解析DEFORM软件中的元胞自动机法
金属材料的性能取决于内部的微观组织结构,而好的材料性能和价格是产品最大的优势。随着现代物理冶金、热成形技术、热处理技术和计算机技术的兴起与发展,使预测和控制金属材料热加工过程中的组织演变成为可能。
金属材料的热加工过程中,主要是晶粒的再结晶和晶粒长大现象决定了微观组织晶粒大小和均匀性,20世纪70年代开始,各国学者对于金属材料微观组织演变过程主要集中在两类数学模型上,唯象理论模型和位错模型。大多数学者采用唯象理论模型是经典的Johnson-Mehl-Avrami-Kalmogorav(JMAK)方程来描述动态再结晶和静态再结晶动力学关系,使用JAMK方程需要考虑金属变形过程中的温度、应力、应变、流场等变量与再结晶体积分数的函数关系,在实际应用中,模拟计算的结果与实验测得数据取得了较好的吻合,得到了国内外研究者的广泛认可。位错模型是基于金属在塑性变形过程中,持续应变导致位错密度变化引起的微观演变,通过计算临界条件、晶界迁移速度,建立再结晶体积分数变化率与位错密度分布函数关系的数学模型。计算机对材料行为的模拟研究与发展主要集中在三个方面:微观行为、介观行为和宏观行为。材料的微观行为是从电子、原子尺度上的材料行为,主要应用于分子动力学和分子力学方面。介观行为是指材料显微组织结构的转变,如金属的凝固结晶、再结晶和相变等过程,介观组织模拟的模型主要有几何模型、顶点模型、元胞自动机模型(Cellular Automata,简称CA)、蒙特卡洛模型(Monte Carlo,简称MC)。宏观行为主要是材料加工方面,主要是材料变形和热处理过程中的应力、应变、温度场等。元胞自动机法最早提出用于模拟生命系统所具有的自我复制功能,其数学模型是时间、空间、状态都离散,空间相互作用和时间因果关系为局部的网格动力学模型,能够模拟复杂系统时空演化过程,广泛应用于数学、物理学、生物学、化学、地理学和经济学等各个学科的非线性现象和分形结构的研究。Hesselbarth和Gobel最早将元胞自动机法应用到再结晶方面,他们的模型研究了再结晶形核和晶核长大的动力学以及其不同的参数和算法对再结晶行为的影响,结果成功的描述了已被公认的再结晶动力学理论JMAK方程。随着国内外大量研究人员进一步发展完善模型,将元胞自动机法应用于不同金属材料再结晶过程,与实验测试得到的再结晶结果吻合。DEFORM软件以模拟金属变形和热处理过程为主要目的,在不断深入研究发展中,加入了金属微观组织演变模拟,能够从宏观和介观两个尺度下模拟金属材料变形行为和组织演变过程,不但具有经典的JMAK法用于金属再结晶模拟,而且包含了当前流行的元胞自动机法和蒙特卡洛法,能够直观的分析观察晶粒演变过程。
目前CA法在再结晶模拟方面的大部分研究与应用,都是针对具体的材料和特定变形条件下,研究人员通过Fortran、MATLAB等编译软件编程定义转变规则和图形可视化,无法直接输入实际复杂的工艺加工过程,适用普遍性不强,难以推广。DEFORM软件做为成熟的商业化软件,使用向导式界面设置界面,流程化操作,简单易用,元胞中的转化规则采用位错模拟模型,与软件中的JMAK方法可形成对照,互相印证,模拟结果可靠。
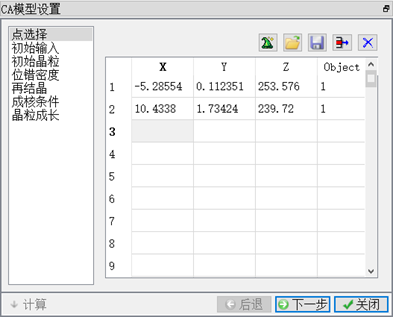
CA模型设置界面
1、工件研究位置的选择。元胞自动机晶粒组织演变模拟都是在介观尺度下的,不可能同时对一个实际工件的所有位置模拟计算,否则计算工作量太大无法实现,因此首先需要确认的是分析哪个位置点。在实际金属加工工艺当中,金属的各个部位变形差异大, DEFORM软件能够在宏观模拟计算中得到金属在变形和热处理过程中各个部位的应力、应变、温度、流场等场变量,对比分析宏观场变量差异性,选择差异较大的位置点作为分析点,可减少重复的计算量。
