新能源驱动电机NVH开发研究
摘 要:本文介绍了新能源驱动电机行业发展现状,详细论述了目前行业内主流电机:永磁同步电机的结构、工作原理和噪声机理,对引起永磁同步电机电磁噪声的转矩波动和径向力波产生机理进行了详细阐述,介绍了扁线电机的 NVH 性能优势,建立了永磁同步电机的 NVH 开发流程和永磁同步电机噪声仿真流程,为驱动电机的NVH 开发提供了方向。驱动电机是新能源车辆和混合动力车辆的核心动力源,基于电磁感应效应,驱动电机将整车提供的电能转化为机械能,驱动整车 行 驶。按照输入的电流划分,可 将 驱动电机分为直流电机和交流电机两种形式。当 前 主 流 的驱动电机为交流电机,将 交 流 电 输 送 给 定 子(通 常 是 硅 钢片搭配铜线 圈,固 定 不 动),产 生 旋 转 磁 场,转 子(由 电 磁铁、永磁体或 硅 钢 片 制 成)受旋转磁场影响,形 成 旋 转 力矩。根据转子与定子的转速一致性划分,又可将交流电机区分为同步电机和异步电机。当前的新能源市场主流驱动电机主要为永磁同步电机和鼠笼式异步感应电机,其中永磁同步电机占国内造车势力中电机比重的绝对主流份额。驱动电机的主要零部件一般包括:转 子、定 子、线 束、壳体、端盖等,其中按价值含量高低依次是定子、绕 组、轴承、转子,成本占比分别为 19%、17%、12%、11%。以 驱动电机总成为下游划分,则 定 子 铁 芯、转 子 铁 芯、定 子 绕组、轴承、端盖等零部 件 为 中 游,铜 线、铝 合 金、硅 钢 片、永磁体等原材料为上 游。上游原材料的供应商多为大型金属材料供应商,包括生产永磁体的正海磁材、金力永磁等;中游生产定子、转子、轴承的供应商多为小型非上市公司,以组装为主;下游生产电机总成的企业主要为三类,分 别为整车厂包括比亚迪、特斯拉等,电机厂包括方正电机、精进电 动 等,传统整车零部件供应商包括博世、大 陆、麦 克纳等。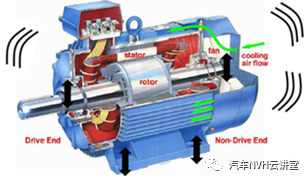
新能源汽车驱动电机是工业电机的一种,鉴于车载工况的特殊环境,新能源汽车驱动电机与传统工业电机在性能方面的特殊差异主要体现在起动转矩大、功 率 密 度 高、调速范围宽、散热需求强、高效区间广、NVH 性能优秀。1)起动转矩大:新能源汽车更强调起步响应、百 公 里加速等性能指标,新能源汽车的驱动电机在起动或低速时要求更高扭矩,将汽车速度以最短的时间提升至期望值。2)功率密度高:车载驱动电机有严格的重量要求、体积要求和功率要求。电机的重量和尺寸直接影响汽车的动力性能和布置空间,电机设计的方向与难点在于尽可能提高功率重量密度和功率体积密度。3)调速范围宽:驱动电机广阔的调速范围可以使新能源汽车省掉传统多挡变速箱,只使用固定档的齿轮组,即可实现宽阔的调速范围,并有效降低成本。4)散热需求强:由于新能源汽车驱动电机的功率密度高,散热问题随 之 而 来。1台150KW 的传统动力系统总成,体积大概在409L,而相同峰值功率的电动汽车动力系统总成,体积可做 到82L,只有传统动力总成的20%。小体积、高功率的设计可带来散热、机 械 振 动、电 磁 兼 容、NVH 啸叫等问题。电机的能量转换效率在90%以 上,峰值效率约在95%,平均能量损耗约占10%,且这10%的能量损耗多以发热的形式体现,因此驱动电机的散热需求较强。