前沿|航空结构件铣削加工变形仿真技术研究与应用
航空结构件以腹板、筋条、缘条组成的薄壁结构为主,具有结构复杂、刚性差等特点。薄壁结构件加工后存在材料毛坯初始残余应力及切削力、切削热相互耦合作用下产生的残余应力。当卸除装夹并充分冷却后,内部残余应力重新分布以达到新的平衡,导致薄壁零件加工后产生明显的整体弯曲、扭曲或弯扭组合变形,造成尺寸超差,加工精度难以保证等问题。近年来,随着计算机硬件能力的飞速提高和有限元理论的不断成熟,数值模拟方法逐渐应用到结构件加工变形预测中。国外发达工业国家,特别是美国和欧洲国家在航空航天和造船等领域已经大量采用了计算机模拟计算和分析技术。国内航空铣削加工领域也逐渐采用了计算机模拟技术 ,但主要是基于简化或缩比模型进行研究和应用,难以获得大型复杂结构件全加工路径下的仿真结果。针对航空结构件在加工中存在的变形问题,本文采用数值模拟的方法,以典型结构为例,探讨建立结构件加工变形仿真模型中材料本构方程建立、毛坯初始残余应力场构建、铣削载荷计算和施加、材料去除过程模拟、网格状态更新和应力释放等方法,并进行了试验验证。最后,对大尺寸航空结构件进行了加工变形仿真,并根据仿真结果,验证了工艺方案的可行性,实现了结构件的一次加工合格。以航空典型结构为例说明航空结构件加工变形有限元仿真建模过程,典型结构图1 所示,其中槽腔尺寸为 150mm×150mm×32mm,筋条、缘条和腹板的厚度均为 3mm,材料为 7B04 铝合金。
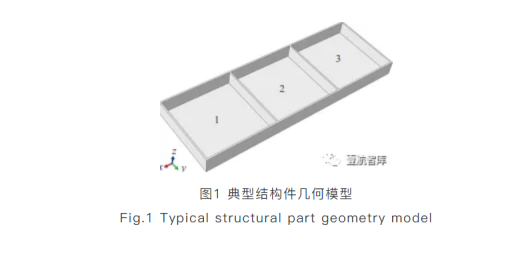
试验件工件材料为 7B04 铝合金,热处理状态为T7451,在金属切削有限元仿真中,常采用 Johnson–Cook 本构模型。在本次研究中,采用的网格去除方法没有包含材料的应变率硬化效应,因此 Johnson–Cook本构模型改写为:
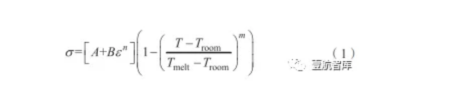
式中,σ 为流动应力;ε 为应变;T 为温度;Troom 为室温;Tmelt 为材料融化温度;A、B、n、m 分别为模型系数。进行压缩试验建立材料本构模型,压缩试样尺寸为φ20mm×10mm,取样方向为预拉伸板轧制方向,环境温度分别选取 25℃、100℃、150℃、200℃、250℃和 300℃,参考应变率为 0.001s–1, 压缩试验在 Gleeble– 1500 型模拟试验机上进行。