基于Abaqus金属管压力成形过程和成形极限图
本文摘要:(由ai生成)
本文讨论了使用Abaqus模拟金属管液压成形的过程,重点在于避免成形过程中的失效模式,如颈缩和破裂。通过成形极限图(FLD)评估材料的成形性,预测断裂失效。模拟展示了应力/应变结果、FLD损坏标准结果和壁厚结果,帮助优化模具几何形状和工艺设置。讨论强调了液压成形工艺的优势,以及有限元分析在预测应力/应变、评估材料成形性和优化工艺参数中的重要性。
目录
介绍
优点
失效模式
失效准则 - 成形极限图 (FLD)
有限元模型
材料特性
加载
结果
应力/应变结果
形成极限损坏标准结果
壁厚结果
讨论
在这文章中,我们将讨论使用 Abaqus 进行金属管液压成形的模拟。采用成形极限图来创建材料的应变包络线,以避免颈缩(破裂),这是此类金属成形过程中可能的失效模式。这将在金属波纹管接头的液压成形过程模拟中得到证明。
介绍
金属液压成形作为传统金属成形工艺的替代方案,用于工件(管材、毛坯、预成型件)的大规模生产,主要用于汽车和航空工业。液压成形主要利用流体压力来使工件成形。液压成形主要有两大类,管材液压成形和毛坯液压成形。这些如下图 1 所示。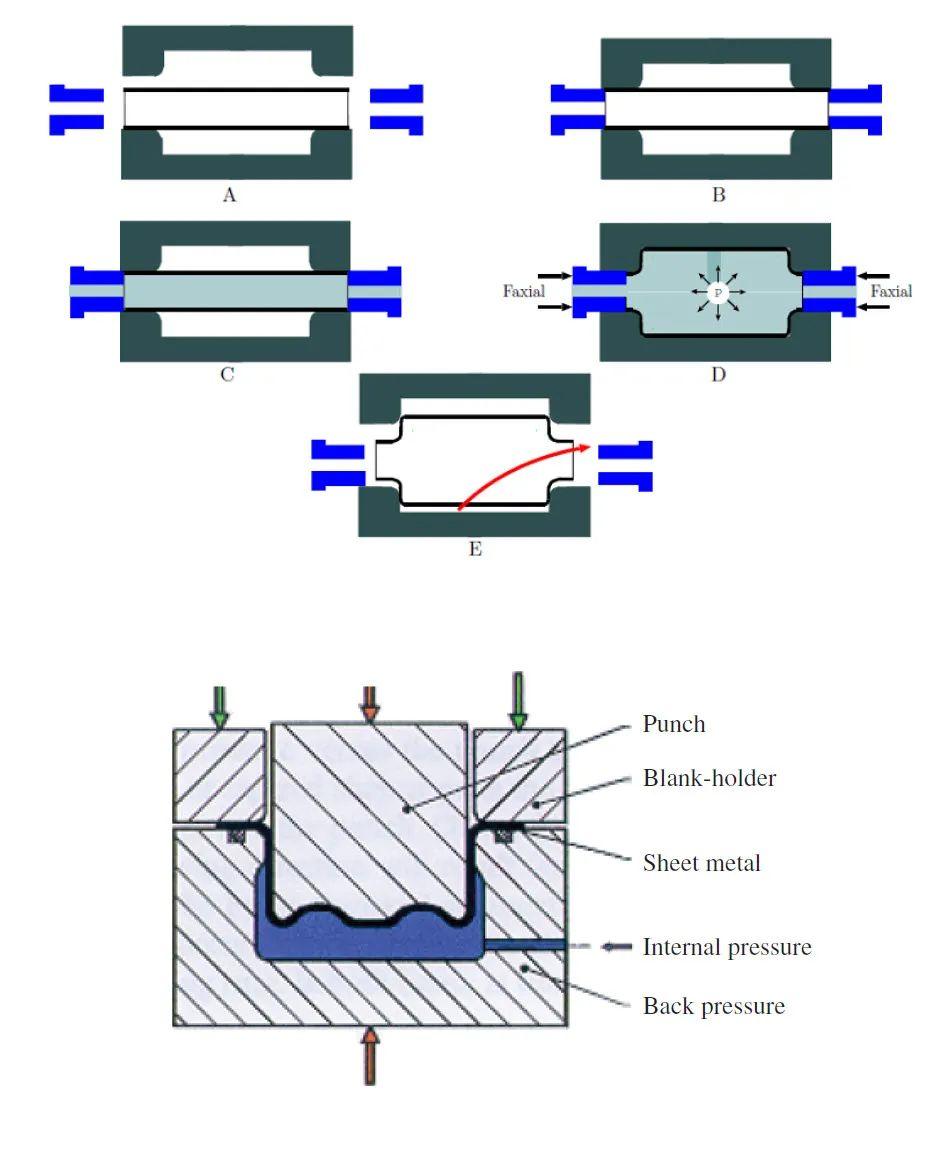
