多工况下发动机振动噪声研究
摘要: 针对某公司生产的内燃机在780 r /min 转速下振动噪声过大的问题,对内燃机做振动噪声试验并得出振动噪声过大的原因,得到该内燃机噪声与振动的分布规律,为后续内燃机的悬置设计提供一定的实验依据。测试内燃机转速分别为780、820、2 200 r /min 且负载不同工况下的振动信号,和内燃机在750 ~ 3 390 r /min 加速工况下的瞬态噪声信号。对所测稳态信号进行频谱分析,计算振动烈度,得出该内燃机转速与负载对噪声的影响,并对瞬态信号进行阶次分析,得到各阶次信号随转速的变化和主要的贡献阶次。最后根据以上对内燃机振动噪声的分析结果对内燃机悬置系统的模态进行设计。结果表明: 稳态工况下,随着转速的提升基频也随之增加,Z 轴的振动烈度比同转速的X、Y 轴大; 内燃机在780r /min的振动烈度大于在820 r /min 的振动烈度,说明内燃机在780 r /min 时产生了共振; 噪声主要由1 阶、2 阶、4 阶、6 阶、8阶机械噪声合成,机械噪声是由轴承或静偏心导致的机械噪声阶次及其谐波阶次,为内燃机的悬置模态设计提供了参考。 关键词: 内燃机; 振动噪声信号; 频谱分析; 振动烈度; 阶次分析 内燃机由于动力强、热效率高等优点被广泛运用于船舶、汽车和其他设备上。但内燃机质量大,振动噪声高,长时间运行时发动机温度和压力过高,气缸内易积攒烟灰和积碳。由于内燃机在运行过程中,活塞撞击和零配件的间隙过大等都会导致内燃机缸盖和机体振动[1]。内燃机表面的振动信号反映了内燃机内部的工作状态,对振动噪声信号进行测试和分析可以得出内燃机内部运行状况和振动噪声产生的原因[2-4]。 21 世纪以来,国内内燃机噪声与振动控制发展迅速。文献[5]中对内燃机噪声源识别技术、内燃机轴系扭转振动产生机制、内燃机噪声声强测试法等做了大量的研究。文献[6]中对内燃机结构振动、表面辐射噪声进行了深入分析,并研究了内燃机结构的振动与辐射噪声间的关系。 本文作者对主流噪声振动测试设备采集的振动噪声信号进行频谱分析,并对分析所得的振动频谱图、ColorMap 图、阶次分析图进行分析,得出振动与噪声产生的原因。 内燃机表面振动的激励信号频谱范围较广。为了研究振动响应信号,采用测试频谱范围较广的加速度传感器和声学传感器。振动信号测量过程中,所测量的信号需要经过传感器、放大器和数据采集系统等。 现主流测试设备主要由德国海德、德国西门子、美国PCB、丹麦BK 等公司生产提供。此次试验采用的是德国西门子公司生产的LMS SCADAS MobileSCM05 多通道噪声振动测试系统,该系统由LMSSCADAS Mobile SCM05 数据采集前端、SimcenterTestlab 18 测试分析软件、Simcenter Testlab 18 模拟合成软件及相应的声学和振动传感器组成。该系统与其他同类产品相比,所测量的振动和噪声信号精确度更高,故测量数据精确可靠。所使用的声学传感器的灵敏度为50 mV/Pa。LMS SCADAS Mobile SCM05 数据采集前端可以记录包括数字以及音频数据、振动信号和加速度信号在内的多种数据。所采集的声音和振动信号由相应的多通道分析系统进行分析和处理。 一般而言,加速度传感器和声学传感器布置在能够充分反映被测对象信息的地方,测点不应布置在阻尼部件上,应该尽可能与直接传递路径相重合; 测点位置应易于传感器的安装与测试; 三向加速度传感器的方向应与发动机激励力的方向一致。