5)高效区间广:新 能 源 汽 车,尤其是纯电动汽车由车载电池包供电,电机效率直接影响续航里程,因 此 对 于 电机的效率要求很高。新能源汽车的驱动电机需要拥有尽可能广的高效率运行区间,正常城市路况下汽车不会频繁起动,也不会持续超高 速 运 行,更多的是在匀速行驶中进行加速超车或减速制动动作,因此中间部分的运行效率尤其重要。6)NVH 性 能 优 秀:与传统工业电机相比,由 于 客 户的挑剔性,新能源车用驱动电机需具备更优秀的 NVH 性能。各生产厂家和主机厂花费巨额的人力与财力用于优化电机噪声,目前驱动电机的 NVH 开发已经成熟。最常见的三种交流电机是永磁同步电机、感应异步电机和同步磁阻电机。交流电机的定子基本相同,主要区别在转子。定子主要由铁 心、线 圈 组 成,定子铁心由硅钢片叠压而成;漆包线绕制成线圈,嵌入铁心槽内,再进行绝缘处理;将绝缘处理后的铁心套入机壳得到定子。定子绕组接入交流电源(通常是三相交流电,三相交流电与空间角度120°的线圈相结合,形成的合成磁场就像是一个强度均匀的磁场在旋转),形 成 旋 转 磁 场,旋转磁场拉动转子旋转。永磁同步电机的转子由铁心、磁钢、轴压装而成,磁钢提供电机磁通,由稀土钕铁硼经粉末冶金法制成,对 电 机性能影响最大。永磁同步电机的转子转速与定子磁场的转速,即交流电频率保持同步。定子绕组接通交流电,产 生 旋 转 磁 场,转子永磁体磁场受定子旋转磁场感应而跟着旋转,进而输出动力。永磁同步电机 的 优 势 在 于,功 率 密 度 高、运 行 效率高、转矩大且平顺、结构简洁紧凑、调速性能好。永磁同步电机的优势在于,功率密度高、运行效率高、转矩大且平顺、结构简洁紧凑、调速性能好。1)功率密度高:永磁同步电机的钕铁硼磁性材料具备优秀的磁力性能,在充磁后不用继续增加外部能量,即 可构建较强的永恒磁场,无 需 额 外 电 路 进 行 励 磁(即 给 导 体通电产生磁场)。在额 定 功 率 下,相同绝缘材料和散热条件的永磁同步电机的功率密度比感应异 步电机大 2 倍以上。2)运行效率高:由于转子使用永磁体,永 磁 同 步 电 机的转子通常无需通电励磁,可减少相关的能量损耗,效 率较高。3)转矩大且平顺:在额定电流范围内,提 高 电 流 即 可快速提高电机扭矩。此外,三相交流电在定子中形成的旋转磁场也较为稳定,使电机输出转矩脉动较小,尤 其 在 低速大转矩工况下(对应整车起步加速阶段),永磁同步电机相较于异步感应电机拥有突出优势。4)调速性能好:永磁同步电机的电、磁和力的三者关系相较于感应异步电机更加简单,更易于调速和控制。异步电机的状态方程是四阶的,转子与定子的方程耦合(转子内的电流是由定子磁场旋转感应产生);永 磁 同 步 电 机的状态方程是二阶的,永磁体的磁场是独立存在的,其 调速性能控制难度低于感应异步电机。5)结构简洁紧凑:永磁同步驱动电机无需设置励磁电源结构和励磁绕组结构,降低了结构复杂性,电 机 结 构 较为紧密,保证了电机运转更加具有可靠性。永磁同步电机噪声包括电机控制器噪声、电机电磁噪声、机械噪声、电池冷却噪声等,主要由电机电磁噪声和机械噪声组成。其中机械噪声包括:轴承噪声、减速器啸叫、转子偏心等,主要由机械件工作产生。电机电磁噪声主要由转矩波动(齿槽转 矩、纹 波 转 矩、时 间 谐 波 等)和 径 向 力波(定转子基波、定转子高阶谐波、电机控制器引入开关频率边频、时间谐波等)作用在电机壳体上,激励电机壳体模态响应,引起共振产生。