基于CAE分析的优化设计方法及变速器后悬置支架优化设计
[摘要]文章提出了基于CAE分析的优化设计方法,介绍了基于CAE分析优化设计方法的工作流程。基于此流程对某车型变速器后悬置支架进行了优化设计,改进了后悬置支架的结构,既减少后悬置支架的质量又确保了零件性能。 传统的产品设计流程是一个人工反复的过程,工程师借助CAD工具进行产品的设计,然后提交到工厂进行加工制造,接着对产品进行实物试验,如果产品不能满足功能要求或者失效,就需要对产品设计进行修改,甚至重新设计,如此反复,直到产品在实物试验中满足全部要求。这是一个周期长,耗费高的过程,已经完全不能满足现代产品设计的要求。 随着计算机软硬件技术的发展,CAE技术日趋成熟,各种数值仿真方法,如有限元、多体动力学、计算流体力学等技术在产品设计中得到大量的应用。产品在初步设计完成后,可以基于CAD模型进行产品性能的虚拟试验,初步考察其工作应力、运动过程、产品寿命等。如果产品不能满足要求,可以立即返回设计人员进行修改或重新设计,从而大大减少实物试验的周期和费用(见图1)[1]。 Altair公司的Hyperworks有限元分析软件提供了良好的优化设计环境,把基于CAE分析的优化设计流程氛围两个典型的阶段,第一阶段是概念设计阶段,首先对设计对象进行分析,确定设计对象的概念设计空间,概念设计空间要包括设计对象的整个轮廓,分析设计对象的载荷工况和设计优化参数,利用拓扑优化的有限元计算方法对整个概念空间进行拓扑优化,获得设计对象的初步拓扑结构,根据设计要求及生产工艺提取初始的概念设计模型。第二阶段是详细设计阶段,主要是转化概念设计模型,对设计对象的几何模型细化分析,确定合理的优化参数,使设计对象的结构满足强度,刚度及加工工艺要求,使材料的力学特性充分利用。这种设计方法效率高,可以提高产品设计质量,降低产品开发成本,缩短产品的开发周期。 以下以某车型变速器后悬置支架为例,详细阐述基于CAE分析和优化设计的方法及步骤。 变速器后悬置支架概念设计几何结构见图2,该件作为动力总成悬置系统中的安全件和功能件,起到支撑悬置、连接变速器以及传递作用在动力总成上的一切力和扭矩,另外,悬置支架的一阶固有频率对车内噪声的影响很大,因此在动力总成悬置系统设计时,应对支架的强度和固有模态进行校核。本文将对此支架在行驶过程中受到的28种不同工况进行应力和模态分析,确保其在所有工况条件下所受应力满足:典型工况下,最大应力应该小于所用材料屈服极限,极限工况下,最大应力应低于材料的抗拉极限的85%。一阶模态大于或接近500Hz。 变速器后悬置支架的有限元模型及边界条件见图3,有限元模型采用线性六面体网格,节单元数为25064。杨氏模量、泊松比、材料性能及密度等见表1。 与变速器连接的三个孔采用固定约束。加载点与零件之间使用刚性单元(REB2)连接,以模拟悬置安装的真实位置,载荷点为发动机悬置硬点位置,载荷见表2,各工况的载荷数据通过ADAMS软件建立悬置系统动力学仿真模型,进行仿真分析而获得。 对后悬置支架进行有限元计算,初步了解后悬置在28种工况下应力情况。得到各种工况下支架所受应力情况如表2所示。由计算结果可知,最大应力出现在向后ROCKCYCLE转矩工况,该工况的应力分布云图见图4。从云图上看,支架尾部安装点处所受应力很小,可以通过改变悬置支架的结构,提高支架的应力水平,使材料的利用率得到提高,同时降低变速器悬置支架的质量。 根据后悬置支架概念模型预分析结果,结构优化的目标是改变后悬置支架的几何机构,降低质量,提高材料利用率。利用Altair公司的Optistruct软件对后悬置支架结构优化,对优化结果提取概念性CAD模型(见图5),图中支架尾部的材料对零部件的力学特性贡献很小,这部分材料可以去掉,不影响零部件的受力特性。 为了对优化后的设计方案与原设计方案进行全面的比较,需对各种工况条件下的应力和模态进行对比。对拓扑优化结果重新生成的CAD模型重新划分有限元模型。与变速器连接的二个孔采用全约束。加载点与零件之间使用刚性单元(REB2)连接,以模拟悬置安装的真实位置,载荷点为发动机悬置硬点位置,载荷见表4。 通过对支架优化前后的最大应力工况及一阶模态进行对比,结构见图6、7。 由有限元分析结果可知,后悬置支架在去掉尾部螺钉安装孔后,最大应力和模态都没有明显的变化。但支架质量可以减少0.15Kg,按铸铝材料18元/公斤来算,此更改可节约2.5元/件的成本,可见该优化既降低了成本,而且还节省了安装空间。 1)基于CAE分析的优化设计方法直接从概念模型开始,以设计参数为目标进行分析优化,得出设计参数间合理的关系,确定设计对象合理的结构,这种设计方法将CAE和结构设计结合点提前到了概念设计阶段,设计的目的性更加明确,设计效率提高,是一种新型的有效的设计方法。 2)对变速器后悬置支架采用基于CAE分析的优化设计方法,后悬置支架的结构更改合理,质量减轻,不仅降低了成本,还节约了安装空间。 3)本文建立的优化设计方法和设计思路还可推广应用到其他汽车零件部件的设计上。在产品结构减重和自主创新领域都有非常重要的意义。 [1] 洪清泉叶洎沅.优化驱动的产品设计流程_产品创新数字化(PLM)_CAE_文库2007 .5 [2] 吕兆平基于有限元技术的发动机悬置支架拓扑优化设计研究汽车工程,2009(4)
往期相关推荐
相关文章,在仿真秀官网搜索:
基于MATLAB+ISIGHT的悬置系统优化设计视频课程推介 著作权归作者所有,欢迎分享,未经许可,不得转载
首次发布时间:2023-04-12
最近编辑:1年前
作者推荐
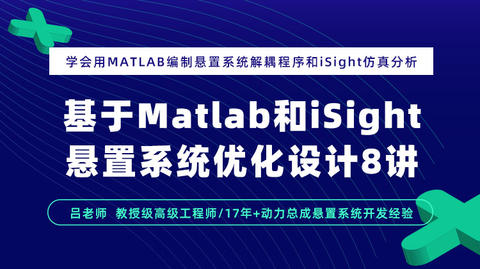