重庆大学刘怀举教授:浅析机械传动齿轮接触疲劳理论研究新进展
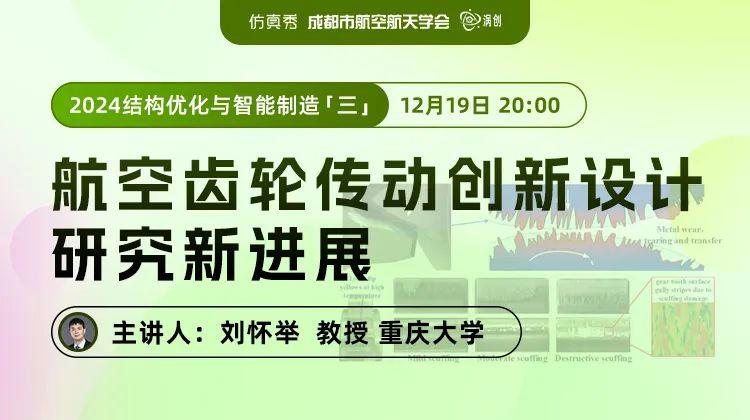
导读:随着航空、风电、重载车辆等装备对齿轮传动功率密度、承载能力、疲劳寿命要求的提高,以微点蚀、点蚀、深层齿面断裂等多种形式存在的齿轮接触疲劳失效成为限制现代齿轮及装备服役性能与可靠性的重要瓶颈。通过调研国内外相关研究现状,描述了齿轮接触疲劳失效模式,归纳了现有齿轮接触疲劳理论与寿命预测方法,介绍了连续损伤理论、微结构力学理论在齿轮接触疲劳研究中的作用,辨识了影响齿轮接触疲劳性能的轮齿界面状态、硬化层与残余应力、材料缺陷等结构-工况-材料要素体系,强调了齿面时变滑滚下宏微观形貌-润滑耦合热弹塑接触机理、粗糙齿面疲劳-棘轮-磨损多源损伤机理、多尺度齿轮材料损伤与性能退化、齿轮抗疲劳制造中的表面完整性及其演化机理等科学问题,总结了超精加工、涂层、喷丸等对提高齿轮接触疲劳性能的影响,为进一步理解齿轮接触疲劳失效机理、形成高性能齿轮抗疲劳设计制造方法提供了参考。本文节选自重庆大学机械传动国家重点实验室刘怀举、张博宇、朱才朝和魏沛堂老师公开发表在机械工程学报2022年2月(第58卷第3期)的学术论文《齿轮接触疲劳理论研究进展》关于齿轮接触疲劳失效机理章节。12月15日19时(周日),我们将在“2024结构优化与智能制造创新技术报告会”邀请本文作者——重庆大学刘怀举教授做《航空齿轮传动创新设计研究新进展》线上讲座。欢迎工程技术人员、科研工作者和理工科学子报名。
一、写在文前
齿轮是重要的机械基础零部件,广泛应用于航空、航天、舰船、汽车、风电等领域,是装备制造业不可或缺的组成单元,直接决定重大装备的服役性能和可靠性。目前装备的功率密度、承载能力和可靠性等要求不断提高,并且高速、重载、高温等极端服役环境逐渐增多,使得齿轮失效问题日益突出。风电齿轮设计寿命要求已逐渐从 20 年延长到 30 年,某些应用场合的齿轮接触应力循环次数要求可能高达108~1010 数量级,超过传统高周疲劳定义的范围,迈入超高周疲劳;航空渗碳淬火齿轮接触压力高达2~3 GPa;传统汽车行业的齿轮接触疲劳极限也有报道表明接近 1 800 MPa,形成典型重载工况。这种高承载能力、高服役寿命的双重要求下,齿轮接触疲劳的控制尤为重要。尽管齿面硬化、精加工等先进加工技术能够提高齿轮接触疲劳性能,仍无法满足服役日益增长的寿命要求。从全球范围看,因齿轮接触疲劳失效导致的装备事故屡见不鲜[1-5],使其成为限制现代齿轮装备性能与可靠性的重要瓶颈。齿轮接触疲劳研究自齿轮诞生起从未停止。作为齿轮最主要失效形式之一,齿轮接触疲劳失效校核成为齿轮设计的必要环节。现有齿轮接触疲劳强度设计方法如 ISO 6336、AGMA、DIN、GB/T 3480等标准在工业界得到广泛应用[6, 7]。但在工程实际中经过强度校核后的齿轮仍常出现接触疲劳失效问题,如何进一步提高齿轮接触性能与疲劳寿命,继而保证其传动可靠性成为当今机械传动领域不可回避的重要科学问题与重大工程需求。在大量的实践过程中,人们逐渐意识到作为齿轮接触疲劳强度分析“基石”的“赫兹接触理论”存在很多假设条件限制,使得现有接触疲劳分析方法缺少对齿轮服役过程中接触疲劳性能退化机理和表面完整性作用机制的深层次科学认识,无法在根本上诠释齿轮接触疲劳失效机理。