图1为电磁噪声机理图。电磁噪声是驱动电机独有的、也是最重要的噪声。气隙中的磁场使得磁密度发生变化,产生了交变电磁力,交变电磁力作用在定子齿槽上,产 生 电 磁 力(径 向 力 和 切 向力),电磁力是与时间相关的交变力,取决于气隙形状、齿槽形状等。径向磁感应强度大于切向磁感应强度,径向电磁力不产生电磁力矩,径向力大于切向力。切向电磁力产生扭矩驱动转子旋转,主要作用是维持交变磁场的建立,径向力波激 励 定 子 结 构,定子结构振动从而产生辐射噪声,尤其径向力电磁力波的频率与定子结构模态一致时,辐射噪声非常明显,电磁力产生的噪声是高频啸叫声,人耳较容易识别到。齿槽转矩是永磁电机特有的问题之一,档永磁电机定子绕组不通电时,永磁体磁场与定子开槽磁阻相互作用产生的转矩,是由永磁体与定子之间相互的切向分力引起。无供电的永磁电动机的转子和定子有自行调整至磁阻最小位置的趋势,从而产生的周期性转矩。齿槽转矩与电枢电流无关,是定转子相对位置的函数,与电机本体设计特性有关(如极槽配合齿槽和磁极的结构尺寸等)。齿槽转矩会引起永磁电机的转矩脉动,进而导致速度波动,使电机产生振动和噪声,尤其脉动转矩的频率与电枢电流谐振频率一致时,会产生共振,势必会放大齿槽转矩的振动和噪声。纹波转矩是永磁电机负载时,定子磁动势和转子电磁特性相互作用产生的扭矩。当定子和转子有相同的谐波感应强度时产生的纹波扭矩,纹波扭矩与谐波阶次成正比,因此,高次谐波的纹波扭矩更大。使用转子斜槽,形成的电磁转矩和感应电动势近似于同一根转子导条均匀分布在一段圆周范围内的平均值,能有效的削弱齿谐波磁场所产生的谐波电动势,从而削弱由这些谐波磁场引起的附加转矩,降低电磁振动和噪声。转子斜槽后虽然也会使转子感应的基波电动势减少,但一般选择的斜槽度相对于极距来说小得多,因而对电机基本性能影响很小,故中小型铸铝转子异步电动机普遍采用转子斜槽。新能源汽车驱动电机在性能方面的特殊需求主要体现在功率密度高、高效 区 间 广、调 速 范 围 宽、起 动 转 矩 大、散热需求强等。因此,新能源汽车驱动电机的发展趋势也将围绕这些性能展开,当前比较主流的几个方向即扁线电机、油冷电机以及多合一电驱动总成。扁线电机拥有更高的功率密度,扁铜线之间间隙较大,冷却油易于渗透,扁线电机的发展推动了直接油冷技术的应用。同时,冷却油拥有良好的绝 缘 性,可作为减速器及齿轮轴承的润滑油使用,也可收集电机余热用于电池包的保温,直 接 油 冷 技 术加速了整车热管理系统集成化的进程,对多合一电驱动系统总成的发展又起到促进作用。扁线电机是指,将定子绕组中的传统圆柱形漆包铜线替换为加工成发卡状的漆包铜扁线。圆线电机的定子绕组横截面中,圆形铜线 间 留 下 了 大 量 间 隙,而 扁 线 电 机 的定子绕组横截面中,矩形铜线可以更好地填充空间,提 高槽满率,这是扁线电机和圆线电机的本质区别。与圆线电机相比,扁线电机的首要优势即损耗降低、效率提升。永磁同步电 机 的 损 耗 中,铜 耗(主 要 是 定 子 绕组中的损耗)占 比 大 约 为65%,铁 耗(定子铁芯与转子铁芯中的损耗)占 比 大 约 为20%,其余损耗占比相对较低。扁线电机和圆线电机的铁耗水平相当,主要差在于铜耗。铜耗具体可分为直流损耗和交流损 耗。圆 线 电 机 和扁线电机都有直流损耗,在电流相数和电流有效值给定的情况下,直流损耗与绕组的直流电阻成正比。