陈继良:电子产品散热设计方法(PPT+视频)
本文内容为陈继良 专家于2022年11月17日在常州 2022能源装备仿真技术峰会 的演讲内容,经陈老师授权,周祺 整理,与各位同行一起学习。今天我非常开心,有这个机会来跟大家分享一下。在内容上介绍的不只是充电桩,可能还有一些涉及到储能的方面。刚才我坐下面听了几位专家汇报自己行业方向的宏观进展、具体产品、核心技术等,非常有收获,感觉不虚此行。第一部分就是能源装备类产品的散热特征。为产品做热管理解决方案,首先显示对该产品做一个定位。比如一块pcb板,它的散热问题就是芯片级的;到了能源产品,它问题的焦点就不是一些芯片而是电池、电芯;再到电池放置在机箱里,或者充电桩整桩的散热问题,就转化成了机箱级问题;最后到对整个电厂、储能厂进行热管理,就达到了环境级。现在我做储能方面的仿真,一直也存在着发热量计算的问题,目前对储能柜这种整机进行仿真,大多数情况是给一个固定的功耗,结果的误差可能会很大。接下来是充电桩的一个拆解。像这类这种类型的产品,它内部的功能模块很多,它需要一个载体,或者说需要一个盒子给它封装起来,要不然很散。在结构设计上,载体封装的形式使整个产品模块化;在热设计上,封装相当于给内部器件创造了一个隔绝外界的环境。就像刚才我提到的一个点,我们在做整机的设计的时候,有很多的发热源,这些热源的发热量和内部结构都很难去精准描述,而这些问题恰恰是热设计的核心问题,或者核心目标。不管是对于充电桩还是储能包它其实都是一个多尺度产品。对于电芯而言,发热量和温度也有关系,同时电芯之间的相互影响也会导致功耗的差异。对于一个整机,往小尺度要关注芯片,往大尺度要关注整个箱与环境的交互,尺度跨度非常大,对于仿真工作带来的难度还是相当大的。当然,仿真工作对于产品前期设计的作用也是很大的。譬如说单个模块的空间排布是符合内部器件的散热需求的,但将它放到机箱里,如果不合理设计模块间的距离、模块的空间位置等等,就可能出现热方面的问题。所以说,热设计的工作,既有挑战,又充满着意义。接下来我介绍一下产品热设计过程中的一些关键性工作。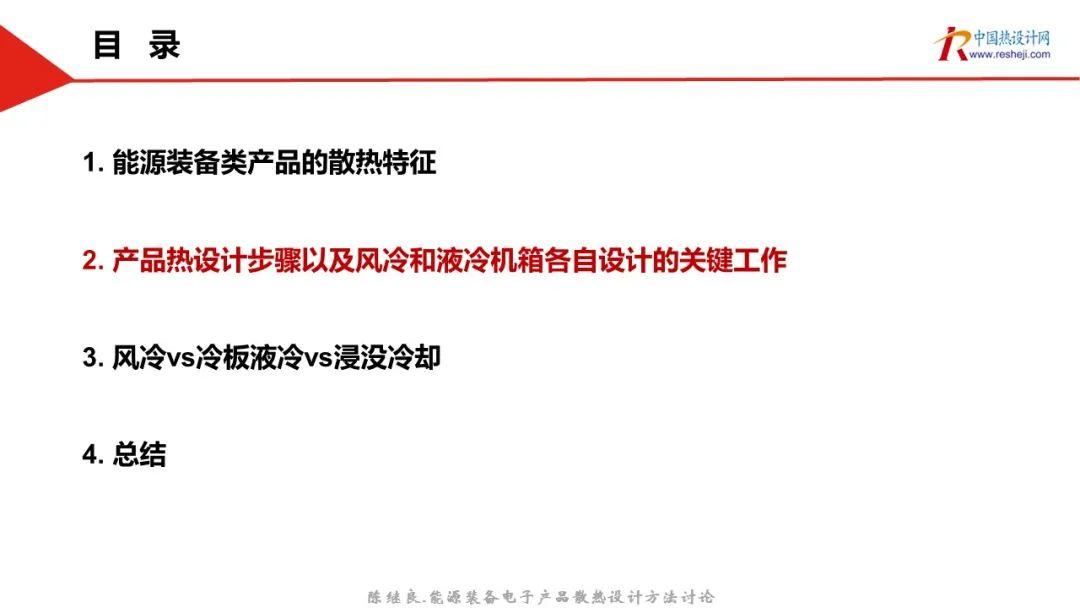
首先是热设计工作大致要经历的一些流程。正常的一款产品的研发阶段,首先要提出一个概念模型,然后通过热仿真找到模型中超温的区域,之后对应提供散热的方案,然后与结构设计进行交互,得出结构上可行的优化方案,最后在优化方案上再进行仿真确认优化的效果。既然产品的研发流程很大一部分依赖于软件,那以后我们通过对软件进一步的开发,能不能实现自动化的设计?首先软件确实很重要,但我觉得更重要的是人。软件永远是在解决框架性的或者说确定性的问题,但真正的设计,需要提出并解决不确定性问题。或者说软件能达到能够处理不确定性的程度,我们现在的技术还达不到。目前对于一款电子产品,主要的散热方式就是自然散热、强迫风冷以及液体冷却。刚才我也提到,对于产品的散热特征要有一个区分。有一些产品可能发热量整体挺大,但实际上它很均散。它全部的发热量都平摊到各个器件,因此每个器件的散热压力都不大。对于芯片而言情况可能完全相反,一个服务器发热量可能也不是很大,但是它的绝大部分热量就集中在芯片,那就需要对芯片进行集中散热。所以散热特征区分对于散热方式选择的意义是很大的。