案例分享 | 片状模压复合材料 (SMC)的数字孪生
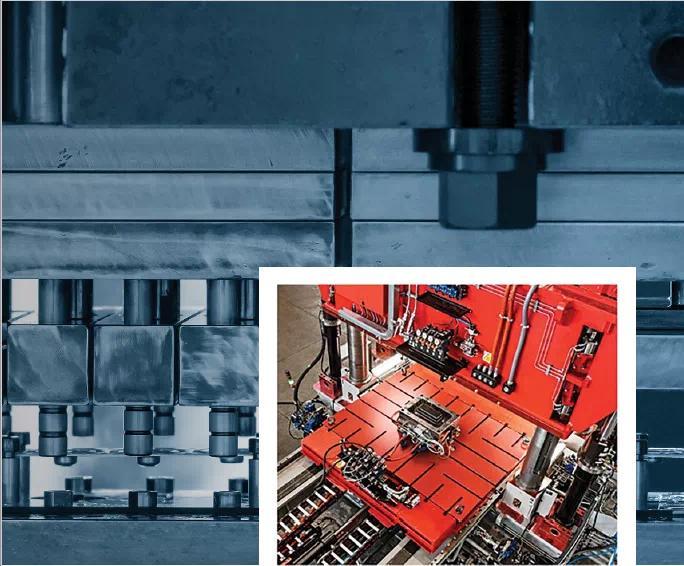
—— ICME 使得 Marelli RideDynamics 公司能够设计可靠的安全关键部件。
“Digimat 软件的使用使我们能够在复合材料的产品开发工作流程中实施具有竞争力的工程方法。因此,可以更好地利用复合材料的机械各向异性性能,避免过度设计的部件,进而优化昂贵的 SMC 材料的使用。
此外,它使我们能够在非常早期的设计阶段集成过程引起的约束,并在成本仍然可以接受时更改零件的设计。”
–SalvatoreSottile,高级材料应用工程师,Marelli 公司
为了汽车行业轻量化的发展,塑料逐步替代金属是一个持续的趋势。片状模复合材料 (SMC)是一种能够满足结构性能和安全关键部件性能的有效材料。此类材料进入市场的关键是其性能的可靠性及可预测性。
Marelli Ride Dynamics 公司(以下简称Marelli公司)已着手开发 SMC 工艺技术用于提供结构悬架部件,这与现有的金属部件相比,将能够减少对环境的影响。虚拟验证是结构和安全悬挂部件产品开发工作流程中的关键阶段,尤其是在处理新型复合材料时。目前已经开发一种将工艺导致的微观结构与各向异性材料特性相结合的集成方法,以确保可以使得结构和安全关键部件满足产品性能,并将其推向市场。为 SMC 材料构建真正的数字孪生,从而在产品开发的早期阶段进行设计优化,需要将SMC 的工艺模拟和材料精确的各向异性卡片相结合。工艺模拟产生SMC 的复杂微观结构使 Digimat 能够在考虑纤维取向和含量的情况下确定局部材料特性。Digimat 根据 Marelli 公司通过标准试样测试创建的高精度各向异性材料卡片确定局部材料特性。以上集成方法的验证是在公司自研的演示器 Omega Beam 上完成的,Omega Beam 是一种如希腊字母Ω形状的梁,包括真实世界的特征,例如可变肋拱厚度、圆角和同时成型的铝质部件。实验测试结果已与数字孪生的模拟结果以及标准各向同性模拟进行了比较。此外,还对 Omega Beam 截面进行了 CT 扫描,以重现部件内的局部纤维取向张量,并将其与公司内部 SMC 工艺模拟结果进行比较。在图 1 中,零件刚度的验证结果显示,各向同性假设模拟的误差超过 25%,导致结果不足以进行设计优化或进一步的产品开发。数字孪生将 SMC 工艺模拟与 Digimat 结构分析相结合,实现了 8% 的预测刚度误差,最小预测误差低于 1%。
图1:
Omega 梁三个位置的模拟刚度误差。
蓝色的各向同性模拟结果在所有位置均显示显著误差。
数字孪生结果可以很好地预测零件每个位置的刚度。
在静载荷实验中,如图 2 所示,数字孪生方法可以准确预测初始失效位置和相应的失效载荷,误差在实验值的 8% 以内。在自由模态分析中,预测的频率响应误差从各向同性假设模拟的 20% 减少到使用数字孪生分析的 3%。将 SMC 工艺仿真功能与 Digimat 各向异性材料建模和结构分析功能相结合,Marelli Ride Dynamics 公司为 SMC 零件开发创建了一个准确可靠的数字孪生。
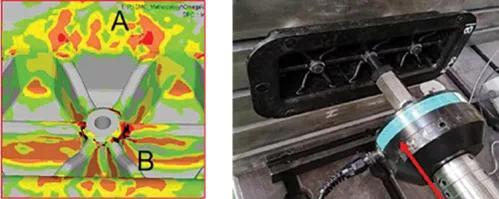
图 2:
静载荷失效指标(左)
静载荷实验装置(右)
SMC 材料的数字孪生使 Marelli 公司能够准确可靠地预测零件性能,从而使设计师能够在设计优化中综合考虑材料特性和工艺的复杂性。新的先进 SMC 悬架转向节,其重量比常规的铝质部件节省约 25%,已经在产品设计初期进行集成开发。工程师对 SMC 试样进行了广泛的测试,并从中得到适合静态和动态性能开发的材料卡片。转向节将采用 ASMC 工艺技术并使用位于都灵的 1500 吨 SMC 压力机制造。