基于台架对盘式制动器制动噪声的研究
[摘要]基于惯性试验台架对盘式制动器进行了制动噪声试验,分析对比了盘式制动器在不同工况、不同类型夹具下的制动噪声表现,并分析了制动噪声在时域内的发生过程。还讨论了制动压力、制动初速度、制动盘温度对制动噪声的影响。最后针对研究结果,给出了制动噪声试验程序编制的建议。在汽车技术飞速发展的今天,对汽车的要求不仅仅体现在操作性、稳定性、安全性等上面,消费者越来越关注汽车的舒适性。汽车制动会产生振动、抖动、尖叫,这是影响汽车驾驶的舒适性的重要指标。汽车制动系统越来越受到人们的关注与重视,开发新型“绿色”制动器是科学家面临的一项亟须解决的问题。按照制动噪声发生的频率不同,K. Brent Dunlap[1]等将盘式制动器制动噪声分为 3 类:将频率在 10~1kHz 的噪声称为低频噪声,将频率在 1kHz~5kHz 的噪声称为低频啸叫,将频率>5kHz 的噪声称为高频啸叫。统计中,一般将大于 70dB 的制动声响列为不可接受的制动噪声。国外针对汽车制动噪声的研究早于国内,早在 20 世纪 30 年代,国外学者 Mills[2]通过对鼓式制动器制动噪声的试验研究,得出制动产生噪声的重要机理:摩擦力-相对速度关系的负斜率机理。50 年代,英国学者 Fosberry 与 Holubecki[3]针对盘式制动器做了大量的实验与研究,得出大多数的制动噪声的产生与摩擦系数的减小有关,而和摩擦片的摩擦特性没有必然联系。60 年代,Spurr[4]提出了 Sprag-Slip 理论,即由于摩擦面自锁作用导致整个摩擦系统不平衡,从而引起振动噪声。80 年代以来,研究者们从简单的物理模型转到了对制动器整体结构的研究,进行全面分析。Kusano[5]等通过对鼓式制动器的研究,提出了用模态分析的研究思路来研究制动噪声。国内对汽车制动噪声的研究开始于 20 世纪 80 年代,何瑞发[6]通过对 EQ140 汽车前鼓式制动器制动发啃的研究,得出摩擦片的烧焦变形、包角、支撑角、端头的倒角对制动时的影响。俄延华等[7]通过建立鼓式制动器的力学模型,总结出鼓式制动器的制动尖叫主要是由于摩擦片的耦合作用而引起的高频自激振动,制动尖叫的发生取决于制动系统的运动稳定性。余为高、于学华[8]通过建立盘式制动器的有限元模型,得知制动噪声的产生与摩擦系数有很大关系。吕辉、于德介等[9]基于响应面法,通过拉丁超立方试验方法采样,建立制动系统复模态的二阶响应面近似模型。余卓平、孟德建、张立军[10]采用道路和台架对制动系统进行振动噪声试验,并对两种试验进行了阐述和对比分析。孙国辉、侯俊等[11]通过是否在制动块底板上增加橡胶阻尼层进行制动噪声对比试验,得出制动盘和制动块的耦合特性是影响制动振动和噪声的一重要因素。侯俊、过学迅[12]以振动力学和有限元理论为基础,建立制动器的有限元模型并对其进行有限元分析。董士琦、过学迅[13]利用 ANSYS 对制动系统进行模态分析,把制动盘固有频率与激振频率进行对比,尽量避免产生共振和噪声。目前测量制动噪声方式有整车测量和台架测量两种。整车外部环境比较苛刻,干扰噪声较多。由于整车道路试验受天气、道路状况及驾驶员操作等原因的影响,一些制动问题工况的复现,尤其是对制动噪声问题的复现,有一定的难度。这时候,从时间和成本上考虑,台架就具有一定的优势。台架试验对车速、制动压力、温度、湿度等试验工况控制更加方便精确,更具有目的性和针对性。相对于道路试验,台架试验有独特的优势。本次试验的台架试验设备是 LINK3900 制动惯量试验台(如图 1 所示),由主电机驱动系统(为试验提供驱动力和行驶惯量)、环境模拟系统 ECU(设定和控制制动环境)、标准步入式 NVH 试验仓(提供自由声场测试环境)三大部分组成,该系统主要测试和分析车角式和车桥式制动试件在不同条件下的制动性能及制动振动噪声。可以采集的主要数据有以及相关传感器精度信息如表 1 所示:典型试验章节中制动压力,制动速度和压力控制方式都略有不同。为了更全面的反映实车制动系统使用情况,程序尽量覆盖不同参数的工况信息。几个比较典型工况信息如表 2所示:图 2 表示了拖磨和冷态低速拖磨情况下制动压力分布情况,实际试验中覆盖的压力范围以某一汽车制动器 A 在 LINK3900 试验台上做制动噪声试验,试验中以 SAE J2521 试验标准进行校核,对制动器在不同工况的制动噪声进行采集,分别按照拖磨工况,减速度工况,正反转工况进行试验统计,统计结果如表 3 所示。此制动器在不同工况下,产生噪声次数和频率并不相同。拖磨工况中共产生 7 次噪声,其中 4 次噪声频率为 3000Hz,另外 3 次噪声为 13800Hz。