悬置系统非线性刚度与间隙设定
通常来说,按照GMW14116这一悬置设计标准,非线性刚度曲线的开发应考虑满足图1所示的要求: 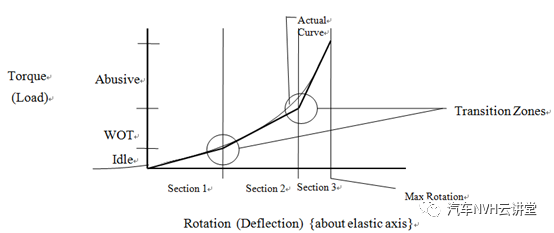
在怠速区间,动力总成悬置子系统主要受一稳态转矩脉冲,子系统主要任务是隔振。Section2: 节气门全开 Wide-OpenThrottle (WOT) – 高频隔振及控制在节气门全开区间,动力总成悬置子系统主要受一稳态转矩脉冲,子系统主要任务是隔振,次要任务是控制。在极限工况,动力总成悬置系统主要受过渡转矩,控制动力总成运动主要任务。1、过渡区域应尽可能的光滑以避免在不同区域产生明显变化。2、在怠速负载下,悬置负载应落在第1部分的前半部分内。3、在正常行驶负载下,悬置负载应落在第2部分的前半部分内。4、在节气门全开负载下,悬置负载应落在第2部分内。1.如果使用线性段刚度足以解决限位、耐久和NVH问题,那么任何的非线性刚度设计都是多余的和错误的。2.在满足限位、耐久的前提下,尽可能将非线性刚度设计的平缓是始终需要追求的目标.比如Ⅲ WOT U向刚度要低于450N/mm。往往会出现设计值与实测值差距较大的情况,需要做校核(见图1)。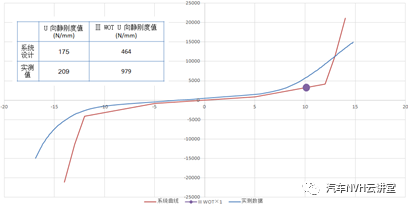
3.发动机类型(汽油机、柴油机)、排量、涡轮增压、缸内直喷等任何能导致缸压增大,或最终使发动机振动增大的技术,都需要在悬置非线性刚度设计的时候予以考虑。即发动机振动越大,对应的悬置非线性刚度需更低更平缓。4.同平台的悬置系统设计,需首先解决振动最大、扭矩最大的悬置系统设计,之后依次校核较低发动机振动和较低扭矩的悬置系统。一般绕曲轴转角是对扭矩直接作用方向悬置非线性刚度设计的刚性约束,目前多数公司使用±3.5°(见表1)。
表1动力总成最大允许位移及转角
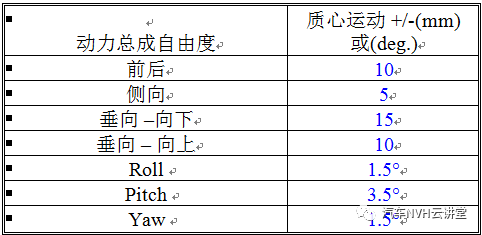
2.但是对于排量大、扭矩大或扭振大的发动机,为了确保NVH性能,需尽可能降低关键载荷点处(比如III WOT)的刚度,这时只能通过两种策略来实现:2)或允许使用限位行程更大的悬置,并使绕曲轴转角达到±5°范围,这样也可以降低每个悬置的关键载荷点刚度。更轻的车身、更大扭振的发动机对悬置系统设计提出了很大的挑战。这种情况下如仍使用硬限位行程较短的悬置,会导致下述情况:1)关键载荷点刚度很难降低,对应关键载荷点隔振差,振动传递多、结构声和声品质可能不好;2)如果硬限位行程较短,后期发现存在问题,再重新设计调整需要更改很多部件,比如外围支架需要重新设计,改模周期较长。实践经验认为,对于三点TRA悬置系统,左右悬置硬限位行程需达到20mm,这样才能有效保证III WOT刚度处于可接受的范围,而对于抗扭拉杆的硬限位距离,需尽可能达到25mm,抗扭拉杆是重要的结构声传递路径,必须加以控制(见图2)。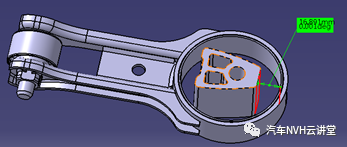
1、圆柱形悬置硬限位距离对车内噪声的影响,见图3和图4.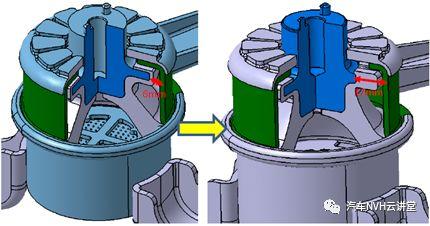
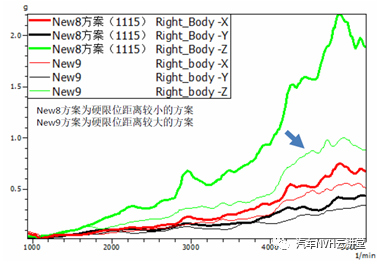
2、梯形液压悬置硬限位距离大小对车内加速声品质的影响,见图5和图6。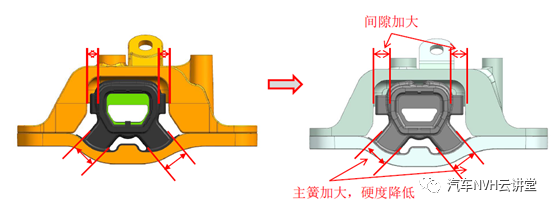
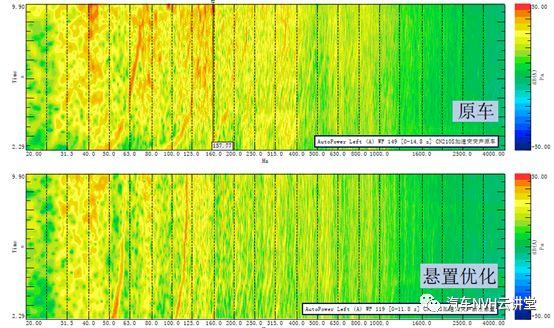