【技研】汽车总装工艺的设计原则
汽车总装工艺的布局首先应遵循前面所述的七大原则,然后结合各企业场地的具体实际进行合理规划。目前常见的总装工艺布局型式主要有S形、T形及U形等三种,如图5-1、5-2、5-3所示。神龙汽车公司、东风本田汽车公司的总装线采用的是S形布局,上海通用汽车公司的总装线采用的是T形布局,载货汽车及微型车总装线大多采用U形布局。 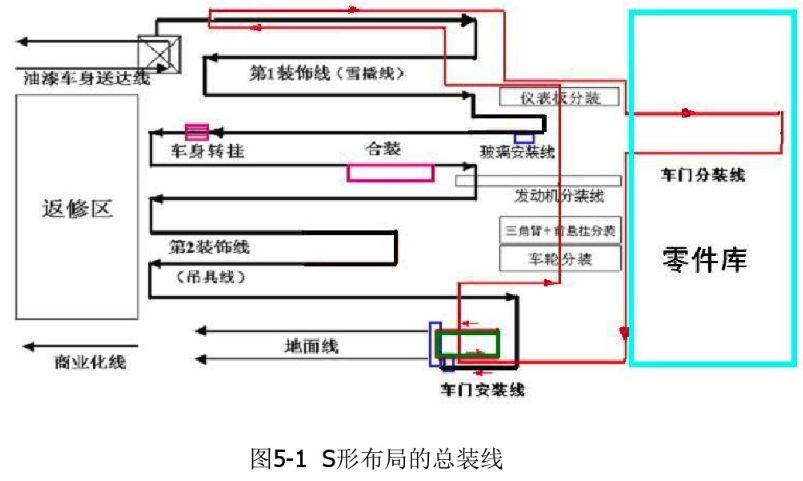
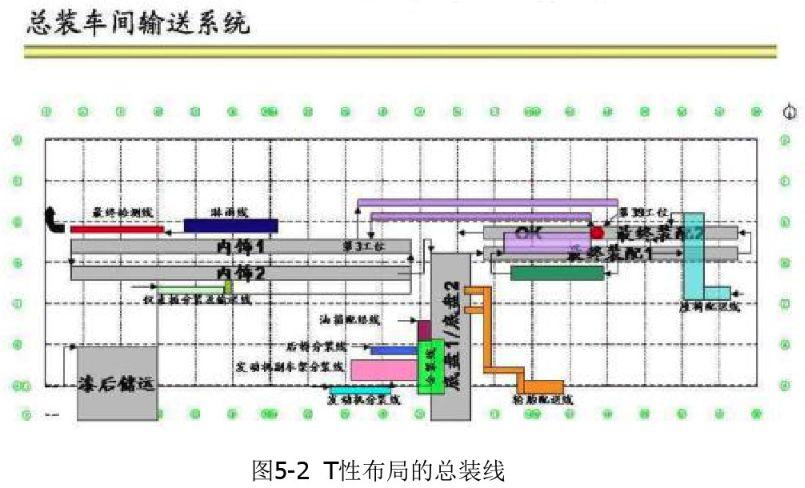
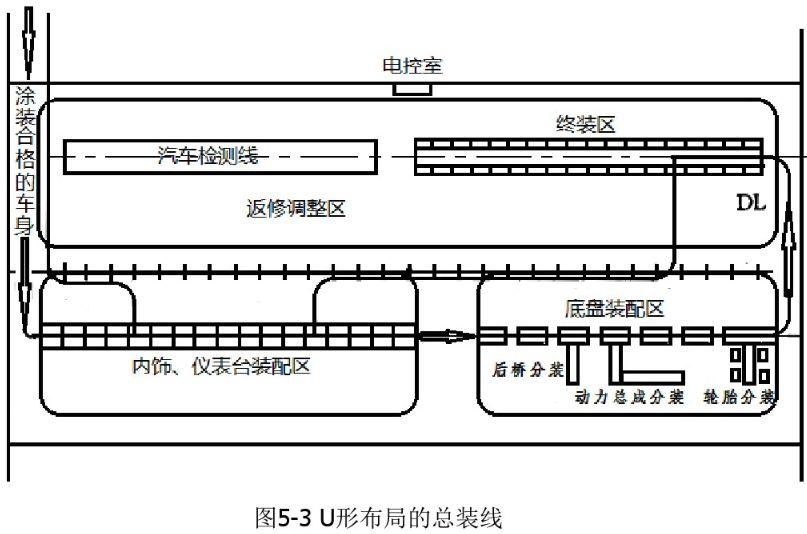
为了便于汽车总装质量的控制与总装工艺的规范化管理,汽车总装工艺常将其分为若干个模块,如:内饰装配一线、内饰装配二线、底盘分装线、车门分装线、仪表台分装线、车轮分装、车身合装线、终装线、性能检测线等。
汽车总装工艺十分复杂,由数百个工位组成,图5-4是某汽车公司汽车总装工艺的主要工艺流程。为了简化总装工艺、提高总装效率,汽车总装已普遍实现了模块化生产,即将多个总成部件按照其装配关系或功能的关联性组合成一个个的装配模块,如:将动力系统(包括发动机及整个传动系统)、车桥与悬架集成为一个底盘装配模块(见图5-5),将汽车全部仪表与空调机组组成一个模块(见图5-6),将车门及安装在车门上的全部附件组合成一个模块(见图5-7)等。
