15年仿真经验,重点难点其实就2个!
导读:大家常说花钱如流水,其实真正如流水的是岁月。自己克制点,钱还是能少花甚至不花的,但是岁月这条小溪,堵不住也截不住,无论你如何节省克制不去使用它,它都会按照自己的步伐永远前进,甚至一代人时间用尽了,岁月还会让下一代人继续蹉跎老去!
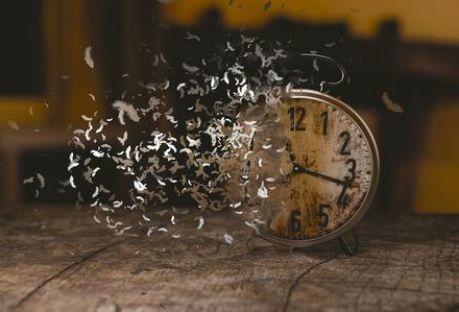
不知不觉间,喜欢的影视明星电视机上看不到了,不知不觉间,工作十年有余了,不知不觉间,接触有限元仿真快二十年了!仿真这个事并不是靠时间积累就能成为专家的。很多人工作时间虽然长,但是大部分时间都是机械重复工作,肯定有很多技术工程师也是过着类似的生活,至少身边认识的人中,工作多年还是只会基础操作的人不在少数。十几年下来,觉得有点技术含量,或者说还有点难度的技术点总结起来就两个,一个是轴承仿真建模,一个是螺栓有限元疲劳计算。一个极限强度计算,一个疲劳强度计算。最近几年,国内的很多技术领域都取得了长足的进步,甚至很多领域都已经达到国际领先水平,但是不得不承认,高端轴承领域不管是设计还是生产,国内依然是弱项,很多高端大型轴承质量依然不如国外的好。这也造成国内轴承设计人才短缺,相对应的轴承仿真方法也相对较弱。任何工业国家,设计生产能力都必然有一个漫长的提升过程,我们当然也不例外。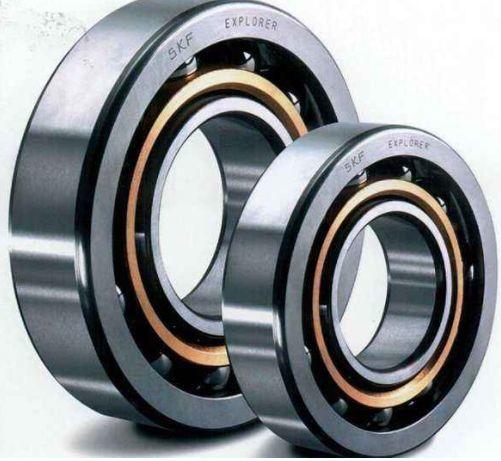
使用动力学仿真软件,模拟一个轴承,简直简单的不要不要的,一个简单操作而已,但是针对静强度中的轴承仿真,就没这么方便容易实现了。
最近各个有限元商业软件新版本,也逐渐出现了简单轴承的仿真模块,虽然有的模拟的不精确,或者收敛性太差,亦或实现的操作方法太繁琐,但是总归能实现了,不用被领导责问“这里有个轴承你为什么不建模?没有轴承你这仿真肯定不准啊!”当然,也可以使用动力学软件进行仿真计算提取结果,然后把提取的反力结果放进有限元软件中去计算,也是个不错的方法。前提是,你会动力学软件,并且时间足够用于两次建模计算。有没有一种方法,既精确,又不借助于动力学软件,操作也不太难,收敛性又好的方法呢?当时是有的,该方法来源也是国外的咨询机构,我们需要做的是消化吸收再利用,以便更好的服务于我们自己的工程项目。ANSYS软件进入国内很多年了,国外使用历史更长一些,全世界无数的工程师再使用有限元计算软件的过程中,总结了很多简单有效的仿真方法,轴承仿真目前应用最广的方法就是使用杆单元模拟轴承滚子或者滚珠,同时对轴承内外圈进行实体建模。该方法得到国际认证机构的认可(其实来源也是国外的仿真咨询机构),建模方法简单易懂,计算过程易于收敛,计算结果也可靠,唯一的缺点就是建模过程稍微复杂一点,只要对软件操作稍微熟悉的人,处理起来也完全没有难度。任何项目咨询,都是价格昂贵且时间冗长的,但是反应到实际技术操作,可能就没有这么复杂难懂了,有些可能是很简单的技巧性操作而已。结合自己多年的实际轴承建模经验,给大家分享一套我的《主流轴承产品仿真实战课8讲》,点击文尾阅读原文可体验。给大家分享几个轴承仿真的小技巧,即使不做轴承仿真,仿真其他机械结构也可能用得到的。1、轴承内外圈必须进行几何清理,小螺栓孔,线孔,小结构等等一律去除!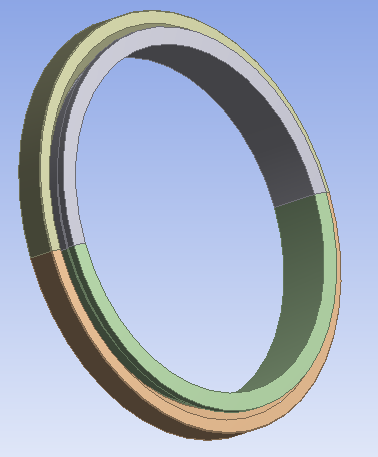
