后桥独立主减悬置优化设计方法
Optimization Methods for IRS Axle MountDesign Yuejun E. Lee and Vince Monkaba
Visteon, Axle & Driveline SBUVisteon, CAE Tools and Methodologies在车辆设计的早期阶段,确定后桥独立主减(IRS)悬置位置和刚度至关重要。根据车辆的不同,IRS后桥悬置的设计要求也不同。设计目标包括零roll条件、静态roll条件和动态roll条件。目前,还没有针对动态roll工况的(IRS)后桥独立主减悬置设计方法。目前的设计方法对于其他两种要求也缺乏准确性和鲁棒性。本文阐述了为实现这三个目标而开发的IRS后桥独立主减悬置设计方法。这些方法在三点布置后桥独立主减悬置(IRS)上得到验证。此外,将刚体模态置于所需频率。与现有方法相比,该方法具有更高的精度和鲁棒性。它们可以显著提高设计质量和生产率。车辆NVH设计试图将传递到车身的后桥和传动系激励减至最小。对于车辆的耐久性,重要的是最大限度地提高车轴悬置的寿命。因此,轴安装位置和刚度的选择一直是后桥独立主减悬置设计中的一个挑战。今天,原始设备制造商和供应商正在密切合作,寻找最好的后桥独立主减悬置设计。与发动机悬置设计实践类似,后桥独立主减悬置可以建模为安装在车身上的集中质量。因此,用于发动机悬置设计的原理可直接应用于后桥独立主减悬置设计。发动机悬置NVH设计采用了三个原则[1]。这些是静态Roll条件,动态Roll条件和模态放置。在静态Roll条件下,将悬置刚度辊轴置于静扭矩轴上,在静力矩作用下产生纯滚动。动态Roll条件的重点是对准悬置刚度转轴与扭矩轴和解耦动态辊。模态放置的思想是将动力总成固有频率移动到期望的频率,而不考虑刚度转轴的对准。如前所述,由于后桥独立主减悬置作为集中质量安装在车身上,上述三个原则可直接应用于后桥独立主减悬置设计[2]。此外,为了耐久性,应满足零滚转条件,以实现三个后桥独立主减悬置的两个前(或后)悬置的相同疲劳寿命。由于扭矩和俯仰轴通常是不同的(图1),因此不可能同时将悬置刚度弹性轴线与两个轴线对齐。因此,根据具体应用,通常使用上述设计标准之一。一般情况下,设计一级后轮驱动(RWD)车辆时,应满足零侧倾条件,以获得相同的后桥悬置疲劳寿命。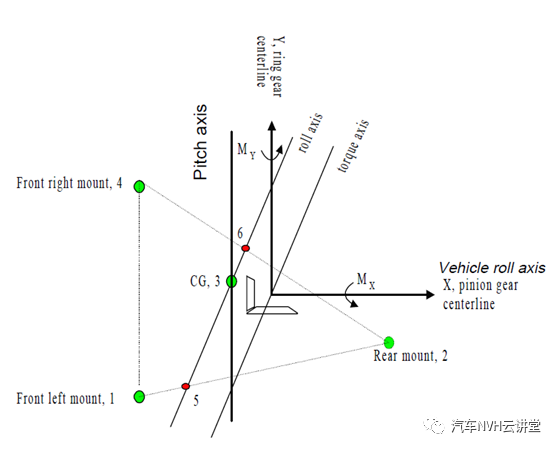
另一方面,对于基于前轮驱动(FWD)的全轮驱动(AWD)车辆,在前轮上分配更高的扭矩,将Roll模态与其他模态(如pitch, yaw等)分离变得更为重要[3]。这主要是为了改善车辆的NVH特性,以及使微调系统响应更容易。在某些情况下,也可以使用在所需频率下放置正常模态的方法。由于缺乏可靠的设计工具,目前工程师们仍在使用试错法来寻找更好的轴安装设计。为了改进设计方法,对技术进行了回顾,并对四种设计工具进行了比较[2]。