环境污染问题的日渐突出,使得清洁能源成为大势所趋,新能源汽车的需求正迅速增长。而作为能量存储单元,电池的性能和使用寿命直接决定了电动车的性能和成本,如何提高电池的性能和寿命成为电动汽车的研究重点。
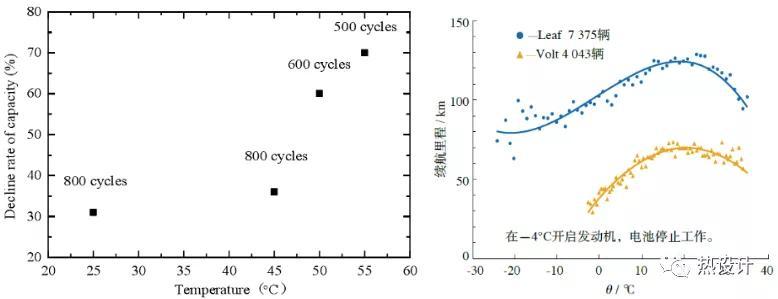
图16-38 典型电池不同温度、不同循环次数下容量衰减程度实验结果(左)
Leaf 和Volt 在不同温度下的续航里程统计(右)
目前,电动车辆上使用的动力电池多为锂离子电池,且是由多个单体电池通过串并联方式组成电池组,从而实现大功率充放电,满足车辆大功率的动力要求。锂离子电池在进行充放电时,由于转换效率小于100%,内部将产生热量。如果散热不及时,会导致电池局部温度快速上升,电池使用寿命大大缩短,严重时甚至会造成电池热失控,汽车发生爆燃。当动力电池温度过低时,电池的容量和寿命同样会极大衰减[6][7]。实质上,使用燃料电池的汽车同样面临电池温度敏感性问题。即所有类型的动力电池均需要温度控制设计以保证运行效率、寿命和安全性。
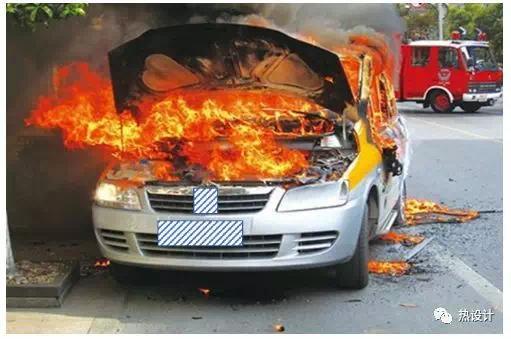
图16-39 因热失控发生爆燃的电动车
1) 确定热管理系统的设计目标:应用场景不同时,热管理方案所受到的空间、重量、成本等限制也不尽相同;
2) 确定电池系统热相关参数:各种场景下的发热量,电池本身的传热特性,电池对温度的敏感性;
3) 根据要求和热学参数,选择合适的热控方式,并输出首版详细热设计方案;
4) 根据设计方案进行打样测试,分析测试结果,实施改进措施,并对方案中的一些自动控制策略进行验证,迭代得到终版设计方案;
5) 整车/整电池包实际样品测试,如有必要,对部分自动控制参数进行微调,输出终版动力电池热管理方案。
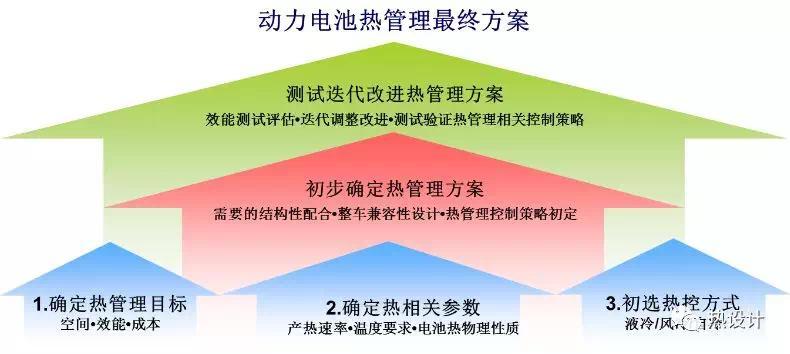
图16-40 动力电池热管理设计步骤和各环节考虑因素
结合电子产品运行场景,电池热管理系统的目标可以细化如下:
保证单体电池处于适宜的工作温度范围,能够在高温环境中将热量及时转移、低温环境中迅速加热或者保温
减小单体电池内部不同部位之间的温度差异,保证单体电池的温度分布均匀;
保持电池组内部不同电池的温度均衡,避免电池间的不平衡而降低性能;
考虑极端情况,消除因热失控引发电池失效甚至爆炸等危险;
满足电动汽车轻型、紧凑的要求,成本低廉、安装与维护简便;
有效通风,保证电池所产生的潜在有害气体能及时排出,保证使用电池安全性;
温度等相关参数实现精确灵敏的监控管理,制定合理的异常情况应对策略。
4.2 电池热学信息确定
任何方案的设计都需要先明确输入信息或限制条件,其中最基础的、必不可少的信息有如下三类:
1. 电池自身的发热速率:热管理方案的原理是通过一定手段将电池发出的热量转移到合适的位置来控制电池温度,电池发热速率决定管理方案的热量转移效率要求;
2. 电池的温度要求:不同电池对温度敏感性不同,而温度是热管理系统控制的核心参数。
3. 电池的热物理性质:在相同的产热速率和热管理方案下,电池本身的导热系数、密度和比热容等电池热物性参数对电池温度表现有巨大影响。
电池热管理系统的设计,实际所用到的热设计知识,与常规电子产品如服务器、电源等产品并无本质差异,仍需要从热传导、对流换热、辐射换热三个角度考量合理的热管理方式。4.2.1 电池发热速率