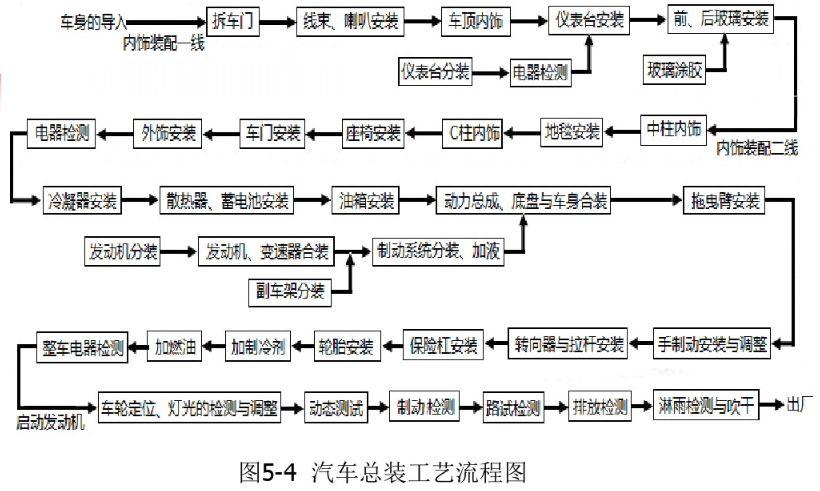
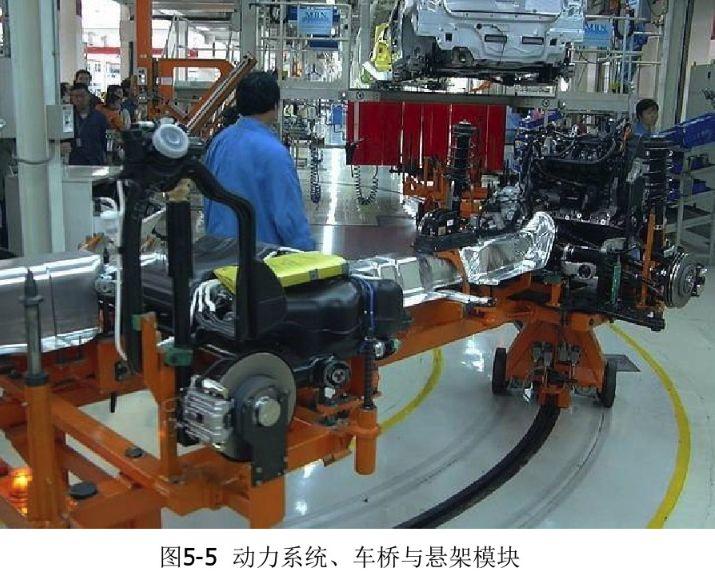
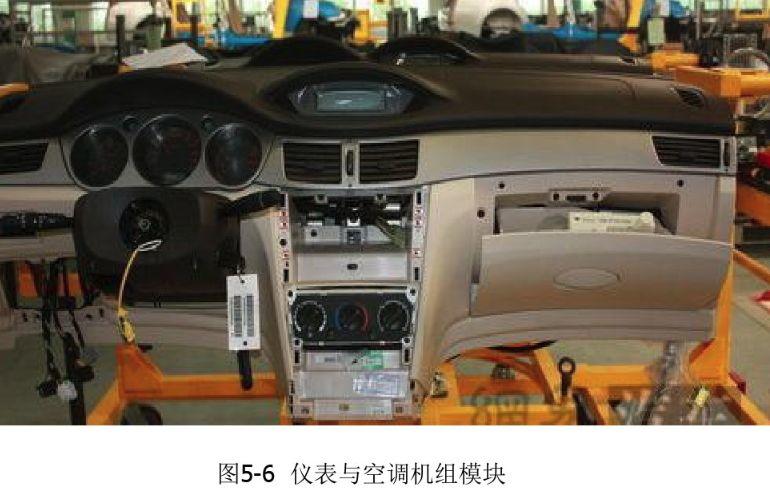
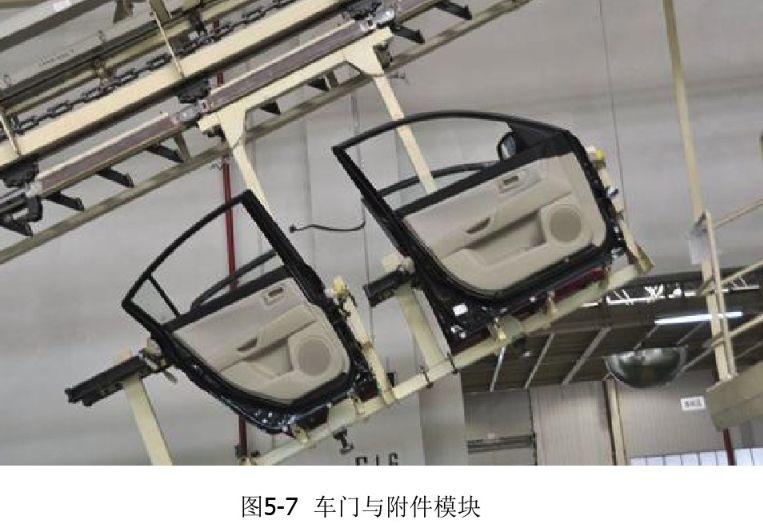
汽车总装已普遍采用准时制拉动式生产方式JIT ,即以看板管理为手段,采用“取料制”,即最后一道工序依据市场需求进行生产,对本工序在制品短缺的量,从前道工序取相同的在制品量,从而形成全过程的拉动控制系统。这种“拉动式”逆向控制方式,把由于企业划分所形成的、相对孤立的工序成产同步化地衔接起来,从容有效地制止了盲目过量生产,大幅度减少了在制品的数量,提高了生产效率和和生产系统的柔性。为此需根据企业的经营方针和市场预测,制定年度计划、季度计划以及月度计划,然后据此制定出日生产计划。但这些计划都是滚动调整的动态计划,对生产只起到预测指导和参考作用。在生产实际中,通过产品订单拉动进行生产。真正作为生产指令的最终投产顺序指令只下达到最后一道工序,即总装配线(混流生产线)。其余工序由总装配线后序顺次上溯,通过看板或同步控制信息拉动进行。
