电动汽车全油门加速整车抖动问题试验研究
摘要:文章以电动汽车全油门加速工况下整车抖动问题为研究对象,通过分析识别主要激励为半轴的轴向派生力引发0.39阶。针对三球销式万向节进行运动学受力分析及理论推导,得出半轴当量夹角与轴向派生力相关。最后基于工程实际,将半轴当量夹角从7°降低至4.1°,优化后整车全油门加速工况下整车振动加速度峰值下降60.68%~70.08%,整车舒适性极大改善。电动汽车由于效率高、污染小、噪声低,具有节能、环保等优势,受到了国内主机厂的特别关注。但由于电动机特有的低转速大扭矩的特性,也导致电动汽车出现了众多新的NVH 问题,比如电机啸叫、减速器打齿等。文献[1]通过在不同车速下的急加速松踏板的声振试验及分析发现,主副车架之间的连接悬置在抖动频段内的隔振性能较差,轮胎与主车架之间的偏相干系数接近1,说明轮胎是产生抖动的主要源头;文献[2]建立车辆多体仿真模型,分析方向盘摆振的影响因素及优化措施,通过DOE 正交试验优化系统参数,优化后有效抑制了方向盘振幅;文献[3]利用基于模态的强迫响应的理论建立了动力吸振器的二自由度力学模型,根据最优同调原理设计出适合系统的动力吸振器参数,利用其吸振功能,成功将方向盘振动加速度振幅降低,振动情况得到改善。文章针对电动汽车在全油门加速时整车抖动开展研究,重点关注传动系统,对三球销式万向节驱动轴总成进行受力分析及理论推导,得出轴向派生力与半轴当量夹角关系,然后对当量夹角进行优化,最后对优化结果进行整车主观、客观的评价。驱动轴是指一种装在变速器与车轮之间,由2 个或多个等速万向节、中间轴杆及其他零件组成的传递扭矩和旋转运动的机械部件,是传动系统中至关重要的一环。在整车运动过程中,车轮受到来自路面的激励会不断跳动,造成减速器和轮胎之间的距离和角度不断变化,万向节的使用满足了这项实际工况的要求。三球销式万向节主要由三柱槽壳、销轴、三销架、球环、滚针及密封装置组成,如图1 所示;三球销式万向节属于轴向滑移型万向节,具有同步性好、角位移大、回转灵活、安装、拆卸方便并能承受重载及冲击载荷等突出优点,所以广泛地应用在轿车行业。当轴向滑移型万向节形成活动角传递动力时,球环随三柱槽壳转动,在滑槽轨道内滑进和滑出,产生滑动摩擦和滚动摩擦,球环与滑槽之间的摩擦力是球环产生轴向窜动力的主要原因。对滑环与滑槽接触点进行受力分析,以滑环1 为例,受力分析如图2 所示。球环2、球环3 受力分析同上,滑动摩擦力沿着销轴轴线方向垂直于驱动轴,使球环沿着销轴做轴向滑动;滚动摩擦垂直于销轴,合力滑移摩擦力沿着滑槽的轴线方向,总的力为3 个球环的滑移摩擦力总和。设球环1、球环2、球环3 产生的轴向力分别为F1、F2、F3;3 个球环共同产生的轴向力可以表示为:F=F1+F2+F3。在三球销式万向节转动的过程中,球环沿着滑槽滑进和滑出受力会变化2 次,同时旋转过程中轴向力随转角变化而变化。同时随着角度的增大,轴向力增大。当当量夹角固定时,总的轴向力F 随转角的变化规律,在1 个周期2π 内,F 周期性变化3 次,而且,槽壳每转1/3π,轴向力的方向就发生一次变化[4]。设电机转速为N,整车的速比为7.7,则减速器输出转速N 减=N/7.7,半轴输出阶次O 阶=3N 减/N。通过计算可得出,三球销式万向节在传动比为7.7 时,产生0.39 阶振动。择市区环城路,试验工况模拟问题工况,转速从0开始全油门加速至5 500 r/min,整车信息如表1 所示。使用LMS Test Lab 软件记录动总悬置主被动端、方向盘位置X、Y、Z 三向加速度信号,电机转速从整车CAN信号中提取,然后对采集的信号进行频率分析。测点位置如表2 所示。全油门工况下,测量方向盘、导轨及悬置主被动端、左右轴头振动加速度和电机转速信号,计算得到X、Y、Z 方向colormap 图。以Y 方向为例进行说明,如图3 所示。由图3 可知,方向盘振动问题主要表现为0.39 阶,对应方向盘抖动频率主要集中在16~25 Hz 和28 Hz及30~34 Hz。对信号进行阶次切片分析,得到方向盘X、Y、Z 三个方向振动情况如图4 所示。电机转速2 300~3 000 r/min、4 300 r/min、4 600~5 200 r/min,分别对应频率16~25 Hz、28 Hz 及30~34 Hz,方向盘抖动较大。对方向盘振动信号进行阶次切片处理,得到X、Y、Z 三个方向加速过程的阶次曲线,如图4 所示。由以上的分析可以看出,方向盘抖动呈现明显的阶次特性,结合受力分析可知,方向盘振动与万向节球销有关。NVH 问题解决思路主要有:源头、传递路径、响应。改问题可以从:“半轴- 轴头- 悬架系统- 车身- 方向盘”及“半轴- 动总- 悬置系统- 车身- 方向盘”。针对每条路径进行分析如下。