案例分享 | 戴姆勒公司利用 MSC Nastran 将产品开发周期缩短10倍
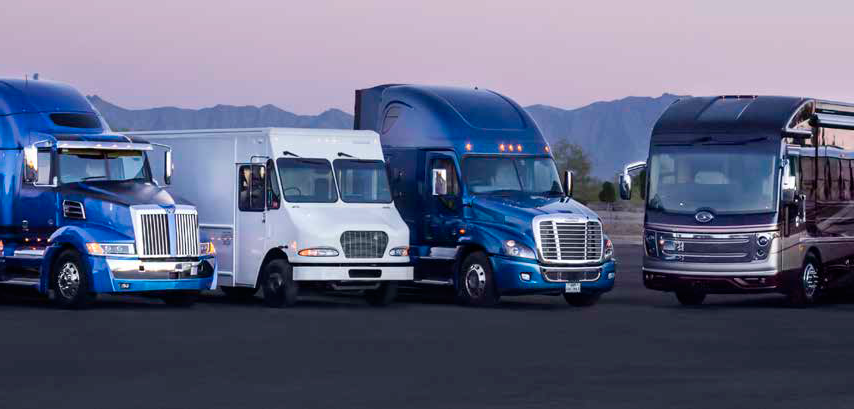
戴姆勒公司制造并销售商用卡车和客车,并提供售后服务和维护。戴姆勒追求效率和创新,公司的北美开发团队正在将计算机辅助工程(CAE)技术应用于汽车开发过程,帮助公司实现这些目标。
制造商研发的汽车需要能够安全运输有效载荷,同时车辆的重量减轻,使用过程中必须确保高燃油效率和减少相关的排放。戴姆勒公司在设计和开发周期的早期阶段就可以预测车辆的疲劳寿命,从而延长产品寿命,减少测试和制作物理样机的投入,最终缩短产品上市的时间。MSC Nastran是耐久性分析工作流程中进行有限元分析的关键软件。我们的团队选择MSC Nastran是因为进行了市场评估后发现其性能始终比竞争对手的有限元软件产品速度快10倍。为了通过使用复杂的弹性轮胎模型和3D道路轮廓来精确复现衬套的动态、非线性性能并捕获道路输入,首先进行多体仿真。根据车辆类型和目标客户群使用不同的占比(例如,公路vs极端负荷应用),物理测试程序的所有耐久性事件均根据占比进行了全长的模拟。
图1. 戴姆勒公司的耐久性分析工作流程
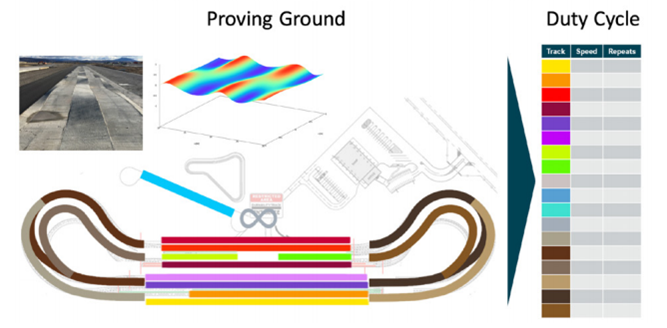
图2. 根据占比模拟物理测试的所有耐久性事件
MSC Nastran中使用有限元方法来计算车辆底部结构(如底盘,驾驶室,引擎盖)中的应力分布。MSC Nastran在有限元仿真中,通过从多体仿真中获取的载荷,在所有界面位置都激励 子结构。有限元分析的应力结果被用于计算每个金属部件和所选塑料部件的损伤。最后,获得整个工作周期的综合损伤分布以及每个耐久性事件的损伤贡献度。特定结构的有限元分析分两个步骤进行。首先,进行常规模态分析,以计算实模态值、残差矢量补偿和模态应力。除了通常的结果数据外,我们还保留MASTER / DBALL和IFPDAT文件。对于特定模型,必须执行一次该分析。第二步,对每个耐久性事件都进行瞬态模态分析,并在第一步模态分析基础上进行“重启动”分析。“重启动”是从上一轮继续运行而不必从头开始的分析方法。在动态分析中,就计算时间和成本而言,模态分析的计算通常是最“昂贵”的操作。使用重启选项,不必为每个耐久性事件重新模态分析计算。这不仅节省了计算时间,而且确保了模态分析的模态振型和多个耐久性事件的参与因子之间的一致性。 第二步的主要结果是计算每个耐久性事件的模态参与因子。此外,还导出了应用于有限元模型的界面载荷以及选定节点的位移。界面载荷和节点位移被用来根据所施加的界面载荷来动画随时间而变化的变形。一旦完成了瞬态响应分析,将使用MSC Nastran的结果,通过nCode中模态应力和参与因子的叠加来得出应力时间历程。对于每个耐久性事件,都会对金属零件进行E-N分析,对塑料零件进行S-N分析。通过这些分析,可以根据占比实现对组合疲劳损伤的准确预测。这样就完成了我们的工作流程。图 3. 卡车子结构-来自MBS仿真的输入载荷
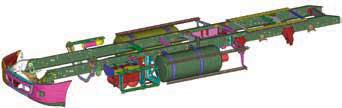
图 4. 来自MBS仿真的带有输入载荷的子结构模拟
使用MSC Nastran和其他有限元求解器的求解时间对比
当比较使用MSC Nastran和行业竞争对手的有限元求解器进行常规模式分析的求解时间时,我们可以看到MSC Nastran可以在5小时内求解模型,而我们以前使用的有限元分析产品在使用相同的机器环境进行相同分析的情况下要花50多个小时才能完成。使用MSC Nastran,常规模态分析(SOL 103)的速度快了10倍。我们使用以前的有限元求解器时,性能问题主要与二阶实体单元的模态应力计算有关。整车的验证包括对底盘、驾驶室和引擎盖结构的分析。通过使用MSC Nastran进行这些分析,将总分析时间减少了几天。因此,使用MSC Nastran求解器对于进行耐久性分析是至关重要的。
上面已概述了戴姆勒公司的耐久性分析工作流程。耐久性过程分析使得我们能够更有效地识别大应力的位置。戴姆勒公司的团队发现整个过程比以前的方法快近十倍。中间文件越来越少,数据管理也变得更加简单。戴姆勒公司的团队已经基于几个参数成功验证了该方法,并且与物理测试数据表现出良好的相关性。戴姆勒公司的团队发现在不久的将来有很多机会运行类似的仿真。MSC强大的MSC Nastran求解器软件和拥有来自现场团队的持续支持以及对开发的持续投资,这将在简化和加快耐久性分析方面产生了重大影响。