X 向是沿着发动机转轴的方向; Y 向是平行于地面的平面上,垂直于X 轴的方向; Z 向是垂直于地面的方向。 图1 所示为建立的台架示意,采用4189 型1. 27cm ( 1 /2 英寸) 自由场传声器和356A32 型三轴加速度传感器测试噪声和振动信号。 此实验在实验室进行,内燃机产生的废气将通过排气管引出室外。由于此内燃机采用的是水冷方式且没有安装空气滤清器,所以在测量噪声时将不考虑排气噪声,只采集了内燃机表面的噪声。当内燃机在试验台架上开始运转时,其油温和水温将上升为常规的工作温度,用试验台架将内燃机转速稳定在设置好的工况下进行测试。将采样频率设置为24 000 Hz。为 确保试验的准确性,每天测试一组数据,一共测试3d,每次测试时间为10 s,测试试验温度和湿度分别为20 ℃和55%。 测试工况如表2 所示。可知对内燃机在转速780r /min、扭矩10/45 N·m,转速820 r /min、扭矩10/50N·m,转速2 200 r /min、扭矩150/250/360 N·m三个稳态工况下进行测量,并测量内燃机在转速780~3 390r /min 的加速过程中的试验数据。 内燃机噪声测试参照国家标准GB 1859—2000《往复式内燃机辐射的空气噪声测量工程及简易法》,按照规定采用九点布置法。噪声测点布置如图2 所示,可见噪声测试的表面为一个矩形六面体,第一张图为矩形六面体的前视图,第二张为俯视图,圆圈代表声学传感器,测试表面与内燃机各侧面平行且距离内燃机1 m。加速度传感器的布置位置根据相关标准应选在机体上或振动较大的结构点上。结合文中分析的内容,将加速度传感器布置在柴油机上部靠近进气口位置、柴油机外壳上部中心位置、柴油机脚支撑位置。 频谱分析是稳态工况信号处理最重要和最常用的一种方法,对测试的时域信号进行快速傅里叶变换,分析得信号的线性自功率谱[7]。为了让人们直观地分析信号的频谱特性,频谱图反映了信号的频率和幅值之间的关系,从而诊断信号的问题频率[8]。 由测点布置可知在柴油机进气口周围布置了一个三向加速度传感器,测出的加速度信号代表了进气口的振动,其在转速780 r /min、扭矩10 N·m,转速820 r /min、扭矩10 N·m 和转速2 200 r /min、扭矩150 N·m 稳态工况下X、Y、Z 向振动频谱如表3所示。振动烈度表示振动强烈程度,国际标准组织( ISO) 常用加速度的均方根值来表示,因为其包含了频率的信息,从而反映了振动信号的能量。表3中的RMS 值代表了780、820、2 200 r /min 的振动烈度。 众所周知,当扭矩一定时,气缸吸入气体的速度随着转速的增大而增大,从而进气管附近的振动强度和频率也会加强。但是由表3 可知,780 r /min 的振动烈度大于820 r /min,可见发动机在780 r /min 转速时内燃机内部零件产生了共振,从而导致了振动烈度的增加。反映了很多汽车在启动时的抖动明显大于行驶时。由于内燃机零部件精度不够,个别气缸气体的作用力较其余缸体增大或减小,使得各缸的进气量不同,导致各缸运动功率不平衡,这些都会引起内燃机受力矩的大小不同,从而产生抖动现象[9]。当转速提高到2 200 r /min 时,进气口振动烈度大幅增加,可见上述论证正确。 由表3 可知,随着转速的提升,发动机的转频也在随之增加,共振发生所在的频率也随之增大。 由测点布置可知在柴油机进气口周围布置了一个三向加速度传感器,测出的加速度信号代表了进气口的振动,它在转速为2 200 r /min,负载为150、250、360 N·m 稳态工况下X、Y、Z 向振动频谱图和振动烈度如表4 所示。 