一种基于V模型下针对三合一电驱总成的NVH优化型研发方案
摘要: 本文针对新能源车用三合一电驱总成NVH系统研发,提出了一种基于V模式的优化型研发方案。通过建模与仿真不仅复现了电磁力和齿轮啮合刚度波动从激励源到传递路径(三合一电驱总成的结构)再到振动、噪声响应上的表现,而且追溯到了非声源的控制器的平板金属部件是噪声放大的主要原因。针对该现象,通过拓扑优化提升固有频率300~500 Hz,使平板件的噪声由结构噪声传递为主向空气噪声传递为主转变,再加上声学包裹等措施,综合性的降低噪声10~20 dB (A)。建模与仿真、测试和优化通过这种基于V模式的优化方案有机的结合到一起,节省了在子系统所占用的开发时间和开发成本。
关键词: V模型;NVH (噪声、振动及声振粗糙度);电驱动;MBS (多体动力学);电磁噪声;齿轮啮合;拓扑优化;PEU (控制单元);ODS (工作变形分析); 新能源汽车运行时,驱动总成的部分能量会以电磁噪声和齿轮啮合噪声的方式通过自身的结构路径及周围的空气路径传递出来。这三类分总成在机械性能上的较大差异使得三合一电驱总成NVH性能开发成为一项复杂的系统工程开发。 综合新能源电驱总成NVH特性、汽车零配件开发体系复杂的特点和量产开发时间的限制,在系统集成开发上,通常会通过引入开发模型来指导产品研发,常见的有瀑布模型、螺旋模型、快速原型模型和V模型等等。 鉴于V模型本身的开发、验证的对称性和广泛应用于系统工程的经验,本文提出了一种基于V模型下针对三合一电驱总成的NVH优化型研发方案来指导新能源汽车三合一电驱动总成的研发。 Forsberg等 [1] 在1990年为系统开发提出一套V模式开发方法,从系统需求出发到系统验证结束。在其需求定义及概念设计端,通过分解来得到子系统甚至到单元组件的需求。同时,在该模型的另一侧通过逐渐升级的验证,最终满足整个系统开发需求的验证。 针对更为复杂的新能源汽车三合一电驱总成,本文提出了一种基于V模型的优化型研发方案,见图1。 Figure 1. A based on V-model research and development optimizing strategy 该方案从仿真建模出发复现了电机电磁力和齿轮啮合刚度波动在整个传递路径上的振动、噪声响应的表现,从系统级仿真结果,即ODS运行变形直接反映了声源虽然是在电机和齿轮箱内,通过传递路径,噪声和振动在控制器的平板金属件上提现一个较为明显。在这基础上,通过对部件进行拓扑优化提升约300~500 Hz,迫使其结构噪声传声为主的形式转变为空气传声,同时,采用声学包裹,以这样一种综合手段来达到降低噪声约10~20 dB (A)。该优化方案将建模与仿真和验证优化有机结合在一起,节约了子系统开发时间和开发经费。 新能源汽车三合一动力总成NVH仿真 主要激励源来自减速箱齿轮啮合以及电机电磁激励。本文以某款三合一动力总成为研究对象,它由单档减速器,48槽8极永磁同步电机和控制器组成,建立永磁同步电机和减速器的三合一动力总成有限元模型,分别通过施加电磁力和齿轮扭矩,进行多物理场耦合振动噪声分析。 M(x)¯¯¯¯¯¯¯¯¯¯¯¯¯¯¯¯¯¯x¨−Qv−CTxλ=FM(x)¯¯x¨−Qv−CxTλ=F(1) 式中: M(x)M(x) 是其质量方程;C是坐标相关的限制条件; λλ 是拉格朗日乘数; QvQv 二次速度矢量。 建立声学模型之前,首先必须建立减速箱齿轴的刚柔耦合分析的多体动力学模型,在Simcenter 3D仿真环境中,齿轮和轴被作为刚体建模,动力总成壳体根据Craig等 [2] 提出的用于动力学分析结构的耦合方法来作为柔性体建模。通过多体动力学仿真,我们可以得到动力总成受到齿轮激励下的瞬态振动情况,便于进一步进行声学仿真分析。如图2所示。首先根据模型实际参数,依次完成轴系建模,齿轮建模,齿轴是参数化的刚体(输入轴齿轮1齿数为31,中间轴齿轮2齿数为20,中间轴齿轮3齿数为80,输出轴齿轮4齿数为77)。通过两级齿轮副减低转速增大输出扭矩。此外壳体,电机冷却水套以及定子根据材料属性建立有限元柔性体。