乘用车电驱系统NVH 综合性能研究
摘要:以某乘用车电驱系统(电机、电控、减速箱)为研究对象,对电驱系统NVH(噪声、振动与声振粗糙度)综合性能进行优化。首先通过分析电机单体、减速器单体主要激励源,确定引起电驱系统声品质恶化的主要激励源;然后通过仿真和试验对备选方案进行对比分析,得到较为理想的声品质优化方案,并对整车进行NVH 试验验证;最后总结电驱系统NVH 优化方法和流程。
关键词:汽车;乘用车;电驱系统;NVH(噪声、振动与声振粗糙度)随着人类进入电气智能时代及电动汽车的普及,主机厂对电驱总成性能的要求越来越高。电动汽车的NVH(噪声、振动与声振粗糙度)性能作为重要驾驶性能之一,受到零部件供应商及主机厂的重点关注。与传统燃油车及其他新能源车相比,纯电动汽车动力总成结构更简单、紧凑,输出扭矩及在整车上表现的加速性能更优秀。驱动电机普遍采用永磁同步电机,变速箱则简化为减速器及差速器的集成,结构大为简化,但同时带来NVH 性能挑战。驱动电机朝着宽调速区间、高转速及轻量化方向发展,尤其是电机带来的高频电磁噪声机理较复杂,声品质较差,噪声污染性较严重。同时,电机控制器IGBT 器件引入的开关频率使进入电机的电流发生“锯齿状”畸变,从而引入带有开关频率的电磁噪声。减速器的一级齿轮与电机一般采用花键等硬链接方式,相对于传统变速箱其结构更简化、紧凑,但失去了能降低扭矩波动、转速波动的中间连接部件(如离合器) ,导致电机输出的扭矩、转速波动被直接传递至车轮,造成车身纵向抖动严重。综上,驱动电机、减速箱、电机控制器集成之后的结构构型及振动噪声特点的不同导致纯电动汽车开发中对动力总成NVH 性能提出了新的、更高的要求。目前市面上大多采用永磁同步电机作为车用驱动电机(也有少数采用异步电机) ,其特点是损耗小、功率高、效率高、调速区间宽及定位准确。其振动噪声的主要影响因素包括PWM 频率、极槽比配合、定转子特征模态、壳体固有特性等。电机振动噪声主要是电机的电磁力,可分为电机径向力和切向力。电机径向力是电机径向振动的主要激励源,电机切向力主要输出电机扭矩。尽管电机本体振动幅值较小,但由于其频率较高,主观感受为“滋滋”的高频电磁噪声,长期处于该环境中,容易使人产生烦躁、头痛等生理反应,严重影响驾驶安全及乘车舒适性。其中电机控制器IGBT 器件引起的伞状阶次噪声f可用式(1)表示:式中:f 0 为IGBT 开关频率;p 为电机磁极对数;Srpm 为电机转速。通常通过调整控制策略及整车声学包处理解决PWM 开关频率噪声,方法如下:1 ) 将开关频率PWM 提高到10 kHz 或以上,尽量避开人耳听觉的敏感区域;2) 将离散开关频率转为随机开关频率,使开关频率部分的能量能分散,避免能量集中;3 )将PWM“畸变”的电流信号通过整流电路进行滤波处理,使“畸变”的电流信号尽量光滑,减少谐波;4)在传递路径方面,通过在整车方面提供匹配的声学材料,提升整车NVH 性能。作用在定子齿面的径向电磁力,根据麦克斯韦应力张量法,气隙磁场中单位面积电磁力瞬时值p n θ ,t 可用式(2)表示:式中:b(θ ,t)为电机气隙磁密;μ0 为真空磁导率。从式(2)来看,电机电磁力具有时空特性,分析电磁力的关键在于对其时空二维进行谐波分析。可采用FFT 二维变换处理。通常电机负载情况下,电机谐波主要包含以下部分:1) 转子磁场自身作用产生的电磁力;2) 电枢反应磁场自身作用产生的电磁力;3) 转子磁场与电枢反应磁场谐波相互作用产生的电磁力。其中主要电磁力谐波由转子谐波及定子谐波耦合而成。