某PHEV车型加速异响问题研究及轴承设计优化
摘要:某插电式混合动力汽车(Plug—in Hy晡d Electric Vehicle,PHEV)在加速工况出现异响,采用噪声、振动与声振粗糙度(Noise、vibration、Harshness,NvH)技术测试,并进行工况分析及轴承设计校核,确定了主轴承异常磨损与加速异响具有关联性。综合相关影响因素,提出了主轴承优化设计方案:在原方案主轴承内表面涂覆树脂涂层,提高其耐磨性能。经起停耐久试验和NvH测试,证实加速异响得到有效解决。本文技术成果对PHEv轴承设计工作具有参考意义。关键词:插电式混合动力汽车;加速异响;轴承;异常磨损;树脂涂层基于对燃油经济性和环保节能要求的不断提高,混合动力汽车技术快速发展。相比于传统的内燃机汽车和常规混合动力汽车,插电式混合动力汽车(Plug—in Hybrid Electric Vehicle,PHEV)通过控制策略对不同工况下的动力输出进行匹配,其燃油经济性得到进一步提高,且低噪声、低排放。轴承的工作性能对内燃机的可靠性、使用寿命等均有影响,是内燃机中的主要零件之一。PHEV车型起动频繁,轴承的耐磨性能面临更严峻的挑战。为了保证轴承工作可靠、耐久,需要持续改进轴承合金材料、制造工艺和轴承的设计方法[2]。当装配、运转和润滑条件都满足时,轴承寿命主要取决于它的抗疲劳性、表面作用力、抗腐蚀性和耐磨特性[3|。目前汽油机用轴承多采用内表面涂覆减摩树脂涂层或内表面加工波纹,提高轴承储油能力,直接或间接提高轴承的耐磨性能。本文介绍了某PHEV车型加速异响问题的分析过程。并从解决问题的角度出发提出了轴承的设计优化方案,进行了优化方案的起停耐久试验和NVH测试证。某PHEV车型运行6.6万km时.怠速工况出现“铛铛”声,加速工况异响更为明显。出现“咚咚”声,驾驶人员在车舱内外均能听到异响。通过噪声、振动与声振粗糙度(Noise、Vibra—tion、Harshness,NVH)技术测得发动机在怠速充电、定值加速工况存在O.5阶次异响,异响频段为200~500Hz,如图1所示。初步分析为轴承间隙过大导致发动机异响。拆机后发现发动机l缸上主轴承出现局部接触磨损,磨损区域在承载区域约1400,磨损量70μm;2缸上主轴承局部磨损量22μm;l缸下主轴承局部磨损量4μm;4缸下主轴承局部磨损量5μm;上主轴承整体磨损呈“喇叭口”型。如图2和图3所示。故障机更换新主轴承后进行NVH测试.异响频段特征消失。更换原磨损轴承复测异响频段复现,仍为200~500Hz。当轴承间隙增大时,油膜压力和轴心轨迹将发生较大的变化.会促使机体振动加剧,噪声增大。当轴承间隙增大30¨m时,发动机噪声会增大3dB[4]。为进行轴承异常磨损分析.按照图4所示的鱼骨图的逻辑进行系统排查。
2.2.1 应用工况排查在城市工况下,低速高里程行驶,车辆长期处于亏电工况时,因电池的荷电状态(State OfCharge,SOC)电量较低,车辆会频繁起动发动机进行充电。在红绿灯停车后起步.行驶中刹车或滑行减速后再加油门等工况中,车辆也会频繁起停发动机,如表1所示。发动机起动时轴承处于干摩擦或边界润滑状态,基于用户实际使用工况,频繁起停大幅增加了轴承的磨损风险。通过某市区实车起停次数测试,在低电量、较拥堵的城市工况行驶过程中.平均起停次数为3.6次/公里,如表2所示。起停频繁,导致轴承出现干摩擦或边界润滑状态的频率增大.是此次轴承异常磨损的主要原因。发动机起动时,曲轴前端受到正时皮带拉力F1和水泵皮带拉力F2的双重作用,二者的合成效果为指向发动机右上方的偏载力,如图5所示,其方向与轴承磨损位置吻合,如图6所示。此发动机亦有传统机型(无PHEV电机),发动机前端布置无差异,传统机型前端也受到同样方向、大小的偏载力,未出现上主轴承异常磨损问题。故发动机前端皮带偏载力并非此次轴承失效的主要原因。该PHEV车型发动机起动方式为电机后端拖拽起动。在0.2~0.4s内将发动机转速拖至1000r/min,同时点火系统完成点火动作。在拖拽起动过程中,发动机主油道机油压力建立情况如图7。转速升至1000r/min以后.0.15s内可建立满足中低速工况所需的机油压力。曲轴轴颈与轴承间可形成良好的润滑油膜。图7显示发动机起动过程的0.35—0.55s内,机油压力较低导致供油量不足,轴颈与轴承间的润滑油膜无法 正常建立。但发动机在生产装配时,会在轴承和轴颈问滴加少量润滑油,这将对摩擦副的润滑状态起到很大作用,此时轴颈和轴承处于混合润滑状态。在滑动轴承流体动力润滑分析中.通常认为轴颈轴线与轴承孑L中心线平行。但由于曲轴前端皮带偏载力作用,实际滑动轴承工作时轴颈在轴承孔中处于倾斜状态,如图8所示。此时。轴承的实际间隙形状发生变化,沿轴线方向的油膜厚度大小不一,油膜厚度较小的位置出现在轴承端部,其润滑状态相对较差[5]。