基于整车传递路径贡献分析法的纯电动车啸叫噪声优化
【摘要】本文针对某电动车的车内啸叫噪声,利用逆矩阵法提取问题工况下各激励点载荷,搭建车内啸叫的传递路径贡献量分析模型。根据分析结果,确认了啸叫噪声的主要路径并对该问题路径提出相应改善措施,将电机隔振系统设计成二级隔振系统;搭建刚柔耦合仿真模型,以隔振器的刚度为优化变量,以问题路径的振动传递率为优化目标,对电机隔振系统进行优化。按照优化结果进行装车试制,经实车试验验证,车内啸叫问题得到明显改善。
关键词:传递路径分析;二级隔振系统;逆矩阵法;噪声优化随着电动车技术的发展,电动车的啸叫问题已逐步被行业所重视,由于电动车的动力总成主要由电机和主减速器组成,两者的激励频率都处于中高频段,容易引发啸叫问题,没有发动机噪声的遮蔽,传至车内的啸叫声更明显,严重影响乘员的舒适性。啸叫的传递路径排查是解决啸叫问题的重要手段,传统的路径排查方法主要是啸叫关键频率比对、逐一切断传递路径等经验型排查方法。随着TPA技术的兴起,传递路径的分析方法逐渐科学化、规范化【1】-【3】。TPA方法的关键在于激励点的载荷识别技术,传统的TPA技术采用的是逆矩阵法对载荷进行识别,此方法精度较高,但是整个测试流程耗时较长,工作量大。为了缩短排查时间,先后提出了OPA、OPAX两种载荷识别方法,OPA法是一种完全基于工况测试数据来识别路径贡献量的方法,在建模分析过程中并没有专门的载荷识别步骤,而是基于参考点响应与目标点响应之间的传递关系来分析传递路径对目标响应的贡献。OPAX法是在工况测试数据的基础上建立参数化载荷模型,通过参数辨识技术来进行载荷识别【4】-【7】。OPA法和OPAX法均是基于工况载荷的路径贡献分析方法,相较传统TPA法精度不足,在工程上没有得到广泛应用。电动车的啸叫声属于中高频噪声,不仅通过结构进行传递,也有部分能量通过空气路径传至车内,为了提高模型精度,本文选用了传统逆矩阵法识别载荷,搭建啸叫传递路径分析模型。在实际工况数据采集过程中,汽车声源众多,车内噪声来源复杂,需要对车内噪声与啸叫传递路径的输入响应进行相干性分析,相干性分析是分析输出信号的频率与各输入信号特征频率之间的关系,即确定各辐射声源对目标点噪声的影响。