典型液压悬置及结构特点
典型的液压悬置有圆锥形、梯形、长腰型以及衬套型以下几种,每种结构都有其性能特点,下面就逐一进行介绍。1、三向刚度比例可调范围大,X:Y:Z=(0.6-1):(0.6-1):1,动静比在1.3~1.7之间。2、三向限位要求容易实现,X、Z可限位,一般Y向有两个方向限位3、液压元件(流道、底膜(皮碗)、解耦膜(盘)、节流盘(拉头)比较容易实现共用。4、阻尼角峰值频率易于调整,解耦效果比较容易实现;5、如果有节流盘的解耦,可以在较大频率范围(200HZ或250HZ以内)实现小振幅解耦;1、需要较大的Z向空间,如果需要对上跳进行限位,则对Z向空间尺寸要求更高。2、组件数量多,装配工艺复杂,需要注意产品的尺寸链控制避免出现液体泄漏问题。3、需要对密封筋的装配变形尺寸和空间进行仔细核对,还要注意皮碗在水下灌装是的工艺问题。4、注意零件极限变形时底膜(皮碗)与下盖的空间关系,避免在预压时就顶死底座,导致动刚度升高。同时还要注意底盖排气孔的位置和毛刺方向。6、零件承受较大侧向载荷时,需要注意结构件的强度能否满足要求。3、三向静刚度比例易调,X:Y:Z=(0.7-2):(0.6-0.8):16、能够在车身大梁较小的Y向空间条件下实现零件布置1、侧向刚度较小调整范围有限,可能会导致动力总成Y向刚体模态偏低,7、梯形液压悬置一般不会设置节流盘,所以高频动刚度硬化频率较低(130HZ);3、阻尼角峰值频率的调整比较容易,解耦效果比较容易实现4、能够在车身大梁较小的Y向空间条件下实现零件布置2、需要对密封筋的装配变形尺寸和空间进行仔细核对,还要注意皮碗在水下灌装是的工艺问题。3、注意零件极限变形时底膜(皮碗)与下盖的空间关系,避免在预压时就顶死底座,导致动刚度升高。同时还要注意底盖排气孔的位置和毛刺方向。将液压功能整合到衬套设计中拥有十分明显的优势。有两种不同的“液压衬套”设计可供选择。第一种设计理念与传统惯性通道液压悬置相似,采用了两腔设计,其中一个是主液室,而另一个则是十分柔软的分液室(图7),通过孔槽将两个液室相互连接起来,当然由于体积较小,加入解耦盘/膜较为困难。第二种理念主要应用于悬架系统。这一理念中同样应用了两腔设计,两个腔体积刚性接近,并且与内外管接合。随着一根管运动,一个腔就变小,另一个舱相应变大,使得在两个腔体之间产生体积流动。这种设计尤其适用于无须承受静态负载的衬套,主要用于悬架。1、空间占用较小,特别能够在车身大梁较小的Y向空间条件下实现零件布置2、阻尼角的调整周期长,成本高,往往需要修改橡胶模具(除非流道由附件装配的结构)5、密封筋的设计和装配尺寸控制需要十分注意,有较大液体泄漏风险6、如果流道由附件装配,需注意配合面的贴合,要不然容易发生内泄漏而导致液压特性不明显的现象。往期相关推荐
相关文章,在仿真秀官网搜索:
液压悬置还分为解耦式和非解耦式?他们有什么区别呢?
著作权归作者所有,欢迎分享,未经许可,不得转载
首次发布时间:2023-04-14
最近编辑:1年前
作者推荐
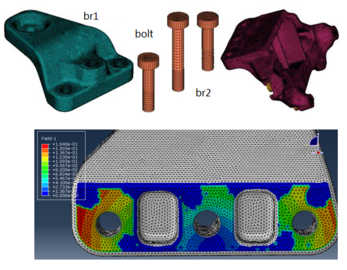