整车底盘CAE仿真技术!
MBS软件不仅可以用来模拟零部件和系统,还可以用来建立整车模型。一个整车仿真模型可以用来虚拟地在模拟路面上“驾驶”车辆,并执行各种模拟驾驶操作。这不仅可以评估车辆的动态特性和操纵性,还可以提供每次机动过程中出现的单个力的分解。这样就可以确定各个组件之间接口处的力。这些值可以用作组件设计的起点。为了提供这种详细程度,必须使用非常复杂和详细的整车模型。但是,根据模拟的焦点,不感兴趣的组件可以估计为集中在组件实际质心的简单质量。
整车的开发是OEM的责任。因此,OEM负责构建、验证和维护任何整车仿真模型。这也是因为主机厂是唯一拥有模拟所需所有数据(底盘、悬架、动力总成、轮胎模型等)的一方。只有当主机厂向供应商提供所需数据时,供应商构建整车模型才有意义。如果是这种情况,供应商可以向原始设备制造商提供工程工作包,包括:
相关的操纵参数(如自转向梯度、响应特性、稳定性、车身固有频率等)及其目标值应由主机厂确定。车辆的动态和自转向特性的仿真不仅需要整车模型,还需要路面模型、轮胎模型和动作定义。表6-1列出了所有主机厂使用的标准驾驶操作。车辆的行驶和操纵性能在很大程度上取决于道路和轮胎之间的力传递。因此,轮胎性能必须精确测量和精确建模。各轴的弹性运动特性对车辆的整体操纵性和动态性能有着重要的影响。主要的弹性运动学参数包括前束、外倾角、后倾角、车轮中心位移等。弹性运动学特性是用运动学和柔度试验台(K&C台)测量的。这种类型的试验台允许运动学和弹性运动学参数彼此区别(见图6-49)。运动试验为了研究运动特性,将车轴刚性地连接到试验台上,并通过压缩和回弹行程同时移动车轮(平行车轮行程)和单独移动车轮(相反车轮行程)。记录由此产生的前束、外倾角和车轮中心位移。弹性运动试验为了研究弹性运动特性,将车轴刚性连接到试验台上,并承受施加在轮胎接触片上的纵向和横向力。记录由此产生的前束、外倾角和车轮中心位移。使用的MBS模拟模型必须使用柔性组件(FEM模型)构建(图6-26和6-17)。车轴弹性运动学特性的目标值在项目开始时确定。一些示例曲线如图6-27所示。参数值,如前束或外倾角柔度,可以通过计算曲线在特定点(例如在设计或中性位置)的坡度来确定。在底盘和悬架设计的早期阶段,车轮负载通常是不可用的,或者是使用原型来测量的。因此,使用基于标准驾驶机动的标准载荷工况,而不是实际载荷工况。假设这些机动是准静态的,即与时间无关。生成的标准荷载工况用于ADAMS模拟,以确定准静态有限元计算(结构刚度、耐久性)的横截面荷载。类似的标准荷载工况被大量的车辆制造商采用。车轮荷载以车轮加速度或数值力或力矩的形式给出。加速度是一个更普遍的值,因为它独立于轴负载。即使车辆重量发生变化,独立于负载的参数值也可以重复使用。表6-2显示了强度分析的标准荷载工况(荷载工况1至10)和耐久性分析的荷载工况对(11和12),(13和14),(15和16)。为了提高仿真的质量和有效性,MBS模型所提供的结果应与以往和现有的实验结果进行比较。在开发过程中,为了达到最大的效率和确保系统的最佳功能,测试和仿真部门之间必须有密切的工作关系。多体模拟和实验测试的结果可以在多个领域进行比较,如表6-3所示。