橡胶衬套疲劳失效案例分析与优化
摘 要:针对某车型控制臂衬套整车耐久路试失效问题,通过分析路谱载荷,以提高衬套抵抗大扭矩变形为目标,重新定义与之相应的试验条件,并对衬套刚度和结构进行优化设计,优化后的衬套通过了新试验条件的台架验证,并通过整车耐久路试验证。台架试验和整车耐久路试结果表明,通过分析路谱载荷重新定义的试验条件合理,衬套经优化设计满足整车耐久性能要求。随着汽车零部件制作工艺和精度的不断提升, 路面等级的不断优化,发动机及底盘本身引起的振动噪声问题凸显出来,消费者对于整车的舒适性要求越来越敏感,橡胶衬套,作为底盘的重要减振部件,发挥着极其重要的作用。通常,主机厂针对零部件开发时,会进行零部件台架耐久和整车路试耐久试验验证,台架耐久验证合格后则进行整车路试验证,以便提高整车路试的成功率,降低整车路试的试验成本,然而在实际开发过程中,也会出现台架耐久和整车路试耐久矛盾的情况,即台架耐久满足设计要求,而整车路试耐久却失效。本文中的案例,介绍了橡胶衬套的初始结构和试验条件满足台架耐久的要求,却不能满足整车路试,从而引出重新定义台架试验条件和重新设计衬套结构。某车型控制臂衬套静态、动态刚度以及台架耐久试验均满足要求,台架耐久试验完成后,进行整车路试验证,在整车强化路试过程中5 千公里左右两件均出现开裂失效。首先,通过对悬架系统所有零部件尺寸,装配关系,受力状态进行排查,确定无异常情况,进一步排除装配、材质、制作工艺及尺寸超差等因素;其次,路试样件与台架试验样件属于同一批次,可以推断台架试验条件不能完全模拟整车路试条件;最后,针对衬套橡胶裂纹位置,深度及断裂表面分析,初步认为衬套同时在径向及摆转方向(见图2 b)存在较大受力,橡胶应力过大造成开裂失效,此衬套定义的性能要求和台架试验条件不能满足整车实际工况要求。为了证实此判断,通过路谱采集,悬架系统动力学模型仿真(见图2 a),得到衬套的分路谱受力数据。通过专业的路谱分析软件nCode 对路谱信号进行处理、迭代分析,并根据线性损伤累计理论(Miner)重新得出衬套的疲劳试验条件,与初始试验条件进行对比,如表1 所示。表1 表明,原衬套定义的加载振幅(力值)远小于由路谱分析后重新定义的受力加载振幅(力值),另外加载频率也有所提升。利用新的试验条件重新对初始结构的衬套进行台架疲劳耐久试验,结果显示衬套在V2 方向49 万次左右出现裂纹,不满足耐久性能要求,且橡胶失效位置和模式与整车路试情况相似,详见图3,此衬套结构不能满足整车耐久性能要求,需要进行结构改进,并进一步表明更新后的实验条件与整车路试工况相仿。因此,产生失效的根本原因是初始的实验条件不能充分模拟整车路试工况,初始结构设计因为台架实验条件原因产生虚度设计。兼顾衬套失效模式,以及新的试验条件下,加载振幅大幅度加大,因此,初始衬套静态刚度需要提升,来降低衬套在大载荷作用下产生的位移,同时,为了最大化的隔离振动,产生较高的隔振效果,动态刚度又不能过高,橡胶材料需要较好的动静比和隔振性能,因此,最终决定采取两方面措施来提升其耐久特性。一方面,在结构上增加衬套橡胶本体径向宽度,增加橡胶本体的胶体体积,增加其静态刚度和动态隔振性能,同时,略减小橡胶本体轴向的厚度,两侧的阻尼孔由原来不对称改为对称结构,尺寸相对减小,目的是缓解其径向V2 方向和V1 扭摆方向应力,详见图4。另一方面,为了减低橡胶本体的剪切成分,增加其压缩成分,将衬套的内骨架初始为冷拔直管,改为冷镦成型的中间弧形内管,详见图5。1)在橡胶本体宽度和高度尺寸相同的情况下,直管的实心方向刚度小于球形内管实心方向的刚度,在同样的实心方向载荷作用下,球形内管的位移行程要小于直管,从而在同等载荷作用下,球形内管的应变要小于直管的应变,同理球形内管的应力也会小于直管的应力,目前球形内管的橡胶本体在宽度和高度尺寸上都要略大于直管的橡胶本体,这样径向的刚度会变得更大,更有利于改善应力。