还有一些产品内部的热源分布,这涉及到不同器件之间的互相影响;包括机箱内部与外部的交互模式,这些涉及到箱体内外的换热效率。接下来是液冷的一些设计。液冷技术在服务器里边的应用比较成熟。对于储能包,可能用到风冷的散热比较多,对于充电桩,内部的温度差异会比较大,因为它主要的热源是个别几个,就开关芯片,还有充电枪的部位。对于充电桩,行业内还没有形成一个统一的标准,所以结构设计和热设计之间的融合会更多一些。对于充电桩的散热问题,绝大多数情况是参考它的发热量。发热量较小,采用风冷是成本较低的方式,但发热量高,采用风冷散热会伴随着功耗过高,噪音过大的问题,这种选择就不太合适了。刚才有些专家的汇报中也提到了集中供冷散热,其实这与热设计的理念不谋而合。从过往的其他行业的演进的趋势上来讲,进行散热热控功耗会低一些。进行热设计,不只是单纯地把温度控制低,同时要控制散热系统本身的功耗,这其实也是新能源的一个精神。比如设计一款充电桩或者储能包,它就是为了减碳,为了节能,结果因为热管理系统使它整体效率变低,这属于得不偿失了。这一点是在热设计中值得考量的。我一直做方案设计,我不可能刻意贬低方案设计的价值。现在我有一个体会,就是方案设计很重要,也很困难,尤其是对一些新兴的产品。我设计完一个方案,如何把它实现出来啊?比如说像一个换热器,或者冷却液,现在都是直接选型号,但是如果有一个课题是外国要改进一种冷却液。这个难度是要远超过直接去选择。面对充电桩和储能包的新的使用环境,我们需要设计新的方案。譬如在潮湿的环境下,产品是否需要除湿?这种除湿与散热的互相作用又是怎样的?出现新的问题后,往往就需要新的技术去解决。机器或者说软件,它只能解决一些确定性的问题,而人,在解决不确定性。现在产品开发节奏越来越快,在开发早期,一些热仿真需要的信息往往无法锁定,譬如发热量,寿命曲线。如果你坚持仿真要在这些信息确定的基础上,那你无法进行设计。因为没有你的评估,其他的工程师也无法给你确定性的信息。所以谁能在更不确定性的条件之下出方案谁就是这个项目的主力。充电桩也好,储能设备也好,热管理技术肯定是这个产品的核心技术。一个设备的安全性是非常重要的,尤其是对于储能。其实对于任何系统。热管理系统不只是管控温度,更主要是管控热失控的风险。有时候不光是热设计的问题,还要从结构、控制等多方进行融合。充电桩、储能设备等大型电子产品,产品的迭代速度越来越快,热设计团队的工作量也会越来越大,同时他们工作产出的价值也会随之越来越大。在以后热设计的过程中,会遇到大量新兴的问题,以前也没什么可借鉴的。很多的标准都还没有制定的时候,很多产品的发热量、材料、尺寸都很难去界定。在这样一个阶段,一个热设计的团队,它做的工作就不再是验证性的,就不再只是做个测试或者仿真,它需要大量其它的能力。热设计团队里会包含一些材料、可靠性等其他工程师在里面,去综合地解决一个问题或者辅助产品的设计,这时候热设计会成为公司内比较核心的一个技术团队。刚才我提到不管是充电桩还是储能包,它都是一个多尺度的产品。当我们设计完一个设备,想它要能够完整的运行,其实任何一个环节出问题都会导致整体的崩溃。这里面也涉及到材料的问题,譬如芯片中用来散热的硅脂,一直存在一些不可靠性的问题,它在高温下会出现性能衰竭的问题。其实这种问题已经存在几十年了,始终就没有人解决。包括到了充电桩和储能电站这种设备,管理人员不会天天呆在设备旁边。