图 1:管材液压成形(顶部)和毛坯液压成形(底部) 液压成形工艺的另一个分类方式是固定模具和移动模具。通常,管材成型被认为是移动模具液压成型工艺,因为工件是在管材端部引起的流体压力和轴向压缩的组合下成型的,这称为轴向进给。确定最佳载荷路径(轴向进给与流体压力之间的组合)对于管内高压成形至关重要,并且在许多情况下是通过试验和错误来确定的,或者更好地通过有限元分析来确定。 优点
- 降低工具成本(更少的部件=更少的停机时间,更简单的工具设计),
失效模式
液压成形中的典型失效模式包括导致工件破裂/断裂的屈曲、起皱和局部颈缩。对于管材液压成形,屈曲和起皱(局部屈曲)通常发生在成形过程的开始阶段,并且与过量的轴向进给有关。可以通过稍微增加流体压力来纠正起皱。这些模式如图 2 所示。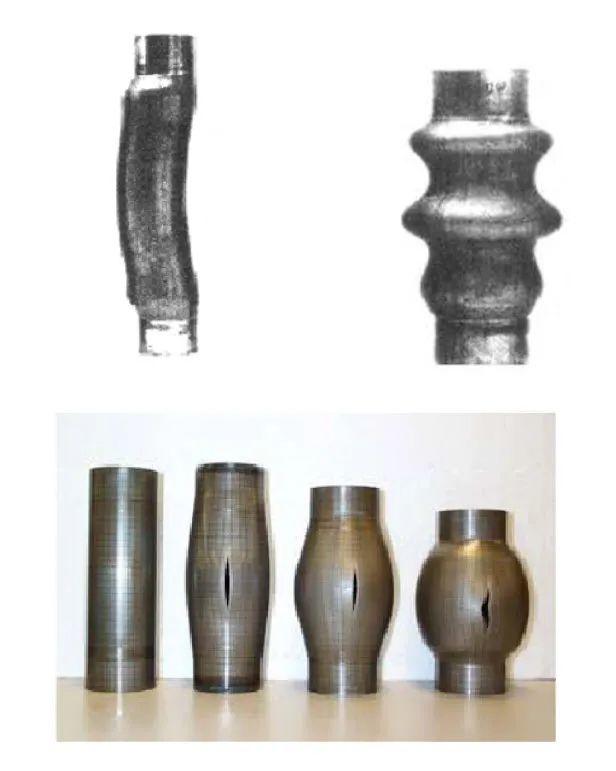
图 2:液压成形中的屈曲(左上)、起皱(右上)颈缩(底部)失效 由于颈缩,可能会发生管爆裂。当颈缩开始时,应变变得不均匀。不久之后,它们就定位了,该区域的刚度急剧下降并发生失效。此类故障是由于流体压力过高而发生的。这就是为什么找到最佳压力(例如负载路径)在液压成形中非常重要,这主要取决于材料特性和工件的最终几何形状。失效准则 - 成形极限图 (FLD)