通过改变衬套结构,起到降低衬套应力的目的,使得衬套的疲劳寿命更长。2)从阻尼孔尺寸方面分析,直管空心方向为不对称结构,这种结构在受到偏摆15°工况作用下,结构的不对称导致两边空心方向的应力、应变不能对称分布,使得应力、应变不能均匀分散,这样更容易导致衬套橡胶本体在一边空心处应力集中且很大,另一边空心处应力较小。由于这种不对称结构导致的应力集中,使得应力较大,缩短了衬套的疲劳寿命,不容易满足台架、路试的耐久要求。球形内管的空心方向为对称结构,这样在同样偏摆15°的工况下,由于空心结构的对称使得衬套橡胶本体上的应力分布更均匀,应力集中相对直管而言更小,橡胶本体的应力也会更小,衬套的疲劳寿命也会更长。新的结构设计完成后,其静态刚度值较初始结构发生较大变化,详见表2,(注:大257/小361,表示初始结构径向方向阻尼孔不对称产生的刚度不一样)。同时,为了验证新结构与初始结构在同样边界条件下应力应变的变化趋势,通过有限元软件Abaqus 进行仿真,结果显示,应力和应变均明显降低,详见表3。为了进一步验证,新结构衬套设计的合理性,以及新的试验条件与整车路试工况的匹配程度,将结构优化后的衬套,重新安装在实验室MTS 多通道试验台架上,进行耐久疲劳试验,试验条件:V2 方向(实心方向):±4200N,6Hz ;V1(空心扭摆方向):±15°,1.3Hz,风冷,两方向同时进行,详见图6。试验结果显示,V2方向交变次数60万次,V1方向交变13 万次,两个方向的力值和位移无明显变化,试验后均无开裂现象,详见图7,因此,可以认为新结构衬套较初始结构衬套疲劳耐久性能有大幅提升。台架试验完成后,为了进一步验证新台架实验条件与整车路试工况一致性,将新结构的样件装车重新进行整车路试试验,试验完后衬套均无裂纹,路试通过,同时,新结构衬套在30km/h 速度过坎工况,振动衰减时间缩短,整车NVH平顺性评价通过。充分证明,初始结构试验条件定义不合理,通过路谱分析重新定义的试验条件与整车路试工况吻合度高,同时,新的结构设计,增加其刚度性能,减少应力集中,对改善衬套耐久性能起到了重要作用。文中针对某车型控制臂衬套整车路试耐久失效问题,确认初始结构设计及台架实验条件不满足实际整车道路试验条件,通过路谱及悬架结构Adams 模型进行受力分析,分离出衬套的原始路谱,通过Ncode路谱分析软件,对衬套的耐久和试验条件重新定义,同时根据初始结构的衬套裂纹失效模式、发生位置和表面开裂特征,判断为应力集中引起的耐久裂纹失效。据此对衬套结构进行优化,适当增加其刚度,减少大载荷下的位移,缓解应力集中现象。更改后的结构通过重新定义试验条件的台架耐久试验和整车道路试验,问题得以解决。通过文中的叙述,可以总结出以下经验,针对衬套耐久问题,尤其是台架试验与整车路试结果相互矛盾时的解决提供依据。(1)不同车型(重量或悬架结构)的衬套设计时,需通过路谱分析和动力学模型得到衬套的受力谱;(3)通过结构设计满足衬套静、动态性能的同时,尽量减少衬套应力、应变,提高其耐久性能。作者单位:(广州汽车集团股份有限公司汽车工程研究院,广东 广州 510640)免责申明:本公 众 号所载文章为本公 众 号原创或根据网络搜索编辑整理,文章版权归原作者所有。因转载众多,无法找到真正来源,如标错来源,或对于文中所使用的图片,资料,下载链接中所包含的软件,资料等,如有侵权,请跟我们联系协商或删除,谢谢! 著作权归作者所有,欢迎分享,未经许可,不得转载
首次发布时间:2023-04-15
最近编辑:2年前
作者推荐
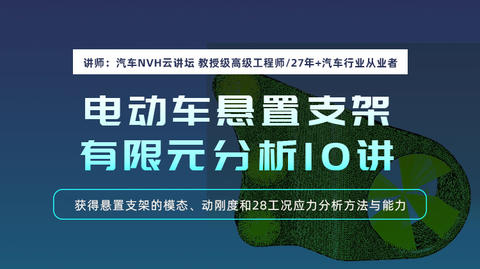