某纯电动汽车车身NVH的优化设计
[摘要]运用ANSA、MSC Nastran、Hyperview等CAE分析软件,对新开发的一款纯电动汽车全铝框架车身,建立铝舍金白车身结构有限元分析模型,设置载荷及边界条件。对白车身的模态、灵敏度、噪声传递函数和空腔模态进行有限元计算。并结合电动汽车的振动结构特点对纯电动铝合金车身NVH进行综合性分析、评价,并给出有效的改进措施和解决方案。在新车设计阶段进行NVH的性能预测分析和研究。对于避免振动、降低车内噪声具有积极意义。以上分析流程可以为后续的纯电动铝合金车身的结构优化提供参考和理论依据。[关键词]纯电动汽车;全铝车身;NVH;模态;车身灵敏度;空腔模态目前,由于汽车日益增加,能源紧缺、环境和噪声污染越来越严重。研究表明,汽车轻量化可以减少燃油的消耗,从而在很大程度上缓解汽车快速发展给资源环境带来的巨大压力。由于铝是一种质地轻,强度大,可回收率高的绿色材料,车身采用铝合金,可以大大降低汽车重量,从而减少能源的消耗。随着人们环保意识的增强,新能源汽车越来越受到人们重视,特别是纯电动汽车。由于安全、绿色、节能、环保得到了人们热烈欢迎和国家大力支持。随着生活质量的提高,人们对汽车的噪声(noise)、振动(vibration)、声振粗糙度(Harsh—ness)(简称NVH)有越来越高的要求[2]。由于车身是汽车的主要组成部分,在设计开发阶段就应该严格控制车身的振动噪声,使其达到较好的效果。由于纯电动汽车与传统汽车的NVH有较大的差别。因此,对独立新开发的一款自主品牌纯电动全铝车身汽车。在设计开发阶段运用CAE技术对车身NVH进行系统设计与优化.可以准确对其NVH进行预测和综合评价.有利于降低噪声和振动,有利于指导白车身的优化设计,有利于提高其声学品质和舒适性,从而可以缩短新车上市的时间,节约开发成本,减少生产后的整改,有助于我国新能源汽车提高自主品牌的创新能力和核心竞争力。运用快速高效的ANSA前处理软件对某新开发的纯电动汽车白车身进行前处理。把建成的白车身有限元模型按网格质社标准进行检查和处理,使其网格质址达到标准要求叽其中,白车身 有限元共有88 407个单元,节点数77 4934个,其 中四边形单元873 196个, 占总数的98.77 %, 白 车身质址296.3kg, 与同类型的传统车身相比减轻了约30%的重址。如图l所示为电动汽车白车身有限元模型。在概念设计阶段,首先,分析竞争车型和参考 车型的NVH性能后,制定总体技术指标,确定开发车型的NVH总体指标及其分解目标值[4]' 并绘 制出整车主要模态规划表,如表1所示。通过模态分析,可以优化车身结构,避开常速下主激励元激励频率,防止4身产生共振,并确定 出车身变形较大的部位, 从而可以改进车身结构 和刚度, 减小振动和噪声的产生与传递玑利用astran 软件对白车身模型进行模态计算,对白车身有限元模型在自由状态下进行模态提取, 除去固有频率接近于零的刚体模态振型,提取其前10阶柔性模态为主要研究对象,求解前10阶的模 态值,如表2所示。输出前10阶振动位移云图并 进行分析,其中图2、图3分别为白车身第一阶扭转模态振型图和第一阶弯曲模态振型图。为减少电动汽车振动和噪声,避免发生共振, 车身结构模态频率应错开主要激振源频率。对于纯电动汽车,车内噪声主要有电机动力总成 噪声、电池风扇噪声、 车外空气流动引起的噪声和外部 的车轮与路面不平衡引起 车体振动产生的噪声玑轿车外部 车轮和路面不平衡引起激励频率一般在20 Hz以下,而车身一阶固有频率实际为27.55 Hz, 明显大于20 Hz, 不易发生共振[8) 。由上述计算结 果分析后可得,一阶固有频率27.55 Hz, 不仅避开了车轮激振频率20 Hz, 而且避开了主要激振椋 频率23Hz, 一阶固有频率大于一阶扭转模态目标值27 Hz, 不存在与电动汽车主要激励諒耦合 共振的风险气但是,一阶弯曲固有频率27.77 Hz 小千设定目标值29 Hz, 现提出以下3种优化改进方案。方案I:在A柱位置横梁增加倒角(左右4个 角),C柱实施同样方案,并增加焊点数扭。方案2: 在方案1基础上,A柱、B柱、C柱分别由1.5 mm增 至2 mm,A柱接头处由1.5 mm增加至2.5mm 0 方案3: 在方案2基础上C柱接头采用刚性单元使 C柱刚性连接。计锌结果:方案l、方案2弯曲刚度 分别为10 268 N/mm、11 566 N/mm, 达不到刚度目 标值12 000 N/mm。方案3弯曲刚度12 598 N/mm, 1阶固有频率为1阶扭转, 提高到了28.29 Hz,2阶频率为l阶弯曲,提高到了31.25 Hz。方案3C 柱接头刚性连接及优化前后对比如图4、表3。