绕管式换热器管板的有限元应力分析和评定!
绕管式换热器因其特有的优点,在行业内已得到业主越来越多的认可、选择,未来在行业内势必将会有更为广泛的应用。我们这个行业虽然是个传统的行业,已经过了知识井喷和建设大发展的红利期。但是,新的技术和不断的创新会是行业发展的一个新的增长极。笔者也看到目前行业内很多企业都在积极的创新和寻求新的发展机遇,而作为行业内的从业人员,也得紧跟行业发展的趋势,不断的学习和掌握新的专业知识和技能。本文为笔者学习NB/T10938-2022《绕管式热交换器》标准的一点总结和理解。
(1)高效紧凑:绕管式换热器具有高效紧凑的特点,能够在单位容积内提供较大的传热面积,每立方米容积的传热面可达100~170平方米。 (2)湍流效果好:绕管式换热器的特殊结构使得流体在换热管束中形成强烈的湍流效果,使得流场充分发展,不存在流动死区,提高了换热系数,减小了传热面积,以最少的材料达到最佳的换热效果。 (3)结垢倾向低:由于流体在相邻管之间、层与层之间不断地分离和汇合,避免了垢物积聚沉淀,减少了结垢的可能性。 (4)重量轻、占地少:绕管式换热器的设备重量小、占地少,安装检维修便捷,容易实现大型化发展。 (5)适应性强:绕管式换热器能适应高压(管内的操作压力可非常高,目前国外最高操作压力可达到2000Mpa以上)、高温差、热冲击的工作环境,具有良好的热补偿能力,传热管的热膨胀可部分自行补偿,消除部分热应力。 (6)特殊性:可设置多股管程(壳程单股),能够在一台设备内满足多股流体、多股介质的同时换热。 (1)清洗、维修困难:由于其结构复杂,清洗和维修相对困难,特别是在高压和高温环境下。 (2)造价高:绕管式换热器的制造和安装成本较高,因为其结构复杂,需要专业的技术和设备。
(1)整体管板热交换器(Ⅰ型):管程为单股流,换热管管孔集中分布在整个管板上的热交换器。
(2)分区布管的整体管板热交换器(Ⅱ型):管程为多股流,各股介质换热管管孔集中分布在整块管板的不同区域的热交换器。
(3)分体管板热交换器(Ⅲ型):管程各股介质换热管管孔集中分布在不同管板上的热交换器。
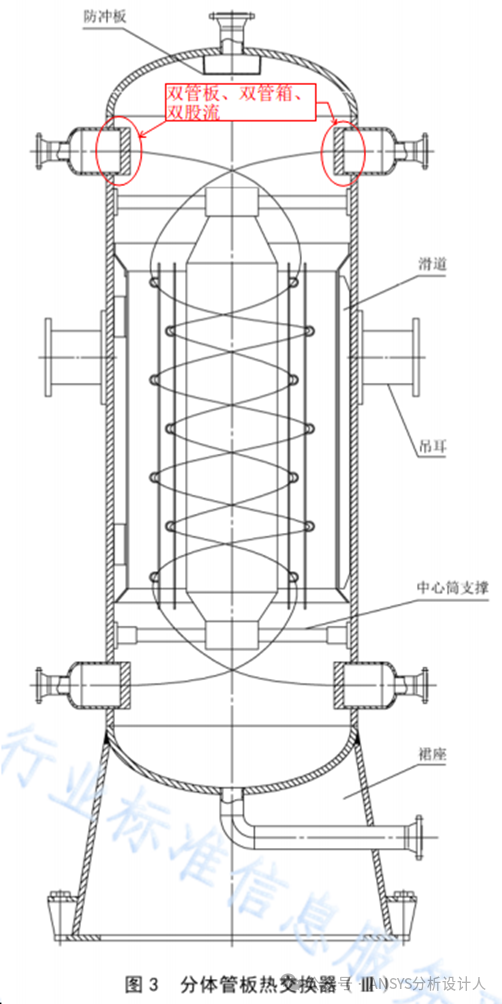
(1)管板局部结构有限元应力分析的流程:可参考下图执行。(2)管板初始厚度的确定:可参照GB/T151-2014中U形管式换热器管板的计算公式进行初步确定。(3)管板计算工况的确定:应根据设计条件按下表的计算工况进行应力校核。g) 同时考虑壳程压力Ps、管程压力Pt和温度场作用。说明:当管、壳程温差产生的应力可忽略不计时,无需考虑温度场的作用,可仅计算1、2、3三种工况,另外,可看出其计算工况比固定管板换热器的计算工况中增加了一条仅考虑温度场作用的工况。
(4)管板计算时应考虑管束重力载荷的影响:重力载荷的加载方式可以等效压力的方式施加到中心筒的截面上。(5)管板计算时考虑管、壳程介质静压的影响:重力载荷的加载方式可以等效压力的方式施加到中心筒的截面上。(6)管板局部结构分析应符合GB/T150.1附录E中的相关规定:a) 材料设计应力强度按GB/T150中的许用应力确定;b) 有限元计算的应力分类和结果评定按4732执行;c) 采用应力分析的管板局部结构的制造、检验和验收按4732执行。