锂离子电池在充放电循环过程中伴随有各种热量的吸收或产生,并导致其内部温度发生变化。这些热量包括由化学反应熵变产生的可逆热Qr,电极因极化产生的极化热Qp,因电阻产生的焦耳热Qj,电池本身因温度升高而吸收的热量Qab,电池内部因发生副反应所产生的热量Qs等[8]。
上述各吸热和放热部分,可以使用如下公式示意性描述:
电池总的产热量:Q = Qr Qp Qs Qj Qab
有的研究将电池的极化热与焦耳热之和等效为由于电池的全内阻带来的热量,而电池的全内阻则可以通过仪器测定。某些情况下,为细化内部热量分布,还可以使用仪器测量电池的欧姆电阻,欧姆电阻即为焦耳热Qj的产生来源[9]。电池的发热速率不是一个固定值。动力电池充放电过程中,电池内部化学反应复杂。热量的产生与电池的类型、充放电速率和工作温度都直接相关,产热机理影响因素的复杂性使得很难直接使用数值方法对电池的发热速率进行模拟计算。下图是50℃工作环境温度下某LiFePO4锂离子电池在1C充放电时电压和热流随时间的变化曲线[8],可见其综合热流密度随时间变化的复杂程度。表格中对比的该电池在不同放电倍率、不同工作温度下的发热量,亦表现出极大不同[4]。图16-41 50℃工作环境温度下CR2025型LiFePO4锂离子电池在1C充放电时电压和热流随时间的变化曲线[8]
表16-8 不同工作环境温度下CR2025型LiFePO4锂离子电池在不同放电倍率下产热量对比(负号表示放出热量)[8]
上述图表仅表述的是LiFePO4锂离子电池的相关实测数据,当电池类型变更,电池的放热特点又有不同。目前,通常采用的研究方法是实验与数值模拟相结合:首先使用试验方法测量典型电池在某些典型温度、不同充放电速率下的产热速率,获得的测试数据通过拟合物理控制方程得出等效的反应热参数,将这些反应热参数加载到数值模拟的模型中,模拟电池在温度连续变化时的电池发热速率。在电池组热管理方案设计过程中,也可以使用数值模拟来预先查看设计效果。需要注意的是,当细致地研究单体电池在充放电过程中电池随温度的实时变化时,简单地将电池的发热速率设定为一个固定值,可能造成模拟结果或理论计算结果有很大误差。当然,这种简单等效仍可以用来定性地对比不同热管理方案的优劣。4.2.2 电池导热系数、密度和比热容
在系统方案设计时,必须考虑电池的导热系数、密度以及比热容。其中:
· 密度:可以通过测试电池体积和质量,根据密度的定义直接获得;
· 比热容:可以通过测试将电池温度升高特定的温度值,测量所需的热量获取;
· 导热系数:导热系数是矢量,由于电池由多种材质组合而成,在不同方向和不同位置处,导热系数不尽相同。导热系数的确定,需要获得电池内部的详细成分构成及对应的几何尺寸参数,通过当量导热系数的计算公式分别获取。
下表为中航锂电70A.h磷酸铁锂动力电池的当量热物理参数和内部相应的内部组成材料属性。
表16-9 中航锂电70A.h磷酸铁锂动力电池热物理参数[8]
除了使用热物理测试,还可通过确定电池中各组分所占用的比例,以及各组分的物理特性采用加权平均的方式计算得出电池的等效导热系数、比热容等参数[10]。4.2.3 电池的最优工作温度
1) 高温运行环境中;
2) 快速充电时;
3) 需要快速放电的驾驶过程中;
4) 低温情境下的充放电过程中。
