橡胶悬置刚度特性对过减速带平顺性影响研究
[ 摘要] 为了研究橡胶悬置的刚度特性对汽车过减速带平顺性的影响,建立了包含悬置系统在内的整车13自由度模型。模型中考虑了液压悬置的刚度、阻尼动态特性;橡胶悬置的多级刚度,主簧和撞块间的间隙。利用建立的模型对过减速带时汽车的动态响应进行计算,通过实车试验验证了模型的有效性。分析了橡胶悬置刚度性能参数对过减速带动力总成振动的影响。结果表明:减小主簧和撞块间的间隙,增大主簧和撞块的刚度可抑制过减速带时动力总成的振动。建模与分析方法可以为橡胶悬置前期设计开发提供有效参考。[ 关键词] 动力学模型;悬置系统;平顺性;振动分析悬置系统不仅需要支撑汽车动力总成,隔离动力总成产生的振动;也需衰减来自路面的振动冲击以防止动力总成产生过大的位移[1]。液压悬置其自身具有大阻尼特性[2],使得汽车在过减速带时,对发动机的振动有非常好的控制。但是液压悬置价格较高,需要的安装空间较大。常规A级车一般采用发动机侧安装液压悬置,变速箱侧安装橡胶悬置的设计方案。通过合理设计橡胶悬置刚度, 主簧与撞块间隙也能对过减速带时动力总成的振动进行抑制。目前,基于整车系统悬置动态响应分析的内容主要集中在点火、熄火、怠速、加速等工况[3-6]。悬置系统对路面激励的振动控制的相关研究较少。在研究汽车受路面激励的振动特性时,主要精力都集中在悬架或者轮胎的设计和优化上[7-8],关于悬置的研究鲜有报道。本文从汽车过减速带,控制动力总成振动的角度出发,计算了汽车过减速带时的动态响应,并通过试验验证了模型的有效性。研究了橡胶悬置主簧与撞块间的间隙,主簧、撞块的刚度对动力总成振动的影响。本文的建模和分析方法可以为橡胶悬置前期设计开发提供有效参考。汽车在过减速带时,来自路面的激励通过轮胎、悬架、车身、悬置传递到动力总成。为了够描述这条振动传递路径,本文建立了包含轮胎、悬架、车身、悬置在内的整车13 自由度动力学模型,见图1。模型中考虑了包含悬置系统的动力总成6 个自由度(3 个平动、3 个转动)、车身的3 个自由度( 垂向、侧倾和俯仰) 及4 个非簧载质量在垂向的自由度[3]。模型中,动力总成横置,前轮驱动。当模型处于静平衡状态时,分别在动力总成和车身质心处建立坐标系Op-XpYpZp 和Ob-XbYbZb,方向参考整车坐标系。通过牛顿第二定律或者拉格朗日方程可以推导出整车13 自由度的振动方程[6]。图2 所示是典型的橡胶悬置静态刚度曲线。为了同时满足悬置限制动力总成位移,衰减动力总成振动的设计要求,悬置的刚度往往设计成多段线性,通过增加撞块来实现刚度的改变。当动力总成安装在悬置系统上,在其自身的重力作用下,悬置会有一定的压缩量,并处于静平衡位置。为了保证在静平衡位置时,悬置弹性中心点与上方撞块间的间隙不至于过大,在设计时,会给悬置Z 向上施加一定的预压量(2~5 mm)。橡胶自身存在一定的弹性特性,悬置在不同刚度段间存在过渡段。对于过渡段的刚度特性,以往文献一般都采用分段线性的方法进行拟合。本文为了建立更精确的悬置模型,引入双曲正切函数来表征悬置过渡段的刚度特性[9]。双曲正切函数表达式