在一个多输入单输出线性系统中,对于输出信号与输入信号有:其中,表示响应信号的自功率谱,表示输出信号中由模型输入信号引起的部分;表示输出信号自谱中由噪声、测试误差所引起的部分。可见,由重相干函数可以得出模型中输入信号对输出信号的影响在全部输出信号中所占的部分。通常根据重相干函数是否大于0.9来判断输入信号是否足够表征系统的输入状况。若两者之间的相关性不足,则说明测试工况数据中车内噪声受其他声源的影响较大。为了排除其他声源的干扰,需对测试工况数据进行多次线性平均处理,将不相关的噪声成分平均掉。根据傅里叶定理可知,一个复杂的信号数据可以视作为多个不同幅值、频率、相位的正弦信号叠加而成。如果其中两个单频信号的幅值和频率相同,但相位相反,它们进行线性平均时叠加而成的幅值为0。因此,将工况测试数据进行多次线性平均后,那些相位关系匹配较差的频率成分会被平均掉。线性平均法虽然能屏蔽不相关的噪声成分,但是对相关信号也会造成一定损失。为了相关信号的完整性,在进行测试工况数据的线性平均时,需要选择一个信号作为相位参考信号,那么与此信号相关的频率成分将不会被平均掉。针对电动车的啸叫传递路径分析模型,在工况数据采集时需在动力总成上安装一个加速度传感器,这个传感器信号就是用来做相位参考的。啸叫传递路径分析模型是基于“源-路径-响应”的系统构架搭建的,
式中为车内响应,为结构路径的传递函数,为结构路径的激励载荷,n为结构传递路径的数量,为空气传递路径的传递函数,为空气传递路径的激励,p为空气传递路径的数量。将汽车视作为一个系统,其啸叫激励源主要是电驱动桥(电机、主减速器),传递路径主要包括悬置、空调管路、车身,响应是指车内噪声及振动。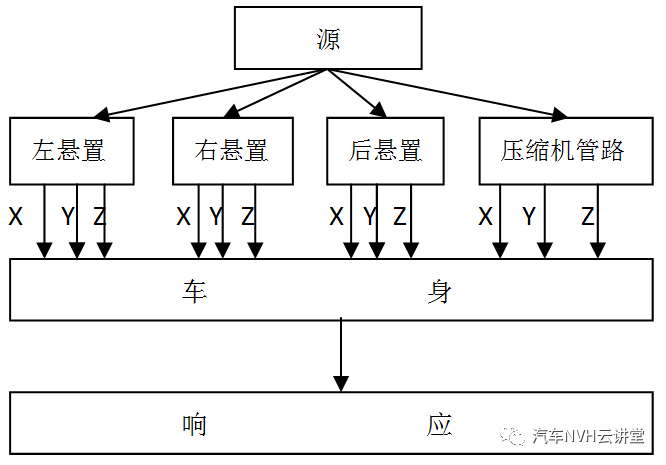
在运行工况下,激励源输出的动态力载荷无法直接获取,需要辅助测试来进行载荷识别。为了准确的识别载荷,需要设置相应的参考点来完成载荷识别。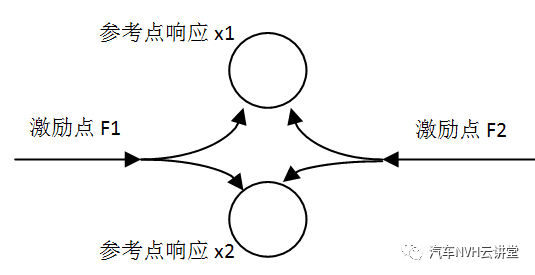
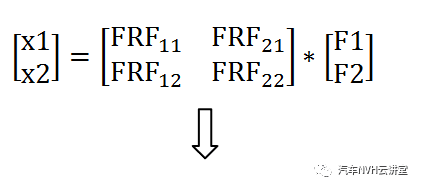