考虑到轴颈倾斜以及油膜压力作用下轴承孑L表面产生的弹性变形影响(轴颈表面硬度远大于轴承孑L内表面硬度.故不考虑轴颈表面的弹性变形),此时的油膜厚度方程为式中,c为半径间隙;z为水平方向坐标,同时垂直于铅垂方向和轴承孑L轴线方向,向右为正:z为铅垂方向坐标,向上为正;p为以z轴为基准的角坐标:6为轴承孑L表面各位置在油膜压力作用下产生弹性变形而引起的油膜厚度变化值(采用变形矩阵方法,有限元分析可求得,此处不作详当轴颈在轴承孑L中倾斜时。轴承的油膜厚度分布情况发生变化,随着轴颈倾斜角度变化,最小油膜厚度^椭的区域分布在与偏载方向同向的轴承端部,且随着轴颈倾斜角的增大,^曲明显减小。如图9所示。发动机起动时曲轴前端倾斜,上主轴承局部位置油膜厚度较小,且PHEv车型起停频繁,导致发动机前端的上主轴承多次处于干摩擦或边界润滑状态,发生异常磨损,如图10所示。磨损区域位于与偏载方向同侧的轴承端部。经检查,轴承装配、主轴承盖螺栓拧紧/拆卸力矩、轴承尺寸公差、曲轴轴颈尺寸公差、缸体主轴承孑L尺寸公差、机油温度、机油压力、机油稀释率等关键参数均在技术要求范围内。未见异常。轴承、凸轮轴衬套、缸体气缸孔内壁、活塞裙部及活塞销座孔未见明显划痕,可排除整机运行工况异常和清洁度不良导致轴承异常磨损。轴承结构和尺寸为常规设计。其中,关键的技术参数,如轴承间隙、轴承背压、轴承内表面粗糙度、直线度及轴承材料承载性能等均满足该发动机使用要求,故结构设计无问题。同时轴承无质量不良问题。根据轴承耐磨性能试验结果可知,增加涂层后的轴承耐磨性能大幅提升.同种测试条件下磨损量降低60%,如图11所示。无涂层轴承与涂层轴承材料结构如图12所示。图12(b)所展示的涂层多为固体润滑耐磨涂层,其成分一般包括树脂、MOS2等无机非金属材料。该涂层的特点为耐磨性能好,引涂层本身含有固体润滑剂,故其具备更好的摩擦顺应性。结合发动机相关轴承材料耐磨性能试验结果分析,可增加涂层来降低轴承磨损量。通过排查分析,确定轴承异常磨损的根本原因为以下两点。(1)发动机起动时,1缸上主轴承在皮带偏载力的作用下局部润滑油膜较小,PHEV车型高频率的起停工况导致磨损风险较高。(2)无涂层主轴承耐磨性能不满足当前PHEV车型实际要求。PHEV车型的低油耗特点主要体现在对驱动形式的控制策略。电子控制单元(Electronic Controlunit,ECu)根据不同的使用工况对发动机和电机的输出比率进行实时调配.频繁起停问题无法从根本上规避。轴承内表面涂覆树脂涂层可提高其润滑性能.降低轴承磨损量。由此确定优化方案为:在发动机1缸上主轴承内表面涂覆树脂涂层,保证发动机起动时,油膜虽未完全建立,轴承仍具有一定的润滑性能,避免主轴承异常磨损。基于PHEV车型路谱采集数据,考虑极端使用情况,如出租、滴滴、商务营运等,数据采集结果详见表4,策划台架起停耐久试验,参考图13。(1)18万次,28万次,36.5万次,48万次起停工况各测点振动加速度幅值(RSs)无明显差异,怠速充电工况无明显异常,结果如图14所示。(2)18万次,28万次升速工况各测点振动RSs值无明显差异;36.5万次,48万次较初始状态,振动RSS值增大0.59左右,升速工况无明显异常。如图15和图16所示。NVH测试结果显示,实施优化方案后,在起停试验中未出现异响问题,有效地解决了当前故障。优化方案的发动机经起停耐久试验后.发动机1缸上主轴承最大磨损量为16斗m,2缸上主轴承最大磨损量为10“m。相比于原方案,l缸上主轴承磨损量降低77%,2缸上主轴承磨损量降低55%,如图17一图19所示。试验结果表明优化方案有效地解决了轴承异常磨损问题。本文对PHEV车型加速工况异响进行了排查和分析,优化了设计方案,经验证,异响问题得到有效解决,结论如下。(1)PHEV车型发动机起停工况频繁,主轴承磨损风险较大,磨损量高达70“m。(2)主轴承磨损导致轴承间隙增加,其值大于临界值时,将引起NVH问题,如异响、振动等。(3)通过轴承内表面涂覆树脂涂层,提高其耐磨性能,降低轴承磨损量,可有效解决由主轴承异常磨损导致的发动机异响。作者:郭吉东。王欣欣。甄洪梅,张伟,宋元强,葛双亮,顾锋作者单位:(宁波吉利罗佑发动机零部件有限公司,浙江宁波315336)
往期相关推荐
相关文章,在仿真秀官网搜索:
基于传递路径分析对某SUV加速轰鸣声问题诊断与优化
免责声明:分享此文仅为传播汽车NVH相关知识,其版权归原作者所有,感谢原作者的辛苦付出;若有侵权异议等请跟我们联系协商或删除,谢谢! 著作权归作者所有,欢迎分享,未经许可,不得转载
首次发布时间:2023-04-22
最近编辑:1年前
作者推荐
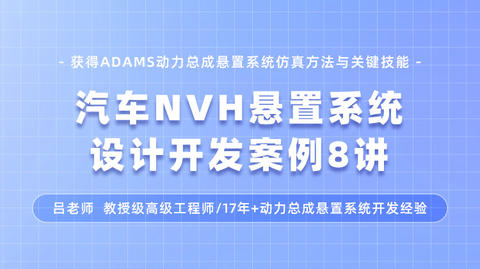