成形极限图 (FLD) 通常用于金属钣金成形工艺中,以评估工件的成形性并避免潜在的故障。这些是根据双轴应变状态下的主应变与次主应变图形成的。作为一项较新的进步,使用了成形极限应力图 (FLSD),因为它们对应变路径变化不敏感。
FLD 是通过特定测试通过实验获得的,是液压成形过程中断裂失效的可靠预测指标。为了考虑与实验数据输入相关的不确定性,通常会引入特定材料的成形极限曲线 (FLC) 的安全裕度。
示例中使用的高强度双相钢的 FLC 曲线如下图 3 所示,以浅蓝色显示(“exp”)。这是通过测试得出的。还显示了示例性设计安全曲线(“安全性”),以及特定钢的某些材料状态的限制线。发生某些故障模式的特定区域也在图 3 中以粗体注释。
图 3:高强度钢的 FLD
有限元模型
在 Abaqus 中研究了 4 mm 厚管的液压成形过程的模拟,以评估特定的高强度钢成形性能。该管在刚性模具上进行液压成型,形成金属波纹管接头。使用 Abaqus Explicit(t=0.08 秒)。 模型中使用了四分之一对称性。下面的图 4 给出了几何形状(具有渲染厚度)和载荷的详细信息。钢管(灰白色)使用壳单元,模具使用刚性壳单元(红色)。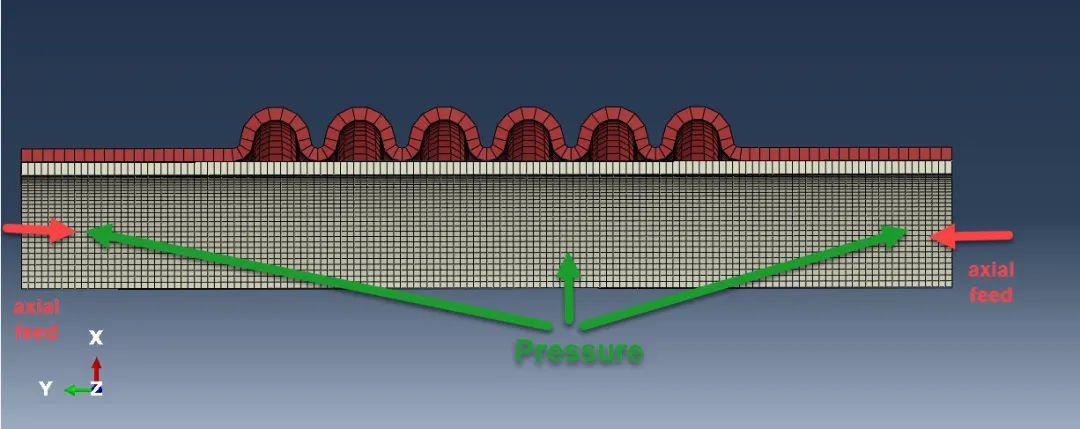
材料特性
