江铃新能源车身轻量化设计!
1. 车身轻量化设计
车身设计包含了如下所示的七大要素 -安全、耐久、NVH、功能、工艺、成本及重量。其中,安全、NVH、耐久代表了车身性能表现;车身设计质量的评价标准取决于这七大要素之间的平衡程度。用最小的成本、重量和工艺投入换来最优的安全性、NVH表现、耐久性并实现相应的车身功能。 汽车轻量化技术是结构设计、材料、工艺的集成应用,主要途径有: (3)先进的制造工艺(如板材 / 管材液压成形技术)其中轻量化材料及其连接技术是关键问题。 江铃集团新能源车型的车身设计为了实现轻量化,在材料应用上有全铝车身和钢铝混合车身,钢铝混合白车身下车身零件材料主要采用冲压铝和高强度钢的方式实现轻量化,钢、铝连接时,为防止电腐蚀,需在钢与铝连接部位涂隔离层。 同时,为保证钢、铝连接强度,需先涂粘接胶,然后使用铆钉SPR 连接;门槛边梁、侧围板加强板等采用热成型钢;翼子板总成根据造型全新设计,材料为铝合金(材料:6016-T4);前端框架将水箱上横梁总成、水箱下横梁总成、左/ 右前立柱总成集成,一次性注塑成型,结构实现模具、装焊、材料、重量等成本降低;充电口盖总成材料为复合材料;前防撞梁总成采用铝合金材料。 热成型材料重量占比 29%,高强度钢重量占比38%,普通钢占比 26%,铝材料重量占比 5%,其它材料重量占比 2%。 开闭件设计前舱盖总成采用全铝前舱盖,满足 CNCAP 行人保护五星级要求;后行李箱盖外板采用上、下分件形式,内板后组合灯处进行分件处理,外板下板采用复合材料;前后门总成为整体冲压式结构车门,窗框结构形式采用半包式结构设计,内板及加强板进行结构匹配,并需满足侧碰、NVH及扭转折弯刚强度性能要求。 内外饰轻量化四大基本方案为减料厚薄壁化、轻质材料的选用、以塑代钢和模块化设计。 (1)汽车内外饰的薄壁化设计与车身采用高强度钢提高模态达到车身减重目的相类似,汽车内外饰使用材料大多为非金属复合材料,通过提高材料的弯曲模量和拉伸强度就能在保证产品性能基础上降低壁厚,从而减轻零部件的重量。如生产汽车塑料保险杠,所选用的材料如果能够将弯曲模量由1300MP提高到 2000MP,则产品壁厚就能由3mm降到到2.5mm,减重15%以上。 (2)轻质材料的使用能带来非常直接的轻量化效果。在当前的主流设计中,轻质合金、复合材料的使用越来越广泛。内外饰材料中,PP改性材料由于来源广泛、价格低廉,其使用量最大。内饰产品中,低密度的 PP 材料内饰板比传统的内饰板能减重8-15%。 采用 EIPP 化学发泡技术的零件相比传统注塑件减重 20% 左右,并且生产效率更高,外观尺寸更稳定。比如在门护板上的应用,实体注塑 1.5mm,发泡后壁厚2.8mm,不仅实现了较大程度的减重,并且比同重量的实体注塑有更高的强度。 天然纤维填充PP能比传统的矿物填充 PP 减重10%;PHC纸质蜂窝做行李舱隔板比传统的PP木粉板减重30%,并且无异味,无VOC;用PHC制造的发动机盖比传统的金属冲压件能减轻50%的重量。 (3)由于塑料的密度只有钢的1/4—1/7,在满足同等强度和刚度情况下能实现减重 30-50%。其中长玻纤增强聚丙烯材料不仅具有高强度、高刚性、好的冲击强度、抗蠕变性能和高尺寸稳定性,而且资源丰富,成本较低,同时还具有良好的流动性可以做出形状复杂的汽车部件,已得到汽车行业的认可。 