模型中齿轴刚体和壳体柔性体之间由轴承模型连接,仿真模型一共包含8个轴承,分别位于电机轴,输入轴,中间轴和差速器输出轴两侧。传动系统由于齿轮啮合,通过轴承将产生的振动作用在壳体上,从而产生振动噪声。如图3所示,动力学仿真基于POT工况(1000~8000 rpm升速工况),其中输入轴施加电机转速,输出轴根据齿轮速比施加相应扭矩,壳体悬置点施加约束。 Figure 2. Multi body simulation model Figure 3. Simulation load condition 通过动力学仿真计算可得到壳体轴承在仿真工况下由齿轮啮合激励所受时域载荷。图4展示了差速器轴承处载荷时域曲线。 Figure 4. Differential bearing load in time domain 由于Simcenter3D软件基于电磁力的声学仿真要求在频域下计算,那么由多体动力学刚柔耦合分析计算的动态时域载荷必须经过傅里叶变换得到频域载荷才能施加到后续声学模型之中。整个声学仿真模型,主要有三部分组成:第一,傅里叶变换后频域下的轴承激励加载在壳体轴承座表面结构网格凝聚节点处,如图5,图6所示;第二,计算壳体结构体的自由模态结果,如图7所示;第三,在壳体结构体 Figure 5. Bearing coupling nodes distribution Figure 6. Bearing load in frequency domain Figure 7. Modal simulation result 外建立声学网格,并且设置声场麦克风测点,用于记录仿真结果。其次计算壳体网格表面到外部声场麦克风测点的声学传递向量(ATV)结果,如图8所示,该传递函数体现了麦克风测点的压强与壳体表面振动的关系。对于多转速的计算工况,整个声学仿真只需要计算一次声学网格的传递函数。最后进行声学仿真得到声场麦克风测点的声压结果。 Figure 8. Acoustic transfer vector 图9展示了控制器上方0.1 m处麦克风测点的声压结果瀑布图。在齿轮啮合激励作用下,二级齿轮啮合7.75阶和一级齿轮啮合31阶的声压在中高转速区域(5000~7000 rpm)比较突出。其中7.75阶对应的频率在646 Hz到904 Hz之间,31阶对应的频率在2583 Hz到3617 Hz之间,说明壳体在此频率区间的固有模态会引起较大的共振。 Figure 9. Acoustic pressure result of microphone measure point above PEU (0.1 m) 图9. 控制器上方(0.1 m)麦克风测点声压结果 永磁同步电机是通过定子绕组电流产生的气息旋转磁场与转子永磁磁场相互作用,产生转矩。气隙磁场中,也产生作用于定子铁芯的电磁力波,通过传递引起整个铁芯与壳体的结构振动,并向外辐射噪声。根据麦克斯韦定律,可以得到单位面积的径向电磁力和单位面积的切向电磁力,即: Fn=B2n−B2t2μ0Fn=Bn2−Bt22μ0 式中: μ0μ0 代表磁导率; BnBn 代表径向磁通密度; BtBt 代表切向磁通密度; FnFn 代表单位面积径向电磁力; FtFt 代表单位面积切向电磁力。其中径向电磁力是引起电机定子和壳体产生振动的主要因素,切向电磁力影响相对较小。电磁力可通过电磁仿真软件计算,并施加在电机定子铁芯齿部。 电磁激励下的声学仿真也主要有三个部分,除了壳体结构体的自由模态结果和结构体表面到外部声场麦克风点的声学传递向量结果。如图10和图11所示,还需在电机定子齿面映射傅里叶变换后各转速频域下的电磁力激励。然后利用声学网格的传递函数,进行声学仿真得到声场麦克风测点的声压结果。 Figure 10. Electric magnetic force in frequency domain Figure 11. Electric magnetic force mapping on mesh 图12展示了控制器上方0.1 m处麦克风测点的声压结果瀑布图,其中24和48阶在高速区间(6000~8000 rpm)的声压比较突出。 