式中:σ ——平顺因子,决定了曲线的平滑程度。引入双曲正切函数之后,悬置产生的支反力Fm 与悬置位移量σ 的函数关系表示为式中:σk,σ-k——正、负向刚度过渡平顺因子;k1——线性段刚度;k2p,k2n——正、负向非线性段刚度;Φp,Φn——正、负向主簧与撞块间的间隙;η——悬置预压量。液压悬置的刚度和阻尼在频域内具有非线性特性,为了能够在时域中进行液压悬置动态响应计算,通过液压悬置悬上悬下的支反力作为模型输入进行计算[10]。在仿真计算时,首先通过悬上悬下的位移、速度、加速度计算得到液压悬置悬上、悬下的动反力,通过动反力计算得到下一步悬上悬下的位移、速度、加速度;如此反复迭代进行计算。实际中减速带的尺寸见图3(a)。标准减速带的宽度为300 mm,高度为50 mm,呈弧形。为了方便计算,将减速带截面简化成一个等腰三角形(见图3(b))。并假设在过减速带时轮胎始终与减速带贴合。在汽车过减速带时,给轮胎施加50 mm 的z 向位移激励。具体的激励加载方法见图3(c)和式(3)。从式(3)可以看出,本文采用的是分段函数的方法对激励进行加载。将橡胶悬置的刚度模型、液压悬置的动反力模型以及轮胎的位移激励模型带入整车振动方程中进行动态响应计算。模型中车身、动力总成、悬架、轮胎的相关参数参考文献[8]。发动机侧采用液压悬置,存在预压,变速箱侧采用橡胶悬置不存在预压。2 个悬置的参数见表1。悬置橡胶刚度动静比为1.4。模拟汽车以20 km/h 的速度过减速带。计算得到的动力总成及悬置系统的动态响应结果见图4—图7。从图4、图5 中可以看出,在汽车过减速带时,动力总成产生了明显振动。振动主要频率为11 Hz,与包含悬置系统的动力总成Z 向固有频率一致。振动加速度并不呈现单一的正弦波动形式,在前几个周期出现明显尖峰,说明在悬置位移增大,主簧与撞块碰撞;刚度产生了突变,导致加速度突然增大。过减速带时,发动和变速箱的悬上振动加速度,以及悬置的动反力见图6、图7。发动悬置由于有4 mm 的预压,安装上发动机后主簧与上方撞块间隙仅为1 mm,振动加速度得到了很好的抑制。加速度正向峰值仅为10 m/s2。而变速箱悬置没有预压,加速度正向峰值达到了45 m/s2。预压对抑制动力总成的振动效果明显。在过减速带时,发动侧承受的冲击较大,产生的动反力较大。但是发动机侧安装了液压悬置,动反力的衰减速度更快。在汽车过减速带时,悬置主要是要尽可能将来自地面的振动衰减,抑制动力总成振动。动力总成的振动加速度无法直接测量,因此,在发动机侧悬置和变速箱侧悬置悬上安装加速度传感器,测量过减速带时悬上的振动来评价悬置隔振性能。试验测试得到的悬上振动加速度与仿真对比结果见图8、图9。试验测试的数据经过30 Hz低通滤波处理。从图中可以看出,仿真结果与试验结果一致性较好,振动加速度出现峰值的频率、峰值的幅值都有很好的一致性。本文建立的模型的有效性得到了验证。发动机悬置有4 mm 的预压,有效控制了发动机悬上振动加速度。根据上一节的分析,悬置的刚度、阻尼、主簧与撞块的间隙等参数对过减速带时动力总成的振动有一定的影响。相对于悬架、衬套、轮胎等底盘部件,悬置的性能参数调整较为容易;根据本文已经建立的整车模型分析悬置设计参数对动力总成振动的影响。本模型中发动机侧悬置已经为大阻尼液压悬置并存在4 mm 预压,这些设计都可以有效抑制动力总成振动,本文将研究重点放在变速箱悬置参数的设计上。在悬置刚度特性设计中,主簧与撞块间需要留有一定的间隙。保证在怠速和高挡位WOT 工况下悬置系统能够有良好的隔振能力。而在加速、减速、点火、熄火等大扭矩工况,悬置系统通过撞块来限制动力总成位移。从图2 中可以看出,预压量的调整实际就是在改变安装状态下悬置主簧与撞块间的间隙。因此,将这两个参数合并分析,统一以悬置主簧与撞块间隙作为研究对象。