谐波耦合是线性计算过程,可用式(3)表示:式中:u 为转子谐波,u = (2γ + 1 ) p (γ = 0 ,1 ,2 ,… ) ;v 为定子谐波,对于整数槽绕组,v = (6k + 1)p(k = 0 ,± 1 ,± 2 ,… ) ;对于分数槽绕组,v = (6k /d +1)p (k = 0 ,± 1 ,± 2 ,… ) 。通常认为电机定子铁心的变形量与力波次数的4 次方成反比,与力波幅值成正比。以8 极48 槽电机为例,因整数槽的永磁同步电机力波次数只能是零或2 p ,且当极对数大于2 时,大于4 次的力波在振动噪声计算中可忽略不计,故该驱动电机的力波次数只能为零。图1 为某车型驱动电机电磁方案。由于驱动电机的特点鲜明,调速范围广,响应快,纯电动汽车减速箱通常作为电驱系统中减速增矩的装置来替代传统燃油车的变速箱。一般减速箱第一级齿轮采用花键轴与电机轴硬连接,其结构更紧凑,成本更低。但缺少变速箱、离合器等衰减电机输出扭矩、转速波动的装置,造成扭矩和转速直接传递至车轮,使整车纵向抖动更明显,扭矩变化速率大,同时产生严重的齿轮啸叫问题。减速器NVH 问题通常由齿轮的宏观参数设计、齿轮变形、壳体刚度、制造误差、装配误差、齿轮自身的微观修行等因素导致。实际工作中,齿轮的传递角度与理想角度总是存在一定偏差,这就是齿轮的传递误差。通常齿轮的传递误差水平控制直接决定齿轮啸叫问题的严重程度。而轮齿对齿面的载荷偏载也会导致较严重的振动噪声。为控制减速箱振动噪声,斑点测试和传递误差测试必不可少。减速箱振动噪声问题的解决方案有:1) 宏观参数选择,合理避开电机主要阶次;2) 微观参数选择,通过合理控制微观参数,减轻齿轮的啸叫问题;3 )提高轮齿的加工精度,将装配精度控制在合理范畴。这需要积累大量工艺装配经验,并不断进行测试验证,从而将减速器NVH 水平提高到更高的水平。表1 为某款车型减速箱齿轮对(见图2)传递误差。二级啮合齿轮对,优化方案传递误差TE 仿真数据比原方案有明显改善。图3 为某车型三合一总成。众所周知,电驱系统的激励源是电机电磁力激励及齿轮轮齿对产生的啮合力。正向开发流程中,电机、减速箱同步进行NVH 开发,待单体优化完成后加上控制器壳体进行总成开发,更进一步则加上控制算法进行总成振动噪声开发。驱动电机NVH 优化一般按照开发流程进行。得到初版电磁方案后,对其气隙磁密、电磁力波进行分解分析,观测反电动势波形的正弦性;然后采用磁固耦合分析方法将气隙电磁力施加到定子齿面,计算定子外表面的谐响应进行评估,同时对转子通过磁固耦合方法计算扭振响应进行评估。将上述计算结果与经验值进行比较,如果计算值存在异常,则采取定子开辅助槽、转子开辅助槽、转子增加隔磁孔、分段斜极等措施进行处理。图4 为某车型驱动电机针对48 阶噪声的优化方案,优化前后气隙磁密谐波含量对比见图5 ,电机定子外表面响应对比见图6 。从图5 可看出:优化后,引起48 阶噪声的11 和13 阶次磁密含量明显减少。从图6 可看出:48 阶噪声[对应图6(a)中1 600和图6(b)中3 600 Hz 等效声功率)降低4 ~ 5 dB 。说明在电机转子的适当位置增加隔磁孔能有效抑制电机48 阶对应的谐波含量。根据式(4)进一步计算两种方案下电机扭矩脉动值δ ,计算结果见图7 。从图7 可看出:两种方案的扭矩波动值相差在允许范围内。原方案扭矩脉动值为4 .97% ,优化方案扭矩脉动值为1 .95% ,优化方案的表现更优,说明优化方案可行。