快速网格变形技术在车身开发流程中的应用
本文摘录自期刊题目名为“快速网格变形技术在车身开发流程中的应用”,感谢作者:广州汽车集团股份有限公司汽车工程研究院的闫亮、姜叶洁、刘向征和袁焕泉
车身是汽车的重要组成部分,是汽车所有总成及乘员的载体,其重量约占整车重量的 40%,对车身结构进行优 化设计能够有效降低汽车自重。传统的白车身开发流程以线框车身结构及截面设计为起点,设计出 CAD 数据后通过 CAE 校核反馈,再 优化设计,见图 1。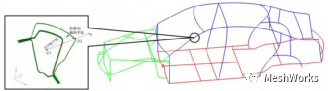

图 1
由于线框结构与详细的车身结构性能差别较大,甚至在某些时候反映的性能趋势与详细车身结构相反,因此工程师借助线框结构设计出的车身详细数模不可避免地存在诸多缺陷;此外,从线框结构开始到建立完详细的钣金结构数模,耗时较长,这一定程度上影响了后续开发的时间。综上所述,现有的车身结构开发流程有诸多缺陷。1 车身开发流程起点的新思路—基于网格变 形的结构灵敏度多目标优化本文作者在长期的研发实践中,依托先进的 CAE 分析工具,提出车身开发流程的全新思路:结合快速网格变 形工具及多目标灵敏度优化分析软件,能对现有平台快速 变形出贴合早期造型 CAS 面的目标车型,进而能获得包含详细工艺特征的准确 CAE 分析模型,再联合多目标灵敏度分析软件建立结构形状参数及厚度参数作为设计变 量,进行结构优化及轻量化,可在整车开发流程的起点阶段较准确获知并优化车身结构各项性能、车身质量,进而 为项目决策提供可靠的指导。1.1新流程的起点——MeshWorks 快速网格变形技术新流程的起点,是借助Meshworks的morph 技术,高质量快速地获得具有详细工艺特征的有限元模型。将已有同级别对标车(或扩展平台的原型车)的白车身有限元模型 导入MeshWorks 软件,根据新的CAS 面对现有的白车身有限元网格模型进行网格变形,直到贴合CAS 面为止。 本文的车身开发流程的起点技术,与当前基于线框模型车身分析技术的重要区别在于,可直接基于具备详细工艺特征的模型开展多目标参数设计,进而通过研究车身结构性能(刚度、模态、轻量化……)对目标参数的敏感程度, 从而可以确定哪些参数对系统或模型有较大的影响。以便对症下药,在后期CAD建模时可获得可信的设计思路。车身钣金的结构形状、厚度,构成了车身的最基本要素,下面将详细说明如何通过这两个基本要素建立多目标参数。白车身结构形状由构件及其接头(Joint,节点)和板壳零件共同组成,是承受载荷和传递载荷的基本系统。所以,结构参数需要考虑白车身接头,如图 2 所示。对于一般钢结构车身,其构件是由成形钢板制件焊接组成的,截面为闭口或开口的薄壁杆件,在车身中起支承和加强的作用。车身下部(底架总成)包括前、后纵梁,底架各横梁,地板及由其两侧边与侧围外板组成的门槛,地板 中间通道,前围板、后隔板、悬架支座及轮罩等;车身上部包括侧围的 A、B、C 柱,顶盖及其边梁,风窗上、下横梁等。所以,在进行结构参数设计时,顶盖横梁、后纵梁、门槛梁、 地板中通道、上侧围纵梁等也是考虑参数之一。厚度参数的设置可以涵盖白车身上所有板壳的选取,以便白车身轻 量化。此处共取形状变量 26 个,厚度变量 16 个。具体参数选取及范围见表 1 和表 2。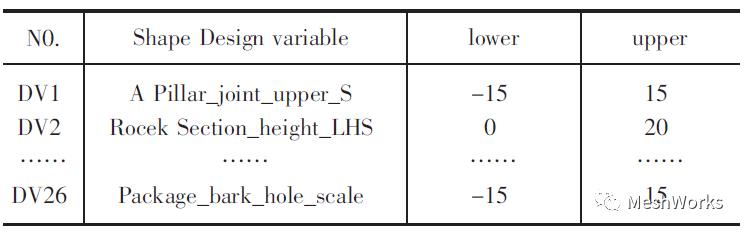
表2 16 个厚度变量
为了优化结构,需要量化所有的设计变量,包括结构参数和厚度参数,即构件截面特性和接头刚度对材料几何 尺寸变化的灵敏度,以及结构整体刚度对截面特性、接头 刚度或板厚变化的灵敏度,以便选择较灵敏的变量或部位 进行修改,引导结构优化的方向。 Isight 软件的优化设计,是对试验设计获得样本库的基础上,运用近似模型方法,建立设计变量与响应变量之间的数学表达式,对响应函数进行平滑处理,降低“数值噪 声”,有利于更快的收敛到全局最优点。常用的近似模型方 法包括:响应面模型、克里格模型或神经网络。本文中用到 的近似模型是响应面模型。根据已有的设计变量及设计变量的变化范围,选取样本点,样本的点的选取通过试验设计 (DOE,Design of Experiment)方法进行抽样,用尽可能少的仿真获取设计变 量与响应变量之间的规律和关系,通过方差分析方法,辨 识对输出参数影响最关键的设计变量,从而有效缩小优化 中设计变量的数量,降低优化的难度和时间开销。