《Mechanics of Solid Polymers》4.9平衡定律与场方程
4.9 平衡定律与场方程
在为材料建立本构方程或解决连续介质力学问题时,遵循一些重要的物理原则是至关重要的,例如:质量守恒、线动量守恒、角动量守恒、能量守恒,以及热力学第一和第二定律。这些原则适用于所有材料和加载条件,并且形成了需要满足的平衡定律和场方程。在此背景下,平衡定律是用材料体积表达的物理规律,而场方程是用材料点表达的物理规律。以下各节将从连续介质力学的角度介绍这些物理原则。本讨论所需的尚未定义的场变量列于表4.1。本章使用的所有变量的总结见第4.14节。为了便于即将进行的平衡定律和场方程的讨论,有必要建立以下运输定理,该定理表达了体积内某个量的时间导数:

在这个方程中, 是任意的空间标量场,Ωc 是在时间 时研究区域的体积,I 是空间速度梯度。该运输定理可以借助方程(4.79)和(4.135)证明,如下所示:
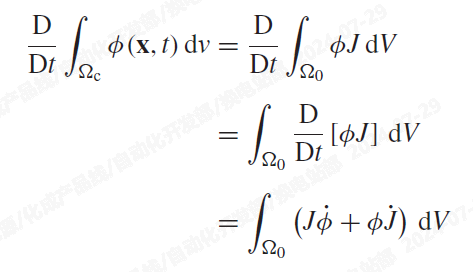
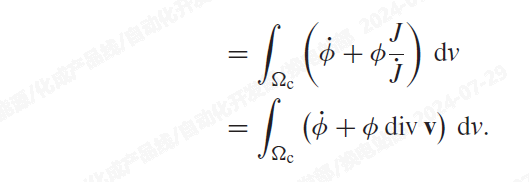
下一节将详细讨论运输定理及其推导过程。
Table 4.1 | 平衡定律和场方程中使用的场变量 |
---|
Specific mass (density) | 比质量(密度) |
Specific internal energy | 比内能 |
Specific Helmholtz free energy | 比赫姆霍兹自由能 |
Specific internal entropy | 比内熵 |