万字长文 | 面向航天器在轨装配的数字孪生技术
来源:北京卫星制造厂、北京理工大学
作者:张玉良、张佳朋等
构建航天器在轨维修维护能力是确保空间系统长期稳定工作的有效途径,而对于空间环境中的在轨装配过程的模拟、监控、诊断和预判,目前的研究尚处于探索阶段,研究成果相对较少且缺乏整体解决方案。
提出采用构建航天器数字孪生体的方式,来抽象表达航天器完成在轨装配的过程、状态和行为。首先分析了在轨装配航天器的结构组成及功能需求, 然后系统阐述了航天器数字孪生体的数据组成、实现方式和作用,最后给出了航天器数字孪生体在设计、制造和在轨服务阶段的实施途径,并对航天器数字孪生体的作用进行了总结和展望
关键词:在轨装配;数字孪生体 ;航天器;产品全生命周期管理
01引言
随着航天技术的飞速发展,空间飞行器的结构、组成日趋复杂,性能、技术水平不断提高,在这种情况下,保证空间飞行器在复杂的空间环境中更加持久、稳定地在轨运行,成为目前空间技术领域亟待解决的重要问题。
传统的航天器研制体系是在地面完成航天器结构研制生产、总装和测试,再通过运载火箭运送航天器进入预定轨道,最后由航天器进行轨道转移、 姿态调整。传统研制体系下,航天器需要在地面安装调试到位,确保“在轨零故障”, 发射前需要携带全生命周期所需燃料,而且缺乏对于空间碎片的主动防护能力。
针对上述存在的问题,国内外均开展了利用在轨装配技术在空间环境中对目标进行绯护和操作的相关研究,通过在轨装配技术可以很好地韶决传统航天器研制体系面临的困难,确保空间系统长期稳定工作,目前巳成为新的研究方向。为解决上述难题,航天器在轨装配需要解决在轨维护、在轨加注和在轨防护3方面的功能需求:
1 )实现在轨维修维护。目前由于缺乏在轨维修维护能力,当航天器发生机构展开失利、部组件失效等故障时,往往导致整个航天器失效。所以,“在轨零故障” 是空间系统设计和研制的理想目标,并且在整个航天器研制生产流程中不懈贯彻严格的质量管理,但是受制于航天 产品固有的系统复杂性、空间运行环境的苛刻性以及成本周期的限制性,以一定概率发生在轨故障很难避免。通过在轨装配技术构建在轨维修维护能力,可以解决由于部组件故障导致航天器失效的问题,确保空间系统长期稳定工作。2) 实现在轨加注功能。目前低轨卫星寿命一般为3年~8年,高轨卫星为8年~ 15年。随着空间电子技术水平的不断提高和卫星平台日趋成熟,卫星所携带燃料不足已经成为制约卫 星寿命的主要因素。预计至 2022 年, 约有 203 颗 GEO 卫星在轨需要燃料补给,包括150颗商业卫 星和53颗军事卫星。对卫星实现在轨燃料补给,以相对低的代价,快速使卫星的任务能力得以延续,使卫星的工作寿命得到大幅提高。3)实现空间防护功能。空间轨道资源极为宝贵,随着人类空间活动日益频繁,空间碎片急剧增加,滞留在重要轨道(如GEO) 上的废弃卫星已成为正常在轨运行航天器的严重威胁。目前, 毫米级以上的空间碎片数以亿计,5cm- 10cm的已编目空间碎片在轨总数接近 17000 个,仅GEO带内(GEO±200km ) 废弃卫星数量超过330颗,约占GEO带飞行器总数的 44%。这些碎片已对正常在轨航天器构成严重威胁,对于上述非合作目标的捕获,不仅可以实现废弃航天器关键部件的重用,也可以大大提高航天器在轨运行安全。综上所述,利用在轨装配技术在空间环境中对目标进行维护和操作,可以很好解决传统航天器研制模式面临的困难,实现在轨装配的关键是解决空间无人环境中的在轨装配过程的模拟和预测,确保在轨装配任务可以顺利实施。针对这些问题,各国研究机构进行了一系列地面、空间论证实验和应用研究。首先是构建在轨产品的“孪生体/双胞胎(twins)”, 如美国国家航空航天局NASA 的阿波罗项目[1]。在该项目中,NASA需要制造两个完全一样的空间飞行器,被留在地球上的飞行器被称为孪生体(twin),被用来反映(或作镜像)正在执行任务的空间飞行器的状态/状况。其次是模拟空间在轨环境,斯坦福大学利用气浮轴承支撑起实验样机模拟微重力环境,马里兰大学为空间机器人Ranger研制的地面试验系统为水浮式验证系统,如图1所示。