式中为激励点F1至参考点x1的力-响应的传递函数,为激励点F1至参考点x2的力-响应的传递函数,为激励点F2至参考点x1的力-响应的传递函数,为激励点F2至参考点x2的力-响应的传递函数。从公式(5)中可看出,若想要完全解出公式,则传函的逆矩阵必须是正交矩阵,或者说假设系统中有N条传递路径,那么传函的逆矩阵必需由N组线性无关的向量组成。为了增加估计可信度,需要将公式进行扩展,将参考点数目增加至所求传递路径激励力数目的两倍以上,因此公式可表示成式中为所求传递路径激励力矩阵,N为激励力数目(或者说传递路径数目),激励点至参考点的力-响应的传递函数的逆矩阵,为参考点响应矩阵,M为参考点数目,一般取。拓展后的传函矩阵,很容易把外界干扰的无用信息带入计算而产生计算误差,为了尽量减少这类误差的出现,需要将传函进行奇异值分解。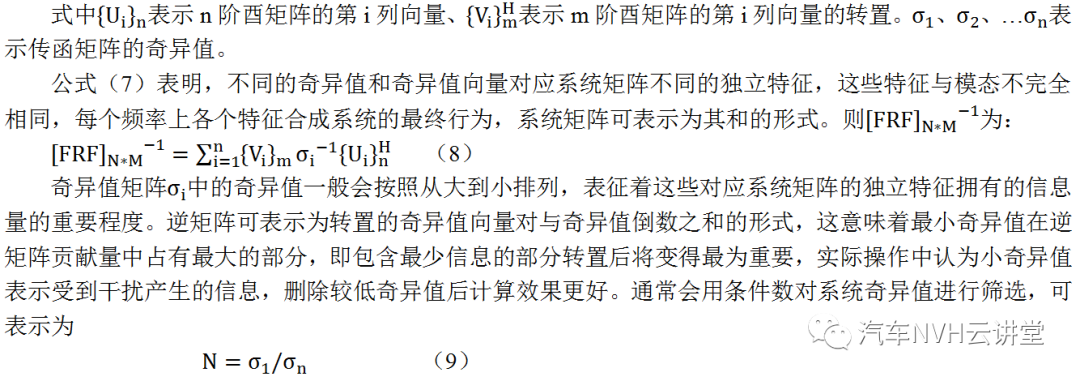

条件数越大,计算精度越小,反之则计算精度越高。西门子软件中存在3种奇异值的筛选方式,分别是个数法、绝对值法、相对值法,给出的推荐条件数为小于100。但是FRF为谱分析曲线,在各个频率下表现出特征信息会有所变化,因此,在实际操作过程中会根据不同频率下实际表现出的特征信息采用更加严谨科学的筛选方式。
首先,条件数特别高的频率段必需删除掉较低奇异值,保证所反求的力载荷计算精度。其次,关键频率段应尽量保持奇异值的完整,以免遗漏关键信息。最后,应在不同频率段使用不同的奇异值筛选方式,使计算精度与保证信息之间达到平衡,但是遇到过小的奇异值可直接删除,因为其对样件行为影响很小。某轻型电动汽车在20km/h匀速工况下啸叫明显,严重影响车内的声品质。为了简要辨别激励来源,首先进行加速工况测试,测试数据记录如图3所示。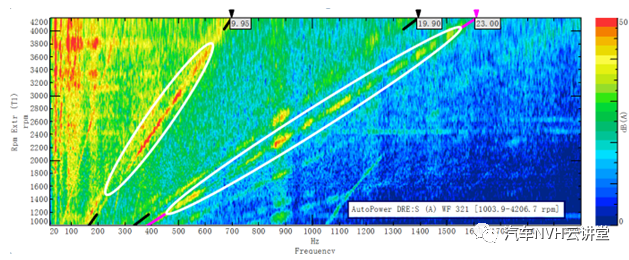