综合上述同一测点的试验数据分析转速和负载对进气口振动的影响。当内燃机转速增大时,各部件的惯性力增大,从而使内燃机相对运动的零部件间撞击产生的振动增强,则测量的振动加速度信号幅值应该随着转速的提高而增加,但数据显示同一扭矩下780r /min 的振动烈度反而大于820 r /min,说明内燃机内部零部件在780 r /min 时存在共振。当柴油机转速相同负载增大时,每循环供油量增加,燃烧的最高压力提高,作用于活塞等运动件的力相应增加,机械振动必然随着负载的增加而增加,所以振动烈度也随之增加。 由频谱分析可得测试信号的频域特性,但无法区分瞬态工况下阶次不同的噪声源可能是同一频率的情况。因此,对于非稳态工况而言,需要对测试信号做瀑布图分析,常采用跟踪转速的方式,并画出Color-Map 图[10]。 分析旋转机械的振动噪声,阶次分析是其中重要的内容,这就离不开ColorMap 图分析。ColorMap 图的横轴表示频率,纵轴表示转速,故ColorMap 图可以反映信号随转速、频率变化的规律,用颜色深浅表示测试信号的幅值大小,红色代表信号幅值的最大值,蓝色代表信号幅值的最小值。 图3 为机械负载下,内燃机转速由750 r /min 匀加速到3 390 r /min 时测得的噪声信号ColorMap 图,表明1 阶、2 阶、4 阶、6 阶、8 阶噪声为内燃机噪声的主要成分。图4 反映了各个阶次不同转速下的噪声对整体噪声水平贡献的大小,图中曲线1 代表了整体的噪声水平。在750 ~ 3 390 r /min 转速范围内,8 阶噪声占主导地位; 6 阶、4 阶、2 阶、1 阶噪声依次减小。总体而言,1 阶、2 阶、4 阶、6 阶、8 阶噪声对内燃机噪声水平贡献最大[11]。 在已设计完成悬置基础上,可以根据发动机的振动进一步优化参数,让传到车内的发动机激励最小。通常,会通过优化系统约束条件来达到隔振的效果。实验结果表明发动机在780 r /min 时产生了共振,故在设计悬置系统模态目标时考虑了转频13 Hz,避免产生共振。悬置系统固有模态目标如表5 所示。 ( 1) 稳态工况下,随着转速的提升基频也随之增加,Y 轴的振动烈度比同转速的X、Z 轴大,且内燃机主要峰值振动频率为内燃机转频的整数倍,验证了实验数据的准确性。 ( 2) 测量的振动加速度信号应该随着转速的提高而增加,但表3 显示同一扭矩下780 r /min 的振动烈度反而大于820 r /min,说明内燃机内部零部件在780 r /min 时存在共振,对内燃机悬置系统设计有一定的指导意义,并给出了悬置系统模态的优化目标。 ( 3) 由图4 可得出噪声主要由1 阶、2 阶、4 阶、6 阶、8 阶机械噪声合成,可对其相应的噪声产生原因进行优化。 作者单位:( 南京工业职业技术大学,江苏南京210023) 往期相关推荐
相关文章,在仿真秀官网搜索:
基于传递路径分析对某SUV加速轰鸣声问题诊断与优化 免责申明:本公 众 号所载文章为本公 众 号原创或根据网络搜索编辑整理,文章版权归原作者所有。因转载众多,无法找到真正来源,如标错来源,或对于文中所使用的图片,资料,下载链接中所包含的软件,资料等,如有侵权,请跟我们联系协商或删除,谢谢!
著作权归作者所有,欢迎分享,未经许可,不得转载
首次发布时间:2023-04-20
最近编辑:1年前
作者推荐
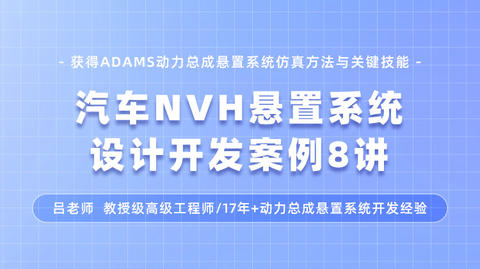