车身灵敏度分析是车身NVH优化设计重要的组成部分。通过灵敏度分析可以确定设计过程中对结构响应最为敏感的部位, 从而可以获得设 计参数和灵敏度系数气在不同分析工况下,对白车身进行不同边界条件加载, 分别计算其模态灵 敏度、前扭转刚度灵敏度、后扭转刚度灵敏度 和弯曲刚度灵敏度。计算分析得到前20个最高灵敏度零部件柱状图。如图5所示为一阶弯曲模态前20 个最高灵敏度柱状图和对应的零部件图。计算结果显示,后侧围内外板、减震器支座及 A柱、C柱 的模态和刚度灵敏度较高。分析结果中给出了校 态,扭转和弯曲刚度的最高的前20个灵敏度数值 和对应的板块,为车身NVH结构优化设计提供理论依据。传递函数不仅可以了解其动态特性,而且可以用千诊断容易产生共振的频率点及其所对应的响应,可以验证设计能否克服共振、疲劳及结构破坏[9) 从而为提高车身的NVH性能提供优化改 进方向。在20-200 Hz范围内,对白车身上选取的l6激励参照点进行添加激励,对每个激励点施加1个单位激励力,计算各个安装点卢压曲线,输出相应的驾驶员和后排乘员耳旁噪声传递函数的声 压曲线。由输出的各个卢压曲线图可以看出,除左 后减谁楛安装点所产生的声压曲线图外, 其余各 个响应点均能满足要求。 左后减振器安装点声压曲线图,如图6 。 分析其安装点声压曲线,发现在67 Hz 处出现峰值,对应的分贝值为 67.l dB, 明显大于目标俏60dB, 需要对其进行优化改进。 根据实际工程经验, 可通过改进螺旋弹簧支撑点位置约束点降低振动幅值, 同时把白车身原来的约束 点位管处的悬臂结构改至纵梁下表面上, 如图7所示e 同时, 把车后轮上方螺旋弹簧支座进行加强, 在车身后部灵敏度高的部位处适当增加焊点 数计,并在前座椅下方添加沥背阻尼板。 优化后, 振动传递响应函数曲线得到了明显的改善, 两条卢压曲线所有峰值均低于目标值60dB。 在最高 峰值处卢压为59.5 dB, 满足目标值要求。由千汽车车室是弹性薄壁腔体结构, 其内部噪声不仅有外部传人车内的辐射噪声, 而且还有 车体薄壁结构与车内空气之间耦合作用产生的低频轰鸣噪声, 这种噪声对汽车的乘坐舒适性有很 大的影响。因此,进行车室空腔模态分析,不仅可 以掌握汽车车内卢场的分布, 采取相应的改进措施进行降噪, 而且能够解释车身低频噪声产生的 机理。在整车结构网格基础上建立六面体网格为主的轿车声腔三维有限元模型, 对白车身结构有限 元模型进行封闭处理, 即在该模型基础上增加仪表台、仪表横梁、挡风玻璃、开闭件以及前后座椅等部件饥把模型设置好模态参数后,并假定车室内部环境处于理想条件下, 利用模态提取算法得 到固有频率和振型,如图8所示(其中规定汽车坐标系的X、Y、Z轴分别为纵向、横向、垂向)。其中,在0 Hz 时出现一致声压模态,相当于结构模态中 的刚体模态。去掉一致声斥,得到车身声学模态前10阶声学频率和模态振型,如表4所示。由模态振型图可得,第l阶纵向声压模态频 率为70.3 Hz, 如图9所示,声腔模态图中相对声压从前向后依次递减,零声压节面出现在声腔中 部,即在驾驶员座椅头部位置处,这对汽车是有利的(9]。第l阶横向卢压模态频率为126.8 Hz, 如 图9所示, 相对声压从前部下端位置处向上端逐渐递减,在后排座椅处出现相对声压最小值。第l 阶垂向声压模态频率为152.2 Hz, 但第1阶垂向 声压伴随若纵向声压一起出现,其前、后排座椅头 部处声压较小。其余声腔模态基本上是纵向、横向 和垂向声压模态的组合玑前10阶空腔声压模态振型均满足设计要求, 其前后座椅头部位置处的声压均未出现过高的现象。本文通过设计一整套车身NVH分析流程,对新开发的电动铝合金汽车车身, 在设计阶段运用有限元软件对车身的校态、静刚度、噪声传递函数、灵敏度和空腔模态进行有限元计算和分析并做出相关评价,对不满足目标条件的部分进行优化并给出可行性修改措施和改进方案。通过优化改进,白车身强度刚度得到加强,振动噪声得到明显降低。以上对电动汽车车身NVH改进和优化,减少了车身的振动,降低了车内噪声,提高设计质量, 并为后续车身结构优化提供设计方向和理论依据。作者单位:(1.200093上海市上海理工大学机械工程学院;2.201399上海市上海同捷汽车设计工程研究院)免责申明:本公 众 号所载文章为本公 众 号原创或根据网络搜索编辑整理,文章版权归原作者所有。因转载众多,无法找到真正来源,如标错来源,或对于文中所使用的图片,资料,下载链接中所包含的软件,资料等,如有侵权,请跟我们联系协商或删除,谢谢!
著作权归作者所有,欢迎分享,未经许可,不得转载
首次发布时间:2023-04-20
最近编辑:1年前
作者推荐
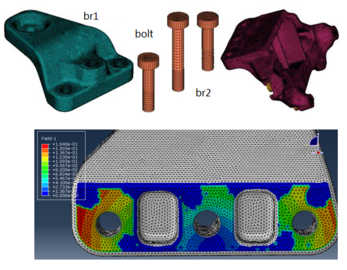