在金属成形过程中,可能会发生各向异性屈服。使用各向同性弹性、希尔各向异性屈服定律用于模型中的塑性分析。材料真实应力与对数塑性应变的关系作为输入给出。对于损伤建模,实施了 FLD 损伤(使用图 3 的曲线)来预测断裂失效。图 5 给出了钢材的应力与总应变曲线,以及 Abaqus 中材料选项卡的详细信息。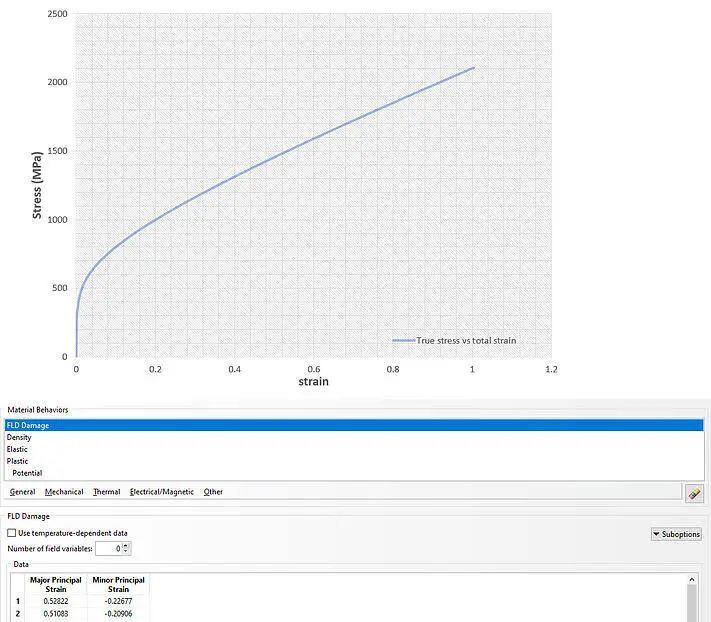
加载
液压成形模拟过程中的载荷输入(图4)是通过一定幅度下的轴向进给(两端同步位移控制)和一定幅度下作用于管子表面的压力载荷来实现的。这些幅值曲线如图 6 所示。这称为加载路径。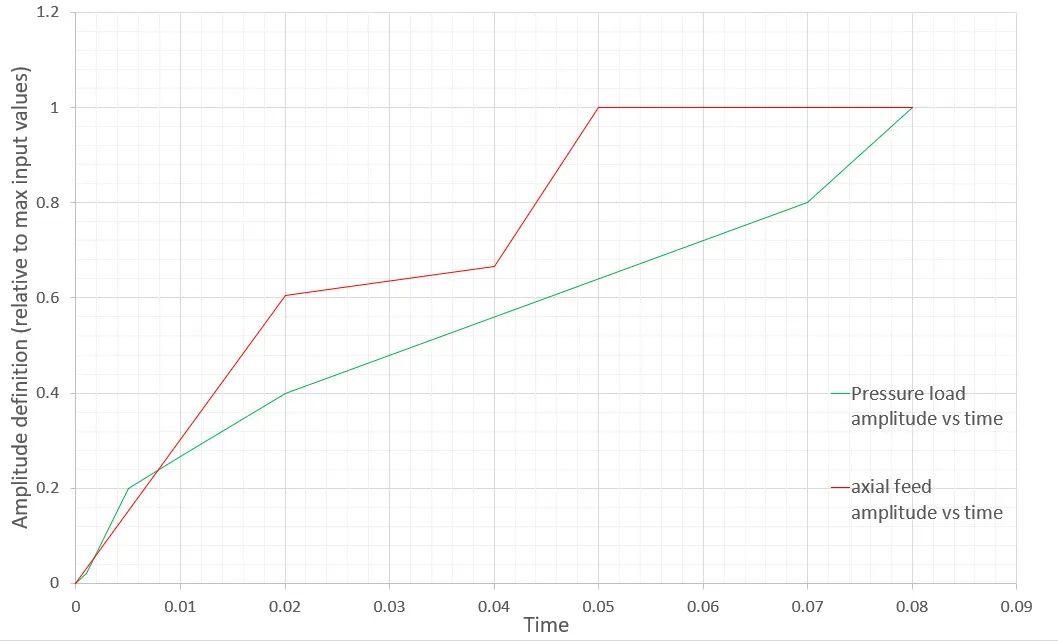
通常,在工艺开始时需要更大的压力,以使材料变硬并避免由于轴向进给的压缩而导致的屈曲/起皱故障(图 6)。找到最佳的装载路径将导致工件具有更好的最终质量。这里选择的加载路径是(相对)随机的。如今,FEA 提供了一种可行且准确的方法来寻找金属成形工艺的最佳负载路径。由于这是一个迭代过程(找到该负载路径),有限元分析通常与优化算法相结合(例如使用Isight )。 结果
应力和应变水平以及方向性(冯·米塞斯应力、最大主应力、最大主塑性应变)可以提供有关液压成形过程中材料状态和限制的见解。这些措施还可以帮助优化模具几何形状,从而有助于避免工件上出现可能损害其均匀性的热点。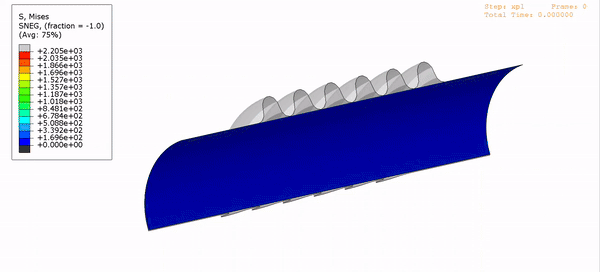