有限元分析实例来源于NB/T10938-2022标准,以分区布管的整体管板为例(Ⅱ型)。(1)管板结构尺寸、材料性能等参数不再列出,感兴趣的朋友可详看标准。 (2)有限元模型及网格划分:考虑结构的载荷特点及结构特点,采用1/4模型三维实体单元建模,计算模型包括管板主体、部分壳程圆筒、部分管程圆筒、中心筒,标准中还将管板与换热管的连接焊缝也建立了模型。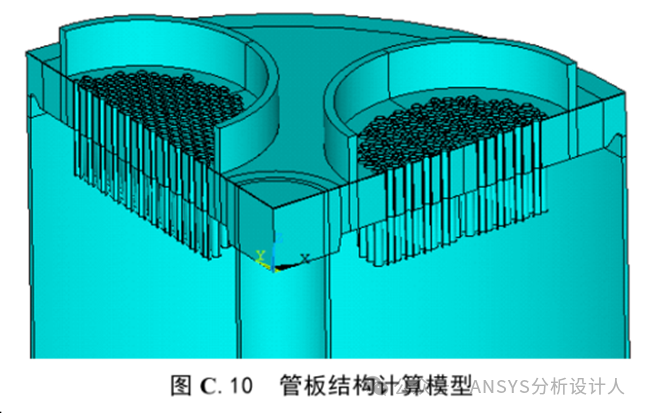
(3)载荷工况:根据设计条件确定了7中载荷组合计算工况,如下表所示。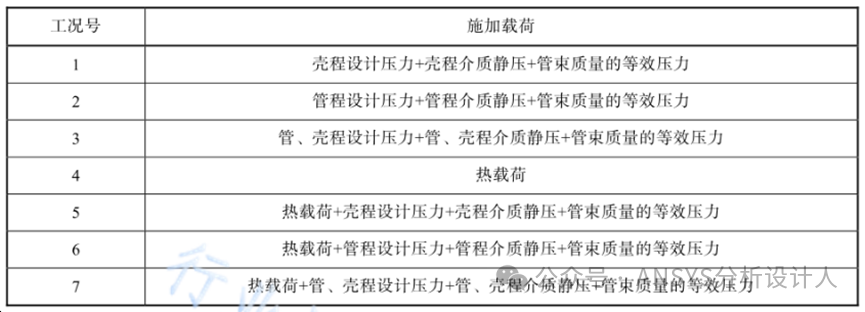
a) 对称面约束法向位移,壳程圆筒截面约束轴向位移;b) 管程压力施加在管箱内筒体、管板壁面及换热管内壁面;c) 壳程压力施加在壳程内筒体、管板壁面、换热管外壁面、换热管与管板连接的间隙面;e) 管束重量以等效压力的方式施加在中心筒截面上;f) 温度场的计算结果作为热载荷导入到计算模型上。(5)有限元应力计算结果:如下图所示,仅列出三种工况,更为详细的计算结果请详看标准。
b) PH2、PH3为管板布管区内管桥间大应力区域厚度方向;c) PH4为管板布管区以外、管箱之间大应力区域厚度方向;d) PH5、PH6为管箱筒体与管板连接的结构不连续区域;f) PH7、PH8为壳程筒体与管板连接的结构不连续区域。(7)应力分类及评定准则:应力分类应根据设计工况及结构区域进行区别划分和评定。对于工况1~工况3,为仅考虑压力载荷不含热载荷的工况,这些工况下各条路径上需要分别考虑和评定SⅡ、SⅢ、SⅣ,如下区分:a) PH1~PH8路径上的薄膜应力均归为一次局部薄膜应力并按SⅡ进行评定;b) PH1~PH4路径上的弯曲应力均归为一次弯曲应力并按SⅢ进行评定;c) PH5~PH8路径上的弯曲应力均归为二次应力并按SⅣ进行评定;对于工况4~工况7,均为考虑温度场有热载荷的工况,这些工况下各条路径PH1~PH8上的应力均归为二次应力并仅需按SⅣ进行评定。
(8)应力评定结果及思考:详细的应力评定结果汇总本文不再列出,另有一个问题提出供思考和探讨,标准中有限元模型将管板与换热管的连接焊缝全部建了模型,但未见对焊缝处应力进行评定,也未见利用有限元计算的应力对拉脱力进行校核。焊缝的建立和焊缝处的应力可能会对管板布管区管桥间路径上(即上文的PH2和PH3)的应力有些许微小影响,对其它路径上的应力评定应是无任何影响的。另外,焊缝处的应力成分中峰值应力会较大,即使考虑了焊缝,但是峰值应力对于SⅡ、SⅢ、SⅣ的评定是没有影响的。是否仅在有疲劳工况的时候,才需要建立焊缝计算峰值应力进行疲劳寿命的评定,当然抛开此处有限元处理和应力计算的准确性,建立焊缝模型与实际结构毫无疑问是更吻合的,但是对于最终计算和评定的必要性究竟有多大,希望听听各位大神们的见解!感谢参与此标准编制的专家们的辛苦付出,让我们从业人员能够对绕管式换热器有了进一步的深入了解和认识。以上内容为笔者学习总结的一点内容,部分为笔者的个人观点和思考,因笔者水平有限,文章内容的理解和解读会有不到位或不当之处,欢迎不吝批评指正!