随着数字化技术的发展,孪生体不再局限于物理产品,开始向虚拟数字化方向发展。2012年,美国空军研究实验室提出了“机体数字孪生体”的概念[2]:机体数字孪生体作为正在制造和维护的机体的超写实模型,是可以用来对机体是否满足任务条件进行模拟和判断的,由许多子模型组成的集成模型。2017年,为实现制造车间物理世界与信息世界的交互融合,陶飞等[3]提出了数字孪生车间的实现模式,并明确了其系统组成、运行机制、特点和关键技术,为制造车间信息物理系统的实现提供了理论和方法参考。综上所述,对于在轨装配过程的验证,研究成果主要集中在物理孪生体方面,数字孪生技术尚处于探索阶段,针对航天器在轨装配的数字孪生技术未见报道。为了实现航天器在轨装配全过程模拟、状态监控以及装配结果预测,本文在分析在轨装配航天器结构组成及功能需求分析的基础上,提出了构建航天器数字孪生体的方式来虚拟表达在轨操作过程和结果预测。首先重点分析了面向在轨装 配的数字孪生体技术路线,然后给出了构建航天器数字孪生体的体系结构,最后提出了航天器数字孪生体在全生命周期各阶段实施途径。在轨装配航天器是一种新概念的航天器,它既具备一般航天器必须的各种分系统,又有适合于执行在轨维修维护、在轨加注以及空间防护功能的特殊装备。与一般航天器系统相比,在轨装配航天器的显著特点是载荷设备更多样,功能更复杂,智能化水平更高,机动性更好。按照各分系统功能的不同,在轨装配航天器的组成分为平台和载荷两部分,如图2所示。平台主要包括为载荷提供支持的保障分系统,为在轨扩展航天器提供能源、温控和通信保障 等。平台主要由结构与机构、热控、电源、姿态与轨道控制、推进、测控、数据管理、总体电路等分系统组成。载荷包括用于执行在轨服务操作的各种设备,如可灵活操控的机械臂、远程观测设备、测距设备、服务对象所需的补给品和 ORU 等,可分为空间目标识别和探测分系统、对接机构分系统、机 械臂及其控制分系统、补给品及其存储管理分系统等。1)空间目标识别和探测分系统用于在一定范围内对服务对象进行搜索、捕获、跟踪、测量, 为实现其他服务操作提供前提。其支撑技术预计后续开展。
2)对接机构分系统用于实现在轨扩展航天器与服务对象的连接和分离操作,大部分服务任务都需要用到对接机构来实现在轨扩展航天器与目标间的刚性或柔 性连接。对接机构一般包括传动缓冲、捕获、连接密封、结构与附件以及控制等子系统,其支撑技术为本课题重点验证部分。
3)机械臂/手及其控制系统用于完成复杂的在轨服务操作,如在轨装配、在轨维修、在轨模块更换等。在轨扩展航天器是机器人技术与航天器技术相结合的产物,机械臂/手的使用是在轨扩展航天器区别于其他航天器的明显特征,其支撑技术预计后续开展。
4)补给品及其储存管理分系统用于储存和管理燃料和ORU等补给品,精确记录补给品的用扯、库存撮,配合其他系统完成在轨加注和在轨模块更换任务。
03面向在轨装配的数字孪生体技术内涵
为了完成在轨装配的过程模拟和结果预测,需要构建与物理产品等价的虚拟数字化表达,抽 象表达真实装置,并可以此为基础进行真实条件或模拟条件下的测试。首先,需要构建在轨装配航天器的数字孪生体。该数字孪生体概念模型如图3所示,包括3个主要部分:1)物理空间的航天器实体;2)虚拟空间的虚拟航天器 ;3)物理空间和虚拟空间之间的数据和信息交互接口。航天器数字孪生体是反应航天器制造过程和执行任务过程的超写实模型,可以对航天器是否满足在轨装配任务条件进行模拟和判断的,由许多子模型组成的集成模型。以航天器舱体数 字孪生体为例,其组成元素如图4所示。航天器舱体数字孪生体是舱体在整个产品生命周期的一致性模型和计算模型,它与制造和维护航天器所用的材料、制造规范及流程相关联。它也是航天器数字孪生体的子模型,其中航天器数字孪生体是一个包含电源系统模型、热控系统模型、控制系统模型、推进系统模型和其他子系统模型的集成模型。所以,在轨装配航天器的数字孪生体应具有多种特性,主要包括:虚拟性、唯一性、多物理性、多尺度性、层次性、集成性、动态性、超写实性、可计算性、概率性和多学科性。综上所述,构建航天器数字孪生体的基本内涵主要包括以下几方面:1)要具备层次性和集成性,例如航天器数字孪生体、舱体数字孪生体、机构运动模型、结构模型、材料状态演化模型等,有利于数字孪生体的逐步实施及最终实现;