内外饰的“以塑代钢”应用中比较有代表性的就是全塑尾门的应用。目前市场上销售的汽车绝大部分的汽车背门都是金属冲压成型的,包含外板、内板、加强板以及内饰板等,零件数量多,结构复杂。 全塑汽车后背门采用 SMC或长玻纤PP复合材料做内板、PP矿粉填充材料做外板,通过粘结方式将内、外板粘结到一起。塑料后背门与金属门相比有更高的集成度和设计自由度,零件数量减少60%,模具费用节省一半,实现减重30-40%。 (4)汽车配件设计的模块化是汽车设计开发的趋势,目前主要有驾驶舱模块、顶棚系统,车门模块、前端模块、地毯与减震垫集成、防火墙模块等。未来十年,模块化设计将会得到快速的发展。如将仪表板、仪表板横梁、空调系统等零件集成到一个模块上,通过机械手安装到车身上,既能实现减重又能提高装配效率。 江铃集团新能源新开发车型在内外饰设计方面也从多方面进行了轻量化解决方案,前后保在满足低速碰撞行人保护等前提条件下薄壁化处理,由一贯保守的壁厚3.5mm减薄为2.6mm;主副仪表台本体及门护板本体选用微发泡材料(PBT+ABS), 可降重10%;后备箱装饰件均选用热压成型软内饰材料;轮罩挡泥板装饰件采用PET/PP无纺棉轻质材料。以上为通过薄壁化、轻质化材料选用和模块化设计路径实现内外饰材料的轻量化。
保险杠薄壁化、仪表台本体微发泡、门护板下本体微发泡 内外饰轻量化目前还存在着几方面的风险问题,材料环保问题、计算分析问题和成本问题,内外饰轻量化设计对设计人员的设计能力、材料的性能和供应商的制造能力都有较高要求,这对于江铃集团新能源乃至国内大多数的主机厂和供应商都是个很大的挑战,但是随着国外一些新材料、新技术、新工艺的引进,必然会对主机厂和供应商的能力提升产生很大的促进作用,使得国内内外饰产业链整体能力得到大幅提升。 江铃集团新车型车身和内外饰轻量化的设计方案,通过CAE分析材料的选用以及结构的优化,碰撞分析和刚强度分析均基本能够满足目标要求。 根据数据模型正碰和侧碰仿真分析,CAE仿真分析优化,正碰中B柱加速度峰值得到明显改善,其峰值脉宽基本能满足要求,纵梁变形模式较为正常,前围入侵降低明显;偏置碰中B柱加速度峰值及前围板入侵量得到少量改善,纵梁前中段压溃变形模式较好,其中前围及关联区域入侵还需进一步优化;B柱及前门入侵量均有明显降低,所有考查项满足目标要求;B柱下段及门槛内板区域强度得到提升,整体侧面入侵变形均有改善。 基 于 白 车 身 三 维 数 据 模 型, 采 用 惯性 释 放, 模 型 无 约 束, 根 据 输 入 状 态,ADAMAS计算输出硬点载荷,工况分析均满足目标要求。 基于仪表台三维数据模型,仪表板与车身连接处全约束,空调与车身连接处约束(X,Y,Z)平动方向,施加1G重力,目标值最大位移小于2mm,分析均满足目标要求。 【免责声明】本文来自网络,版权归原作者所有,仅用于学习等,对文中观点判断均保持中立,若您认为文中来源标注与事实不符,若有涉及版权等请告知,将及时修订删除,谢谢大家的关注!
著作权归作者所有,欢迎分享,未经许可,不得转载
首次发布时间:2023-04-14
最近编辑:1年前
作者推荐
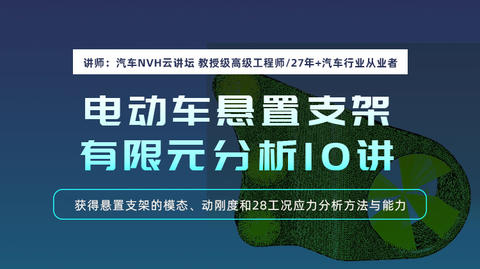