形性随着SiC添加量的增加而降低。12% 的SiC添加量时样件的致密度超过99.4%。当添加量为15 vol%或更高时,会观察到明显的缺陷(如大孔和毫米大小的裂纹)。此外,轻质SiC 的添加降低了复合材料的密度,从而提高了比强度。 2. SiC的添加对显微组织有显著影响。添加SiC后,微观结构形态从胞状结构变为树枝状结构。在没有后热处理的情况下观察到大量纳米沉淀物,由于SiC颗粒和位错可以作为优先成核位点,因此可以通过异相成核原位形成。沉淀动力学分析表明,添加SiC提高了成核速率。SiC颗粒可能与基质和原位形成的化合物颗粒发生部分反应。残余应力随碳化硅含量的增加而增加,碳化硅促进了奥氏体相的形成。 3. 新制备的复合材料的硬度和强度随着SiC添加量的增加而增加。12% 的SiC添加量时样件的硬度达到438 HV0.1,同时达到了约1.2 GPa的最大屈服强度,相比基体马氏体钢相比增加了约29%。此外,3%SiC添加量时样件实现了最高的抗拉强度1.6GPa,增加了约38%。
总体来说,华南理工大学的团队所采用的与现有主要由陶瓷颗粒增强3D打印陶瓷增强金属基复合材料不同的制备方法,使材料的最高屈服强度和抗拉强度分别大幅度提高。潜在的强化机制包括析出物和SiC颗粒双相第二相强化以及位错强化。