为了达到NVH的目的,可以使用虚拟的四个试验台进行低频(0到25hz)试验,以确定车身的横摇、俯仰和偏航频率以及悬架的固有频率。图6-28中的图表显示了计算数据和测量数据之间的比较。在比较计算数据和测量数据时,必须特别注意轮胎接触面处的边界条件(不打滑或受限)。表6-4显示了研究的兴奋类型为了使用强度计算和随后的实验验证来设计和优化底盘部件和系统,必须知道准确的横截面载荷[16]。负载管理包括分解系统级上发生的负载并确定产生的组件负载。对于底盘系统,系统级载荷由车轮力和驱动载荷组成,这两种载荷通常由车辆制造商定义。部件级包括独立的底盘部件(控制臂、车轮托架、底盘副车架),其设计需要精确的横截面载荷。负荷管理中使用的计算方法和过程称为负荷级联。图6-29提供了与底盘开发过程相关的负载管理计算任务、方法、先决条件和结果的摘要。计算过程从左到右显示。在系统级,创建和/或测量合成负载和实验负载(按此顺序),以用作MBS仿真中的输入负载。计算横截面荷载,并用于设计构件的结构和操作强度。这些计算出的载荷也可用于验证试验。图6-30中的下一行表示使用测试设备的负载级联的替代路径。这种方法特别昂贵和费时。在大多数情况下,负载级联是使用ADAMS/Car多体仿真软件的一个版本来执行的,该软件已经扩展到包含所需的功能。MBS软件允许创建、分析和优化车辆模型,与使用原型的耗时实验运行相比,所需的工作量要少得多。然而,在一个模拟可以被认为是真实的之前,它的结果必须与实验数据相比较。这些实验数据为保证仿真结果的质量提供了参考。由于在底盘开发的早期阶段既不存在原型轴也不存在实测载荷,因此只能在更高级的阶段进行比较。为了评估MBS模型的准确性,还需要精确分析计算的横截面载荷(对于合成和测量的载荷情况)与车轮力和驱动载荷之间的关系。实验确定的力和力矩必须经过复杂的前后处理。这是与负载管理相关联的主要任务之一。以下段落详细描述了应应用于MBS模型的荷载、模型验证比较点的选择以及荷载数据的分析和评估。多体仿真所起的中心作用如图6-31所示。瞬态、高动态道路力和力矩不仅用作轴试验台的输入值,而且还使用相关的虚拟试验台应用于MBS轴模型。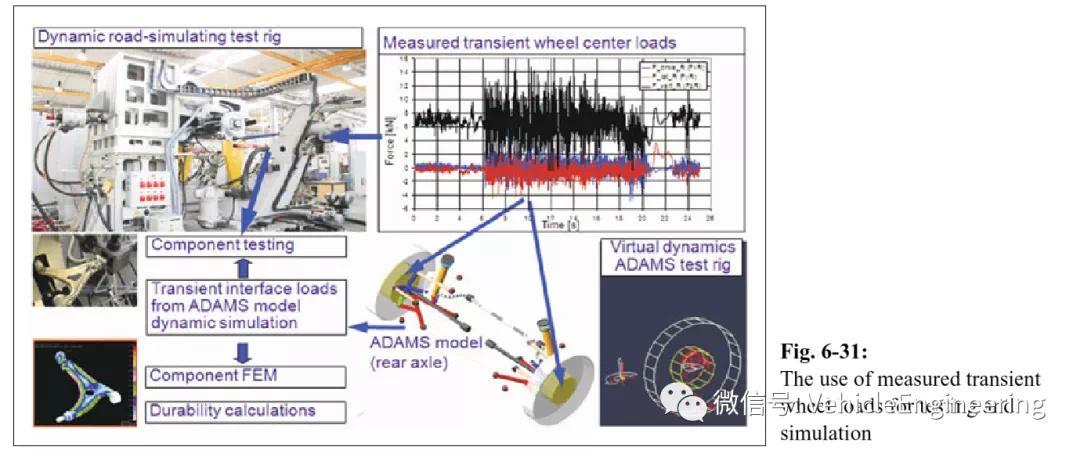
本小节描述了MBS模型验证中可用和推荐的荷载和荷载情况。 多体仿真验证的输入数据包括准静态和/或动态载荷情况。为了便于与实验结果进行比较,并允许使用易于理解的参数来证明模型的合理性,所使用的荷载应尽可能简单,例如纯垂直车轮力或简单垂直车轮行程。例如,对于静态载荷情况,可以使用应变计精确测量由已知车轮力或弹簧行程距离产生的支柱反作用力,并使用手动计算进行双重检查。即使在车轴开发的早期阶段,静止车辆处于空档位置或在特定的负载条件下的负载也是已知的,因此非常适合用作仿真模型的验证负载情况。模拟模型的行为也必须在动态载荷条件下进行研究。在大多数情况下,部件设计时还必须考虑动态载荷。同样,用于模型验证的输入负载信号应为具有恒定或稳定变化频率的简单正弦力信号。只要可能,验证负载情况应该是连续的,而不是重叠的。例如,应单独检查模型对悬架压缩和制动的响应,而不是作为组合载荷情况。仿真模型提供的输出数据包括规定连接点处的横截面载荷(例如两个部件之间的橡胶衬套、车轮托架与前束连杆的接口等)。