图 2 为 7B04 铝合金准静态压缩试验的真实塑性应力 – 应变曲线,可以看到,室温环境下(25℃),7B04铝合金出现了典型的应变硬化现象,在屈服点附近没有出现平台现象,按照工程中屈服极限的计算方法,取 A=σ0.2,应变硬化参数 B 和 n 采用线性拟合的方法计算,根据试验结果可得:A=436.21MPa,B=184.5MPa,n=0.345。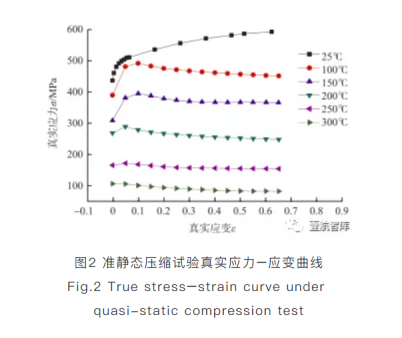
从图 2 可以看出,7B04 铝合金的应力随着环境温度的提高而降低,这说明材料发生了热软化现象。Johnson–Cook 模型热软化项参数 m 可根据不同环 境温度下的屈服应力拟合得到,忽略应变率硬化项 的影响,参数 m 由式(1)计算。根据高温压缩试验结果,绘制等效温度 ∆T 和参数 m 的曲线,如图 3 所示。可以看到,曲线符合指数函数,对试验数据进行拟合可得:
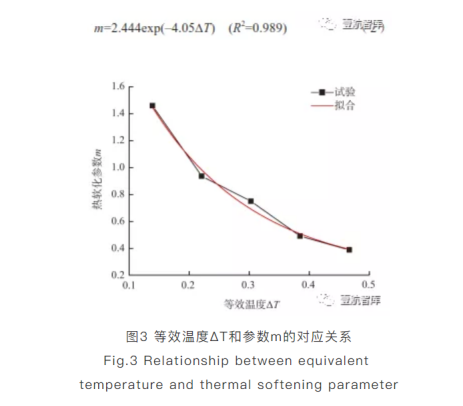
值得注意的是,图2 的 7B04 铝合金高温真实应力– 应变曲线中出现了应变软化现象,由于 Johnson–Cook模型不含有应变软化项,因此需要对模型进行修正。文献 [6–8] 表明,材料在高温下出现应变软化的原因为晶粒发生动态回复和再结晶。通过观察和对比应变软化曲线及相对常温曲线变化幅值,可以确定应变软化项同时受到应变和温度影响,应变软化项为:
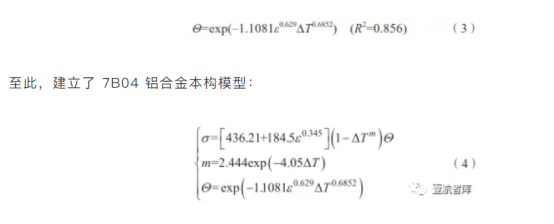
文献表明,毛坯初始残余应力对薄壁结构件铣削加工变形具有重要的影响,因此在有限元模拟时需要将残余应力作为初始条件加载到模型的网格单元积分点上,以提高仿真结果的精度。在本研究中,残余应力的测量使用剥层 XRD 法,其原理是将试样表面剥除一层后,会引起试件剩余部分的应力重新分布而产生变形。测量时取预拉伸板横截面,采用电解抛光方法去除取样影响层,按试样厚度方向分为 20 层,第 10 层为板中面,如图 4 所示。
利用 XRD 法测量出该层轧制方向和宽度方向的应力,实测的预拉伸板初始残余应力分布如图 5 所示。
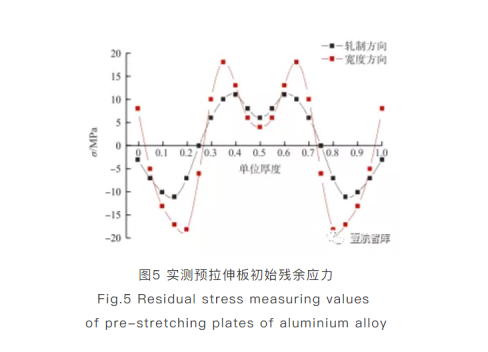