现代齿轮研究者和制造商逐渐认识到必须通过对包含轮齿界面状态、硬化层、残余应力、材料强度与缺陷等在内的齿轮表面完整性的全方位认识才可能满足现代高端重载装备对齿轮接触疲劳性能的要求,基于表面完整性的齿轮接触疲劳研究也成为未来齿轮工作者的重要研究方向。国外先进机构已形成自有的较为完整的齿轮表面完整性设计制造检测体系与方法[8-10],而国内目前对齿轮表面完整性设计和抗疲劳制造认识不足。如若再不开展相关基础研究可能导致高性能齿轮等关键零部件与国外先进水平的“隔代差距”,从而放大主机装备的技术差距,严重危害国防安全与国民经济。通过调研国内外相关研究现状,描述了齿轮接触疲劳失效模式,归纳了现有齿轮接触疲劳理论与寿命预测方法,介绍了连续损伤理论、微结构力学理论在齿轮接触疲劳研究中的作用,辨识了影响齿轮接触疲劳性能的轮齿界面状态、硬化层与残余应力、材料缺陷等结构-工况-材料要素体系,强调了齿面时变滑滚下宏微观形貌-润滑耦合热弹塑接触、粗糙齿面疲劳-棘轮-磨损多源损伤、多尺度齿轮材料损伤与性能退化、齿轮抗疲劳制造中的表面完整性及其演化等科学问题,总结了超精加工、涂层、喷丸等对提高齿轮接触疲劳性能的影响,为进一步理解齿轮接触疲劳失效机理、形成高性能齿轮抗疲劳设计制造方法提供了参考与依据。二、齿轮接触疲劳理论研究进展结论与总结
经过几代齿轮工作者的努力,齿轮接触疲劳理论与分析方法已经取得了长足发展。
(1) 初步建立基于表面完整性的分析方法。逐渐意识到以齿面微观形貌、润滑状态、硬度梯度、残余应力、微结构、材料缺陷等要素构成的表面完整性体系对齿轮接触疲劳性能的重要作用,也在这些因素的影响方面开展了一些理论和试验研究,摸清了其中一些影响规律,对传统赫兹接触理论及常规强度设计标准有了创新性突破,初步建立了基于表面完整性的齿轮接触疲劳分析方法。
(2) 涌现一批先进的理论分析如粗糙表面部分弹流润滑接触、连续损伤力学理论、扩展有限元法、晶体塑性理论、数据驱动方法等;也探索出一些先进的齿轮接触疲劳试验、加速等效疲劳试验、在线无损智能检测表征方法等,为进一步阐明齿轮接触疲劳失效机理提供了重要的研究手段。
但在齿轮接触疲劳理论方面仍存在以下的不足,需要在接下来的研究中不断完善。
(1) 完善基于表面完整性的齿轮接触疲劳理论。目前对于基于表面完整性的齿轮接触疲劳分析理论仍不完善,主要体现在:① 轮齿界面力学方面,齿面微观形貌与润滑形成复杂的耦合界面系统,存在热、弹、塑、流等多物理场耦合机制,也在发生疲劳-磨损协同演化,具有明确物理意义的考虑多场耦合和多源损伤且能高效求解的轮齿界面力学模型亟待完善;② 对于残余应力在齿轮接触力学响应、疲劳裂纹萌生及扩展中的作用机制仍不明确,也缺乏相关的试验验证,试验方面实现残余应力单因素调控具有挑战性;③ 微结构及尺度效应对性能影响仿真手段欠缺,齿轮内部结构损伤检测技术相对不足。通过表面完整性参数的表征不断完善结构-工况-材料要素体系,基于多源、多尺度损伤与断裂理论,构建齿轮接触疲劳数值模型,描述齿轮疲劳进程中力学性能退化、微结构演变,结合试验验证,揭示齿轮接触疲劳失效机制,开展多表面完整性要素的性能驱动的主动设计,形成高性能齿轮抗疲劳设计方法。