2)要具备超写实性,包括航天器几何模型、多敏感信息融合与处理模型、运动机构及气液传 输物理模型、材料演化模型等;
3)数字孪生体要具备广泛性,即包括整个产品全生命周期,并从设计阶段延伸至后续的产品制造阶段和产品服务阶段。
4)数字孪生体要具备可计算性, 可以通过仿真和分析来实时反映对应产品实体的真实状态。
04航天器数字孪生体的数据组成及构建途径
目前,国内外对航天器数字孪生体的研究成果较少。本文从航天器研制到在轨服务的全生命周期,分析了航天器数字孪生体的数据组成、实现方式、作用及目标,提出了航天器数字孪生体的体系结构。航天器数字孪生体远远超出了数字样机的范畴,除了表达几何信息和功能信息外,还包含了航天器研制过程和在轨服务状态的描述信息。同时,产品数字孪生体是一个过程模型和动态模型,会随着航天器研制和服务过程数据的产生而不断演化和增加。考虑到数字孪生体数据的不断演化和增加的特点,本文提出基于航天器全生命周期的阶段进行数字孪生体组成数据的划分,组成航天器数字孪生体的数据主要包括:设计数据、工艺过程数据、制造过程数据和在轨服务过程数据。1)设计数据:包括航天器三维模型(表达几何形状信息几何数据),属性数据(表达产品原材料、规范、分析数据、测试需求),三维标注数据(表达产品尺寸与公差),包含航天器各部组件间装配关系的设计BOM, 以及设计文档。
2)工艺设计数据:包括工艺过程模型(毛蚽模型、每道工序的工序模型),工序设计数据(加 特征信息、制造资源信息、加工方法、工艺参数信息),质量控制数据(检验/测量要求信息、关键/重要工序质量控制要求信息),工艺仿真数据(几何仿真、物理仿真、焊接仿真、装配过程仿真),工装设计数据。
3)制造过程数据:包括制造BOM、检测数据、技术状态数据、生产进度数据、工装数据、质量信息数据、生产环境数据、工艺装备数据。
4)在轨服务数据:包括在轨操作动作数据、过程监控数据、健康预测数据、多敏感器采集和分析数据等。
基于上述航天器数字孪生体的数据组成分析,本文针对航天器设计、制造和在轨服务3个阶段分别提出了数字孪生体的实现方式。在航天器设计阶段,为了构建产品数字孪生体,首先需要用一个集成的三维实体模型来完整表达产品定义信息,基于模型的定义 (Model Based Definition , MBD) 技术是解决这一难题的有效途径。该技术以模型为核心实现产品研制全过程一致性、关联性和共享,解决了工程数字化与管理信息化紧密关联纽带,使得产品的定义数据能够驱动整个制造过程下游的各个环节。具体实现过程如下:①有序规划设计阶段数字孪生体的体系结构。将上述设计数据中的所有信息进行分类管理和显示,将信息按照各种需求分类,形成信息的各种描述形式,如设计描述、工艺描述、制造描述、检验描述、维护描述和协作描述等。提出将航天器数字孪生体分为构型层、舱段层、布局层和总装层4层模型,并规定每层模型包含的数据内容和接口,既保证数据模型轻量化又保证数 据利用效率。
②构建一个全三维标注的产品模型,包括一维模型的设计信息、技术要求、尺寸公差以及工艺信息的规范化表达。将设计要求、工艺技术要求、尺寸与公差、材料特性、检验要求等统一表达在三维设计模型中,依据三维标注的国家标准,建立三维标注模板,实现基于三维的规范化标注,标注效果如图 5 所示。
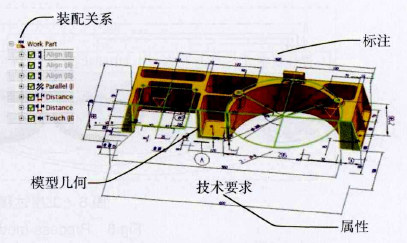
图 5 全三维标注的产品模型示意
③进行基于设计模型的可制造型评价。根据结构件加工精度要求,对三维设计模型进行工艺性审查,实现模型的可装夹性、可加工性、可焊接性、可装配性的全面评估,建立工艺能力约束集合,发现设计中的缺陷,并及时反馈和更改,实现设计数据与可制造性工艺数据的快速交互,缩短设计制造过程的迭代周期。