通过对毛坯进行残余应力测量,按照力平衡、力矩平衡的原则构建残余应力场,再将残余应力值插值到相应的单元积分点上,如图 6 所示。
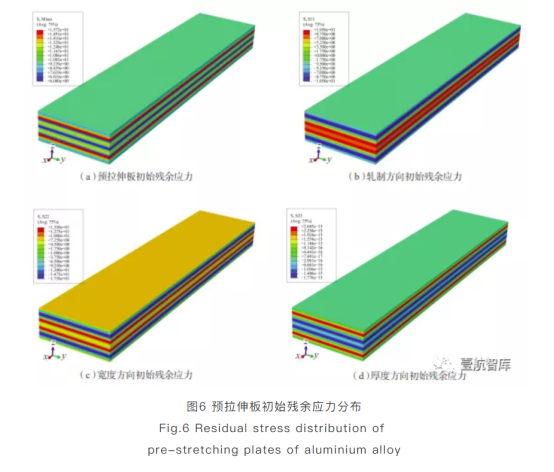
受计算机内存的限制,整体结构件的材料去除过程难以采用切屑成形方法,因此本研究采用单元生死技术实现材料的去除。单元生死技术通过对网格的刚度矩阵乘以或去除减缩因子,使网格实现失效或激活。失效的网格表现为相关单元载荷为零,同时其质量、阻尼、比热以及其他物理量也被置零,即单元不参与刚度矩阵的计算,其过程如图 7 所示。单元生死技术能够降低计算时间,同时保证较高的模拟精度,考虑到切削过程属于高度非线性的热力耦合过程,本次研究选用 ABAQUS/Standard 作为求解器模拟结构件铣削加工过程,网格选用三维六面体单元 C3D8T,其尺寸与实际切削深度和切削宽度匹配。
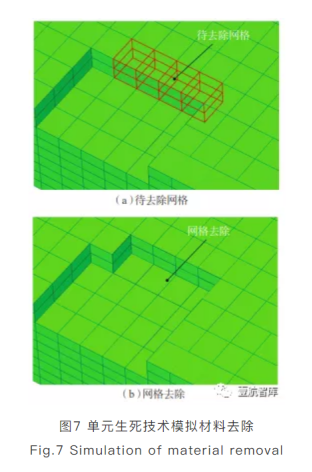
在加工框类零件时,常采用外环走刀方式,即从槽腔中心开始,以叠刀系数围绕槽腔轮廓逐层铣削,针对试验件结构特点,编制了数控加工程序,如图 8 所示。刀具轨迹的步长根据当前槽腔网格尺寸确定,每一步代表沿步长方向去除相应的网格。
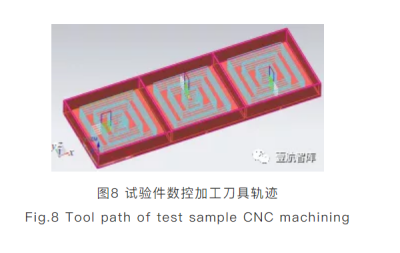
在铣削过程中,铣削力随时间变化,仿真中可将铣削周期分为若干个离散的分析步,以模拟出动态铣削力下的零件变形情况,但这种方法会大量消耗机时和内存,难以在工程中应用。考虑到后续有限元仿真的计算效率,本研究采用工程中常采用的平均铣削力进行仿真计算。采用四因素三水平正交试验建立 7B04铝合金切削力和切削温度的计算模型,铣削刀具为双刃整体硬质合金立铣刀,直径为 20mm,螺旋角为 25°,试验机床为 DMG monoBlock 高速铣削加工中心,最高转速为 24000r/min,冷却方式为空气冷却,分别使用Kistler 9257B 型压电式测力仪和热电偶测量铣削力和铣削温度,取稳定切削阶段连续 10 个周期内的切削信号平均值作为平均切削载荷。试验安排和结果如表 1所示。
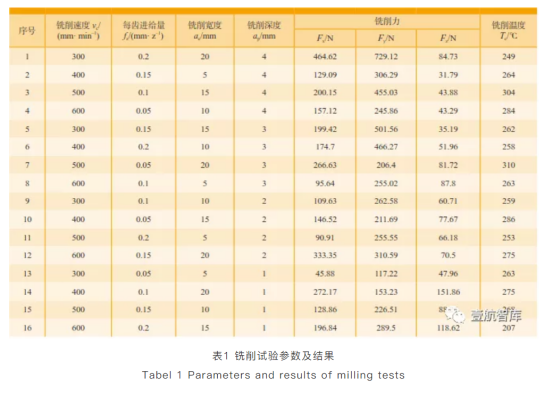