由图10 可见,与原始状态相比(变速箱侧悬置主簧与撞块之间的间隙为3 mm),将间隙增大至5 mm 时,变速箱悬上振动加速度明显增大,峰值达到了80 m/s2,与原值状态相比增加了近90%。受到来自路面的冲击时,较大的间隙会让动力总成振动幅值明显加剧,悬置很难抑制动力总成的振动。将间隙减小到1 mm 时,振动峰值仅为34 m/s2,与原值状态相比降低了36%。同时,由于间隙减小,动力总成在刚度线性段和非线性段间来回振动,振动频率增加,但是振动衰减速度加快。悬置主簧的刚度直接决定了动力总成刚体模态频率分布以及解耦率的大小[2],合理的频率分布可以避免发动怠速共振,各阶模态振动耦合;良好的解耦率可以让6 个方向的振动更加独立、可控。由图11 可见,将主簧刚度降低至原来的一半后,变速箱悬上加速度峰值增加了一倍。低主簧刚度直接导致动力总成受到冲击时动力总成产生的加速度较大,与撞块接触时冲量较大,直接导致振动加速度变大。而当主簧刚度增加至原来的2 倍后,大刚度主簧有效控制了动力总成的振动。增大主簧刚度可以降低变速箱悬上振动。悬置撞块的设计主要是为了在大冲击工况下限制动力总成的位移。撞块刚度大,动力总成位移限制好,刚度小,在主簧与撞块接触时,刚度突变小,产生的应力较小。主簧与撞块间间隙分别为3 mm 和0.5 mm 时,撞块刚度对变速箱悬置悬上振动加速度的影响见图12、图13。有较大间隙的情况下,主簧与撞块接触时,产生的冲量较小,间隙为3 mm 时,改变撞块刚度对变速箱悬上振动加速度影响不大。而当间隙减小到0.5 mm 后,主簧与撞块接触时加速度较大,产生冲量也变大,大刚度撞块可以有效控制动力总成振动加速度。当撞块刚度增大为原来2 倍时,振动峰值降低了40%,但是小间隙也带来了主簧与撞块的频繁撞击,振动频率明显增大。(1)本文以汽车过减速带,悬置系统对抑制动力总成振动为研究目标,建立了整车13 自由度模型。模型中考虑了液压悬置的刚度阻尼频变特性,橡胶悬置刚度非线性特性以及主簧与撞块间隙。计算了动力总成以及悬置在汽车过减速带时的振动响应;动力总成的振动频率主要成分与其自身Z 向模态一致。(2) 进行了实车过减速带的试验。测试得到了发动机侧和变速箱侧悬置悬上的振动加速度。对比了仿真与试验测试的结果,两者有较好的一致性,验证了模型的有效性。(3) 基于建立的模型,分析了变速箱悬置主簧与撞块间的间隙,各段刚度对动力总成振动的影响。分析结果表明:在保证怠速和高挡位WOT 工况下悬置隔振性能;动力总成刚体模态频率分布和解耦率以及悬置本身疲劳耐久在能够符合设计原则的基础上,尽量减小主簧和撞块间的间隙,增大主簧刚度可以减小过减速带时动力总成的振动;当主簧和撞块间的间隙较小时,增大撞块刚度可以减小过减速带时动力总成的振动。作者单位:( 201804 上海市 上海汽车集团股份有限公司 技术中心)
往期相关推荐
相关文章,在仿真秀官网搜索:
基于HyperWorks/MotionView轮毂电机驱动电动汽车的平顺性分析
动力吸振器在CVT车型LockUp时的方向盘振动控制中的应用
免责声明:分享此文仅为传播汽车NVH相关知识,其版权归原作者所有,感谢原作者的辛苦付出;若有侵权异议等请跟我们联系协商或删除,谢谢!
著作权归作者所有,欢迎分享,未经许可,不得转载
首次发布时间:2023-04-22
最近编辑:1年前
作者推荐
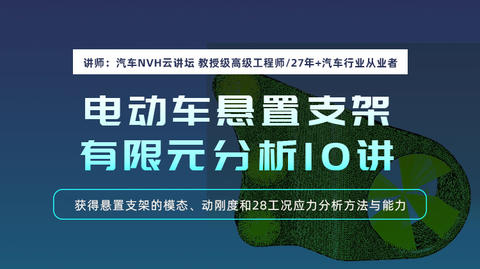