对左右悬架系统主被动端振动加速度信号进行分析,提取问题阶次0.39 阶振动进行对比,由于篇幅的原因,选择前悬架左侧减振器进行研究,具体如图5 所示。可以看出,主动侧0.39 阶振动在对应的转速段内,无明显峰值,且在整个转速范围内低于量值小于被动侧,说明悬架系统不是振动的主要传递路径。对左、右、后悬置主被动端振动加速度信号进行分析,提取问题阶次0.39 阶振动曲线,由于篇幅的限制,选择后悬置作为分析对象进行研究,具体如图6、图7所示。从图6、图7 可知,2 300~3 000 r/min 下,动总左、右、后悬置主动侧及被动侧振动均有峰值,尤其被动侧Y 向峰值达到1.25 m/s2,说明Y 向振动是主要振动且由动力总成左右摆动传递到车身所致。在4 300 r/min、4 600~5 200 r/min 转速范围同样存在峰值,但均小于0.5 m/s2。主动侧Y 向振动峰值达到10.83 m/s2,振动量级大。针对主动侧振动大问题,完成整车状态下动总刚体模态测试,测试结果如表3 所示。在常用转速区间,电机转速为1 000~5 600 r/min,0.39 阶对应的频率范围主要为6.5~36.4 Hz;因此主要关注低频振动;动力总成刚体模态一般分布在该区间内,从测试结果来看:存在15.49 Hz、16.41 Hz、23.75 Hz和32.05 Hz 与抖动频率相近,导致动总的抖动增加,传递的能力变强。传递至车身的振动越大,激励其附件系统产生NVH 问题的概率就越大。在盘抖动与传递至车身的振动频率关系很大,因此整车状态下,进行方向盘模态测试,测试结果如图8、图9 所示,可以看出,方向盘存在25.40 Hz、31.15 Hz 模态频率,与动总传递至车身的振动频率23.75 Hz 和32.05 Hz 产生耦合隔振,导致在全油门加速工况下,方向盘出现严重抖动问题。通过以上分析得出:1) 整车全油门加速工况时,方向盘异常抖动,对应电机转速2 300~3 000 r/min、4 300 r/min、4 600~5 200 r/min,频率为16~25Hz、28Hz及30~34 Hz;2) 产生抖动激励源为半轴产生的0.39 阶次振动;3)振动传递主要路径为半轴、动总、车身、方向盘,与悬架系统无关。传递过程中动总刚体模态加剧了振动,导致传递至车身振动增加,2 300~3 000 r/min 振动明显;4)方向盘模态与刚体模态产生耦合共振,导致在4 300 r/min、4 600~5 200 r/min 转速范围方向盘共振。由于电动汽车悬置设计需要重点考核大扭矩及限位作用,刚度不能过小,否则会产生严重问题,因此降低悬置刚度参数不现实。从响应角度避频,提高方向盘模态频率空间有限,不能完全避开转速激励频率,优化成本较高。再结合工程开发要求,主要考虑低成本、高效率快速解决问题为主,因此建议从半轴安装角度进行优化。将驱动半轴夹角由7°减小到4.1°,然后进行试验验证,试验结果如图10 所示。可以看出,调整半轴角度后,车辆全油门加速工况下,整车振动及方向盘振动均明显下降,X 方向从3.51 m/s2 降至1.38 m/s2,降低60.68%;Y 方向从3.71 m/s2 降至1.11 m/s2,降低70.08%;Z 方向降低至1.51 m/s2,降低69.37%;电机转速在2 300~3 000 r/min 时,方向盘抖动改善很大,在可接受范围内有轻微的抖动;4 300 r/min 时,几乎感觉不到方向盘抖动;4 600~5 200 r/min 时,几乎感觉不到方向盘抖动。针对某款电动汽车全油门加速工况下,方向盘抖动问题进行试验研究,得出0.39 阶振动激励来源于驱动半轴。分析传递路径对振动的影响,电机转速在2 300~3 000 r/min 范围,激励与刚体模态耦合,振动传递到车身。电机转速在300 r/min、4 300~5 200 r/min 范围,激励频率与方向盘模态耦合导致方向盘模态共振。对半轴进行受力分析和试验验证,结果表明:不同平衡量半轴方案的整车搭载验证,确认半轴动平衡量对整车振动问题影响不大;半轴布置角度是导致半轴激励过大的直接原因。优化后整车加速工况下,方向盘振动加速度峰值下降60.68%~70.08%,人员主观评价得到了极大的改善。提供了一种基于半轴当量夹角调整快速解决工程问题的方案,为电动汽车方向盘异常抖动问题的解决提供参考。作者单位:(合众新能源汽车有限公司汽车工程研究院)免责申明:本公 众 号所载文章为本公 众 号原创或根据网络搜索编辑整理,文章版权归原作者所有。因转载众多,无法找到真正来源,如标错来源,或对于文中所使用的图片,资料,下载链接中所包含的软件,资料等,如有侵权,请跟我们联系协商或删除,谢谢! 著作权归作者所有,欢迎分享,未经许可,不得转载
首次发布时间:2023-04-15
最近编辑:1年前
作者推荐
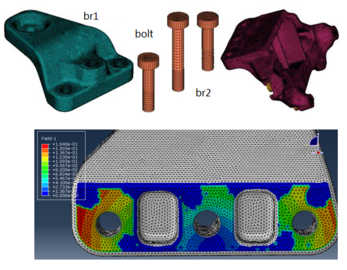