(2) 极端服役条件下齿轮接触疲劳损伤机制。在国家航天与航空、船舶与海洋、川藏铁路等重大工程的需求推动下,对极端服役环境下高可靠、长寿命齿轮传动提出了更高要求。极端服役环境带来齿轮传动服役行为、评价方法、基础数据等方面的全新挑战,传统服役条件下齿轮设计方法与制造技术已不能满足极端服役环境下齿轮的性能需求,亟待开展高温材料本构、高温齿轮服役性能退化、试验方法与基础数据的研究。
(3) 加强建设齿轮接触疲劳实验与数据。开展齿轮接触疲劳试验是验证理论分析方法、积累基础数据、标准制修订,继而实现真正的高可靠齿轮设计的重要支撑。面向高性能齿轮试验需求,齿轮接触疲劳试验机还存在加载能力与高速能力略显不足、真实时变载荷运行情况模拟能力弱、在线健康监测能力较弱、试验与检测标准方面亟须改进等问题。应继续加强试验数据建设,搭建更多的齿轮接触疲劳试验台,探索在线、智能齿轮接触疲劳定量检测技术,并善用大数据、人工智能等技术,建设面向我国齿轮材料与工艺环境的接触疲劳基础数据库,真正服务我国齿轮行业。
(4) 推进齿轮抗疲劳制造方法与技术。齿轮最终是造出来的,而不是设计出来的。受工艺方法和成本限制,最终制造出来的齿轮可能并不能达到设计要求水平。在航空等对齿轮表面完整性要求很高的应用领域率先应用了这些先进的制造技术,但由于对工艺与表面完整性和疲劳性能的关联规律认识不清楚,使得这些工艺并未产生最优化的效果。持续推进齿轮抗疲劳制造方法与技术并实现真正的工艺优化和性能提升才是齿轮疲劳研究的最终目的。
(5) 开发齿轮接触疲劳分析专用软件。目前我国齿轮强度分析软件几乎全部被国外垄断,是典型的“卡脖子”技术。结合在齿轮接触疲劳方面的体系研究,开发齿轮接触疲劳分析专用自主软件,将先进理论模型真正应用于工程实际,解决齿轮设计制造中的难题,显著提升行业竞争力并有利于打破国外长期的技术封锁。
由于篇幅原因,《齿轮接触疲劳理论研究进展》论文关于齿轮接触疲劳失效机理、齿轮接触疲劳理论、齿轮接触疲劳影响要素和参考文献的内容这里不做介绍。感兴趣的朋友请点击文章的附件下载查看。
三、航空齿轮传动创新设计研究新进展报告会
高性能齿轮传动是航空发动机、直升机、风电等高端装备关键基础件,其技术水平决定了装备性能和可靠性,是我国“工业强基”的重要构成。基于表面光滑、材料均质等假设的常规齿轮疲劳设计方法已难以保障其高可靠、高功率密度服役需求,齿轮疲劳失效导致的航空装备故障和人机安全问题屡见不鲜,成为机械传动领域的“卡脖子”瓶颈。当前,重庆大学刘怀举教授团队持续十余年产学研攻关,解决了航空齿轮表面完整性与疲劳性能协同定量关联难题,开发了完备的齿轮疲劳试验成套技术体系,提出了齿轮抗疲劳宏微观参数智能协同设计新方法,指导航空齿轮高表面完整性创成,引领了齿轮抗疲劳设计学术前沿,应用于中国航发集团相关传动装置,支撑航空齿轮疲劳性能达国际先进水平,相关技术辐射特种车辆、风电等领域,产生显著的国防、经济与社会效益。以下是直播安排:
2024结构优化与智能制造(三):航空齿轮传动创新设计研究新进展-仿真秀直播
获赞 10937粉丝 22416文章 3890课程 233