工位是总装生产线上的基本单元,工位地址提供物料运送的位置,安排生产人员并完成装配任务。总装线上的每一个工位都配置有装配用的专用工具和设备,供生产人员用于各总成部件的装配。待装配的车身作为装配基体,在流水线上以一定的速度移动,各工位的操作工在移动中完成本工位的装配工作。
为了便于管理和提高生产效率,常将大总成大系统的装配、同类零部件的装配组合在一起进行集中装配,这就是总装线上的工段。如前面所述的内饰装配一线、内饰装配二线、底盘装配线、车门分装线、动力总成分装线、动力总成合装线、仪表台分装线、终装线、性能检测线都是总装线上的独立工段。
工位节距,是工位起点和终点之间的距离,额就是前一辆车和下一辆车的间隔距离。不同工段的工位节距往往不尽相同。
流水线节拍是指车身从一个工位的起始点移动到终点的时间。流水线节拍决定混流生产条件下各工位的工位工时。
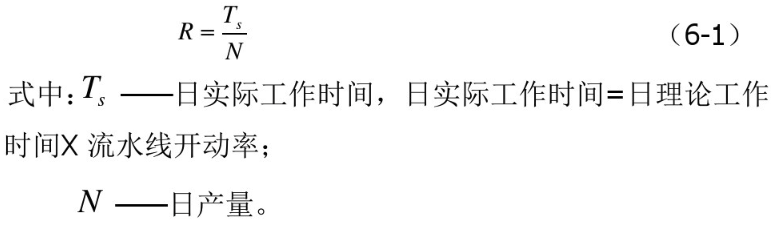
工位时间:完成工位作业内容所需要的时间。如果一条流水装配生产线上只生产一种车型,则应均衡每一工位的作业内容,使各工位的作业时间尽可能地等于流水线节拍。但对于多车型共线生产的柔性生产线,由于各车型在同一工位所装配的零部件不一定相同,装配工序也可能不一样,要使作业的时间都接近流水线节拍往往很难,甚至是不可能。因此,在进行工艺设计时,应根据各车型的生产比例算出等效工位工时,使之尽可能接近流水线节拍。
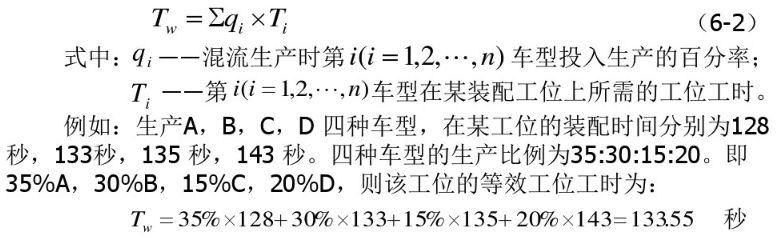