当实际测试运行(道路荷载数据收集,RLDC)中的荷载可用时,这些横截面荷载在设计过程的后期进行验证。使用横截面载荷作为输出数据需要定义与基于组件的局部坐标系相关的接口。这些接口的定义还必须考虑与测量仪器相关的限制。在非理想情况下,试验部件载荷数据(使用道路模拟试验台或在RLDC期间测量)可在与模型基于部件的局部坐标系中的位置不完全相同的测量点处获取。还必须注意的是,仿真模型中的坐标方向并不总是与测量设备的坐标方向匹配。例如,不可能总是在两个部件之间的界面的确切中心安装应变计。比较点必须位于车轴的不同部分(不重叠),并应选择使所有三个力方向的独立验证成为可能。
张力和/或压缩中的两点连接为比较点提供了一个最佳位置,因为应变计可以精确地附着在加载方向上,并且MBS模型中的局部坐标系可以定向以匹配。从这些比较点获得的测量信号可以根据输出是负值还是正值直接转换为张力或压缩。实验结果与模拟结果具有很好的可比性。以下部件适合用作比较点,因为它们很容易安装传感器,以测量其在x、y和z方向上的位移或变形:
Fx:下控制臂和车轮托架(靠近控制接头)之间的连接,在后拖拉杆上(如适用)
Fy:前束连杆,下控制臂和车轮托架(控制接头)之间的连接,上控制臂和车轮托架之间的连接(对于双横臂悬架系统)
Fz:支柱(弹簧/减震器系统)、下控制臂和车轮托架之间的连接(球节上的拔出力)和稳定杆上的连接。
包含模拟和实验负载与时间函数的数据集通常必须在评估之前进行处理,因为测量数据通常包括预加载偏移量。
为了确定仿真的质量,通常使用以下过程分析加载时间数据集:
载荷时间数据的可视化分析
通过LMS-Techware软件包,可以比较MBS仿真和相应试运行的部件负载信号,该软件包能够确定曲线的一般特性以及相移和峰值负载偏差的相关性。峰值负荷偏差,特别是垂直方向表示模拟模型和试运行之间的发散力-位移曲线(如弹簧、阻尼器、二次弹簧)(图6-32)。关于频率相关性,模拟和实验悬架负载的典型固有频率和PSD振幅应在垂直方向(车身:约1至1.5 Hz,底盘:约10至14 Hz)和水平方向(约20至30 Hz)上相互关联。 由于原始测量数据通常使用最大频率为50赫兹的低通滤波器进行预处理(这种滤波通常在记录数据后立即出现在测试轨道上),因此只需检查0至50赫兹的频率范围。使用低通滤波器的预处理有助于消除可能的混叠效果,并解释了道路模拟试验台的驱动功率有限。如果PSD在几赫兹范围内显示高振幅(与典型固有频率的偏差),则很可能存在混叠(图6-33)。a) 对称类扫描与发生频率:对称类扫描用于评估荷载相对于其发生频率的分布,同时考虑荷载方向(张力或压缩力)和静态荷载的大小。 静态荷载(发生频率高)可在曲线的转折点或“前端”进行区分,而最大和最小荷载(发生频率低)可在最小循环次数下找到。这允许执行以下模型检查:- 检查不同负载条件下的静态轴负载检查不同车辆高度水平控制设置(在道路上,越野)
- 通过创建车轮和减振器上的力的类扫描图来检查车轮和减振器负载之间的比率
- 检查减振器的力-位移曲线以确保适当的压缩力和回弹力
- 检查最大力和最小力的偏差(偏差可以指示MBS和试验车辆或车轴中的不同部件力-位移曲线(二系弹簧、阻尼器)。