基于本研究的结果,提出了两种新的设计方法,即使用GenesisV5.0优化软件[4]和内部工具[5]。在本节中,给出了零roll条件、静态roll条件、模态匹配与跟踪以及动态roll条件设计的优化设计问题公式。对于前三种设计,使用Genesis V5.0。在动态转动轴设计中,使用了内部工具。Genesis是VMA工程公司开发的商业优化软件,它可以进行拓扑、尺寸和形状优化。应用其尺寸和形状优化函数,可以找到满足零转动条件和静态转动条件的悬置位置和刚度。利用其模态匹配和跟踪能力,人们还可以在所需频率下放置和跟踪各个模态。然而,作为一个限制,它不能控制模态形状时,放置模态频率。内部工具是一个发动机悬置NVH设计工具。它将所有刚体模态的模态能量置于所需频率,并解耦模态形状。本研究使用了一个带有三个悬置(两个前悬置和一个后悬置,图2)的后桥独立主减,其有限元模型如图3所示。准双曲面齿轮传动比为3.31。使用相同的悬置衬套用于两个前悬置(网格3和5),以减少制造复杂度。结果,总共选择了15个设计变量,其中包括6个刚度和所有三个悬置的9个x、y和z位置。独立后桥主减组件被建模为一个集中质量单元,放置在其重心(例如网格9)和几个刚性单元,以确定准双曲面小齿轮(网格27)和差速侧齿轮(网格14和15)的位置(图3)。在准双曲面小齿轮上施加1000(牛米)的输入扭矩,在差动侧齿轮上施加3310(牛米)的阻力扭矩(根据3.31的传动比计算),其位置由从属节点(网格14)确定。网格8和9定义了在网格9上通过C.G的俯仰轴。为了定义有效扭矩轴(或刚度滚动轴),使用网格9和10。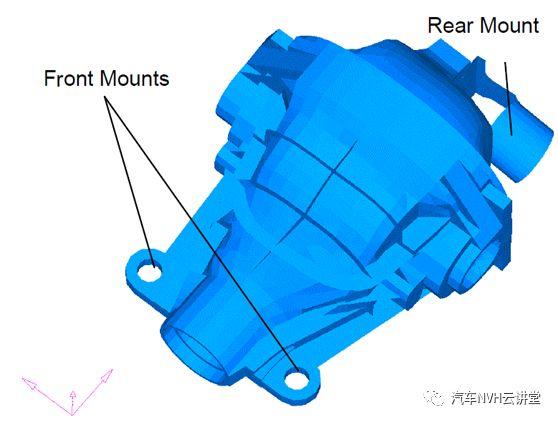
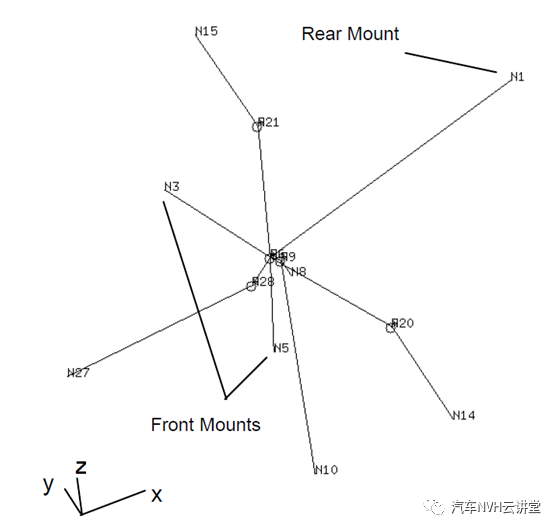
零转动条件是当车辆受到有效扭矩时,车轴仅绕车辆坐标系中的pitch轴(图1)旋转。优化问题是通过最小化两个前悬置的垂直位移差来实现的,该约束仅在允许pitch轴的旋转自由度的约束下进行。静态转动条件是通过将刚性转轴平行于静扭矩(或有效扭矩,图1)轴对准,同时迫使硬度转轴穿过后桥独立主减的C.G(3)。优化问题是通过最小化定义静态转矩轴的网格9和10的所有平移位移来制定的。Genesis提供了将系统固有频率与目标值匹配的能力,同时在设计变更期间跟踪系统模态。利用该功能,可以设计出具有期望固有频率的系统,并在不同的设计周期内跟踪模态开关。目标是将第一、第二和第三模态分别移动到10、20和30(Hz)的任意选择值,同时跟踪模态以进行可能的模态切换。内部工具是一个发动机悬置NVH设计工具。它使用能量方法将接地发电厂所有刚体模态的模态能量尽可能接近期望频率。在主目标函数中,它既包括模态的形状,也包括模态的频率。基于解耦(仅限振型)的二次目标函数可用于在频率和解耦之间进行权衡。扭矩转轴[5 ]用于定义安装刚度转轴。由于发动机和后桥独立主减悬置系统的相似性,将内部工具应用于后桥独立主减悬置非常简单。输入数据的实现使得只有滚动模态是解耦的。