某后置发动机客车车内轰鸣声原因及改进
摘 要:分析某后置发动机客车车内轰鸣声产生的原因,并通过改变传动系统的转动惯量,较好地解决此问题。关键词:客车; 后置发动机; 传动系统; 车内轰鸣声; 转动惯量随着客车发动机功率的不断提高和车辆结构的轻量化设计,动力传动系统的扭振问题越来越突出,成为客车振动和噪声的主要根源之一。发动机转矩向车轮传递过程中,会激发动力传动系统的扭转模态。当发动机的旋转激励频率与传动系统扭转模态的频率一致或接近时,便会使传动系统产生强烈而规律的扭转共振,激励被大幅放大,传递到车身,引起车内轰鸣声。在国内商用车领域,对这一问题的研究尚处于起步阶段,且多采用通过对测试数据的阶次分析、模态分析、传递路径分析等方法,确定噪声的振动来源及峰值产生原因[1-5] 。本文也采用这一方法对某后置发动机旅游客车开发中遇到的车内轰鸣声问题进行研究,为类似问题的解决提供参考。某9 m 后置发动机旅游客车,配置直列6 缸柴油发动机, 6 挡手动变速器。在4 挡全油门加速过程中,发动机转速1 400 ~ 1 500 r/ min 之间,车内出现较明显的车身抖动和轰鸣现象,主观评价车内后排噪声较大,并有明显压耳感。采用LMS Test. Lab 多通道测试系统对车内噪声进行客观数据采集。为便于分析,截取4 挡全油门加速行驶过程车内后排噪声声压级曲线,如图1 所示。由图可知,发动机转速达到1 452 r/ min 时,车内后排噪声出现峰值,达到81. 22dB(A),客观数据与主观评价相符。通过FFT 转换,得到其噪声频谱图[6-7] ,如图2 所示,发动机转速1 450 r/ min 左右时,车内轰鸣声能量贡献主要来自3阶激励频率72 Hz。车内轰鸣声多为结构噪声,其控制方法大多是从噪声的激励源和传递路径上进行处理[8-9] 。根据经验,动力传动系统扭振对后置发动机车辆车内振动噪声存在较大影响[10] ,初步对传动系统扭振进行测试。测试全油门加速过程中变速器一轴在各挡位下的扭转振动数据,其中扭振幅值最大的4 挡一轴扭振频谱和扭转角速度曲线如图3 和图4 所示。由图3 可以看出,4 挡的传动系统扭转模态频率为72Hz,与发动机的三阶模态频率相同。分析图4,在发动机转速1 450 r/ min 附近出现角速度波动峰值,最大扭振角速度达到6. 1 rad/ s。而且图4 变化趋势与图1 变化趋势较一致,均在发动机转速1 450 r/ min附近达到最大值,有明显的强相关,因此,判断全油门加速过程中在发动机转速1 450 r/ min 附近,车内出现的低频轰鸣声主要激励源是:发动机三阶激励频率72 Hz 与4 挡状态下的动力传动系统扭转模态产生耦合共振所致。根据上述分析,车内轰鸣声主要为低频结构振动所致,所以不分析空气传递路径。针对本文问题,主要结构传递路径有:① 动力总成—悬置—车架—车身—车内声腔;② 动力总成—传动轴—驱动桥—悬架—车架—车内声腔。分别对车架、驱动桥壳等主要结构传递路径的关键点振动进行响应测试分析。根据测试结果,驱动桥壳以Y 向振动最大,在发动机转速达到1 450 r/ min左右时,在72 Hz 附近出现峰值,达到2. 45 m/ s2,其频谱如图5 所示。车架以X 向振动最大,在发动机转速达到1 450 r/ min 左右时,在72 Hz 附近出现峰值,达到0. 9 m/ s2,其频谱如图6 所示。