从数据分析,该车啸叫问题主要是由9.95阶和23阶两阶激励引起的,23阶和9.95阶激励分别为电动汽车主减速器的第一减速齿轮啮合阶次和第二减速齿轮啮合阶次,所以该车啸叫问题主要激励源为主减速器,分布频率主要集中在150-600Hz,在汽车匀速20KM/h的工况下其啸叫频率主要集中在500Hz附近。20km/h匀速工况为该问题的主要抱怨工况,因此,本文主要对该工况进行路径贡献分析。如图4所示,该电动汽车以电机与主减集成在一起的电驱动桥为动力总成系统,采用三点悬置支承,空调压缩机安装在电驱动桥上,通过管路与车身连接,每个激励点仅考虑三个平动自由度,忽略旋转自由度。因此,电动车啸叫的传递路径总共有(悬置数目3+空调管路3)12条结构传递路径。在中高频段电动汽车的啸叫存在一部分能量会通过空气传递路径传至车内,但是电机包裹测试验证后,车内啸叫噪声无明显变化,因此,本文的啸叫传递路径主要针对啸叫的结构传递路径。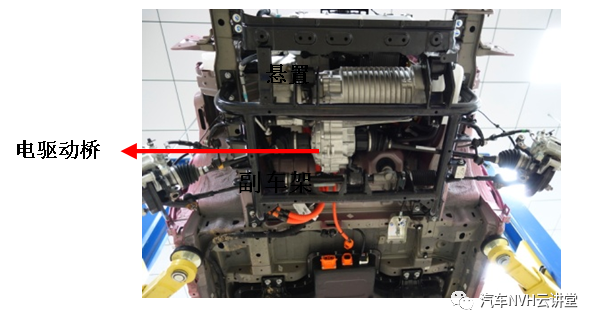
搭建传递路径贡献量分析模型时,需要重新采集工况测试数据,为了降低路面激励对车内声音的贡献,测试必须在光滑沥青路面上进行,信号采集过程中可在线使用频谱分析,同时保留幅值和相位信息,参考相位点选择电机本体振动点,平均方式为线性平均5次/秒,部分测点图片可参考图5。测试工况为电动汽车车速为20km/h匀速行驶工况。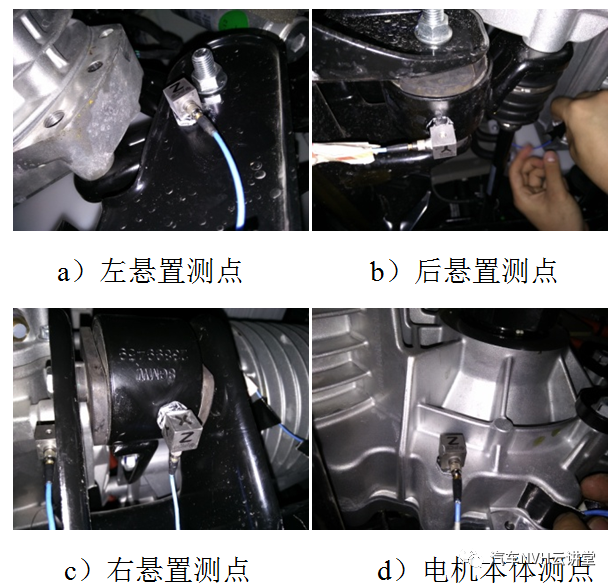
为了搭建传递路径贡献量分析模型,需要测试激励点至车内的传递函数以及用于提取载荷的各激励点之间的相互传递函数。为了保证测试的精度,传递函数的测试在消声室内进行。本次测试采用的LMS的测试设备,在悬置被动端、压缩机管路被动端布置三向振动传感器,具体 位置参考图5,在车内驾驶员内耳布置麦克风,依次用力锤锤击各激励点,输入信号加力窗,输出信号加指数窗,测试数据要求常相干函数大于0.85,各激励点锤击三次,取平均值,测得各激励点之间的结构传递函数及激励点至车内的结构传递函数。将测试所得的工况数据和传函数据代入公式(5),根据公式(7)(8)(9)舍弃较小条件数并针对关键频段(500Hz附件频段)的条件数进行筛选后,运用逆矩阵法得到激励点载荷。各激励点载荷数据如表1所示。
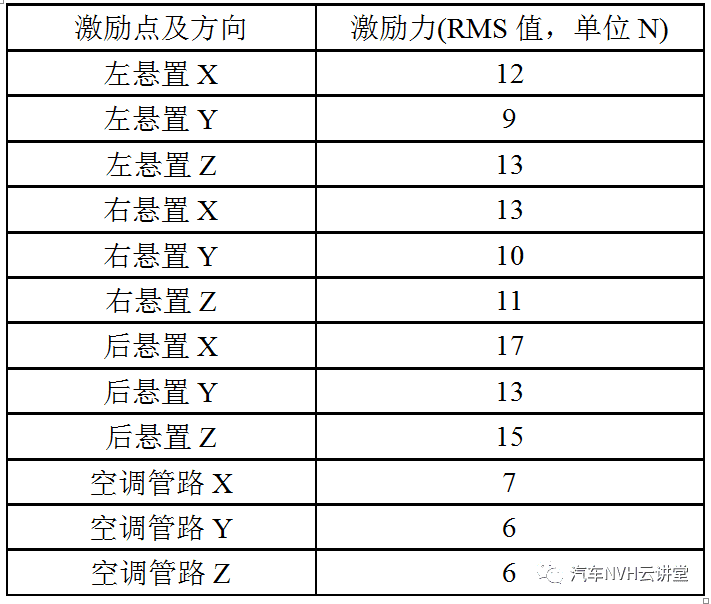