Genesis在三次迭代中收敛到零滚动条件的解。前悬置力见表1。可以看到,两个前支座上的力相等。在表2中还提供俯仰轴运动数据,其仅示出Y轴上的旋转位移(Ry),其绕X轴和Z轴的零旋转。因此,Genesis可以用于三维空间的零转动条件设计。与当前的二维Excel电子表格设计过程相比[3]。创世纪在更短的时间内提供更精确的设计。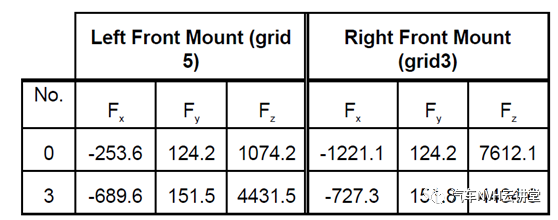
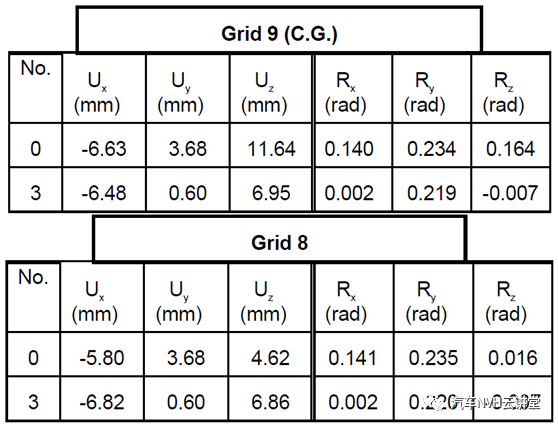
Genesis花了10次迭代才找到一个满足静态侧倾条件的设计。表3示出了定义静态转动轴的两个网格、网格9和10的位移。正如可以看到的,两个网格的位移都是零,除了绕X轴(Rx)旋转。该X轴在局部坐标系中定义并与转矩轴对齐。因此,静态横摇条件在设计迭代10时实现。因此,Genesis可以用于三维空间的静态滚转条件设计。与当前的二维Excel电子表格设计相比[6],Genesis在更短的时间内提供了更准确的结果。
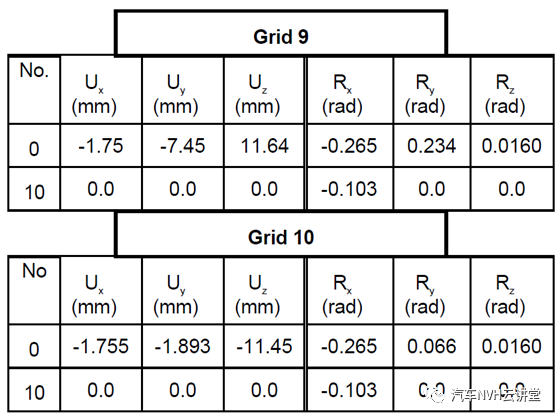
表4显示了设计迭代0和4时的后桥正常模态。我们可以看到模态1、2和3与目标值10、20和30(Hz)匹配。在本例中,由于没有模态切换,因此没有报告跟踪数据。否则,模态切换警告信息以及原始和新的模态命令将在Genesis输出文件中报告。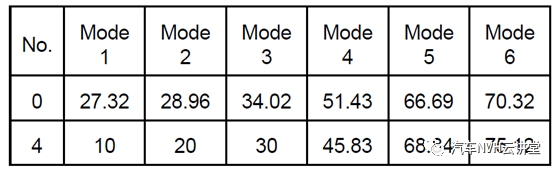
表5显示了初始和最终设计的三个悬置的安装刚度和位置。该工具输出从几个随机起点获得的解。其中,选取目标函数值最小的作为最终设计方案。在表5中,给出了其中一个最终设计。然而,它发现了其他具有相同目标函数值的设计。此外,这些设计彼此有很大的不同,其中一些由于其他设计原因(如包装空间)而不实用。这意味着,使用当前公式,设计空间中的响应面是一个平面。缩小设计空间可以消除这个问题。在本例中,施加的唯一约束是分离滚动模态。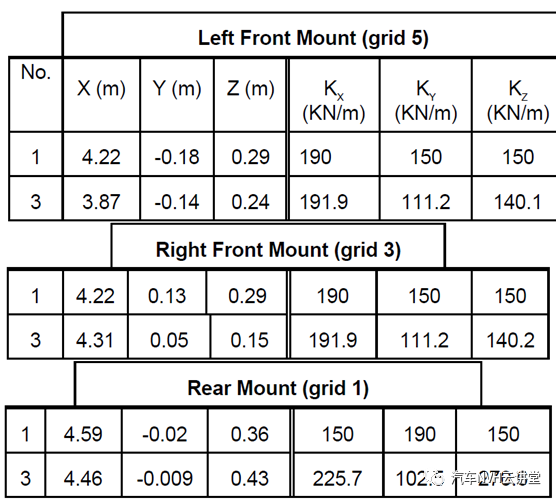
请注意,这不是报告的最终解决方案;而是随机开始解决方案2。表5中给出的设计也通过Genesis进行了验证。一般来说,如果滚转模态是解耦的,则当轴在其滚动模态频率下被激励时,C.G应该只绕转矩辊轴旋转。为了验证这一点,创建了一个局部坐标系,其X轴与从先前结果中找到的扭矩滚轴对齐。在系统滚动频率(93.82hz)下施加动态扭矩。在新的扭矩-滚转轴坐标系中发现了C.G的位移。Y轴和Z轴的平移位移和旋转几乎为零(表6),仅围绕转矩滚转轴(X轴)旋转。这表明只有横摇模态被激发,因此横摇模态被解耦。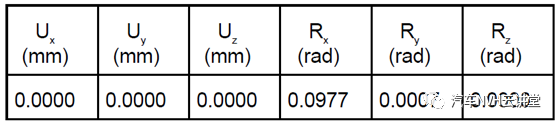