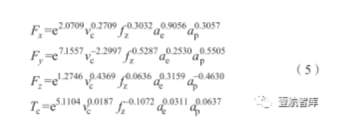
在实际铣削过程中,剪切面是沿切削刃变化的空间曲面。此外,由于切削层厚度是随刀齿所在位置不同而发生变化,作用在剪切面上的力载荷和热量载荷分布情况更为复杂。因此,必须对剪切面以及作用在其上的载荷进行适当的简化,如图 9 所示。根据待去除网格的面朝向,可以将剪切面简化为相邻网格的交界面,载荷简化方面,需要将式(5)得到的铣削力和铣削温度转化为面载荷施加在简化的剪切面上。
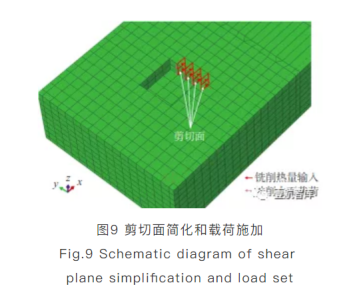
为达到计算精度和计算效率的平衡,仅在当前需要加工的槽腔划分密集的网格,其他槽腔网格较为稀疏。考虑到不同槽腔网格的连接问题,其他槽腔网格沿与当前槽腔连接方向粗化,如图 10 所示。为实现当前加工槽腔的网格细化,在不同的加工阶段将隔框设置为不同的加工状态,加工状态随着槽腔的加工顺序不断更新,当隔框加工完毕后其状态不再变化。
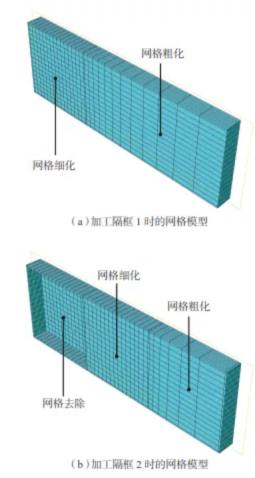
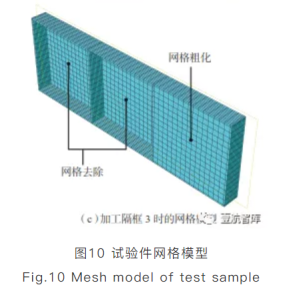
当一个隔框处于加工阶段时,其网格从粗网格变为细网格,细网格需要根据上一步计算结果,结合粗网格节点信息,经过插值方法得到。为保证网格细化后的计算精度,插值方法采用基于质心的三维插值方法,状态更新结果如图 11 所示。可以看到,更新后的 Mises 应力和温度继承了更新前的状态。
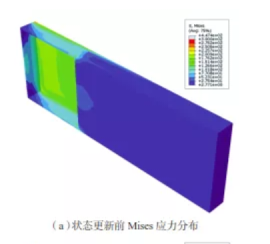
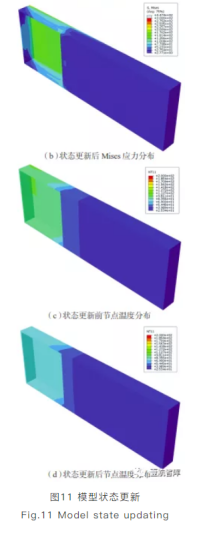
根据建立的有限元模型,对试验件进行加工变形模拟,选取两种不同的加工方式:一种为先加工两端隔框、再加工中间隔框(1–3–2);另一种为先加工中间隔框、再加工两端隔框(2–1–3),对比隔框加工顺序对加工变形的影响。在完成模拟后,进行实际加工,用三坐标测量机测量变形量,铣削参数为 vc=188m/min、fz=0.1mm/z、ae=10mm、ap=3mm,铣削刀具选用双刃整体硬质合金立铣刀,直径为 20mm,加工后试验件如图 12 所示。
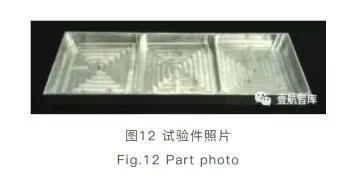