其中前三种需要降温,最后一种需要加热。不同电池的理想工作温度区间是不同的。在进行电池热管理系统设计之前,需要明确电池的最优工作温度范围。电池热管理系统最关键的目标就是在汽车所有运行状态下都保证电池温度位于这些合理的工作温度区间内。在当前工艺技术水平下(2018年),Ni-MH电池的最佳工作温度范围为20~40℃,极限为-20~60℃;铅酸电池最佳工作温度范围为25~45℃[6],极限为-20~60℃。磷酸铁锂电池的工作电压区间在2.0~3.65 V(三元电池的工作电压区间在2.75~4.2 V),放电工作温度为 -20 ~ 55℃,充电温度为0 ~ 45℃。需要注意的是,温度区间的确定必须要和电池的工艺技术水平和所要求的使用寿命关联起来确定。目标温度区间除了决定电池包中冷板、风扇等具体结构件的设计,其上下限值还是设计电池热管理系统自动控制策略的重要参考本书第一章概括过电子产品热问题的内外两个解决思路。电池的热问题也与之相同:向内提升电池本身技术工艺,即电池能量密度更大,能量转化效率更高,相同尺寸的电池储能更多,且输出功率相同的情况下发热速率更小,材质适应的温度范围更广;向外则是电池热管理系统的设计,通过自然散热、强迫风冷或者液体冷却等外部措施控制电池包的温度。本书重点解读后者。此处将电池的热管理按照风冷散热、液冷散热和相变冷却三种类型来描述。4.3.1 风冷散热
风冷散热相对来讲是比较原始的电池热管理方案,由于效率低下,目前高续航的纯电动汽车已经极少使用。电池包自身的自然散热设计所使用的优化手段与3C电子产品完全相同,详细可参考本章第一节内容。其差异之处在于电池包和整车空间位置的协调。当使用自然散热方案时,将电池包置于通风、远离其它发热体的车体部位对电池温度表现直观重要。图16-42 串联和并联风道
类似的,强迫风冷设计的电池包也是如此,其采用的散热优化手段可以参考本章第二节内容。强迫风冷设计的电池包,风道的设计几乎演变成电池包内电池的排布形式和箱体进出风口形态和相对位置的设计。由于电池本身发热速率的复杂多变性,目前多数强迫风冷设计的方案中,电池的排布仍严重依靠实际测试确定。常见的电池包中过风形式有串联和并联两种。串联设计的风道,冷风在电池包内在前进的过程中温度逐渐升高,致使处于下风向的电池温度偏高,从而导致电池包内电池的温度不均匀性较大。而并联风道可以较好地规避这一点。也有实验表明,并联风道的设计,更有利于形成均匀的温度场。综上所述,在风冷散热中,除去拓展散热面积、高导热材料的选择、高性能风扇的选择等常规强化散热措施,电池的安装位置和风道形式是关键设计点。4.3.2 液冷散热
随着电池功率密度的提升,空气为热载体的热管理方式已逐渐无法满足温度控制的要求。液冷散热的高效移热及强大的均热能力,使其日渐成为动力电池包热管理的首选方案。下图描述了几种典型的液冷方式。图16-43 液冷电池热管理的几种形式[11]
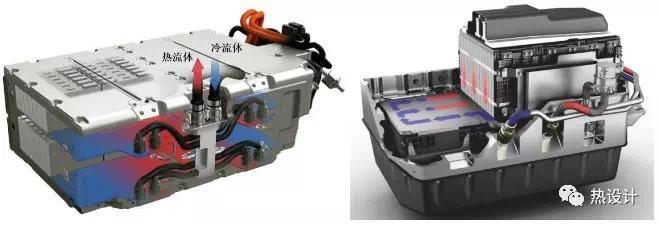
图16-44 电池包液冷散热示意图(左:Panamera S E-hybrid;右:特斯拉Model S)
对于间接液冷的电池包,传热介质可以采用水和乙二醇的混合液或者低沸点的制冷剂。电池包中,冷板与电池之间的导热衬垫除了有降低接触热阻的功能,同时还应充当缓震、绝缘和阻燃作用。液冷方案的电池包还可以和车体的发动机制冷液或车载空调进行连接,形成整车级的综合热设计方案。空调制冷方式原理示意图如下图所示。
图16-45 空调制冷式电池热管理系统原理简图