Figure 12. Acoustic pressure result of microphone measure point above PEU (0.1 m) 图12. 控制器上方(0.1 m)麦克风测点声压结果 通过仿真中的ODS分析,控制器的平板件在工作运行状态下表现出相对较为明显的变形,其主要原因是这些冲压平板件结构薄弱,一阶约束下的固有频率都低于800 Hz,见表1。在振动噪声传递中,它们体现主要为结构传声为主导的噪声传递,在后期很难通过一些隔声的声学包裹策略来减低该噪声,因此在这里采用了拓扑优化方法来提升其固有频率。 Table 1. Improvement of eigenfrequency 以上盖板为例,见图13,对初始设计仿真发现其固有频率在516 Hz,然后通过填补材料提升至845 Hz,然后优化材料质量分布,最终可以实现其固有频率达到806 Hz,即超过800 Hz的目标。 Figure 13. Topology optimization of upper cover plate 通过拓扑优化的方法,将三合一电驱动总成的主要噪声放大部件由结构噪声传递为主导转变为空气噪声传递为主导之后,采用声学包裹方案,可以最大程度的提升降低噪声传递的效果。 Figure 14. Comparison of initial state, stiffness improvement and acoustic package combined with stiffness improvement 图14. 初始状态、刚度加强和声学包裹配合刚度加强下的对比 从图14中可见,通过先提升固有频率再做声学包裹的综合方案,控制器上盖板的测点声压级下降约10~20 dB (A)。 三合一电动力总成的NVH性能验证通过在半消声实验室的环境中,对其主要的行车工况:小油门、中油门、大油门和制动能量等多种工况进行考核。通常采用5点法布置传声器,分别考察近场10 cm和远场1 m处的声压,见图15。 Figure 15. Shanghai Electric 160 kW EDS in Anechoic laboratory of CATARC 图15. 上海电气160 kW电动力总成在中汽研半消声实验室 通过在中油门工况下采集近场声压数据,后处理成为瀑布图,可以观察到三合一电驱总成各个声源阶次的分布,见图16。 Figure 16. Noise characteristic of EDS 由于是二级减速,共有两组齿轮啮合,产生7.75和31阶次啮合及其谐波阶次的噪声。电机主要产生24和48阶次噪声。控制器的变频噪声主要表现在基于载波频率10 kHz的阶次。以电机电磁力阶次为例,见图17,总压级的部分峰值点是主要由阶次噪声贡献的。 Figure 17. Overall noise sound pressure and order contribution 在相同工况下通过声源定位测试,同样发现一级齿轮啮合31阶噪声和48阶电磁噪声在控制器上盖位置较为明显,同仿真ODS分析结论一致,见图18和图19。 Figure 18. 31th order noise source localization Figure 19. 48th order noise source localization 本文介绍了一种基于V模型下针对三合一电驱总成的NVH优化型研发方案,首先通过仿真和建模还有测试上找到了对应的阶次噪声,并分析其基理从而进行产品优化,下一步可以把电磁激励和齿轮激励源耦合在一起进一步完善建模和仿真流程。 免责申明:本公 众 号所载文章为本公 众 号原创或根据网络搜索编辑整理,文章版权归原作者所有。因转载众多,无法找到真正来源,如标错来源,或对于文中所使用的图片,资料,下载链接中所包含的软件,资料等,如有侵权,请跟我们联系协商或删除,谢谢! 著作权归作者所有,欢迎分享,未经许可,不得转载
首次发布时间:2023-04-20
最近编辑:1年前
作者推荐
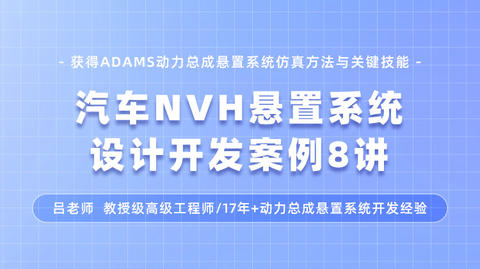