对比图2、图5、图6 可以看出,驱动桥壳和车架振动频谱与车内噪声谱的趋势一致,因此,可判断动力传动系统较大的交变扭矩通过后桥主减啮合力反作用在主减输入轴轴承上,引起驱动桥壳Y 向振动加剧,再经过悬架传递到车架,而后引起车内轰鸣声。即上述②为引起全油门加速过程中车内轰鸣声的主要传递路径。通过试验模态分析,可获得车内声腔模态。前四阶声腔模态表现为前后伸缩特征,频率分别为17. 93Hz、37. 76 Hz、57. 23 Hz、67. 40 Hz;第五阶声腔模态表现为前后伸缩、纵向和横向交错的特征,频率为74. 20 Hz,与发动机的激励频率耦合。综上得知,来自发动机3 阶的激励频率72 Hz,与动力传动系统扭转模态耦合共振,通过动力总成—传动轴—驱动桥—悬架—车架路径传递至车内,再与74. 20 Hz 声腔模态产生耦合引起车内轰鸣声。将整车看作一个振动系统,驱动桥主减输入轴扭转交变扭矩为其激振力,减小该交变扭矩,可改善车内轰鸣声。再从传递路径分析,可采取以下改善措施:①调整离合器刚度和阻尼,衰减发动机向变速器输入轴扭振的传播;②调整传动系统的转动惯量、扭转刚度等,以改变系统的固有频率,使共振转速避开工作转速或常用工作转速范围[4] 。由于减小发动机激励和调整离合器减振刚度需要对零部件结构进行调整,周期太长,不确定因素多,对已定型的车辆来说极难实现。所以,本次采用上述较为简单的措施②避开耦合共振频率[11-12] 。其优点是周期短、成本低。考虑空间结构,最终确定方案:在变速器输出端或驱动桥输入端增加一个惯量法兰。首先临时在变速器输出法兰外径套装不同质量的圆盘,结合整车试验及主观评价,最终加装质量为1. 85 kg 的圆盘(对应转动惯量为0. 25 kg·m2 ),主观评价车内后排噪声在各挡全油门加速时最低。由于套装圆盘可靠性差,时间长有脱落和断裂风险,所以最后利用UG 软件设计一款质量为1. 85 kg、转动惯量为0. 25 kg·m2 的法兰,安装在变速器输出法兰与传动轴输入法兰之间,随传动轴一起转动。装好惯量法兰后,再测试全油门加速过程中变速器各挡传动系统的扭振和车内噪声情况:1、2、3、5、6挡一轴扭振均无明显峰值;4 挡变速器一轴扭振峰值出现在50 Hz,避开了耦合共振频率;72 Hz 处扭振角速度降至0. 24 rad/ s;车内低频轰鸣声现象主观感受基本消失。在发动机1 450 r/ min 处车内后排噪声为74. 09 dB(A),相对原状态降低了7. 18 dB(A),改善效果显著。本文基于“激励源—传递路径—响应” 的思路,分析车内轰鸣声产生原因,最终通过增大传动系统转动惯量的方法,将4 挡状态下的动力传动系统扭转模态降低22 Hz,有效避开耦合共振频率,车内后排噪声显著降低,主观评价良好。作者单位:(厦门金龙联合汽车工业有限公司, 福建厦门 361023)往期相关推荐
相关文章,在仿真秀官网搜索:
【干货】四驱车型动力总成常见NVH问题识别与控制!
免责申明:本公 众 号所载文章为本公 众 号原创或根据网络搜索编辑整理,文章版权归原作者所有。因转载众多,无法找到真正来源,如标错来源,或对于文中所使用的图片,资料,下载链接中所包含的软件,资料等,如有侵权,请跟我们联系协商或删除,谢谢!
著作权归作者所有,欢迎分享,未经许可,不得转载
首次发布时间:2023-04-15
最近编辑:2年前
作者推荐
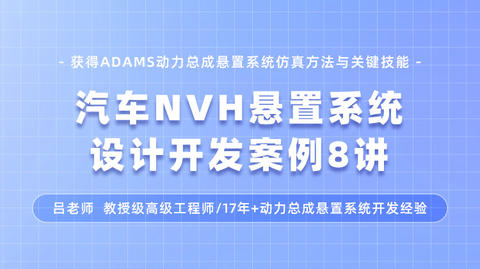