激励点处提取的载荷显示,后悬置X、Z向的激励力略高于其他路径。将提取的载荷数据及测试得到的激励点至车内结构传递函数数据代入公式(3),拟合得到的车内噪声与测试的车内噪声对比结果如图6所示,各路径的贡献量分析结果如图7。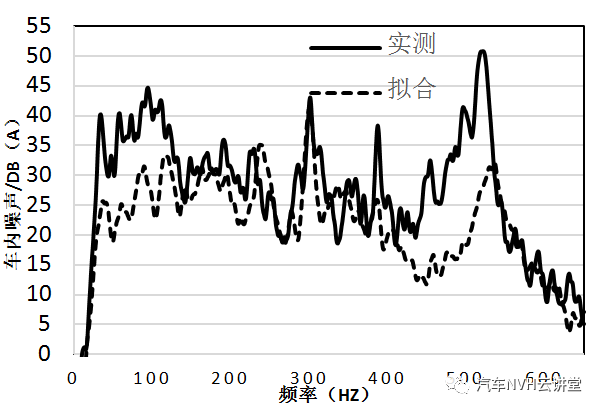
从对比结果可看出,由于本文分析的传递路径为啸叫的结构传递路径,因此拟合结果与实测结果在幅值上有所降低,但是关键频率的峰值频率基本吻合,该传递路径贡献量分析模型可作为解决车内啸叫噪声的参考。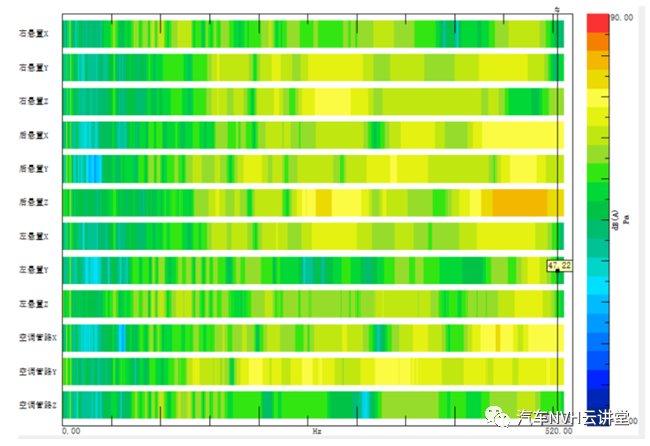
从分析结果可看出,在500-520Hz关键频率段后悬置X、Z向的结构传递路径对目标点的贡献较大,在520Hz的频率下,空调管路X、Y向的结构路径也存在着较大的贡献。激励点对车内噪声的贡献量主要由该路径所受到的激励载荷大小和路径对振动的传递率来决定。从上文分析已知,后悬置X、Z向的激励力略高于其他路径。但是目前在工程上并无对电动汽车的动力总成激励载荷的量化标准,所以无法直接判断在后悬置X、Z向的激励力是否过载。因此,需通过电机总成壳体模态分析对问题进行进一步分析与排查。而在动力总成系统中,若其内部激励频率与壳体固有频率发生共振,则系统对激励点处的激励会明显增高。动力总成各部件的壳体模态分析结果如图8所示。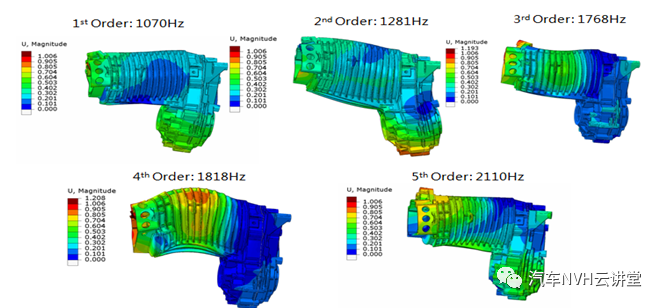
分析结果可看出,壳体总成前三阶模态频率分别为1070Hz、1281Hz、1768Hz,电机总成各部件的模态与问题的激励频率(500-520Hz)无明显的耦合现象,动力总成壳体共振不是啸叫问题产生的主要原因。对试验样车进行NTF传函敲击测试,从NTF图中看出在,后悬置X、Z向的结构传函都高于平均水平,因此,该问题的主要解决方案围绕优化路径的振动结构传函展开。
从路径贡献分析可知,后悬置路径点在一段宽频范围内呈现较高的贡献,没有出现明显的共振频率。为了改善后悬置路径点的传递特性,需要增大后悬置至车身的力衰减,因此,在副车架与车身的接附点处增加衬套,形成一个二级隔振结构。 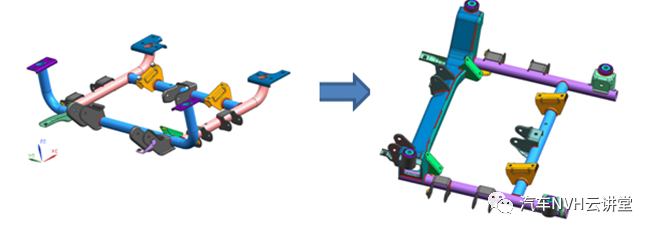