在航天器制造阶段, 航天器数字孪生体的演化和完善是通过与产品实体的不断交互开展的。因此,如何实现航天器制造过程数据的实时准确 采集、有效信息提取与可靠传输是实现数字孪生体的前提条件。随着物联网、工业互联网技术的不断发展和完善, 为信息获取提供 了技术保障。在制造阶段,构建数字化孪生体的方式如下:①构建面向数字孪生体的制造工艺体系。首先将以3PR (Prod uct-Process -Plant-Res ource) 数据构架的产品、工艺、工厂、制造资源整合成一个统一的LDA (Lifecycle Data Architecture) 数据模型,形成企业单一的数据源,保证数据的唯一性和准确性;再以结构化3D可视化的工艺形式进行工艺规划和3D工装设计,对于工艺/工序/工步数据、工装设备等生产资源数据、工厂/生产线/装配区等生产布局数据,通过集成PDM、MES、ERP 来实现物空间和虚拟空间下的数据协同。
②编制三维结构化工艺。基于产品BOM分解的每个零件节点均可分解为若干工艺,工艺可分解为若干工序,工序可分解若干工步。各级节点挂接工艺内容、所需要的工装、工具、检验标准、工艺过程模型等相关信息,形成工艺的结构化数据描述。对于三维结构化工艺的各项数据,均真实地反应实体产品的演化过程和最终状态,该演化过程同时在数字孪生体上 体现。以三维工艺中的工序过程模型为例,数字孪生体除了要体现零件从毛还到产品过程的几何信息变化外,还需体现切削力、切削 温度、切屑变化对产品的影响信息,如图 6 所示。
③实时采集实体空间的动态数据。针对制造资源(生产人员、仪器设备、工装工具、物料、AGV小车、托盘),结合产品生产现场的特点与需求,利用条码他术、RFID、传感器等物联网技术, 进行制造资源信息标识,对制造过程感知信息采集点进行设计,在生产车间构建 一个制造物联网络,实现对制造资源的实时感知,并将数据进行标准化封装,形成统一的数据服务,供其他环节调用。
④不断优化数字孪生体状态。通过制造工艺体系中的数据接口,将动态数据传输至统一数据源,并分发给相应数字化系统,实航天器数字孪生体的生成和不断更新。
航天器在轨服务阶段,需要完成在轨维修维护、在轨加注和空间防护任务,并且是在高度无 人环境下进行, 因此需要对航天器的 状态进行实时跟踪和监控, 包括航天器的空间姿态、空间环境、质量状况、使用状况、技术和功能状态等,并根据航天器实际状态、实时数据、使用和维护记录数据对航天器的健康状况、寿命、功能和性能进行预测与分析,并对执行任务情况进行提前预警。①多敏感器参数获取。在物理空间,在轨装配航天器需要采用物联网、传感技术、移动互联技术,通过多种敏感器获取与在轨装配任务相关的实测数据,包括测距仪信息、多目相机的目标识别信息、外部环境感知信息、力/位精细感知信息、气液传输信息等。将上述信息获取后,通过天地通信设备,将获取到的航天器全部信息传递至地面服务器,供数字孪生体进行相关数据提取。
②信息融合与评估。上述物理空间获取的信息,需要映射到虚拟空间的航天器数字孪生体中。在虚拟空间,采用模型可视化技术实现对物理产品使用过程的实时监控,并结合历史使用数据、历史维护数据等,采用动态Bayes、机器学习等数据挖掘方法和优化算法实现对产品模型、结构分析模型、热力学模 型、产品故障和寿命预测与分析模型的持续优化[4],进而通过数字孪生体完成航天在轨装配任务验证和结果预测,并用以制定物理空间中航天器的控制策略。
③持续优化与改进。需要指出的是,航天器数字孪生体是物理产品在虚拟空间的超现实模型, 始终存在拟实化程度的问题。所以要针对数字孪生体与物理空间产品之间的偏差不断进行修正,只有通过数据的不断积累,才能持续提高数字孪生体的拟实化程度。对于已发生的偏差, 采用追溯技术、仿真技术实现问题的快速定位、原因分析、解决方案的生成,并修正数字孪生体模型,以及其与物理产品之间的映射关系,既能保证数字孪生技术的不断推进,又能为后续任务执行提供数据支撑。