结果表明,Genesis是后桥独立主减悬置设计的有效工具。具体来说,零转动条件、静态转动条件和模态匹配可以在三维空间中实现。Genesis还可以处理一般的有限元模型,包括梁、集中质量、弹簧和刚性单元。该工具可用于三维空间中的动态转动设计。通常,该工具在放置模态频率、匹配模态形状和解耦模态方面更为强大。尽管在本报告中评估了三个悬置系统,但这些方法也可以应用于四个悬置设计。The authors would like to express theirthanks to Scott Bergeon, Farrokh Sabeti from Ford Motor Co., Gary Kopp and ToddFreeman from Visteon ADSE NVH Section for their kindly supports.1. R. Solomon, “Reduced Shake Engine MountSystems”, Automotive Engineering International, April 1998.2. Fatma Kocer; Yuejun Lee, “Review of CAETools for IRS Mount Optimization”, Engineering Tools and Methodology, Report #A935 C-99-0.28, October 1999, Visteon Corp.3. Todd D. Freeman, “Rear Axle IsolatorSystem Design Overview”, Visteon ADSE Internal Report, November 1998.4. VMA Engineering, “Genesis User Manual -Version 5”, November 1998.5. Scott Bergeon, “Mount DesignOptimization Tool Manual”, Ford Report, June 1998.6. Arcaris, R. (1995), “IterativeThree-Mount Axle Optimization”, Personal Note.Yuejun Lee, ylee10@visteon.com刚性转动轴(Stiffness roll axis)是系统在指定扭矩下旋转的轴线。扭矩轴(Torque axis)是施加有效扭矩的轴。扭矩辊轴(自由自由扭矩辊轴)被定义为无约束系统由于施加的转矩而旋转的轴。扭矩辊轴是系统惯量和所施加扭矩的轴线的函数。这个轴穿过系统的重心。零侧倾状态(Zero-roll condition):在有效扭矩下,后桥作俯仰运动,无侧倾角。静态滚动条件(Static-roll condition):将刚性辊轴与有效扭矩轴对齐。动态滚动条件(Dynamic-roll condition):将刚性转动轴与扭矩转动轴对齐。
往期相关推荐
相关文章,在仿真秀官网搜索:
ADAMS悬置计算基础1:手把手教你用ADAMS建模分析悬置系统固有频率
ADAMS悬置计算基础2:手把手教你用ADAMS计算悬置静载及动力总质心位移转角