针对二级隔振系统,搭建仿真分析模型,如图11所示,模型按照“电机总成(刚体)-动力总成悬置-副车架(柔体)-副车架悬置-车身(刚体)”的拓扑结构搭建,其中悬置简化为3个相互垂直的线性弹簧黏性阻尼元件,副车架柔体模型保留前12阶模态。
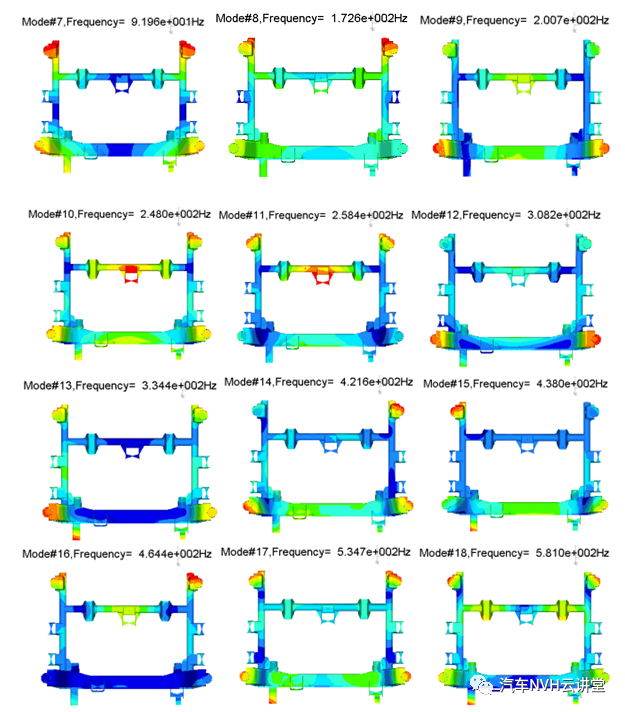
系统单极隔振与二级隔振的隔振性能分析结果如图15所示,相比单极隔振,二级隔振结构的振动传递率在中高频段整体下降,但是500Hz附近的振动传递率下降幅度较小,无法规避啸叫风险。因此,本文在二级减振结构的基础上,对隔振系统的悬置刚度进行优化,搭建优化模型【10】-【12】如公式(10)所示,以在480Hz-520Hz频率范围内达到最佳的系统隔振效果。该优化模型的优化变量为动力总成及副车架悬置刚度,为保证橡胶工艺可行性,优化范围为原方案刚度值的正负30%,为了减小系统模态之间的能量耦合,系统的各阶模态频率间隔大于10Hz,为防止急加速或急减速时电动汽车的低频瞬态扭矩冲击,需对极限工况下的电动汽车的瞬态扭矩冲击时能量频域分布的情况进行分析,分别采集该电动汽车在wot run-up(全负荷加速工况)和tip in/out(急加速/减速工况)下的瞬态扭矩冲击数据如图13所示,对其进行能量频域分布情况分析如图14.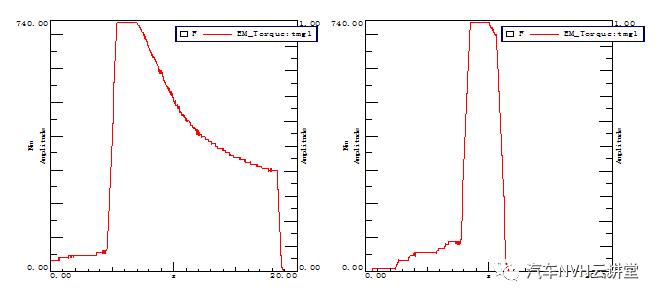
图13 wot run-up(左)、tip in/out(右)瞬态扭矩
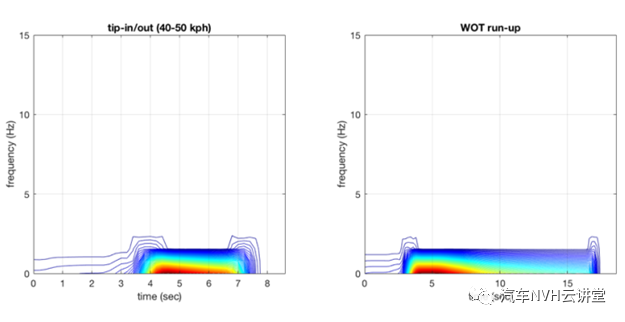
从能量频域分布情况看,系统的冲击能量频率集中在3-10Hz,因此,在优化模型中需将系统的各阶模态约束为大于10Hz。为保障电动汽车的底盘操纵稳定性,副车架的悬置刚度值需大于,优化目标为系统在480Hz-520Hz频段之间的振动传递率最小。系统频响函数的计算方法为模态综合法,优化算法采用NSGAⅡ多目标遗传算法。为车身振动响应,为后悬置处力激励,s为系统的模态阶数,为s阶模态的阵型,、、分别为对应的质量、阻尼、刚度矩阵,为系统各模态之间的最小频率间隔,为系统的最小模态频率,为副车架悬置刚度,为动力总成悬置刚度。为原方案副车架悬置刚度值,为原方案动力总成悬置刚度。