把模块沉浸在电介质的液体中的直接液冷方案,介质必须绝缘,以免发生短路。出于价格考虑,硅油是当前重点考虑的液体绝缘冷却介质。除了冷却效应,使用硅油直接冷却还可以起到很好的阻燃作用,避免汽车在出现事故时由于电池局部高温而发生爆燃。浸没式冷却虽然效率高且控制得当时更加安全,但由于本书第四章所述的缺陷,目前尚未规模化商用。液冷设计的动力电池与常规3C产品方法并无本质区别。其使用的优化设计方法如流道设计、流量确定、冷板材质选择、流动截面形状设计等基本相通。4.3.3 相变冷却
电池对温度的敏感性很容易令人与与相变材料(Phase Change Material, PCM)对热量产生的温度反应连接起来。PCM的特征是在极小的温度变化范围内可以收大量热,在需要维持恒温的设备中经常使用(如保暖服装,电器防热外壳、保鲜盒、保温盒、取暖器、储能炊具等[12])。利用PCM 进行电池冷却原理是:当电池进行大电流放电时,电池释放大量热,PCM 吸收电池放出的热量,自身发生相变,而维持电池在相变温度附近。此过程是系统把热量以相变热的形式储存在PCM 中。当电池温度下降到PCM 熔点以下时,相变材料又可以释放自身能量,维持电池温度。通过材料的相变化可以经济地将电池温度控制在合理范围内。通过冷却原理可以清楚地看到,PCM的相变潜热和相变温度是其在电池热管理中应当考量的关键因素(密度、毒性、价格等传统因素当然也很重要)。理论上讲,当PCM的体积潜热足够大时,电池甚至只需要被包裹在PCM中就可保证温度适中(运行间歇较长且可能置于寒冷环境中的车型,需要加热部件以保证冷启动)。没有了运动部件和占据大量空间的换热器、冷板管路等部件,其可靠性、紧凑性和装配难度显然极具优势。动力电池的最佳工作温度是一个范围,当动力电池温度过低时,电池的容量和寿命会极大衰减。可能的原因包括电解液受冻凝固等[2]。在低温时,由于电池的活性差,电池负极石墨的嵌入能力下降,这时大电流充电很可能出现电池热失控甚至安全事故。一般而言,加热系统是为了满足在低温环境下能够使电池能正常使用。加热系统主要由加热元件和电路组成,其中加热元件是最重要的部分。常见的加热元件有可变电阻加热元件和恒定电阻加热元件,前者通常称为PTC(positive temperature coefficient)(图-16-46),后者则是通常由金属加热丝组成的加热膜(图-16-47),譬如硅胶加热膜、挠性电加热膜等。
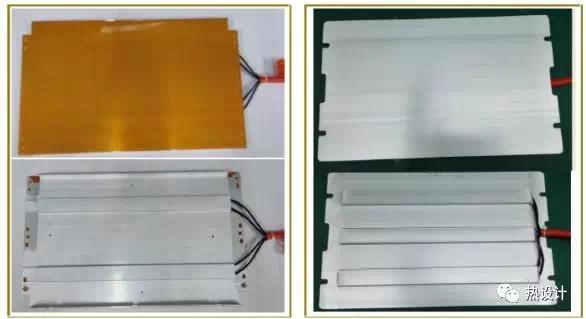
图16-46 平板式PTC加热器
PTC由于使用安全、热转换效率高、升温迅速、无明火、自动恒温等特点而被广泛使用。其成本较低,对于目前价格较高的动力电池来说,是一个有利的因素。但是PTC的加热件体积较大,会占据电池系统内部较大的空间。
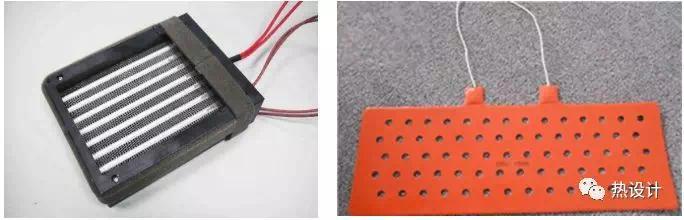
图16-47硅胶加热膜、挠性电加热膜