通过上述方法,完成航天器数字孪生体构建后,可以带来诸多好处。首先,可以对航天器在物理空间中的形成过程完成模拟、监 控、诊断、预测和控制;其次,可以推进航天器生命周期内各阶段的高效协同;最后,还可以进一步完善数字化的航天器全生命周期档案,为全过程质量追溯和产品研发的持续改进奠定数据基础[5-6]。模拟在轨任务执行:通过构建航天器数字孪生体,可以在执行在轨装配任务前,使用数字孪 生体在搭建的虚拟仿真环境中模拟执行任务过程,尽可能掌握航天器在轨服务的状态、行为、任务成功概率,以及在设计阶段未考虑到的问题。同时,可以通过改变虚拟环境的参数设计,模拟航天器在不同环境下的运行情况;通过改变在轨任务策略,模拟不同操作方式下对任务成功率、航天器寿命产生的影响。通过模拟为在轨任务内容确定、在轨任务策略制定以及面对异常情况的决策提供依据,并从实际使用端优化航天器设计。监控和诊断航天器制造和在轨服务过程:由航天器数字孪生体创建过程可知,在航天器制造以及在轨服务过程中,制造数据和在轨服务数据会实时地反映到数字孪生体中,数字孪生体可以动态实时地监控航天器研制过程和在轨服务过程,并将过程数据以数字化形式存储下来。所以,不论航天器在研制过程中或者在轨服务过程中发生故障,均可以通过数字孪生体中的监控数据和历史数据进行故障诊断和定位。预测和评估:在航天体制造阶段,通常会遇到各种非理想状态,如焊接变形导致轮廓度超差、应力释放导致平面度超差等,这时需要技术人员对非理想状态进行分析,并评估其对后续研制的影响。而通过构建航天器数字孪生体,可在虚拟空间中对非理想状态进行集成的模拟、仿真和验证,依托制造环节实时映射到数字孪生体中的检验和测量数据、关键技术状态参数等数据,实时预测和评估对后续研制任务的影响,并用以指导对非理想状态的决策。在航天器在轨服务阶段,通过航天器上的多敏感器,获取实时数据,包括负载、温度、应力、结构损伤程度以及外部环境,并将实测数据关联映射至航天器数字孪生体。基于已有的产品档案数据、基于物理属性的产品仿真和分析模型,实时准确地预测航天器实体的健康状况、剩余寿命、故障信息以及在轨任务的成功率等。与目前的三维数字化制造模式不同,通过构建航天器数字孪生体,可以在其全生命周期各阶段,将产品开发、产品制造、产品服务等各个环节数据在产品数字孪生体中进行关联映射。在此基础上,以产品数字孪生体为单一产品数据源,实现航天器各阶段的高效协同。同时,基于航天器数字孪生体技术,可实现对产品设计数据、产品制造数据和产品服务数据等产品全生命周期数据的可视化统一管理,并为产品全生命周期各阶段所涉及的各类人员(包括工程设计和分析人员、生产管理人员、操作人员、在轨服务指挥人员)提供统一的数据和模型接口服务。另外,Grieves[7]也 指出,数字孪生体的出现,使得企业能够在产品实物制造以前就在虚拟空间中模拟和仿真产品的开发、制造和使用过程,避免或减少了产品开发过程中存在的物理样机试制和测试过程,能够降低企业进行产品创新的成本、时间及风险,解决了企业开发新产品通常会面临的成本、时间和风险3大问题,极大地驱动了企业进行产品创新的动力。航天器数字孪生体是航天器全生命周期的数据中心,记录了航天器从概念设计直至报废的所有模型和数据,是物理产品在全生命周期的数字化档案,反映了产品在全生命周期各阶段的形成过程、状态和行为。航天器数字孪生体实时记录了航天器从出生到消亡的全过程,并且在航天器的各阶段都能够调用该阶段以前所有的模型和数据,在任何时刻、任何地点和任何阶段都是状态可视、行为可控、质量可追溯的。例如在航天器在轨服务阶段,当发生异常情况,之前地面验证试验未进行相关环境测试时,航天器数字孪生体在设计和制造阶段的所有数据和模型记录集合,能够在新环境下提供准确的模型和数据来源,并预测结果,为异常突发情况提供决策基础。
05结论
在轨装配是当前空间技术的一个新的方向,它提供了一种新的航天器研制模式,拥有这项技术可对空间的故障飞行器实现在轨修理,而不是重新发射予以替代。通过维护和对载荷升级,可有效延长空间飞行器的使用寿命,增强其系统能力。此外,在轨服务技术也能够实现空间防护,大幅提高航天器在轨稳定性。目前,各国研究机构均投入了大量的技术力量进行相关技术研究, 而在轨装配的地面验证技术则是影响在轨任务成败的最关键环节。目前,航天器数字孪生体的构建和应用还处于初级阶段,仍需解决多项问题。同时,数字孪生体主要在设计阶段应用,在产品服务阶段的应用较少。因此,通过梳理面向在轨装配的航天器数字孪生体的数据组成,研究各阶段航天器数字孪生体的构建方式,不断优化数字孪生体和物理产品之间的映射关系,不仅为在轨装配任务的验证技术提供了一种新的技术手段,而且会因为大量数据的积累,不断推进在轨装配任务的技术水平,提高完成任务复杂程度。
