水泥窑SCR脱硝入口导流板对流场分布影响有多大?
水泥窑SCR脱硝设备入口导流板设计合理性直接影响SCR脱硝效果。无疑,传统的燃煤电厂脱硝SCR主体侧入口设计方案最成熟最合理(参考:SCR脱硝上气室及导流板到底怎么做才合理),毕竟有几百上千套大大小小的脱硝设备摆在那里。烧结、球团、白灰窑等烟气也都沿用了这种形式。因此,侧入口方式是更可靠的形式。然而,从大概2018年至今,水泥行业据统计新上脱硝设备300多套,其中大部分高温高尘脱硝技术选用的SCR是顶入口方式,部分中温中尘和低温脱硝沿用的仍然是传统侧入口。主要原因是高温高尘脱硝设备布置位置限定了入口烟道联系形式,顶入方式需要的空间更小,C1出口烟道到SCR的衔接更顺畅。但顶入方式节省空间带来的另一个问题就是,流场均匀性不好组织。根据业内同行交流并查阅相关文献,咱了解到的脱硝入口天圆地方导流板布置方式有如下几类。 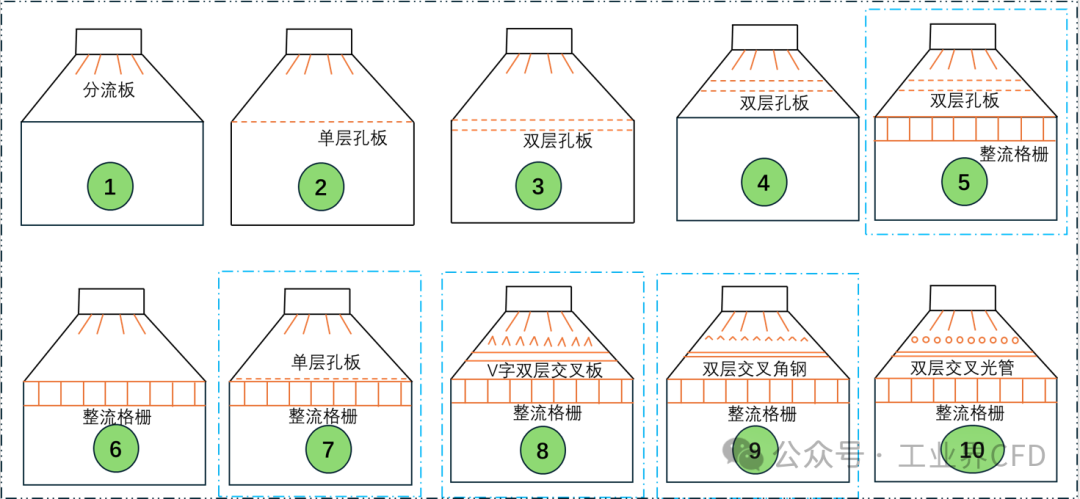
第1、2两种方案直接不解释,流场不行,有采用这两种方案的,咱个人认为直接改造就完了。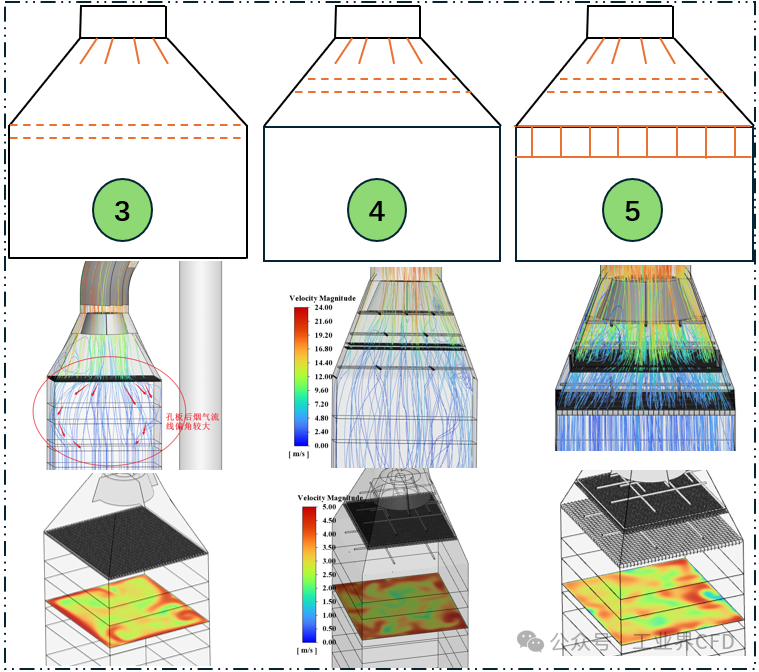