绝缘挠性电加热膜是另一种加热器,它可以根据工件的任意形状弯曲,确保与工件紧密接触,保证最大的热能传递。硅胶加热膜是具有传统金属加热器无法比拟的柔软性的薄形面发热体。但其需与被加热物体完全密切接触,其安全性要比PTC差些。加热膜另一明显缺点是电池被加热温度较难控制。动力电池能量密度和成本是电池包最关注的指标。2016年4月,工业和信息化部、国家发展改革委、科技部联合印发了《汽车产业中长期发展规划》。规划的新能源领域的阶段性目标是:(1)到2020年,锂离子动力电池单体比能量〉300Wh/kg;系统比能量争取达到260Wh/kg;成本<1元/瓦时.(2)到2025年,新能源汽车占汽车产销20%以上,动力电池系统比能量达到350 Wh/kg。同年发布的《节能与新能源汽车技术路线图》也提到了纯电动汽车动力电池的比能量目标是2020年350Wh/kg, 2025年是400Wh/kg, 2030年是500Wh/kg。动力电池管理系统中,冷板、液体工质、换热器、导热界面材料、泵、加热片等都属于热设计的直接控制范畴,其重量可能占到整个电池包的30%甚至更多,电池包中热管理相关物料重量的考量和对产品竞争力的影响比常规的3C产品要明显得多。热设计师在充分关注温度的同时,必须严格把握热管理系统所占用的空间和重量,确保整体设计的合理性。
参考文献(全部)
[1] 柏立战, 林贵平, 张红星. 环路热管稳态建模及运行特性分析[J]. 北京航空航天大学学报, 2006, 32(8):894-898.
[2] IEC GUIDE 117 -- Electrotechnical equipment – Temperatures of touchable hot surfaces Appendix A, 2010.
[3] Tang, Heng, Tang, et al. Review of applications and developments of ultra-thin micro heat pipes for electronic cooling[J]. Applied Energy, 2018, 223:383-400.
[4] 张炯.4G/5G 融合,促进网络演进发展.https://www.zte.com.cn
[5] 中兴通讯.中兴通讯5G高频基站产品荣获2017中国设计红星奖.
http://www.sohu.com/
[6] 饶中浩, 张国庆. 电池热管理[M]. 北京: 科学出版社,2015;
[7] Ramadass P., Haran B., White R., et al. Capacity fade of Sony 18650 cells cycled at
elevated temperatures Part II. Capacity fade an alysis[J]. Journal of Power Sources, 2002,
112(2): 614-620.
[8] 宋刘斌. 锂离子电池(LPF)的热电化学研究及其电极材料的计算与模拟.中南大学博士学位论文.2013;
[9] 梁金华. 纯电动车用磷酸铁锂电池组散热研究. 清华大学硕士学位论文. 2011.
[10] 云凤玲;高比能量锂离子动力电池热性能及电化学-热耦合行为的研究[D];北京有色金属研究总院;2016年
[11] Pesaran A. Battery Thermal Management in EV and HEVs:Issues and Solutions [J]. Battery Man, 2001, 43(5): 34-49.
[12] 陈爱英, 汪学英. 相变储能材料及其应用[J]. 洛阳理工学院学报(自然科学版), 2002, 12(4):7-9.
作者简介:陈继良,仿真秀专栏作者,文章节选自机械工业出版社发行,陈继良老师编著的《从零开始学散热》,点击可订购。