图 13 为两种加工方式下的应力分布,可以看到,应力主要集中在最后加工的隔框的腹板处,而筋条的应力相对较小,存在较大的应力差,将会导致零件四周向中心的弯曲变形。

图 14 为两种加工方式下的整体变形,可以看到,试验件缘条发生了明显的上凸弯曲变形,最后加工的隔框变形量最小,这是因为先加工的部位经过长时间的应力释放和再平衡,内部应力趋于均匀,而最后加工的部位内部应力与其他部位的应力存在较大的应力差,结合隔框结构自上而下刚度增强的特点,出现了这种变形形式。此外,中间加工的隔框(见图 14(a)中的隔框 3、图14(b)中的隔框 1)变形量最大,这同样是由应力释放不充分造成的。
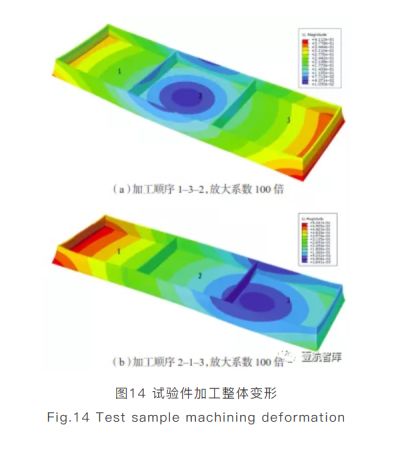
对比算例变形结果可以发现,在先加工两端再加工中间的策略下,试验件的变形较为均匀,变形量也较小,这是因为无论先加工何处,中间相对两端均会产生应力差,造成零件发生两端翘曲变形,如果中间部位后加工,则会在中间保持较高的刚度以抑制变形。提取先加工两端再加工中间策略的试验件中线处腹板沿长度方向(x 方向 ) 的变形量,并与三坐标实际测量结果对比,结果如图 15 所示。模拟值变化趋势符合试验值,但数值偏小,这可能是由于材料本构模型误差,最大变形量发生在隔框 3 的端点,模拟值和试验值分别为 0.0576mm和 0.0683mm,最大误差为 16%,基本可满足工程应用需要。
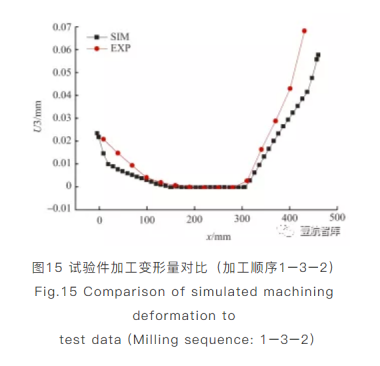
某大型铝合金整体薄壁结构件长度约 5m,筋条和腹板厚度均为 3mm,毛坯为 7B04 铝合金预拉伸厚板,要求加工后零件自然状态下最大变形量不超过 5mm。对结构件几何特征进行分析,结构件框体轮廓尺寸大、结构复杂,相对于零件长度而言腹板筋条厚度极薄,在加工过程中变形问题十分突出。在制定工艺方案的过程中,首先确定加工刀具和工艺参数:双刃φ32 铣刀,主轴转速 n=10000r/min,铣削宽度ae=10mm,铣削深度ap=3mm,进给速度 vf=5000mm/min,按照从两端到中间对称加工的思路进行加工,使结构件尽可能保持刚度。使用建立的薄壁件加工变形预测模型,进行结构件的加工变形仿真,其结果如图 16 所示。可以发现,结构件发生了翘曲变形,且变形量沿长度方向基本均匀分布;最大变形发生在两端,即刚性最弱的部位,且最大变形量均 <5mm,从仿真结果来看,初步制定的工艺方案是合理的。
