某车型路噪性能优化控制
[摘要]:通过 分析某车型的路噪问题,确认该车辆行驶在粗糙路面和石块路面时,车内的相关路噪问题。采用试验传递路径分析方法,获得各传递路径对路噪的贡献量,锁定产生主要贡献量的相关系统部件。利用已有的整车CAE模型 ,对整车模型进行ODS分析,根据阵型结果找到对峰值影响较大的部件,并快速验证。结合试验和CAE手段,制定合理的优化方案,从而提升整车路噪性能。关键词:路噪,传递路径分析(transfer path analysis,TPA),ODS分析,CAE分析Key words: Road Noise, TPA, ODS Analysis, CAE随着汽车技术的不断发展,消费者对汽车的NVH性能有了越来越高的要求,其中在中低速行驶时的路噪性能越来越受消费者的关注,是汽车用户对汽车品质最敏感的主观感受之一。高品质的汽车一定要有高品质的路噪性能特性,因此在整车NVH性能开发过程中,对路噪问题的研究就显得至关重要。本文针对某车型的路噪问题通过传递路径分析的方法,对轮胎、悬架、副车架及其与车身连接点等进行试验传递路径分析,结合整车CAE模型仿真分析,从各个传递路径中锁定主要的能量贡献路径,找出主要的贡献部件,从而对路噪性能进行优化。某车型前悬架为麦弗逊式独立悬架,后悬架为多连杆独立悬架,在粗糙路面和石块路面行驶时,主观评价评价后排有明显的Drumming Noise(隆隆声),严重影响整车的舒适性,直接影响整车的NVH性能。在粗糙路面上60km/h行驶时,对该车进行客观测试,并与目标车对比分析, 发现在车内前排151Hz附近和 后排213Hz附近存在明显噪声峰值。客观测试数据如图1所示,注:红色实线是该车型的前排噪声数据,绿线虚线是该车后排噪声数据。路噪主要是路面激励轮胎产生的噪声,根据传递路径的不同,路噪分为空气传递噪声和结构传递噪声,传递图如下图2所示:主要机理如下:轮胎胎面以及道路的空腔形成“气泵效应”,当轮胎接触地面时,胎面或者道路空腔离聚集的空气受到挤压突然外流,当轮胎离开道路接触面时,空气将突然流入,在这个“气泵效应”过程中产生噪声,主要是通过空气传播传如车内[1]。路面对 轮胎的激励产生的结构噪声来自两个方面,一方面是路面通过接触面对轮胎不断地局部压缩和释放产生垂向力,另一方面是路面与轮胎橡胶在接触面不断地滚挤和释放产生纵向激励力。路面对轮胎的激励力经过轮胎内空腔和轮辋的耦合系统传递到车轴,从车轴传递到底盘悬架系统,进而传递到车身,传入车内。传递路径分析的主要思想就是将机械系统简化为“源-路径-响应点”的模型,如图3所示。系统被分为主动侧和被动侧,主动侧包含了噪声和振动源,被动侧包括响应点。激励力即作用于被动侧上的力和声压作为系统的输入。传递函数(FRFs)用来表示激励力和响应点之间的关系,传递路径的动力学特性通过FRF表示在TPA模型中,目标点响应可表示为:
其中,为激励力,表示由振动源作用在机械系统上的结构载荷;为体积加速度,表示由声源作用在机械系统上的声载荷;表示激励力i或声源j到响应点k的频响函数。目标点的响应由结构贡献和空气声贡献叠加而成,本文针对结构传递的路噪进行分析优化控制。TPA分析方法最重要的步骤是得到准确的激励力、及传递函数FRFs。传递函数FRFs通常是通过力锤和标准声源作为已知激励,再测量目标点处的响应得到。对于激励力的获得,本文采用逆矩阵法,由被动侧参考点响应乘以传递函数矩阵H的伪逆得到载荷力:其中,H!"为传递函数矩阵,表示激励力i到被动侧参考点j的传递函数。F!和传递函数的测量方法一样。a!表示激励源附近的被动侧参考点在运转工况下的响应[3-4]。最后,传递函数FRFs和激励力合成目标点的响应信号公式(1),每条路径的贡献可由此分析得到。在粗糙路面上以60km/h匀速行驶,测试从车轮、悬架弹簧、减振器及与车身连接点振动加速度,同时测试车内前后排目标点的声压级,动态工况下各传递路径振动加速度测试试验照片如图3、图4、图5所示。在半消声室内测试各传递路径到车内前后排目标点声振传递函数和各个传递路径激励力到各自参考自由度的振振传递函数。在用利锤测试频响函数时,需要拆除车轮、悬架,用以消除各系统激励力耦合的影响;用力锤分别敲击悬架系统与车身连接点的x、y、z 三个方向,同时测量车内前后排目标点的声压信号和各个激励点参考自由度的振动加速度响应信号,传递函数试验照片如图6所示。将试验测得的各路径激励处到各参考自由度的频响函数和在粗糙路面以60km/h行驶时各参考自由度的加速度信号带入公式(2),可以计算得到60km/h匀速行驶时各传递路径的激励力。将各传递路径的激励力和各激励点到目标点的声振传递函数带入公式(1),可以得到由路面激励轮胎产生的结构传递路噪声的合成噪声。如图7、图8所示,车内前后排目标点实测噪声值和用TPA模拟计算的数据吻合,可见TPA的计算结果可信。根据公式(1),可以计算出各传递路径对车内路噪的贡献量。分别针对问题进行贡献量分析,如图7、图8所示给出了151Hz和213Hz附近各路径对车内路噪的贡献量。从图7可以看出左后拖曳臂Z向对车内151Hz附近车内路噪在路径上贡献比较大,从图8可以看出左侧后悬下控制臂Z向对车内213Hz附近车内路噪在路径上贡献比较大。需要对这两条路径进行优化,来控制车内路噪。