b) 应力对与累积发生频率(图6-34):应力对图显示了荷载相对于其累积发生频率(所有荷载循环的总和)的双倍振荡幅度。与类扫描不同,不考虑平均值(例如静态预加载)。与类扫描图类似,模拟和实验结果的总体行为应该相互关联。在小的累积发生频率范围内可以发现高动态荷载。如果曲线具有不同的最大累积出现频率,这表明模拟中的小振幅载荷数量与实验确定的结果不同。这意味着MBS模型中存在错误。这些误差可能是由于衬套或轴承刚度过大(橡胶衬套、车轮轴承)或数值求解过程的不正确调整造成的。荷载引起的损伤是影响构件耐久性的重要参数。以力和力矩为输入参数,利用Miner损伤累积准则计算损伤。由于累积损伤的计算对载荷变化非常敏感,应力对作为载荷谱引起的单个相对损伤的函数,应作为MBS模拟和实验结果可比性的进一步参数进行评估。只要最大损伤值(X轴上的最终值)相差小于20%到30%,模拟和实验结果中的载荷就足够相似。大的力差和小的循环次数(由x轴上的小值表示)通常会导致损伤的差异,而这些差异无法由较小的载荷补偿(图6-35和6-36)。由于载荷谱的变化只能针对具有相同斜率k的假定Wóhler曲线,因此计算的损伤是一个相对值。坡度k应尽可能接近荷载作用构件所用材料的坡度。应注意的是,10%的荷载增加(对于所有振幅)会使损伤增加1.1k倍(k=5ˇa系数为1.61)。
如果部件设计的车辆荷载是通过在某个虚拟路面(坑洞、路缘石等)上“驾驶”来计算的,则需要更复杂的模型。只有在极其精确的轮胎和路面模型可用时,才能提供精确的载荷数据。整车耐久性仿真尚处于研发阶段。因此,极限荷载工况和道路荷载的模拟通常不用于确定构件荷载。对于极端负载情况,每个原始设备制造商都使用自己经验证的值和负载数据。 当今车辆中越来越多的主动动力系统已经将正常驾驶员的标准工作范围扩展到线性车辆行为的界限之外。因此,有必要对现代车辆在线性和非线性范围内的动力学行为进行分析。在下面的段落中,描述了一个结构化的过程,该过程允许在运行条件下对车辆进行分析,直至并包括极限范围。这一过程也是车辆动力学系统发展的基础。以DIN/ISO所描述的车辆动态特性的评价方法为基础,采用系统论方法,使车辆的动态特性能够在期望的工作范围内得到描述。这种车辆行为描述在下文中称为“操控指纹”。基于车辆作为一个系统的结构表示,以下传输方程可用于各种工作范围和激励:
传递矩阵G(s)包含关于系统输入和输出之间传递路径的信息,因此可用于描述系统在目标操作条件下的传递行为。传递矩阵为分析车辆的操纵和动态行为奠定了基础。下面几段着重介绍横向动力学。横向动力学研究中最重要的输出值是横摆角速度(横摆角速度)ψ、车辆侧滑角β、横向加速度av和侧倾角Ψ。系统由方向盘转角输入δLRW激励。因此,用于描述系统行为的简化传递方程变为:车辆的横向动力学行为随车辆的速度和横向加速度而变化。因此,横向动力行为域被定义为由这两个轴组成的图。在此范围内,选择操作点,以便研究整个线性操作条件范围(图6-37)。对于这些操作点中的每一个,可以使用二阶线性传递函数来描述四个输入和输出路径的传递行为。这些传递函数表示系统在选定操作点的小信号行为。为了确定特定工作点的小信号行为,系统在选定的工作点内和周围受到激励。