电驱动桥用减速器NVH 优化研究
摘要: 电驱动桥系统噪声过大或异响问题将降低整车的乘坐舒适性, 同时直接影响乘客的主观体验及评价。针对某款由电机、减速器和车桥组成的电驱动桥出现的噪声大及异响问题, 通过试验测试排查出噪声和振动来源, 并采取相应的整改措施进行优化,消除了异响, 降低了噪声值, 取得了显著效果。关键词: 电驱动; 振动噪声; 异响; NVH 优化某款电机、车桥与减速器集成为电驱动桥系统, 并配置在公交车辆上。在装车试验验证阶段, 发现电驱动桥系统存在噪声大和异响的问题: 车辆正常行驶过程中在车内可听到从电驱动桥系统处传出的较大的噪声并伴有沉闷的、有节奏的“轰轰” 声; 在加速踏板和制动踏板动作时有明显的短暂的“咚咚” 的异响, 制动踏板动作时异响尤为突出。为此, 本文作者针对此问题采取了相应的整改措施进行优化, 消除了异响, 降低了噪声值, 取得了显著效果。针对上述问题, 借助具有振动和噪声信号采集及处理功能的专业工具———LMS Test Lab 振动噪声测试系统,在车内电驱动桥上方———后排座位处布置了麦克风采集噪声, 在电机和减速器上分别布置了振动传感器采集振动数据, 对车辆运行过程中电驱动桥系统产生的问题进行了深入的分析研究[1] 。以加速过程为分析对象, 以阶次分析技术[2] 为主要分析方法, 对产生较大的噪声及低沉异响及产生原因进行初排查。采集到的噪声分布如图1 所示, 车内噪声5. 93 阶及其高次谐阶次、8 阶及其高次谐阶次的噪声较大, 且存在电机PWM 载波频率产生的噪声成分[3] 。分析了安装在电机和减速器上的振动传感器采集到的数据, 如图2 所示。电机和减速器振动在5. 93 阶、8阶、24 阶及其高次谐阶次上均有体现, 且电机存在共振和PWM 载波频率的振动成分, 振动与噪声分布有一定的相关性。进一步排查, 在台架上对减速器的振动进行测试,辨别电驱动系统噪声和振动的源头。减速器台架振动测试结果如图3 所示, 存在5. 93 阶和24 阶次及其高次谐阶次。可见, 8 阶及其相关阶次振动和噪声是电机相关的特征阶次。具体地, 电机特征阶次为8 阶, 两级齿轮传动的减速器的啮合阶次分别为24 阶、5. 93 阶。电机特征阶次的高次谐阶次(3 次、6 次等) 与一级齿轮的啮合阶次及其高次谐阶次重合(2 次)、电机特征阶次的高次谐阶次(3 次、6 次) 与二级齿轮啮合阶次的高次谐阶次(4次、8 次等) 相接近、一级齿轮啮合阶次和二级齿轮啮合阶次的高次谐阶次( 4 次、8 次) 相接近, 引起了电机和减速器、减速器自身的振动耦合, 产生较大的振动噪声并伴有低沉的、有节奏的轰轰声。以车辆加速—匀速—制动—滑行运行工况对踏板动作时的异响进行分析研究, 运行过程中在车辆后排采集到的噪声数据如图4 所示。在松开油门踏板, 踩下制动踏板及松开制动踏板时均存在较宽频带的范围产生了无规则的噪声分布。分析了安装在电机和减速器上的振动传感器采集到的数据, 如图5 所示。在全工况范围内, 车内噪声和电机的振动在趋势上有一定的相关性。在踩下制动踏板时, 减速器振动变化和噪声的变化有一定的相关性, 受工况变化引起的振动尤其明显。