整车CAE分析能够快速锁定问题,并提供有效优化方向,以下阐述整车CAE分析对路噪改进的贡献。整车模型有以下部分组成:模态车轮+底盘模型+TB模型+声腔模型,其中模态车轮模型是由详细车轮模型减缩而来,且考虑了轮胎压力、轴荷和轮胎声腔与结构的耦合,将重点说明。在动态分析中,使用相对较少自由度的车轮模型来代替真实的轮胎和轮辋,这个模型就是模态车轮模型。建立详细车轮模型,包括:轮胎和轮毂。轮毂由CAD数据生成;轮胎胎面从轮胎的剖切面获得,整合轮胎和轮毂的两部分。如图9 所示。有限元模拟时使用实体单元和壳单元,橡胶材料使用CHEX(8)、CPENTA(6)和CTETRA(4)单元,材料卡片为MAT1,增强层使用CTRIA3和CQUAD4单元。图10展示了轮胎模型的截面。车轮的胎压为2.2bar,前后轴荷分别为462.5kg和320kg,自由模态分析时需要考虑这些边界条件。由于轮胎材料参数的不确定性,分析值不能很好的和试验值吻合,需要进一步优化模型。使用SOL 200[5]优化方法,使分析模型和自由模态相匹配。优化模型考虑胎压和轴荷引起的车轮变形,因为这些边界条件会使轮胎变形,刚度产生变化,使用Nastran求解序列Sol 106[5],处理这个非线性过程。使用非线性分析的结果作为优化分析的输入,设定优化函数。最终优化结果是CAE模型模态值与试验匹配,分析FRF与试验一致。具体结果见表1及图11。由于详细轮胎模型自由度较多,且需要考虑胎压、轴荷及轮胎声腔和结构的耦合,搭载在整车模型中计算动态响应,会使计算模型十分复杂。对详细车轮模型进行减缩,可以得到模态模型,大大提高计算效率。减缩过程如下:定义轮胎与地面的接触区域;生成计算轮胎模态矩阵的关键字;计算胎压和接触区域的轮胎变形模型;计算及输出变形轮胎的质量和刚度矩阵。完成模型减缩后,需要重新验证减缩模型的准确性,计算减缩模型的FRF曲线和模态,并与试验值进行对比。首先进行整车路噪分析,在车轮接地面施加通用载荷,获得车内的声压响应。参照试验结果, 155Hz和211Hz与车内相关噪声峰值有比较明显的相关性,应该进行优化。在整车状态下,进行使用Nastran的SOL 108求解序列进行ODS分析,ODS分析结果显示155Hz和211Hz时,拖曳臂的阵型明显,认为拖曳臂的振型对这两个峰值贡献度考虑到底盘件与操稳关联度较大,不建议从拖曳臂本体进行优化,而对拖曳臂与车身安装点进行优化,增加局部刚度,减少底盘力往车身上的传递。另外,可以减弱拖曳臂衬套的刚度,同样可以减少力传递。验证结合CAE分析结果,从结构噪声传递的特性出发,需要考虑激励力的贡献和声振传递函数的贡献。分析发现左后拖曳臂和左侧后悬下控制臂的激励贡献大于其对车内路噪的传递函数的贡献。因此从激励力的角度优化左后拖曳臂和左侧后悬下控制臂。提高左后拖曳臂与车身连接点的刚度,减小激励力,降低车内路噪。针对左侧后悬下控制臂影响,减小其与车身连接衬套的刚度,提升衬套隔振性能,降低车内路噪,由于衬套刚度降低,下控制臂系统频率有所降低。如图16所示为提升左侧后悬下控制臂与车身连接点刚度,图17为左侧后悬下控制臂衬套位置示意。优化后车内路噪改善效果如图18和图19所示,前排151Hz和后排213Hz附近噪声分别降低了3.2dB(A)和10.3dB(A),车内路噪明显减小,主观评价非常满意,达到预期目标。应用试验TPA结合整车CAE模型进行ODS分析的基础上,得到以下结论:(1)利用试验TPA的分析计算云图的结果,准确锁定车内路噪的主要贡献路径;结合整车CAE模型进行 ODS分析,快速准确的制定优化方案。(2)通过提高左后拖曳臂与车身连接点的刚度,减小左侧后悬下控制臂橡胶衬套的刚度,有效的控制了结构传递的路噪声,使车内路噪得到有效控制。作者:田明灿,张承志,庄惠敏,吴列,TABATA,曲婧瑶免责声明:分享此文仅为传播汽车NVH相关知识,其版权归原作者所有,感谢原作者的辛苦付出;若有侵权异议等请跟我们联系协商或删除,谢谢!
著作权归作者所有,欢迎分享,未经许可,不得转载
首次发布时间:2023-04-22
最近编辑:2年前
作者推荐
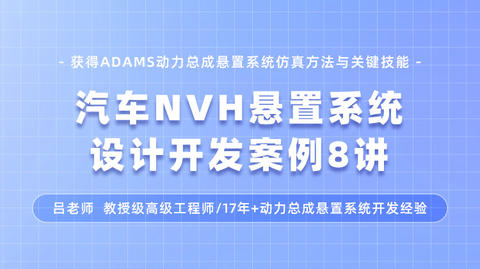