一旦出问题设备往往无法得到及时的维修。因此这种设备中材料的可靠性越发重要。这页PPT里我提了两行红字,这两个问题可能不起眼,但严重性很大。在PCB板中,芯片的下面有基板,一般是陶瓷的或者金属的,芯片与基板热膨胀系数之间不匹配,在反复的工作循环中,这可能就会造成部件的失效。现在国产化是一个大的趋势,但其实我们国内在一些领域的技术经验都是很缺乏的,我们国内公司很多是知其然不知其所以然。如果说你连这个产品的形态为什么是这样都不知道。怎么创新呢?包括后面我们怎么去引领国外的竞争对手能够遵循我们的标准去设计、生产产品,这个也很困难。这里我做了一个风冷和液冷方式的对比。从成本上来讲,其实有一些浸没式冷却,它比冷板式冷却还便宜,如果是相变的。那它的成本就高一些,包括寿命和稳定性也是冷却系统评估的一项重要指标。在这里面需要很多头部企业的共同努力,去制定行业内的标准。现在液冷冷却的成本还是很高,首先是没有量产,其次正是因为没有标准化,没有标准化就意味着不确定性太多,加大了设计的成本。用空间多了你也得放它是一个很标准化的一个产品,这样其实导致整个行业能够做的成本。液冷和风冷最大的一个差别就是,风冷产品,譬如说服务器,它更换一个模块十分容易,不会对整个设备做出大的更改。但如果发热量比较高或者散热空间比较小的时候,产品可能就要转向液冷。对这种产品进行维护的时候,它内部的结构更加复杂,因此需要更高的标准化。像汽车里面的标准化现象就很明显。那对于充电桩或者储能包内部的液冷系统,就需要大量标准化上的努力。对于风冷系统,标准化的问题可能就集中在风扇上。风扇出现一些问题,譬如说积灰、风量不够,这时候就着重解决就行了。对于液冷系统,很多情况下你都很难判断出问题的地方。接头、传感器、冷却液等都可能造成它的损坏。这一方面是挑战,但也是给一些头部的企业机遇去抢先解决这些问题,制定一些标准。现在中国在新能源领域取得了一些领先地位,说明相关头部企业的技术在该行业是领先的,这就更有必要依靠技术优势去取得标准化的领先地位。对于浸没式冷却,大部分非相变的,它更适合于一些散热均匀的系统,像CPU芯片这种集中发热的系统就会造成比较大的浪费,但对于储能包这种就比较适合,因为它需要电池间有比较好的均匀性。对于所有有热需求的产品,基本上都会面临四个挑战。其中最主要的就是材料方面的创新设计。譬如说对于冷却液,一般在低温的情况下它的流动阻力会加大,造成冷却效果的劣化,同时一般在流速越高的情况下流动阻力也越高。如果我们能设计出一款冷却液来改善这些特性,这对于冷却的提升效果是很明显的,这其实就是材料。这些表面上看都是别的行业,但实际上它对于热设计是非常有帮助的。但从方案设计的角度上来讲,一个系统的散热能力很快就会达到上限。因为散热用到的模块,比如换热器、水泵、管道,这些东西都是很成熟的。在这样的框架下去设计一个系统,就相当于进行排列组合,很快就达到最优了。所以在这种框架下要获得更优化的结果,肯定是需要学科间相互的配合。对于芯片领域,有些第三方的材料研发出来,它的耐受温度很高,但其实到目前为止我们在热管理材料领域都没有拿到这种界面材料,可以承受两百多高温,所以这就是一个卡脖子的环节。主要还是要解决材料上的问题再进行方案上的设计。 著作权归作者所有,欢迎分享,未经许可,不得转载
首次发布时间:2023-01-31
最近编辑:1年前