具体地, 在踏板动作时, 传动扭矩瞬间突变, 由于传动侧隙的存在使传动系统运动副间会产生碰撞和噪声[4] 。判断该电动系统扭矩控制精度低及轮间存在较大的侧隙产生的异响问题。在不改变电驱动系统动力性的前提下, 优化了轮系配比。优化后的一级、二级齿轮的特征阶次分别为27、7. 6, 避开了传动系统内部特征阶次以及和电机特征阶次重合及相近的现象, 进而避免系统的共振及因此而产生的噪声大和“哄哄” 异响的现象。研究表明, 重合度越大不仅可以提高齿轮的承载能力, 而且可有效降低轮系噪声[5] 。细高齿齿轮采用了小模数、小压力角、大齿顶高的齿轮参数。小模数齿轮不但可以提高端面重合度, 且因齿根的减薄可提高轮齿柔性, 进而更易吸收轮齿的振动。小压力角的齿轮刚度也相应减小, 齿轮啮入和啮出的动载荷减小, 引起的冲击振动则相应减小。齿顶高系数增大可直接增大轮系重合度。与原方案采用标准渐开线齿轮不同, 新设计轮选用了小压力角、小模数和大齿顶高系数的细高齿齿轮设计, 增大了轮系重合度, 以实现减小轮系噪声目的。原方案和新轮系配比方案齿轮基本参数见表1。该减速器侧隙包含两级齿轮副侧隙以及差速器轮系侧隙。为了保证轮系润滑良好、补偿载加工制造偏差、安装误差、荷变形、热变形等因素的影响, 须有适当的齿轮侧隙。侧隙过小, 会引起轮系卡滞, 齿面磨损; 侧隙过大, 齿轮啮合或者反向啮合时的碰撞会产生较大的冲击和噪声。差速器内部侧隙为0. 32、0. 29 mm, 该侧隙值偏大为减速器工况变化时产生异响的主要原因。新方案该差速器侧隙分别调整为0. 20、0. 19 mm。为了进一步降低工况变化时传动系统产生的撞击及噪声, 在轮系动力传动许可范围内进一步收缩了一级、二级轮系的齿间侧隙, 较原方案减小12. 6%。优化全部完成以后, 通过装车试验对整改效果进行检查。在车内明显感觉到噪声有大幅降低, 且未有异响产生。分别采集了系统在运行过程中的振动和噪声数据, 驱动系统消除了因特征阶次重合或者相近而产生的振动耦合, 如图6 所示。优化后电驱动系统全工况内噪声最大为75 dB, 较原方案降低了10 dB, 电机和减速器竖直方向上振动有效值分别降低了50%和67%。电驱动系统的集成化设计是今后电驱动发展的主要方向。集成化电驱动系统NVH 面临电机噪声振动、减速器噪声振动、系统结构集成产生的噪声和振动等问题。在设计及优化过程中需要综合考虑电机噪声振动控制、减速器噪声振动控制、传动系统动力学匹配以及控制算法的优化等问题。传动系统中不可避免的侧隙是产生振动和噪声的主要原因。在进行电驱动产品设计开发时需要综合考虑系统功能和性能需求进而选择合理的最优的侧隙参数配置。作者单位:(中车戚墅堰机车车辆工艺研究所有限公司, 江苏常州 213000)免责申明:本公 众 号所载文章为本公 众 号原创或根据网络搜索编辑整理,文章版权归原作者所有。因转载众多,无法找到真正来源,如标错来源,或对于文中所使用的图片,资料,下载链接中所包含的软件,资料等,如有侵权,请跟我们联系协商或删除,谢谢!
著作权归作者所有,欢迎分享,未经许可,不得转载
首次发布时间:2023-04-18
最近编辑:2年前
作者推荐
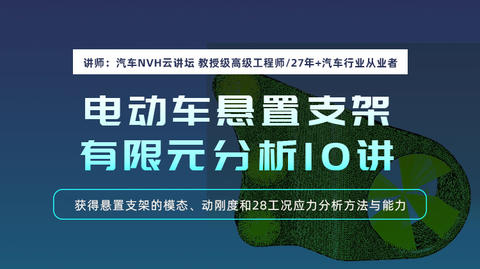