2、可以把内外圈切分成两个半圈,再合成一个Part,既不影响结构计算,还能更方便的观察几何特征。3、轴承内部结构应力分布复杂,而且是运动部件,建议有需求的学员尝试切分简化处理模型。我们知道,主机架是风力发电机组中最关键和承载最复杂的部件之一,其良好的设计、可靠的质量和优越的性能是保证风电机组正常稳定运行的关键因素,是风力发电机组结构设计的重点和难点。对类似的复杂结构部件,有限元法越来越多地应用于风机部件强度分析中。风电机组中的大部件损坏,很多部件都是与主机架连接的部件,如齿轮箱箱体,主轴承,力矩臂等,而这些部件的损伤,也是和主机架的安全性稳定性所相辅相成的,这也更说明了主机架安全稳定的重要性。风电机组的主轴,其功能是将扭矩载荷传递给齿轮箱以及发电机,将其他载荷传递给支撑结构主机架。在实际风机故障中,主轴承损坏主要为滚子破损或保持架损坏,而对于主轴承损坏严重的情形下,主机架轴承安装位置都不可避免的造成一定程度的损伤,甚至于需要重新返厂维修整机。在设计和选用轴承的过程中,需要对轴承的性能和寿命进行分析,以便及时改进设计,合理选型,提高风力发电机组的可靠性,避免失效,降低成本。我们知道轴承结构主要是双排滚子轴承支撑结构。首先看一下主轴承的结构形式以及与主机架的安装配合形式。如图1为主轴承结构图的横切图。轴承为内外两环,内部滚子为带锥度的近圆柱体,内外两环之间设有保持架结构,主要为了保持滚子能均匀匀速滚动。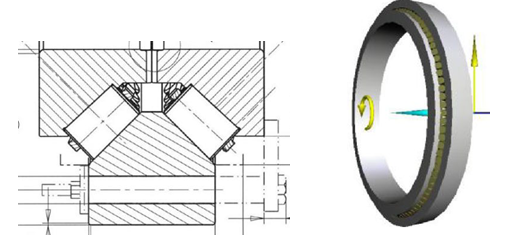
我采用三维有限元计算方法,按主机架的实际几何特征建立模型。以便计算所得的结果能较好反映实际问题,并能更详细和准确地反映真实应力的分布,得到不同位置的应力,从而为主机架的强度校核及改进主机架结构设计提供依据。主机架材料一般是球墨铸铁,铸造结构。采用三维软件建立主机架的CAD模型,并在ANSYS模块中进行有限元计算。使用的载荷是轮毂中心固定坐标系载荷,主机架有限元计算模型有必要对连接过渡段和主机架的主轴承进行建模。而在建模计算过程中分析发现,轴承建模方式的不同对主机架的应力计算结果有较大的影响,不同的工况相差5%至15%不等。在有限元计算中,圆锥滚子轴承的模拟通常采用简化滚子的方式,即保持轴承内圈的构造,将滚子用几根受压不受拉的杆单元替代,同时轴承内外圈采用solid187单元,这样的简化模拟出了轴承只传递压力的特点。目前,国内外风电厂家基本使用的这种建模方式建立轴承模型用于主机架的强度计算分析。两种不同轴承模拟方法的主机架计算应力结果存在明显的区别,使用没有联系的杆单元计算出来的主机架应力值要大于使用有联系的杆单元的计算结果。出现这种情况的主要原因,是由于主机架前端轴承安装位置的整体刚度存在着巨大的差别,同时载荷在向主机架后端传导时的作用方式也不存在差别。后者的作用方式,是在主机架前端圆环面端建立了相互联系,向后端传导载荷时也更均布一些,所以应力分布也更均匀一些。