[1] Rosen R, von Wichert G, Lo G, et al. About the impor tance of autonomy and digital twins for the future of manu facturing[J]. IFAC -Papers Online, 2015, 48(3) : 567- 572.[2] Tuegel E J. The airframe digital twin: some challenges torealization [ C]. AIAA/ ASME/ ASCE/ AHS/ ASC Structur es, Structural Dynamics and Materials Conference, 2012.[3] 陶飞,张萌,程江峰,等.数字孪生车间-一种未来车间运行新模式[J] .计算机集成制造系统, 2017, 23 (1) : 1-9.TAO Fei, ZHANG Meng, CHENG Jiang-feng, et. al. Digital twin workshop: a new paradigm for future workshop [J). Computer Integrated Manufacturing Systems, 2017, 23 (1): 1-9.[4] 范玉青.基于模型定义技术及其实施 [J] .航空制造技术, 2012, 402 (6): 42-47.FAN Yu-qing. Model based definition technology and its practices [ J). Aeronautical Manufacturing Technology, 2012, 402 (6) : 42-47.[5] 周济.智能制造一— "中国制造 2025" 的主攻方向[J].中国机械工程, 2015, 26 (17): 2273-2284.ZHOU Ji. Intelligent manufacturing- main direction of " made in China 2025" [J]. China Mechanical Engineer ing, 2015, 26 (17): 2273-2284.[6] 刘检华,孙连胜,张旭,等.三维数字化设计制造技术内涵及关键问题[J].计算机集成制造系统 , 2014 , 20 (3) : 494-504.LIU Jian-hua, SUN Lian-sheng, ZHANG Xu, et. al. Con notation and key problem of three-dimensional digital design and manufacturing technology[J]. Computer lnte grated Manufacturing Systems, 2014, 20 (3): 494-504.[7] Grieves M W. Product lifecycle management: the new paradigm for enterprises[J]. International Journal Product Development, 2005, 2 (1/2) : 71-84.[8] 庄存波,刘检华,熊辉,等.产品数字孪生体的内涵、体系结构及其发展趋势 [J] .计算机集成制造系统, 2017 , 23 (4) : 753-768.ZHUANG Cun-ho, LIU Jian-hua, XIONG Hui, et. al. Connotation, architecture and trends of product digital twin [ J]. Computer Integrated Manufacturing Systems, 2017, 23 (4) : 753-768.