方案3将孔板布置在变径下方直段,这有个好处,支撑梁好做。方案4、5将两层孔板布置在变径内,由于变径内流速比催化剂入口流速要高许多,注定不能采用大开孔率的孔板,否则阻力太大。如果开孔率仍然沿用0.34-0.4,此处的两层孔板阻可能达到500多Pa。 据了解,行业一哥的很多项目采用3、4类设计,孔板开孔率搞到了70%。经过校验,这种方案的流场均匀性有些问题。不是我说的啊,有同行对此方案提出了质疑,有问题找他们[文章:栅格型导流板对SCR反应器内流场影响特性分析],当然咱也校验了,3、4就不是最优方案,犟也没用。经过孔板后,烟气流线偏向四周跑你有什么办法,这就是我在上一篇“从CFD流场角度探讨水泥窑SCR脱硝催化剂积灰磨损挂灰等问题产生的原因及解决方案”中介绍的首层催化剂四周发生掏蚀现象的原因。解决方案就是,采用方案5,直段增加一层整流格栅。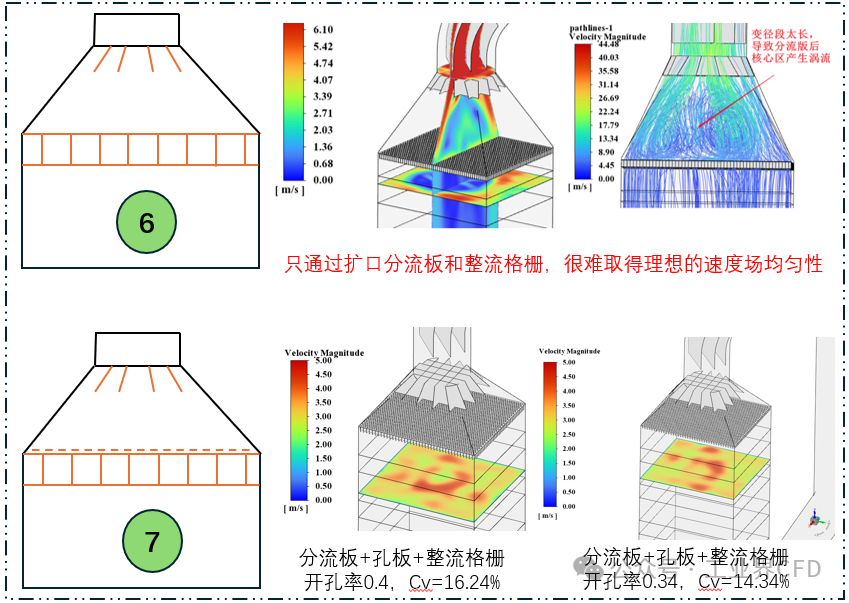
上图方案7对比了常规孔板开孔率范围下的流场均匀性指标,但由于水泥窑烟气高温高尘工况粉尘含量太大,出于对积灰风险的考虑,业主较为排斥孔板方案。但跟同行交流得知,有项目采用了开孔率0.5的孔板,现场并没有出现积灰问题(不排除此类应用都是中温中尘的脱硝工艺,参考[中温中尘SCR烟气脱硝系统流场优化的研究])。有参与过类似设计方案的小伙伴可留言交流。 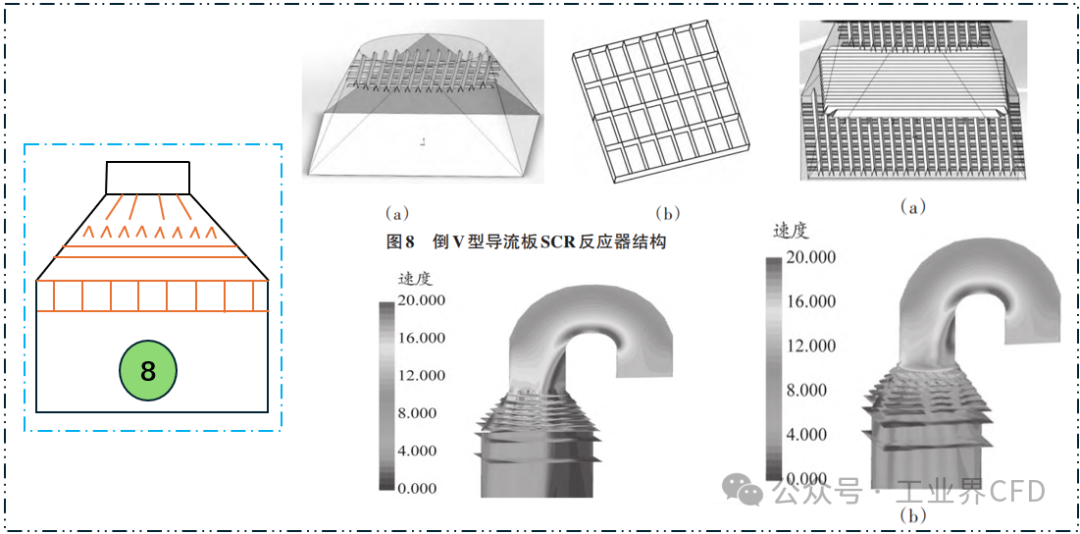