对激励信号的要求部分取决于工作点的线性极限,以及由此产生的传输行为的预期相关频率范围。随机或正弦输入信号最适合用作测试信号。这些测试信号叠加在选定操作点所需的固定方向盘角度上。正弦扫频信号在车辆试验中得到了很好的应用。识别方法用于根据记录的频率响应值确定二阶传递函数。然后,这些传递函数可用于计算表征车辆操纵性的各种动态参数。这些特征值可以在横向动态范围内绘制,即作为车速和横向加速度的函数,以获得车辆的操纵指纹(图6-38)。除了车辆操纵性的标准评估外,本文所述的指纹法为工程师提供了描述和评估整个横向动态特性范围内的操纵性的可能性,包括车辆附着力的物理极限。指纹法不仅可以用于伴随客观和比较的车辆评估,还可以作为车辆开发过程中处理行为的连续描述,从最初的需求规范开始 最终确认。虽然指纹识别方法是针对横向动态领域发展起来的,但也可以扩展到纵向和纵向动态领域。有关指纹方法的详细说明,请参见[21]。在确定新悬架系统的弹性运动特性时,采用基于新型模型的控制系统设计方法来描述弹性运动效应。该弹性运动学模型的基础是根据[22]中的转向模型,添加弹性运动学和运动前束差角。转向模型的输入值对应于已知车型的不同条件值和输出值。转向模型的输出值是车辆模型的输入值。侧向力引起的弹性运动前束角差(由转向模型输出)可以作为侧向力对车轮切割角影响的反馈函数集成到车辆模型中(图6-39)。是第i个车轮前束角变化的量度,用于测量在所选工作点AP处第j个车轮上横向力的变化。反馈矩阵的各个分量对应于各种前束力-位移曲线Y Y-XXK G=-的负梯度Y XG。负号源于前束差角(作为正值添加到车轮切割角中)的定义,源于输出反馈(要求输入负反馈值)的定义。预滤波矩阵主要考虑转向比iL。作为描述弹性运动特性的仿真模型,使用包括轮胎磨合行为的线性化车辆模型来描述横向和偏航运动:
使用极点规范[23]确定输出反馈的直接方法用于指定反馈矩阵。这种方法允许在合成轴系时考虑许多不同的特性。该模型提供的可能性在[21]中描述。 设计过程应在几个不同的操作点进行。结果值是趾力-位移曲线的梯度。通过对轮胎力进行积分,可以将其转化为力-位移曲线。这些力-位移曲线不一定能用被动系统来实现。因此,该设计过程非常适合确定主动轴系统的要求。实现所需的力-位移曲线是车轴开发人员的责任。目标趾力-位移曲线的形状是以客观准则的形式根据操纵要求确定的。这些准则被转化为控制系统准则,即极点和零点。参考车辆动态特性的“操纵指纹”描述可作为新轴系开发和优化的基础。新车轴所需操纵性能的极点和零点可直接从参考车轴的传递函数中获取。本文提出的弹性运动学控制理论设计方法为轴系的先进设计提供了新的可能性。车辆的动态性能要求可以作为设计过程的一部分直接考虑。该分析设计过程允许在车辆动态系统设计的高级概念开发阶段进行试验和测试。这导致必须进行的模拟和实验测试的数量减少。弹性运动学的控制系统设计最初是为了调整由侧向力引起的前束和外倾角行为。从理论上讲,开发这些用于纵向力和弹簧行程的方法是可能的,但这尚未实现。本文经授权来自VehicleEngineering。

硕士
|
CAE仿真负责人
个人著作《汽车NVH一本通》
获赞 1136粉丝 5958文章 921课程 20