液压成形过程中波纹管上的 von Mises 应力 (MPa)。
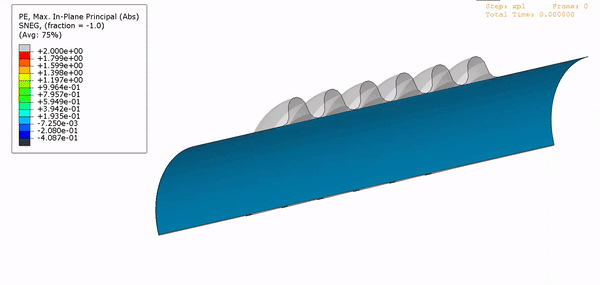
形成极限损坏标准结果
跟踪 FLD 损伤 (FLDCRT) 将有助于深入了解材料的成形性限制。这可以帮助评估不同的材料并针对特定的液压成形工艺或模具形状决定最合适的材料。
FLD标准的结果如下所示。只要 FLDCRT 保持在 1 以下,材料点就会保持在图 3 的极限曲线下方。对于波纹管示例,材料保持在成形极限内,直到过程完成前 0.01 秒。
在液压成形模拟结束时,在样本 (FLDCRT>1) 最大塑性应变位置观察到失效。最后两帧的详细信息如下图 7 所示。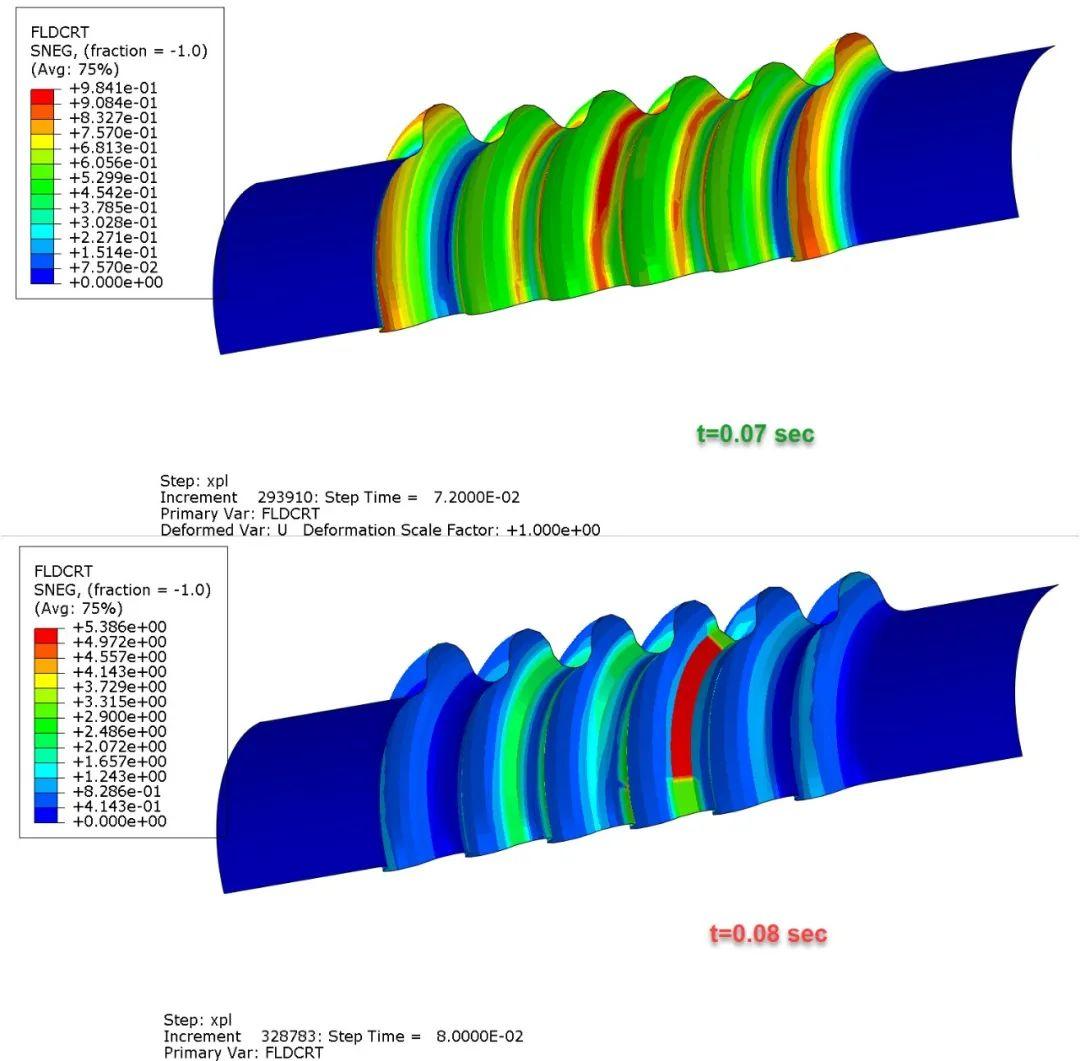
图 7:液压成形期间波纹管的 FLDCRT 结果(最后两帧)。
下面的视频给出了金属波纹管液压成形的 FLD 标准结果。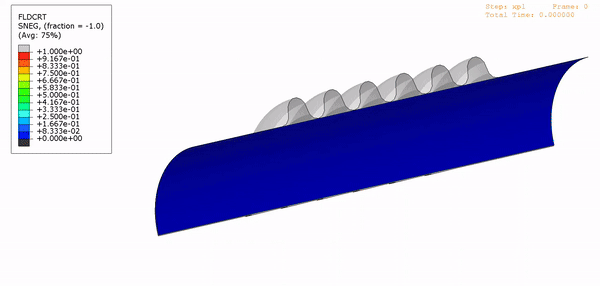
壁厚结果
初始管厚度为 4 毫米。通常,在管液压成形中,由于轴向进给的压缩,预计管端部的管截面会变厚。波纹管最终壁厚 (STH) 的详细信息如下图 8 所示(单位:毫米)。