减速度工况共产生了 6 次噪声,噪声频率均为 13800Hz,而正反转工况并没有产生制动噪声。可以说明,不同工况条件下,制动器的噪声不一定被激发。而制动噪声的频域分布又有着频率相似性。制动噪声看起来有随机性,但是一般都是满足特定工况才会发生,所以在制定制动噪声测试规范的时候,要充分考虑车辆行驶的工况。而在做制动噪声分析的时候,要对噪声发生做频率分析,才能进行有效改进。针对汽车制动系统做台架试验时,可根据试验夹具的不同,分为车角式,悬架式和车桥式试验。三种夹具的组成可以参考表 4,后两种类型的夹具可以预先给制动角施加载荷,保证振动传递时悬架部件参与,更接近实车,但成本较高。对于样车 B,我们分别采用车角式和悬架式夹具进行噪声测试。试验中运用的夹具如图试验完毕后,将噪声尖叫声压级和噪声频率统计完毕后,结果如图 4 所示:从图中可以看出,用车角式夹具时,制动噪声主要集中在 7800Hz,9800Hz 和 14300Hz。而同样的零部件在使用车桥式夹具时,噪声主要集中在 2200Hz,3300Hz 和 9800Hz。这说明制动噪声与悬架零部件是有关联性的,不同的夹具类型和悬架形式会导致不同频率噪声的激发。2200Hz 和 3300Hz 的噪声属低频啸叫,产生机理为零部件之间的模态耦合[14],说明夹具不同改变了零部件之间的耦合状态。关于在一次制动过程中,摩擦条件不断在变化,当噪声发生条件满足时,噪声便会发生。这使得研究一次制动过程中噪声发生时间,便有了意义。比如图 5 所示,制动噪声并不是在一开始就产生。随着温度的不断升高,制动器间的摩擦情况发生改变,摩擦材料膨胀,计算摩擦系数变化,温度从 140 上升到 155,制动扭矩不断增加。在温度上升初期,并没有明显的制动噪声发生,当拖磨至 2.7 秒时,扭矩增幅达到 20%的,开始出现大于 70db 的噪声,并在 2.7s 至3.5s 不断出现制动噪声,且有不断增大的趋势。此噪声在频域上表现为 7800Hz。很多噪声都是如此,在一次制动过程中,并不是从始至终都有噪声,需要在制动过程中达到一定条件才会出发,经观察发现,噪声发生在中后期居多。在惯性试验台上对制动系统进行同一工况不同制动压力的制动试验,得到的试验结果如从图中我们可以看出在不同制动压力下,噪声的产生情况是不同的,制动压力在 0-25bar范围是制动噪声的多发区,这说明在较低的制动压力下制动噪声发生倾向性较大。在压力较高时,制动噪声发生的倾向性减少,这与摩擦面和制动盘之间的接触稳定性有关。在制定制动噪声测试规范时,应将更多的章节设置为低压制动。汽车在高速和低速下制动时,产生噪声的频率及大小是不同的。这说明制动初速度对制动噪声也是有影响的。针对这一情况,在相同条件下对不同的车速进行制动试验,其结果如图 7 所示:当车速在 3kph 与 10kph,对汽车进行制动时,制动噪声出现的频次叫高,当车速在高速 50kph 与 80kph 下对汽车进行制动时,汽车制动噪声发生率明显变低。用户用车的角度来讲,一般都是在交通拥堵,路口红绿灯前等低速工况下频发制动噪声问题。而高速工况,用户制动次数较少,一般为紧急制动或者制动初速与制动末速差距不大,与拥堵工况大不相同。在编制噪声测试规范时,应考虑低速工况多一些。图 8 是在不同温度下制动噪声发生概率的分布图,我们可以看出不同温度下的制动,制动噪声发生频次有一定的差异,在 25℃、75℃、125℃、150℃制动时,制动噪声出现的概率较高。制动温度只是一个初始条件,单独考虑并无明显规律。但在制定制动噪声试验规范时,也应尽量覆盖不同温度段,与制动速度和制动强度统一考虑。本文是基于惯性试验台架对盘式制动器进行制动噪声研究,得出了以下结论:1) 不同制动工况下,制动噪声发生的趋势不同,在编制制动噪声试验程序时,应考虑2) 夹具类型不同,制动噪声的表现不同,建议使用更接近实车的悬架类型夹具或全轴3) 在一次制动过程中,制动噪声并不是一直在发生,而是随着制动条件改变才发生,4) 当制动压力较低,制动初始速度较低时,制动噪声发生倾向性更明显。本文研究仍有一定的局限性,以后还要结合不同温湿度的外界环境以及制动器在涉水等作者:周明岳 1,阿比拉涅 2,冯博 1,冯天骥 1
免责声明:分享此文仅为传播汽车NVH相关知识,其版权归原作者所有,感谢原作者的辛苦付出;若有侵权异议等请跟我们联系协商或删除,谢谢! 著作权归作者所有,欢迎分享,未经许可,不得转载
首次发布时间:2023-04-22
最近编辑:1年前
作者推荐
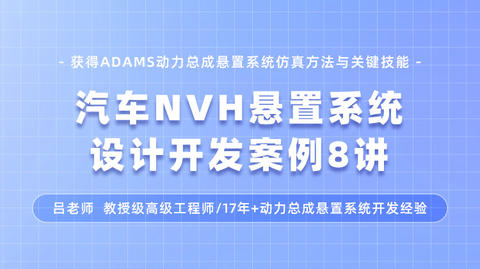