由 于 圆线更细,电阻更高,因此圆线电机的直流损耗通常高于相同条件下的扁线电机。由于圆线绕组的单个绕组截面尺寸较小,交流损耗可以忽略不计,而扁线绕组由于截面尺寸较 大,受趋肤效应和邻近效应影响,交 流 损 耗 相 对较大。除提高效率、降低损耗外,采用扁线电机 与 圆 线 电 机相比具有更大面积的高效区间、更高的功率密度、更 强 的散热能力 和 更 优 秀 的 NVH 性 能。从 源 头 分 析,相 同 功率、更低铜损和铁 损 大 幅 降 低,高 更 的 效 率,也 意 味 着 更低的各个阶次径向力幅值,间 接 带 来 整 体 NVH 主 要 径向力的全面降低;扁线电机需要从槽口嵌线,直接 通 过 铁芯端部插电即可,意味着更小的槽口设计,即更小 的 齿 槽转矩;更高的定子 刚 度:扁线电机绕组刚度更高,也 即 提高整体尤其是定子刚度,同样的径向力波,壳体表 现 出 来的振动幅值越小,同样辐射噪声也越小。新能源汽车对续航里程、功 率 密 度、能量利用效率的要求越来越高,电驱动 系 统 逐 渐 向 集 成 化、小 型 化 和 轻 量化的方向发展。目前已经发布的多合一电驱动系统包括三合一、四合一、六合一、七合一甚至八合一电驱系统,其中最常见的还是三合一电驱动系统。电 驱 动 系 统“多 合一”的集成化方案可以共享电路及功率半导体,减 少 线 缆用量,有效缩小电驱动系统的体积和重量,提高功率密度,实现轻 量 化。对 电 机 总 成 的 NVH 控 制 起 到 更 有 效 的作用。一般电机 NVH 开发流程共包括八个部分,见 图 2。分别为:设计 需 求、拓 扑 设 计、电 磁 设 计、仿 真 分 析、A 样机、整改优化、B样机、整车匹配。1)在设计需求阶段,根据性 能 需 求,对 标 竞 品,确定电机性能参 数 和NVH 性能指标。2)拓扑设计阶段确认电机类 型、转 子 结 构、长径比、槽数等结构及其对NVH 的影响。3)电磁设计阶段设计电机几 何 尺 寸 以 及 极 槽 配合、绕组、材料选型及其对NVH 影 响,齿 槽 转 矩 分析等。4)仿真分析阶段包括电磁仿 真、结 构 仿 真、多 物理场 仿 真、平 衡 其 他 性 能指标,见图3。5)A 样机阶段进行样机台架 NVH 测试、校验 仿 真 结果、结构模态测试、噪声源识别测试。6)整改优化阶段进行电磁方案优化、结 构 方 案 优 化、性能平衡、最优方案选择。7)B样机阶段对优化后样机进行台架 NVH 验 收、装车 NVH 验证、达成单体目标等。8)整车匹配阶段进行整车试验验证、悬 置 设 计、声 学包开发、目标达成确认等。本文介绍了新能源驱动电机行业发展现状,详细论述了目前行业内主流电机:永磁同步电机的结构、工 作 原 理和噪声机理,对引起永磁同步电机电磁噪声的转矩波动和径向力波产生机理进行了详细阐述,介绍了扁线电机的NVH 性能优势,建立了永磁同步电机的 NVH 开 发 流 程和永磁同步电机噪声仿真流程,为驱动电机的 NVH 开发提供了方向。作者单位:(中国汽车技术研究中心有限公司,天津 300300)
免责声明:分享此文仅为传播汽车NVH相关知识,其版权归原作者所有,感谢原作者的辛苦付出;若有侵权异议等请跟我们联系协商或删除,谢谢! 著作权归作者所有,欢迎分享,未经许可,不得转载
首次发布时间:2023-04-22
最近编辑:1年前