常用的 试验设计方法包括正交数组和优化拉丁方,这里采用优化拉丁方选取样本点。42 个变量,选取 100 个样本点。得到相应的 DOE 矩阵。由于车身结构的对称性,为了减少设计变量的个数,降低计算时间,以几个接头等结构和车身各板厚为设计变 量,将左右相同的部件的厚度设置为同一个设计变量,共 有 42 设计变量,100 个样本点,根据响应面得到各个设计 变量对性能影响的灵敏读分析。各个变量对目标函数的影 响,一般只考虑影响程度在 5%以上的变量。至此,已经获得影响车身结构性能(刚度、模态、轻量 化……)重要的结构部件。下面将重点以这些部件为结构 优化及轻量化的对象,开展 CAE 分析。白车身结构的轻量化设计是采用优化设计方法,在保证车身结构性能的前提下,通过对车身板件厚度的重新分 配,达到轻量化的目的。优化设计是一种寻找确定最优设 计方案的技术,通过对设计变量的合理选择,在实际约束 状态下,使系统性能指标最优。白车身结构的约束优化设计问题可表述为
式中:x=[x1,x2,x3,…,xj,…,xn]T,x 为由车身板件厚度组成的向量。xj 、xj 分别为设计变量的上、下限;f( x)为白车身结构质量函数;g(k x)为约束函数。 考虑两个学科对白车身性能的影响,包括弯曲刚度和扭转刚度,弯曲模态和扭转模态的影响。选择对上述工况有较大影响且可以改进的白车身结构及板厚作为设计变量,即 1.2.1 中提到的结构参数和厚度参数,根据制造的实际情况,定义设计变量的取值范围,共计42 个设计变量,26 个结构变量,16 个厚度变量。 优化的目标和约束分为两条路径进行:①目标函数定义为弯扭刚度、模态最大,定义的约束条件为质量能够接受的最大值,旨在寻找质量一定的情况下,性能的最大值;② 目标函数定义为白车身质量最小,定义的约束条件如表3。 采用优化拉丁超立方法对实际可取水平生成刚度、模态的样本矩阵,既可用于参数灵敏度分析,设计变量的DOE 矩阵。 根据设计变量和优化工况的特点,刚度、模态近似模型选取二阶逐次替换的响应面模型。为确定近似模型的精度,对其进行了随机抽取样本点的误差分析方法,结果表明所建立的近似模型满足工程开发的精度要求,弯曲、扭 转刚度、模态的误差分析结构,刚度、模态近似模型的误差都小于2%。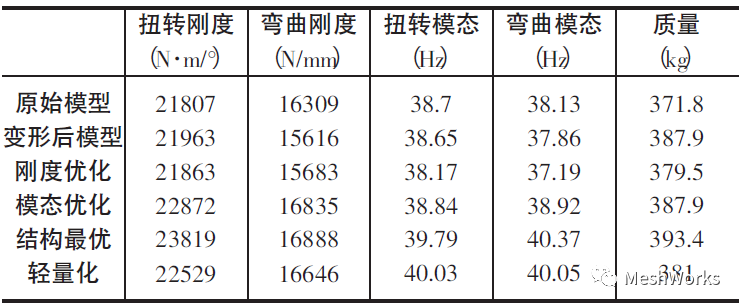
变形后的基础模型,其扭转刚度 21963N·m/°,弯曲刚度 15616N/mm,扭转模态 37.86Hz,弯曲模态 37.86Hz,质量387.9kg,经过刚度、模态优化后,其扭转刚度 23849N·m/°,弯 曲 刚 度 16888N/mm, 扭 转 模 态 39.79Hz, 弯 曲 模 态 40.37Hz,质量 393.4kg,可见,优化后,扭转刚度提高8.45%,弯曲刚度提高 8.15%,扭转模态提升 2.95%,弯曲模态提升 6.63%,质量增加 5.5kg;轻量化后,其扭转刚度 22529N·m/°,弯曲刚度 16646N/mm,扭转模态 40.03Hz,弯曲模态 40.05Hz,质量 381kg,轻量化后,扭转刚度提高 2.58%,弯曲刚度提高 6.6%,扭转模态提升 5.73%,弯曲模态提升 5.78%,质量减小 6.9kg。 通过上述快速网格变形的多目标优化分析,最终得到合理的有限元模型。将这些有限元模型导成 CAD 格式数据,导入 CAD 设计软件(如 CATIA)中,即可获得合理的整车模型。由于此步得到的 CAD 数模已经事先进行了足够详细的 CAE 分析,可以认为此版数模是足够详细准确的。本 文 根 据现有的白车身有限元模型,通过 MeshWorks软件中的 MORPH 功能,在车身预研阶段, 根据 CAS 面,建立了白车身在预研阶段的有限元模型,并且在MeshWorks 软件里建立了结构参数和厚度参数,作为所选取的设计变量,联合 ISIGHT 优化软件,对白车身性能以及质量进行了优化,在保证白车身结构静、动 态特性的提升的前提下,使白车身质量减小 6.9kg,实现了轻量化的目的。事实上,此技术已有效地指导了 GS4、 GA8、GS8 等上市车型的车身结构设计,并在后续项目中继续使用。展望下一步,将切实结合广汽研究院整车开发 流程,继续优化快速网格变化技术,提前介入分析,使车身 结构设计开发更为快速、准确;此方法已纳入广汽研究院 整车开发核心技术。