对两种方案通过整车进行NVH 测试验证,优化前后整车WOT 工况下近场电机48 阶噪声测试结果见图8 。从图8 可看出:优化后,电机48 阶噪声在低速工况下平均降低5 dB(A)左右,与仿真结果基本吻合,进一步验证了优化方案的可行性。某车型减速器主要存在减速器特征阶次啸叫问题,对应阶次为26 和9 .02 阶。为此,针对减速器1 、2 级阶次啸叫问题进行两轮轮齿优化。第一轮优化主要在保持轮齿宏观参数不变的情况下对微观参数进行优化。经过轮齿参数检测,发现齿形斜率误差及齿向斜率误差较大,经过微观磨齿优化,减小齿形和齿向斜率误差,将其控制在合适精度范围内。磨齿前,齿轮的径向跳动误差及鼓形量误差都较大,磨齿优化后尽量降低径向跳动误差及齿轮的鼓形量误差。图9 为第一轮轮齿优化后WOT 工况测试结果。从图9 可以看出:减速器26 阶噪声司机室内控制在31 dB(A)左右,满足客户要求。因此,可将第一对轮齿参数、工艺装配参数进行固化,便于后续NVH 问题控制。9 .02 阶噪声在2 000 ~ 3 100r/min 速度区间存在局部峰值,对应频率为300 ~470 Hz ,为左悬置共振引起的局部噪声加强。第二轮优化设计A 、B 两套修行方案(见表2 )并安排4 台样车进行对比分析,分析结果见图10 。从图10 可看出:第二轮齿轮修行方案(A 、B)下,转速为2 500 ~ 3 000 r/min 时,9 阶噪声偏大,对比原状态和第一轮优化结果,存在一定恶化。26阶噪声,A 、B 方案均可接受。9 .02 阶噪声工况区间为2 100 ~ 3 500 r/min ,对应频率为300 ~ 470 Hz 。针对9 阶噪声恶化问题进行排查。初步判断该问题为低速低频问题,采用排除方法进行分析。动力总成出现低频问题可能是由于电机旋变盖板及电控的上盖板刚度不足。但进一步分析二者振动数据,该频率区间没有出现明显振动带。因此,可以排除这两个零部件,基本排除动力总成的问题。进一步将振动传感器布置区域扩大至悬置。根据图10 ,该问题主要是由于300 ~ 470 Hz 区间共振带导致9 .02阶次噪声加强而引起的局部噪声加强效应,根据推断及后续测试数据判断与左悬置被动端支架模态偏低有关。9 .02 噪声与左悬置问题区域基本一致,判断9 .02 阶噪声恶化现象是由于左悬置刚度较低引起,可将左悬置刚度提高,消除共振引起的噪声加强现象。该文阐述了电机激励原理及振动规律,分析了PWM 载波对动力总成噪声的影响,并提出对应措施;阐述了减速器激励原理及振动特性,分析了纯电动汽车减速器与传统燃油车的区别,提出了控制减速器所引起噪声的措施;最后以某车型纯电动动力总成为例,对驱动电机及减速器进行NVH 优化,使其动力总成符合客户要求。作者:陈建明,冯勤龙,沈丁建,朱咸强,毛鸿锋,黄明明作者单位:(中车株洲电力机车研究所有限公司,湖南株洲 412005)往期相关推荐
相关文章,在仿真秀官网搜索:
本公 众 号新能源汽车相关文章汇总(截止到2020年12月10日) 免责申明:本公 众 号所载文章为本公 众 号原创或根据网络搜索编辑整理,文章版权归原作者所有。因转载众多,无法找到真正来源,如标错来源,或对于文中所使用的图片,资料,下载链接中所包含的软件,资料等,如有侵权,请跟我们联系协商或删除,谢谢!
著作权归作者所有,欢迎分享,未经许可,不得转载
首次发布时间:2023-04-18
最近编辑:2年前
作者推荐
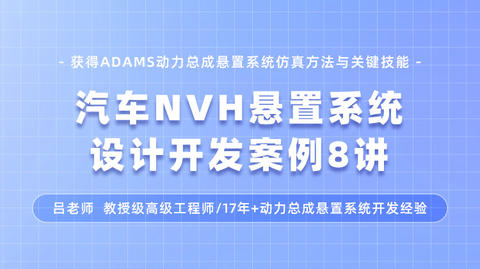