以上方案在来流弯头内都需要设置导流板,尽可能保证扩口上方速度均匀,不要有大幅度的偏斜,否则仅通过V型导流板和格栅也不能很好的取得流场矫正效果。从上面的研究结果来看,三层交错倒V型板能取得较好的效果。咱的部分项目结果显示,只要是来流弯头增加导流板,保证天圆地方来流没有那么大的偏流,通过分流板+倒V型板+整流格栅也可以取得较好的流场分布效果。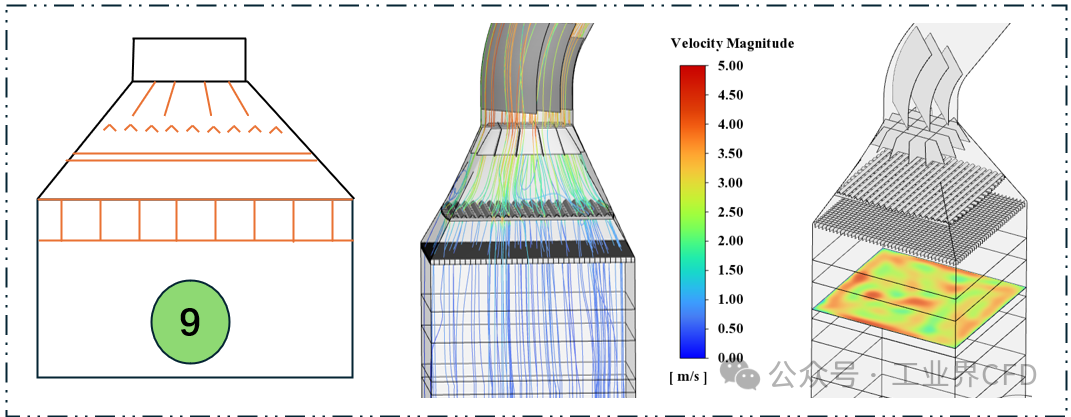
上图是通过分流板+双层交叉角钢+整流格栅取得的催化剂入口速度分布均匀性和流线图,效果较好。通过调整双层交叉角钢的位置和间距,可以很好的降低阻力损失并提高速度均匀性,尤其需要通过流场优化,调控好边壁侧角钢到壁面的距离,可以有效防止催化剂入口两侧壁面流速较高的情况发生。 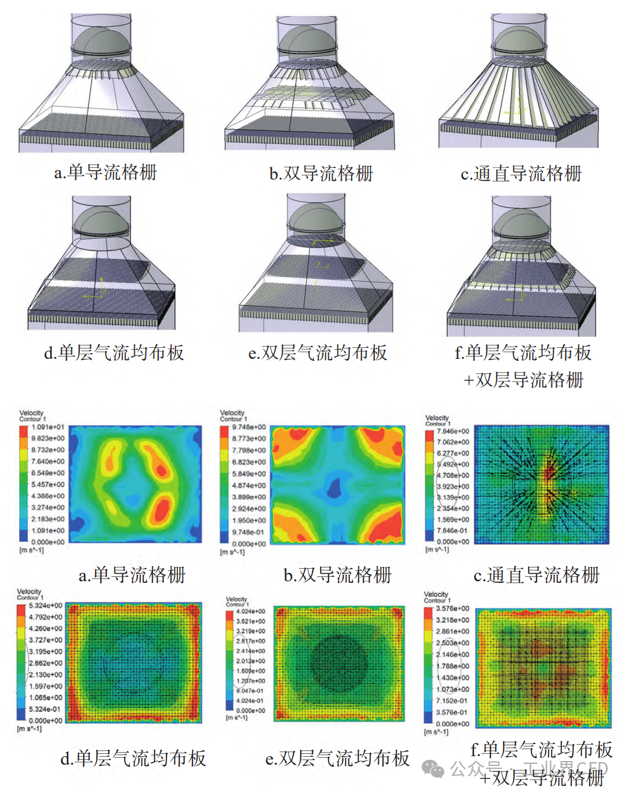
上图是同行[参考:水泥窑SCR脱硝反应器入口烟气均流扩散的数值模拟研究]采用的一些优化措施。如果是中温中尘脱硝工艺,我认为优化结果是可取的,但是对于高温高尘,我还是排斥孔板方案。 本文内容只是根据以往项目积累的一些经验,存在认知局限性,如有不当之处,还请大佬私信指正。有问题可扫下方二维码联系。
工业界CFD:133-0129-2587
——END——
本号专注于工业设备的仿真方法和技术交流,经验分享及案例展示具有片面性,内容仅供参考。版权归原作者所有,若有侵权,请联系我们删除。