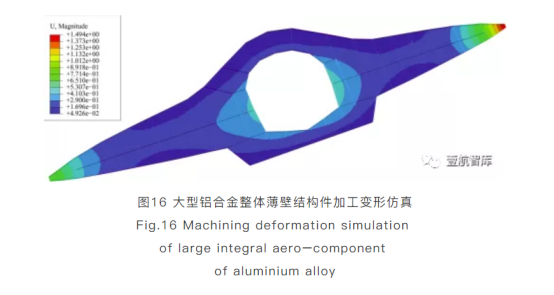
根据仿真结果,按照制定的工艺方案,在 QW–25–80 型五坐标龙门式数控铣削加工中心上进行了结构件的铣削加工,其结果如图 17 所示。
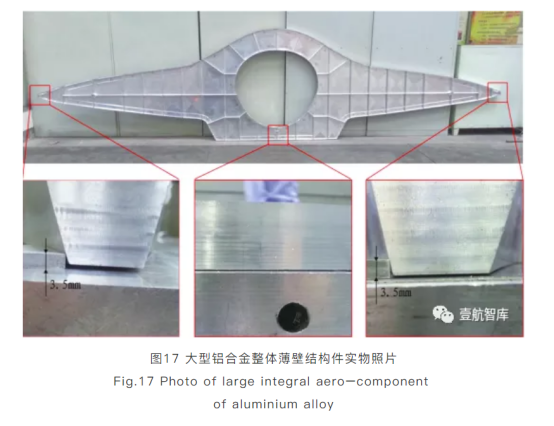
大型铝合金整体薄壁结构件检验结果如图 18 所示。可以看到,变形量模拟值变化趋势基本符合试验结果,最大变形量的误差在 22% 左右。虽然数值模拟结果与实际加工存在一定误差,但考虑到数值模拟是在一定简化基础上进行的,模拟结果可以接受。框类零件加工变形的模拟方法能准确预测其加工变形规律,可以为大型整体框类结构件的数值模拟运算及实际加工工艺规程制定提供技术支持。
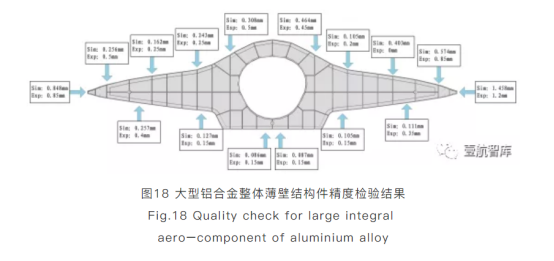
本研究借助理论解析建模、有限元模拟和试验验证等手段,系统研究了航空结构件铣削加工变形预测方法,得到了以下结论:(1)研究了航空结构件铣削加工有限元模拟所涉及的本构模型建立、毛坯初始应力场构建、切削载荷施加、网格细化与状态更新等问题,建立了用于薄壁件加工变形预测的有限元模型。(2)在典型结构上对两种加工策略进行了加工变形仿真,发现先加工两端后加工中间的策略能够利用零件自身的刚度抑制变形,且变形量较为均匀,对该种策略进行了试验验证,结果表明模型具有较高的精度,能够满足工程应用需要。(3)采用先加工两端后加工中间的策略制定了大型铝合金整体薄壁结构件工艺方案,通过加工变形仿真验证了工艺方案,并进行实际加工。实际加工结果表明,结构件变形量和变形趋势与试验结果基本吻合,实现了大尺寸铝合金整体薄壁结构件的一次合格加工。免责声明:本文引用自《航空制造技术》2019年第62卷第3期,作者丁悦,刘畅,文章著作权归作者所有。文章仅供参考阅读使用,如有侵权,请联系删除。需参阅该论文所在期刊,请到正规渠道购买。
著作权归作者所有,欢迎分享,未经许可,不得转载
首次发布时间:2021-01-26
最近编辑:3年前
获赞 10071粉丝 21537文章 3532课程 218