按照优化模型进行优化计算,得到优化结果为动力总成悬置:左悬置刚度降低30%、右悬置刚度降低27%,后悬置刚度降低25%;副车架悬置:前悬置刚度降低20%,后悬置降低23%。系统的振动传递率优化结果如图16所示,优化后的系统振动传递率在500Hz附近下降明显。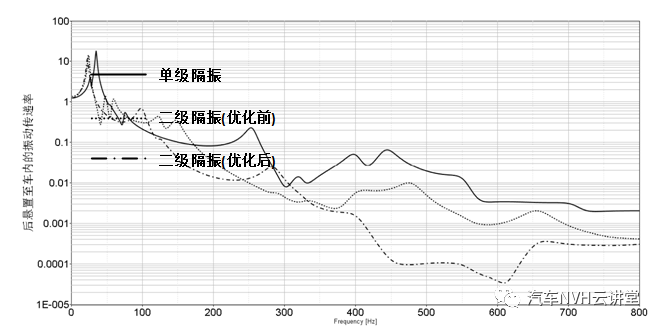
按照优化结果试制样件,在整车上进行测试验证,客观数据记录如图17,发现将新方案装车后在20km/h工况下电动车车内的的啸叫噪声降低,主观声品质提升较大,将噪声数据进行9.95阶、23阶阶次切片,优化结果如图18所示,车内9.95阶、23阶噪声明显降低。因此,新方案对电动汽车的啸叫问题改善非常明显。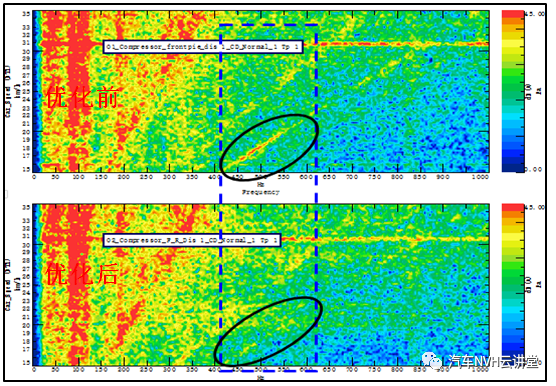
图17 优化后车内加速噪声colourmap对比图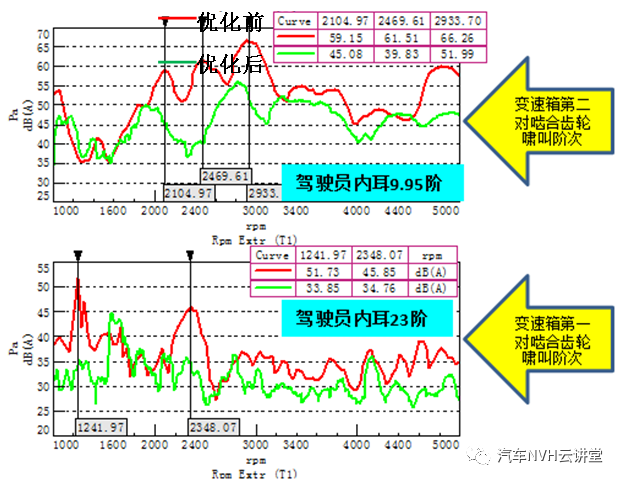
(1)传递路径贡献量分析是解决电动汽车在低速下的中频啸叫噪声一种重要的分析手段。本文运用传递路径贡献量分析对某纯电动汽车的20km/h匀速工况下车内啸叫进行分析,最终找到啸叫噪声的关键传递路径。(2)激励点对车内噪声的贡献量主要由该路径所受到的激励载荷大小和路径对振动的传递率来决定。改善传递路径的中高频振动传递特性是消除车内啸叫的重要手段。(3)优化隔振系统中的悬置刚度值可改善隔振系统的固有频率分布,最终改善系统的隔振系能。本文搭建刚柔耦合仿真模型,以隔振器的刚度为优化变量,以问题路径的振动传递率为优化目标,运用遗传优化算法对电机隔振系统进行优化。按照优化结果进行装车试制,经实车试验验证,车内啸叫问题得到明显改善。【免责声明】本公 众 号所刊载上述内容,资料等来自于网络、社会实践、个人总结、技术论坛等,对文中陈述、观点判断保持中立,不对所包含内容的准确性、可靠性或完整性提供任何明示或暗示的保证。如果您认为我们的授权或者来源标注与事实不符,请告知我们,我们及时修订或删除。谢谢大家的关注。