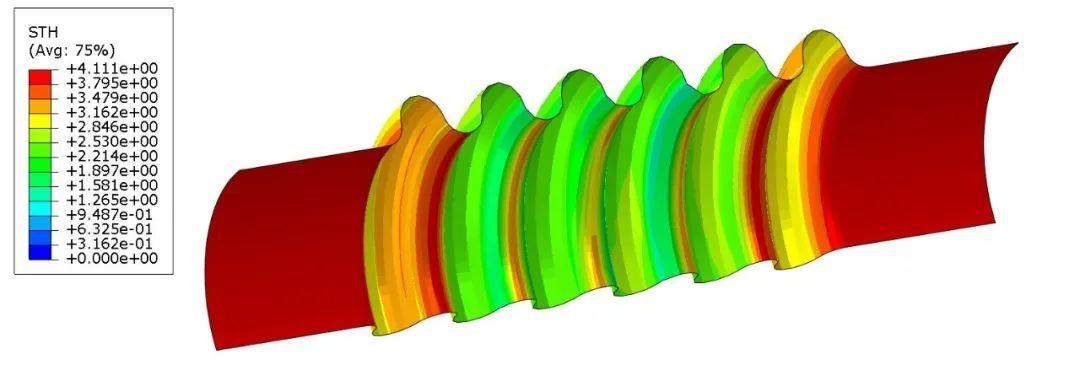
在液压成形过程结束时检查壁厚均匀性有助于评估成品的质量。尽可能均匀的壁厚是理想的。此外,壁厚可以帮助识别和改进液压成形工艺设置。通过监测壁厚,可以改进加载路径,例如图6的振幅曲线的参数。 当与优化过程仿真结合使用时,该功能变得特别强大,可以修改某些输入参数(加载路径、处理时间),以便将工件厚度减少的百分比保持在一定范围内。 讨论
在上一节中,介绍了波纹管液压成形模拟的结果。液压成形工艺由于其相对于传统成形工艺的上述优点而变得相当流行。 此外,由于新的二氧化碳排放法规要求减轻部件重量,而结构要求保持不变,预计液压成形在未来几年将得到更广泛的应用。与液压成形过程相关的参数的不确定性使得使用计算机模型来模拟/优化液压成形非常有吸引力。- 可以实施 FLD 损伤来评估材料的可成形性,甚至保持在一定的 FLD 限制百分比以下,
- 可以研究模具工件摩擦特性并修改这些特性以获得波纹管的特定凸出高度,
- 通过优化例程最小化 FLD 百分比的可能性(可以使用 Isight 或类似软件),
- 评估特定液压成形工艺和/或工件几何形状的不同材料的可能性,
- 可以优化液压成形工艺的加载路径参数,以实现最大的壁厚均匀性或保持在一定的厚度减少范围内(可以使用 Isight 或类似软件)。