工作要素又称工序,是装配过程中全部工作内容的一部分,是完成某项操作所进行的最小工作单元。
按照精益生产的理念,从前道工序流到后道工序的零部件必须是100%的合格率,绝不允许任何不合格品从前工序流到后工序。
所谓100%的合格率,不仅是指已加工完成的零部件及产品的加工质量应全部合格,同时还包括是否按照生产工艺的要求完成了对零部件及产品的全部作业。若操作工在本工位作业区域内没能完成装配作业,则该产品被视为不合格产品,不允许流到下一工位的作业区。若出现某一工位在其作业区内没能完成其作业内容,该作业岗位的工人就必须拉下标有Andon的开关或按钮(见图5-8),停止装配线的移动,继续进行未完成的装配作业(这时班组长会前来协助完成装配),知道作业完成后在此拉下Andon开关,重新启动装配线的移动。
一旦某一工位的一名员工拉下Andon绳或按下Andon按钮,停止装配线的移动,其他岗位的员工也被迫停止装配而处于空闲状态。如此不但影响了整个装配线的工作效率,也影响了流水线的开动率。此外,若装配流水线频繁的停止、启动,还会对装配线的使用寿命带来不利影响。这就是为何必须均衡工位作业时间的原因。
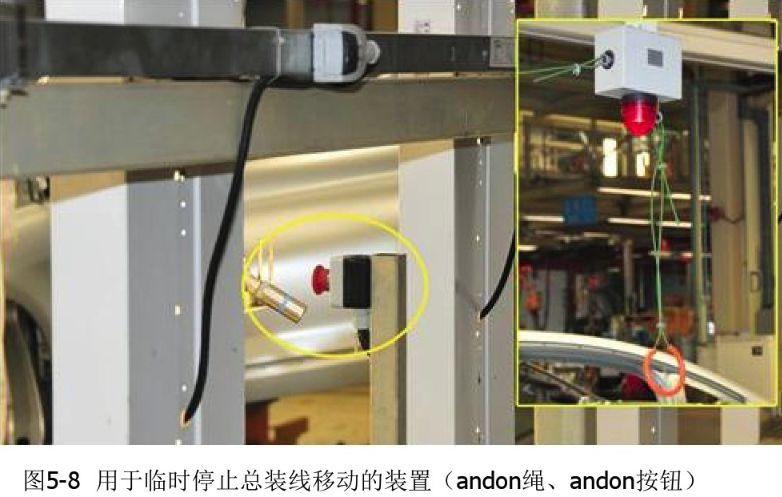
著作权归作者所有,欢迎分享,未经许可,不得转载
首次发布时间:2022-10-22
最近编辑:2年前