2、元胞生成。DEFORM软件中直接定义元胞晶格横向和纵向数目即可自动生成。晶粒再结晶模拟中,小的元胞晶格数目50×50、大的500×500,甚至更多,满足了各类金属不同大小晶粒尺寸分布的需求。另外还需要用户从计算机硬件配置和计算时间上考虑来设置初始元胞的数目。3、初始元胞形态。再结晶模拟的初始元胞形态是初始晶粒的大小和分布,DEFORM软件为更加符合实际工艺进行模拟,可通过EBSD扫描电子显微镜看到的晶粒分布结果直接输入到软件中使用。如果不方便读取导入,还可通过初始晶粒尺寸的平均值和标准变差,自动生成晶粒初始分布。4、元胞变化规则。根据位错模拟模型理论,材料在变形和热处理过程中,变形导致加工硬化产生位错,回复再结晶位错消失。DEFORM软件中的CA法包括了位错数学模型、再结晶类型、形核条件、晶粒长大等四个元胞变化规则,全面还原了晶粒的再结晶与长大过程。

式中,m为硬化敏感系数,Q诶激活能,h0硬化常数、r0回复常数、为应变速率修正系数,K为用户指定。对于铝合金、镍基合金、钢等,DEFORM软件提供这些材料在上述方程中的参考值,以及退火后金属材料中的初始位错密度大小,用户也可任意输入其它材料的系数值。
如果用户需要使用新的元胞转变规则模拟微观组织变化,允许自定义二次开发,在DEFORM软件界面下,综合考虑变形和热处理过程中的宏观场变量,模拟晶粒的演化过程。
元胞自动机设置定义完成后直接点击计算即可。模拟结果展示了整个加工工艺过程中当前位置点的晶粒、晶界、位错密度的分布,以及晶粒大小、晶界角、结晶形状长宽比的统计图。
下图所示为铝合金棒料的反向挤压成形案例,棒料挤压成形后,外缘红色区域出现了粗大晶粒缺陷,通过DEFORM软件模拟其成形和微观组织演变过程,提前预测到缺陷,并分析粗大晶粒的产生的原因,后续可通过修改挤压速度、金属温度等工艺参数优化工艺。
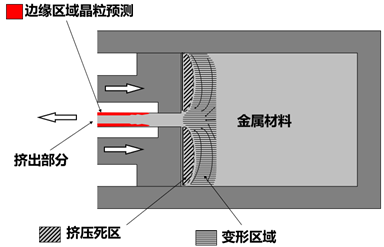
使用CA法模拟计算得到结果如下所示,挤压开始后发生动态再结晶,平均晶粒尺寸由于再结晶现象发生不断变小,但挤压完成后,从棒料外缘区域开始晶粒长大,出现了粗大晶粒。随着前端棒料温度的缓慢冷却,晶粒不断长大,挤压完成后将会产生更多的粗大晶粒。
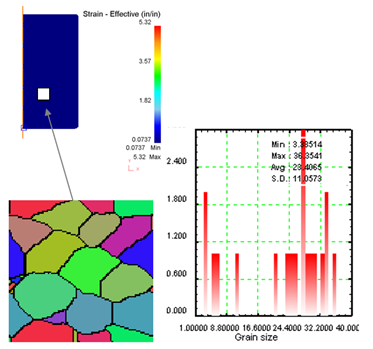
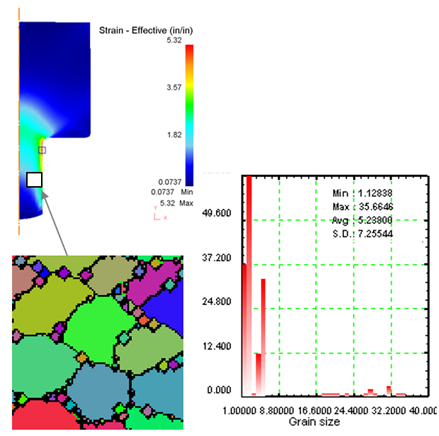
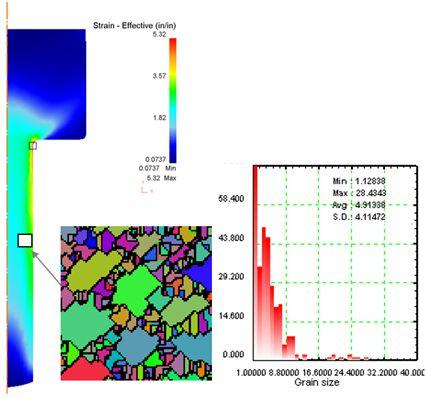
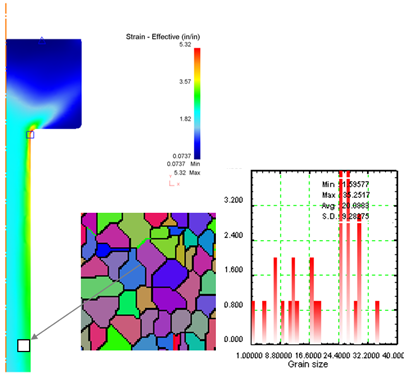
使用DEFORM软件的JAMK模拟得到的结果如下,对比分析挤压阶段各个区域的平均晶粒尺寸分布和大小,结果一致。
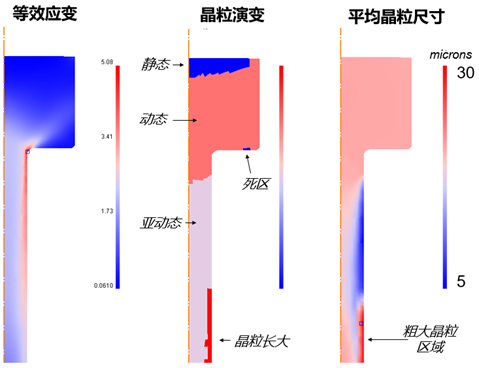
实际试生产后的,对棒料成形阶段的各个断面观察,如下图所示,金属材料刚挤出型腔时无粗大晶粒,之后从边缘位置开始晶粒长大产生粗大晶粒,远离型腔端面后,由表面向里晶粒不断长大,最终只有芯部保持了细小的晶粒。挤压完成后的粗大晶粒占到了总体积的70%以上,与模拟结果一致。
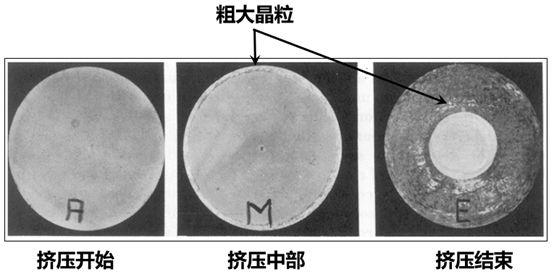
DEFORM软件中CA元胞自动机法能够结合宏观模拟计算结果,应用的位错理论模型适用大部分金属类型,是一种直观的可靠的金属再结晶演变过程的模拟工具。